PLATING SHOPS FOR THE NEW MILLENNIUM
by Ted Mooney, P.E. Ret., finishing.com, Pine Beach, NJ
Imagine . . .
. . . walking into a business office and seeing the telephone operator seated before a big old-fashioned switchboard, routing calls from this line to that by frenetically yanking patchcords from this jack and plugging them into that one. Imagine seeing the accountants hard at work on hand-cranked adding machines, and the engineers struggling with slide-rules. Your jaw would drop in astonishment.
But,
for no other reason than that we are accustomed to it, many of us in the plating industry can look at plating shops which have not been substantially modernized in 40 or more years and not be shocked. Or worse, stand by in silence while an associate spends good money rebuilding a shop with new equipment -- but which shop will be indistinguishable from photos of the shop their grandfather built in the early '50s! Is it 'forward thinking' to build a brand new 1955 shop?
Times have changed, and economic factors have changed. And in this age, we are also raising a new generation of citizens who are most emphatically NOT used to 1950's style wet-processing facilities, and will not tolerate their existence.
PLATING SHOPS MUST BE DRY
An old-fashioned switchboard at least has quaintness and harmlessness on its side. But a plating shop with rinsewater splashing around on the floor is a shop with toxic waste splashing around! As it was put so succinctly by New Jersey's former Governor, Tom Kean: " 'Toxic' is a matter of statute, not opinion." In a few years--at most--customers, employees, regulators, and the general public not only will be shocked to see such facilities, but will be outraged as well -- ready to judge the owners and managers as socially irresponsible.
The first principle in designing a shop for the present and the future is that it must be dry. Achieving a dry shop involves several general requirements:
- Process islands
- Enclosed waste lines
- Secondary containment
- Attention to detail
Process Islands
In bygone days, plating shops were often arranged with a cleaning line in one area, an acid room in another, and the plating processes in a third. Wet work was carried from one area to another, dripping all the while, with wastewater consequently tracked around by the operators.
Such an inherent flaw usually cannot be rectified a tank at a time, but requires rethinking the whole plating shop. Work must enter a line dry, stay on a single wet-processing island, and be dried before leaving the process island and entering the transportation or walking aisles. This usually means that each processing line must be independent and self-sufficient with its own cleaning, pickling, plating, and post-treatment tanks.
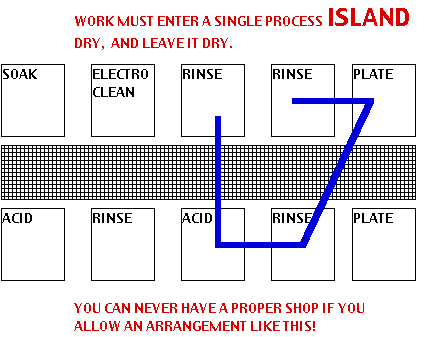
Enclosed Waste Lines
Old-fashioned shops often have trenches into which wastewater and waste solutions flow, not only splashing around but relentlessly searching for a breech in the floor coating through which they can leach into the ground. It is the nature of the floor coatings in plating shops to go unmaintained for years or decades; and, because the coating is right on the floor with no observable dry space between it and the floor, it is nearly impossible to notice a leak before damage is done. In the long run, an impervious floor coating in a plating shop is the exception not the rule; allowing wastewater to flow in open trenches is almost a guarantee of contaminating the earth below, and no one can even keep track of all the plating facilities that have been saddled with cleanup costs in the millions.
In modern shops all waste must be conveyed in enclosed pipes. The pipes, whether in a trench or not, must be elevated off the floor a bit so that there is a space between the bottom of the pipe and the floor which can be observed to be dry. While few plating shops yet use double containment piping, in planning any revamped area be sure to at least allow space in the trenches and vias for the piping to be double contained in the future.
Secondary Containment
Valves and piping occasionally fail, tanks get overfilled, and acts of God like fire and earthquakes damage primary containment devices. For all these reasons, as well as to comply with local sewer codes, OSHA safety rules, and pollution prevention regulations, secondary containment is becoming increasingly necessary.
Some people feel that a curbed and coated floor is a good secondary containment device, but the author believes plastic containment pans are often a better approach for two reasons. First, a leak in a containment pan elevated off the floor is visible and can be corrected before any contamination of the ground occurs, while a breech in a floor topping can be almost undetectable. Second, for good housekeeping and worker attitude it is imperative that it be understood that the floor is supposed to be dry; to install a floor which is designed to be wet is a contradiction and an invitation to sloppiness.
Attention to Detail
It is important that an attitude be instilled which says that wastewater should not reach the floor, and that if it does it must immediately be cleaned up. Equipment that can help make this possible includes drip shields between each tank and each containment pan. Adequate freeboard and drain & overflow piping is also necessary so that slosh-over doesn't occur when work is immersed in the tanks
Usually, alarm horns should be installed to sound when liquid is detected in floor sumps or containment pans. This is desirable because there should be an immediate "downside" to the presence of liquid in these areas or it will soon be accepted as normal. Then, of course, the secondary containment device will have become a primary containment device, and there will no longer be any secondary containment.
For many decades it was routine for steam traps to vent to the atmosphere. The resulting accumulating moisture not only accelerates corrosion, but inevitably results in a wet shop. Today, there are few shops where condensate is not returned to the boiler; but there should be not a one.
PLATING SHOPS MUST BE BUILT OF THE RIGHT MATERIALS
Extensive rust and corrosion can be costly, condemn housekeeping programs to failure, demand impossibly high maintenance levels, and imbue most who see it with the suspicion that something is terribly wrong.
Vital to modern shops is the use of modern materials. Whereas steel tanks and catwalks can sometimes be essentially unmaintainable, PVC, polypropylene, and proper grades of fiberglass will last indefinitely in most plating environments without significant maintenance.
Even worse than steel is aluminum, and aluminized or galvanized materials. These materials are deliberately designed to corrode! See, in some environments the corrosion products comprise a relatively impervious skin; but in a humid and acidic plating shop, aluminum and zinc accelerate corrosion rather than retard it. Where sheet metal must be used for roofing panels and other uses, make sure it isn't galvanized or aluminized. And, while speaking of the roof, remember that substantial wide flange girders may be heavier and more expensive than spindly bar joists, but they can be painted and otherwise regularly maintained at a fraction of the cost.
Not only should the major equipment items be built of plastic, but the little ones should be as well. Metal electrical conduit, pipe, pipe support clamps and patent channel can be virtually impossible to maintain in a plating environment; but when these items are made of plastic they can be installed and virtually forgotten; with occasional cleaning will look brand new for many years.
Plated steel bolts, nuts, and washers don't belong anywhere near a plating tank. Where plastic can't easily be used, stainless steel hardware should be the minimum requirement.
Depending on the process chemistry, it is usually advantageous to nickel plate the anode and cathode rods and saddles, resulting in tremendously improved appearance, corrosion resistance, and durability over plain copper. The copper in bus runs can be lacquered to prevent corrosion and to enhance cleanability.
PLATING SHOPS MUST BE CLEAN
To appreciate the importance of cleanliness in a plating shop, consider a parallel: As you drive up to a MacDonald's restaurant and see employees hard at work washing windows that are obviously already spotless, do you worry about the cleanliness of their food preparation counters--or is it just illogical that the counters could be dirty when the employees have nothing better to do than rewash windows that are already clean? Similarly, if you run a plating shop which is spotless you will have far less trouble with the regulators and the public.
While it is certainly important to enforce a program of regular cleaning, the shop also should be easy and practical to clean in the first place.
In designing the process islands, allow for access all around. When one side or end of a tank line is inaccessible due to being placed against a wall, it can be dangerous or impossible to clean and maintain. Instead, maintain aisleways between walls and the process lines on all four sides.
Tanks should be elevated a minimum of 12" off the floor so that the underside of the tanks can be readily inspected and maintained, and so there are no blind areas where sweeping and mopping are impossible and dirt and trash accumulate.
If your maintenance people have to climb ladders or install temporary scaffolding to gain access to an area, that area will not be likely to be kept clean and properly maintained. Permanent access platforms are the solution.
Shape the contour of the floor, and design the walkways, so that there is a bare minimum of structure to clean, coat, and maintain. Strive for an integrated design where each piece of structure serves multiple purposes, rather than tacking on "this & that" and then having to clean, paint, and maintain countless little brackets and supports forevermore.
New shops should be planned with high headroom. Substantial exhaust ventilation is becoming increasingly necessary for safety reasons as well as to maintain cleanliness, and it can be nearly impossible to design a draft-free environment when high air flow rates are employed in a shop of low headroom. Additionally, a high headroom shop reduces corrosion of the ceiling panels and roof supports, keeping the working environment cleaner and more maintainable--not to mention permitting better lighting, providing cleaner air for the employees to breathe, and reducing the feeling of claustrophobia that a plant full of chemical tanks and hot vats can impart.
PLATING SHOPS MUST BE BRIGHT
To try to save energy at the cost of inadequate lighting in a plating shop is perhaps the ultimate example of penny wise and pound foolish. The energy requirements of lighting a plating shop are so minimal compared to rectification and tank heating that they can probably be safely ignored; and if the cost of rejects is taken into account, a good case can be made that bright lighting actually saves energy.
Most shops should probably double their number of lighting fixtures before even bothering to do any calculations or lighting measurements! In many jurisdictions, the power company will even help you pay for this new lighting if you use energy efficient fixtures.
High pressure sodium fixtures might be okay for outdoor lighting at night, but the author's opinion is that for a proper work environment, lighting must be white, not orange. Fluorescent lighting fills this bill adequately, but even better are metal halide lights. And metal halide lights mounted way up in the rafters are one less thing exposed to corrosive tank fumes, thereby simplifying cleaning and maintenance. [Updated for 2022: LED lighting is now the way to go whenever practical].
In designing a new plating shop, an additional factor that can be considered is available daylight. Some shops, like some artist's studios, have taken outstanding advantage of natural lighting. Yes, we are advocating windows.
When considering the tangible benefits of proper lighting, the intangible should also be kept in mind. As long as there are humans on this planet there will be primordial suspicion about dark places. Even children know that bogeymen hide in dark corners. And to the regulators and the public, the bogeymen that live in the dark corners of plating shops have the names "Environmental Skeleton" and "Imminent Disaster". Just because these bogeymen aren't seen in the dimness is not convincing evidence they're not lurking there. The only sure way to drive them away is to turn up the lights.
PLATING SHOPS MUST BE COLORFUL AND INNOCENT
Just as cleanliness in the visible areas generates a confidence that the less visible areas are clean, bright paint in varied colors implies a sense of organization and purpose, a feeling of safety and predictability, that things are under control and all is well -- the "Sesame Street effect".
Acid tanks might best be bright red, while acid rinses are bright pink, and other tanks other bright colors. Electrical panels should be blue enamel, moving parts OSHA orange, and aisleways yellow. Ceilings and walls should probably be brilliant white, not only for a clean appearance but to enhance reflectivity and thus raise lighting levels.
While you're brightening things up, if you've worked hard to keep your grounds uncontaminated and your shop air clean, demonstrate it with outdoor plantings and an abundance of living things inside.
None of this is meant to be taken as cynicism--as if we should try to con people with a slick paint job, like some oily car salesman. Rather, the fact is that we should be constantly organizing, planning, thinking, and improving all the time. And having done so, having made real progress, we should turn up the lights and proudly show off what we've achieved, and transmit that sense of organization to others--not obscure it all under a uniformly lifeless coat of drab institutional paint.
CONCLUSION
We live in changing times, with new technology constantly making improvements possible. Some of the possible changes are inexpensive, easy to implement, and can be done in step-wise fashion beginning immediately. Others are much more expensive, and may essentially require starting over in whole areas of the shop.
But the public will soon be asking for the heads of anyone operating a plating shop in the fashion of the '40s and '50s, so it is most certainly not too early to begin our general plans to bring our shops into the next century.
photo courtesy of United Silk Screeners
This document may be copied in its entirely for internal use within an organization, but may not be edited nor republished; it may be linked to, but it may not be 'framed' by another website.
Disclaimer: It is not possible to diagnose a finishing problem or the potential hazards of an operation via these pages. All information
presented here is solely for general reference and does not represent a professional opinion nor the policy of an author's employer.