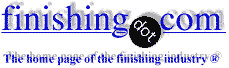
-----
R.O. WATER REQUIREMENT FOR SS ELECTROPOLISHING?
I am involved in setting up a new electropolishing line. The products to be processed are welded and/or formed 316L stainless steel components, ranging in size from 1 ft3 to 60 in. x 30 in. x 24 in. The process steps are 1. Nitric-HF pickle @150deg., 2. ambient rinse, 3. Phosphoric-Sulfuric acid electropolish @125 deg., 4. Dragout rinse @120 deg.,5. ambient rinse, 6. 20% nitric acid dip @120 deg., 7.ambient rinse, 8. 160 deg. rinse. The water source at this location has total hardness of 400-450 ppm. We intend to re-use rinse water, passing it through a deionizer. We have been advised to soften and reverse osmosis filter the water used for rinsing and solution evaporation make-up. Is this necessary, what problems will we have if we use untreated water or just softened water in this process? Thank you.
Thomas Kemp2006
First of two simultaneous responses --
A lot of people use tap water in electropolishing processes. However, a DI or RO final rinse will eliminate water spots. It is also recommended for solution make-up.
Since you are planning to recycle the rinses with a deionizer, you could use the same unit to produce DI make-up water, but this will increase the frequency of regenerations and the volume of metal-containing waste water that needs to be treated. If this is a problem, then an RO can solve it.
We see this situation in plants that operate with zero discharge of process waste water. In these cases, an RO system for make-up is a good way to reduce the amount of waste that will need to be evaporated and hauled off-site.
consultant - Cleveland Heights, Ohio
2006
Second of two simultaneous responses --
A correction - toal hardness of the water supply is 224 ppm, TDS is 470 ppm, silca is 9.2 mg./l. Sorry about that.
Thomas Kemp2006
2006
Purer water (RO or DI) rinses better. Tap water forms precipitates such as calcium sulphate & fluoride which also scale RO membranes.
I suggest using 2 rinse tanks at each rinse step and counterflowing the rinses: 7b to 7a to 5b to 5a to 2b to 2a. See Ted's articles in the finishing.com On-line Library:
"Plating Shops for the Nineties and Beyond" and
"20 Ways to Cut Water Usage in Plating Shops."
Additional comments:
For the high purity water supply, consider 'double RO' -- replacing the DI unit with a 2nd RO unit.
To reduce the liquid wastewater volume to treat, add a small RO unit to the reject stream of the 1st RO [provided flow is high enough to keep concentrations low enough to avoid clogging membranes].
150 F is hot for a nitric-HF pickle Ø easy to over pickle (etch) & much fuming.
125 F is a bit low for the phosphoric-sulfuric EP solution. Raising it to 140-150 F and adding surfactant will lower viscosity, reducing dragout.
Perhaps add a spray rinse prior to the EP dragout rinse Ø reduces changes of the latter.
If using copper fixturing (best conductivity), include stations for racking after pickling and unracking prior to nitric passivation.
- Goleta, California

Rest in peace, Ken. Thank you for your hard work which the finishing world, and we at finishing.com, continue to benefit from.
The amount of dissolved solids in your influent water is hardly significant compared to the amount of dragout you will be removing in the de-ionization processes. True, the rinses will last longer, but not much and hardly worth the effort. If you are going to deionize your rinses I hope you have a lot of time and a big wallet for regeneration and replacement membranes.
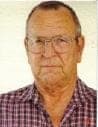
Paul Morkovsky
- Shiner, Texas, USA
2006
Q, A, or Comment on THIS thread -or- Start a NEW Thread