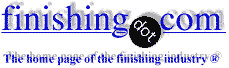
-----
Starting-up a Galvanizing Kettle with Zinc Ingots
Q. I have started up a new zinc kettle and galvanized about 30 ton of material, and had to stop the kettle because of much dross - around 5 mt generation. I would like to know if this is normal due to a new kettle? All parameters from the process were checked, iron content in flux was below 2 g/L. dross was very bright and shiny, appearing to have a lot of zinc in it. I stopped the kettle and there was a deformed spot in one of the walls. I used SHG for this startup as recommended.
Carolina Aires- Sao Paulo / Brazil
July 8, 2021
A. It is normal to have a high dross production on the startup of a new kettle. But this should reduce after about 2 weeks.
The new kettle wall will create some dross, and also form an alloy layer on the inside surface in contact with the zinc. Until this dross layer on the kettle wall forms, some dross will fall to the floor of the kettle and needs to be removed.
When dross is removed, it is like wet sand on a beach. Sandy gritty granular material containing seawater on the beach, and in dross, containing some clean zinc. You do not want to loose that good zinc, so the usual way to get it out is to dig a shovel into the dross while still in the spoon / grab and work it about (agitate). Allow the zinc to drain out safely. That zinc can be put back in the kettle.
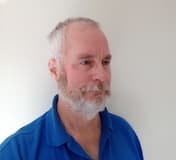
Geoff Crowley, galvanizing consultant
Crithwood Ltd.

Bathgate, Scotland, UK
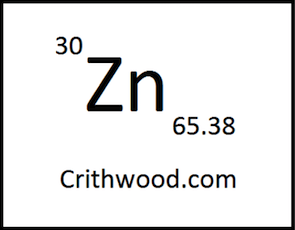
August 10, 2021
⇩ Related postings, oldest first ⇩
Q. Sir,
After repairing of our Galvanizing kettle, now we are putting back the zinc block back to the kettle. On the time of removal we made the liquid zinc as near about 1 mt size block.
Q. My question is, is it okay if we are putting back the same block to kettle or shall we have to fill with new zinc pieces.
Thanks and Regards
- Dammam, Saudi Arabia
January 29, 2012
A. You can use the same zinc that came out, though this might not be enough.
You need to pack it in carefully, to avoid air pockets between (pack as tight as possible without forcing it, and ensure as much surface area contact as possible with side walls to get heat transfer.
Use 25 kg ingots to fill voids.
You will want a special heat up program, probably supplied by kettle manufacturer. Don't be tempted to rush that, you can cut years off the life expectancy of the new kettle!
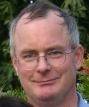
Geoff Crowley
Crithwood Ltd.
Westfield, Scotland, UK
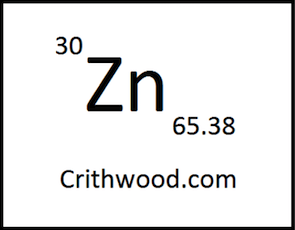
February 1, 2012
On first charge with zinc ingots, can we add water?
Q. On first time heating zinc ingots, can I add water in kettle so that kettle plate cannot get heat?
Deepak Parsekargalvanizers - Mumbai, Maharashtra, India
July 8, 2014
? Hi Deepak. I'm not experienced enough to answer your question, but I would like to know if I am at least understanding it. Are you asking whether you can "boil" the zinc ingots with water in your kettle to get them up to 100 °C as the initial heating step?
Regards,
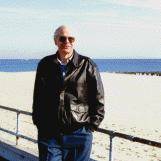
Ted Mooney, P.E.
Striving to live Aloha
finishing.com - Pine Beach, New Jersey
July 2014
![]() |
A. Dear Deepak. Gunatit Builders ![]() Manjalpur, Vadodara, Gujarat ![]() July 11, 2014 A. I think the question might refer to starting up a new kettle, packed with zinc ingots to melt out in preparation for galvanizing. ![]() Geoff Crowley Crithwood Ltd. Westfield, Scotland, UK ![]() July 11, 2014 |
by Kuklik & Kudlacek
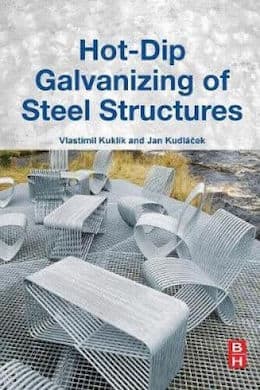
on eBay or Amazon
or AbeBooks
(affil link)
Q. Please advise how charging is done in new pot, with ratio.
SURENDRA M.KULKARNI- Boisar, Maharashtra, India
August 19, 2015
Hi cousin Surendra. Please explain more exactly what it is that you want.
It's hard to tell how broad your question is: are you asking strictly about the best stacking pattern, or about proper gloves, eye protection & footwear for charging the pot, along with enclosed space protocols, etc.? Please start by introducing yourself, and try to put more words in your question than you want in the answer :-)
Thanks!
Regards,
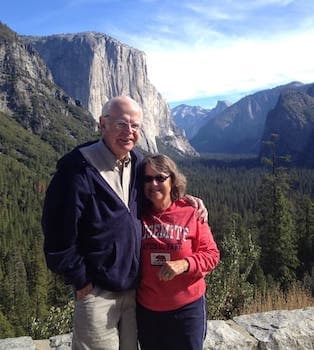
Ted Mooney, P.E. RET
Striving to live Aloha
finishing.com - Pine Beach, New Jersey
August 2015
Best melt down arrangement of zinc ingots in a new kettle?
Q. What would be the best melt down arrangement of zinc ingots inside the new kettle? We are using 20-kg zinc ingots and wooden wedges. Instead, I would like to use 3-ton zinc blocks for shortening the alignment time.
Btg Zengo- Turkey
March 23, 2017
A. Yes, there is a very special way to arrange the Zinc Ingots inside the Zinc bath for melting.
1. There are certain pics I can share with you but I don't have any of your contact.
2. Anyway, Keep the Zinc ingot surface in maximum contact with the Zinc kettle inside surface so that maximum heat can transfer to the Zinc.
3. you can keep Zinc ingot vertically, make it stand putting another zinc ingot. Pack it tightly.
4. you can fill normal drinking water in to the Zinc kettle after filling it with Zinc, it will make homogeneous heating of zinc at least up to 100+ °C
- Delhi, India
April 6, 2017
Thanks for your answers, Mr. Dalela. Feel free to e-mail those pics to to share them with all :-)
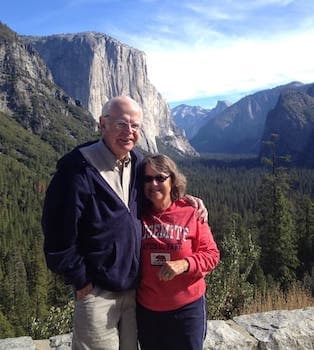
Ted Mooney, P.E. RET
Striving to live Aloha
finishing.com - Pine Beach, New Jersey
A. I don't like the idea of filling the voids with water. It's true that this would help heat transfer up to about 100 °C, but after that all that water has to be boiled off, and the energy required to do that would be enormous!
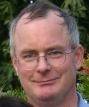
Geoff Crowley
Crithwood Ltd.
Westfield, Scotland, UK
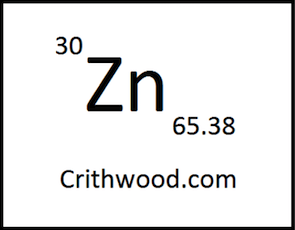
April 25, 2017
A. Dear Sirs,
Zinc filling pattern is changed now. There must be 100 mm to 150 mm gap between zinc ingots layers. Please refer to photos.
- Vadodara, Gujrat, India
July 19, 2017
![]() |
I remember being advised long ago to step lively as I passed under a strand of uncoiling screw machine wire because a rogue loop could decapitate me, and just this week I saw an Indian ad for just such an installation, with the workers ducking their heads as they scurried below the snaking, uncoiling, overhead strand :-) Regards, ![]() Ted Mooney, P.E. RET Striving to live Aloha finishing.com - Pine Beach, New Jersey August 2017 |
Q. Dear All,
It's been great reading your forum! We are setting up a new Galvanizing line. Kettle size 12.5m L x 2.6m D x 1.8m W. I was also wondering what's the best way of stacking zinc ingots (25 kg) and how many tonnes of lead do we need to add in at start up & how do we arrange it too?
There are many suggestions from various sources but surprisingly all have their own opinions. Is there like a SOP for this procedure?
I'll highly appreciate your comments and suggestions.
Sonic Galvanizing Malaysia - Selangor Malaysia
October 14, 2017
Are zinc ingots added to galvanizing tank while it's running?
Q. I would like to understand for "hot dip galvanization" process --
1) how is the molten zinc bath refilled / zinc bath level maintained?
2) Is zinc block / zinc ingot dipped into zinc bath to maintain the level? If so, how is it dipped?
Thanking in advance
- Mumbai, Maharashtra and India
December 8, 2017
A. Vivek,
You will get many opinions on how to stack a kettle for the first melting of zinc, and also for whether or not you should add lead. (you don't have to, and in some countries are not allowed to).
One thing all agree on, and that's that you need good conduction between the kettle wall and the zinc, so as much as possible should be touching the walls.
Ankit:
Zinc ingots are added during production between dips. Some add at shift end for convenience, but this is a bit like adding an ice-cube to a cup of hot coffee, it just melts away and is gone quite quickly. A calculation shows how much to add when the level drops a little (taking into account that molten zinc is less dense that solid), so that when the level gets low enough for a whole ingot, its added. But ingots come in many sizes from 25 kg to several tonnes. It is lowered into the bath of molten zinc on a crane in a similar way to how the steel is lowered in. If on a chain, then the chain is taken out again afterward.
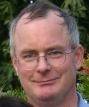
Geoff Crowley
Crithwood Ltd.
Westfield, Scotland, UK
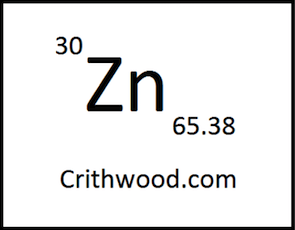
December 10, 2017
Thanks Geoff. Now I understand the illustrated stacking pattern; it's about wedging the ingots in to maintain pressure against the tank walls for good contact.
Regards,
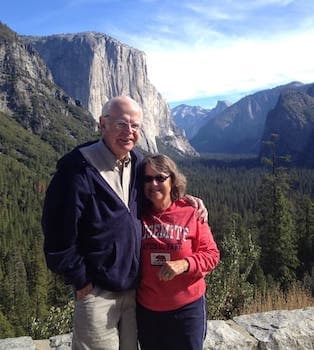
Ted Mooney, P.E. RET
Striving to live Aloha
finishing.com - Pine Beach, New Jersey
December 2017
Q. Dear sirs,
We are about to shift from our old Galvanizing kettle to built stand by furnace. New kettle will be set within a few weeks. My question: is the best way to start the new kettle with the pre melted zinc from old kettle? Will it be ok to fill new kettle with 2 ton zinc blocks? What if we start heating new kettle then pump molten zinc directly from old kettle to the new one.
Bahra Cables - Jeddah, Makkah, Saudi Arabia
February 20, 2019
A. The question on whether to hold zinc molten from old kettle to use in new one is one of cost and time.
It costs more, as you have to rent the temporary kettle(s) to hold the zinc, and as they are mostly electric, you will need a generator (most plants don't have enough spare electric capacity), so more rental, then diesel. Bargain on using a lot!
But you save some heatup time in your new kettle, and that is a saving in time (= money), and in gas.
It is quite practical to add some solid zinc ingots to a new kettle (perhaps 5-10% of capacity - any amount), and preheat that partially loaded kettle in usual way (and if you don't know, get this important info). Then when preheat done, pump back the molten zinc being held.
There's a limit to how long to hold the zinc in electric kettles - ask the provider. I suspect weeks is too long, they're usually looking for days.
Be very careful on preheat, even with a little zinc in, it's easy to overheat and destroy the kettle. Don't ask me how I know this!
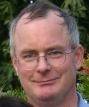
Geoff Crowley
Crithwood Ltd.
Westfield, Scotland, UK
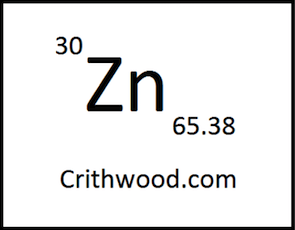
February 21, 2019
Thanks Mr. Crowley,
Actually we have standby furnace 6 meters distance from old zinc kettle. We are planning to fix the new kettle at the new furnace. For that I'm thinking to keep the old running and start preheating of new one then start pumping zinc to the new kettle directly from old Galvanizing kettle.
Bahra Cables - Jeddah, Saudi Arabia
March 4, 2019
Q. Now if we are going to make preheating for new kettle with partial filling, what could the best practice to safely transfer molten zinc from old kettle to the new one without cause over heat for kettle.and is there any recommendations for heating graph.
Mohammed. Farouk Abdallah [returning]Bahra Cables - Jeddah, Makkah, Saudi Arabia
March 16, 2019
A. Molten zinc is normally moved by pump. Special submersible pumps are made for this purpose where the motor and pump impellor are a long way apart using a long driveshaft about 1.2 x the depth of the kettle. Of course there needs to be pipework as well. There are any number of contractors who have this equipment and move it round the world doing this very job.
On preheat, assuming a part filled kettle with ingots (cold) and then a partial pump over of molten metal, the preheat would be the same as for a fully loaded cold kettle - long and slow! And with plenty of redundancy of thermocouples for checking and controlling temperature (don't ask me how I know that!).
The heatup schedule should be agreed with the kettle maker, and it is inappropriate to detail one here. Too much is at risk to get this wrong for lack of information. There's many factors to take account of. Suffice to say that it is possible, even easy to totally wreck a brand new kettle in under 12 hours by doing this wrong. If you don't know, get advice, and if that costs some money, pay it.
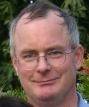
Geoff Crowley
Crithwood Ltd.
Westfield, Scotland, UK
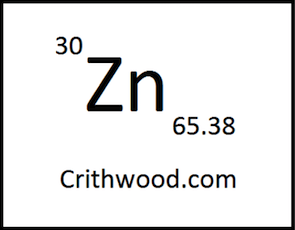
March 19, 2019
March 24, 2019
A. to Mohammed. Farouk Abdallah.
as of my experience that shifting the molten material from old to new tank will save your time and it practical.
just you have to take care of.
1- bring the new kettle to the temperature of the old(molten) its easy to compare the temperature by good quality infrared thermometer.
2- fill the molten material in a new tank for half meter height(it will transfer the heat from side walls to the end walls)
3- keep maintain heat in new kettle until the end walls are reaching to 70% temperature of side walls.
4- add more one meter molten material to the new kettle. and maintain it for other one hour or bit more you will see that all sides are on almost the same temperature.
5- add the rest of the material to he kettle and its done.
Note: by using your infrared thermometer as a reference, you can calibrate you, new temperature controllers.
any objection or counter comments will be highly appreciated.
Alshaya industrial automation & services co - Fahaheel, Kuwait
A. The use of an infra-red thermometer "gun" needs some caution. They are highly dependent on the emissivity of the hot material. Almost useless when pointed at molten zinc, and if you hit the sidewall of the kettle with the laser pointer, then shift to molten zinc, then huge variations in apparent temp can be seen.
I think that thermocouples give a more reliable indication, where they measure the temp of whatever they're immersed in. Be that molten zinc or air.
But be sure to have tested, thermocouples and several in operation, don't rely on only one.
The temperatures on heatup like this are critical. Overheat the kettle and you can remove (dissolve) 10mm of kettle wall in 10 hours.
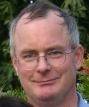
Geoff Crowley
Crithwood Ltd.
Westfield, Scotland, UK
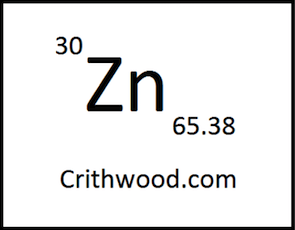
March 25, 2019
Q. I have situation where a kettle ruptured, leaked molten zinc and was temporarily patched. Some of the zinc was recovered, and the kettle was replaced. To remove the damaged kettle, the owner cut the kettle at the level just above the rupture and removed the kettle from the furnace. The kettle and the remaining zinc is around 37 tonnes. Is there a way to recover this zinc? Can the zinc be effectively cut from the kettle? If so, what method? Can the kettle be cut from the zinc effectively?
DENNIS MURONConsulting Engineer - Greenville, South Carolina USA
August 28, 2019
A. Went through this on a galvalume line and used an oxygen lance to scarf out and salvage our frozen/leaked material.
Mark Postema- Rancho Cucamonga, California, USA
October 12, 2019
Q. Dear Sirs,
Regarding to starting new galvanizing kettle, I'm planning to use 50% of zinc from old kettle. Is it OK to add zinc Ash (skimmings) to fill gaps between blocks to get uniform heating?
Bahra Cables, SAUDI ARABIA
January 8, 2020
![]() |
A. In my opinion the use of old Zinc which is of irregular shape, can be used in the middle of Tank. - Delhi, India January 10, 2020 No! ![]() Geoff Crowley Crithwood Ltd. Westfield, Scotland, UK ![]() January 10, 2020 |

Q, A, or Comment on THIS thread -or- Start a NEW Thread