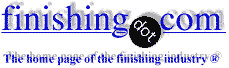
Steps for hot dip galvanizing
-----Current question and answers:
Thanks for the initiatives on this site. Lots of information for new starters.
Can you help me know, what is the least size of Galvanising tank possible for a job size of 2400 mm long X 1100 HEIGHT x 40mm width. If possible I wish to have a bench type model with all other preparatory processes in a space of 500 Sq ft area.
What are the topClass Safety & Healthy precautions needed considering the IoT / Control Electronics Technologies of 2020. Is it so harmful? Albeit, this HDG is not becoming OBSOLETE and any alternate possible as a sacrificial coating.
Thanks
- CHENNAI TAMILNADU India
March 2, 2021
A. Hi Babu. I'll have to wait for someone better versed to tell us whether it's practical to build a small galvanizing facility in 500 sq. ft.
Our ever expanding technology is unlikely to make HDG obsolete any time soon, but what can happen is new technologies can chip away at the edges. Tell us what it is that you are galvanizing, what properties of galvanizing make the process attractive in your situation, and what the exposure and required lifetime are ... because maybe an alloy zinc electroplating may be sufficient for your specific needs.
Trying to advise of all the necessary Safety & Health precautions in a short internet posting is unfortunately impractical, but you can do a literature search for papers on the subject. And surely there are galvanizing and safety consultants who can help.
Usually the Internet of Things applies to high volume consumer items before it gets to low volume specialty stuff for galvanizing shops, but it anyone knows of such devices for galvanizing hopefully they'll speak up.
Luck & Regards,
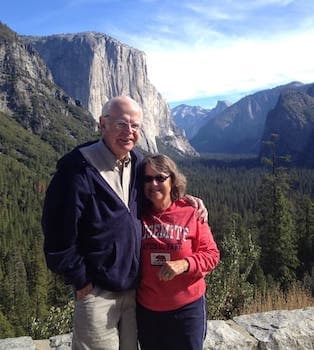
Ted Mooney, P.E. RET
Striving to live Aloha
finishing.com - Pine Beach, New Jersey
March 2021
Q. It is a tubular construction made of 1 to 2 mm thick pipes 6 ft x 4 ft ht and thickness is 35 mm. Looking for a cost effective way of doing. But, want to be 90% conscious of the environmental impact and 10% on Customer need, committed though. But, the hiccups and process gaps, must be catastrophical to my team if at all I start. Too many loop holes to fall through, and hence risks are more. Being a hardcore Mechanical Engineer, the non compliance must not be established as part of the system.
In addition, I respect the ISO14001 and its positive impact. Fear of falling into system loopholes that might impact the team, and cost impediments plus the 100% Recycling of process waste (non availability or my ignorance) is what I want to know more.
Technically, can the HDG parts can be powder coated for colour finish.
thanks Mr Ted for your reply.
- Chennai TAMILNADU India
March 3, 2021
A. Hi again Babu. Yes, HDG parts can be powder coated after proper zinc phophatizing, but that takes space too. Short of suggesting a few books about galvanizing, phosphatizing, electroplating, and powder coating it is difficult to offer short direct answers. You haven't told us who you are, what your 'team' does, what the parts are, what their exposure condition is, why you feel HDG galvanizing plus powder coating is the appropriate finishing regimen, or why you want to do the finishing in-house rather than farm it out -- but if I correctly understand the material to be only 1-2 mm thick, I'll reiterate that electroplating may be more appropriate than HDG.
Readers can usually answer highly specific questions which they clearly understand in the few sentences or paragraphs appropriate to a public forum, but it may not be possible to usefully cover broad subjects that briefly :-)
Luck & Regards,
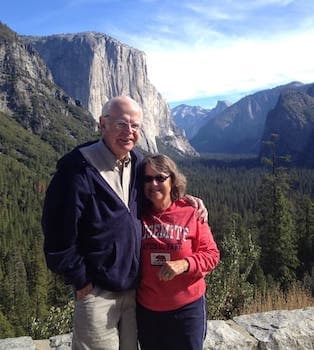
Ted Mooney, P.E. RET
Striving to live Aloha
finishing.com - Pine Beach, New Jersey
March 2021
A. Dear Babu.
As requested by you for Galvanizing of your job size 2400 mm long x 1100 mm height x 40 mm wide.
Your Galvanizing kettle should be minimum 2500 mm long x 700 mm wide x 1400 mm Height (if given sizes are welded).
It's better to share some of your job pictures or drawings to suggest most suitable size for your job and also know production capacity you are looking for per hour basis or per day basis with 8 hrs shift. Based on above, we can suggest some better options.
adv.
You can contact us directly also on my contact number 9825045114
Gunatit Builders

Manjalpur, Vadodara, Gujarat
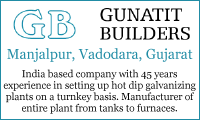
March 12, 2021
⇩ Related postings, oldest first ⇩
Q. I would like to start a galvanizing small scale plant in United Arab Emirates. Would like to know technical steps for galvanizing.
F.M.Bootwalaaluminium and steel - U.A.E.
2006
2006
A. Sir:
In the UAE the following steps would likely be best:
1) caustic soda ⇦liquid caustic soda in bulk on
Amazon [affil link]
(NaOH) 10% at 160 °F. Heated using fire-tubes.
2) Caustic Rinse at room temp.
3) Three sulfuric acid pickling tanks at 150 °F. Heated by hot water from waste flue gas and hot water boiler. Coils of Zirconium.
4) Two series acid rinses at room temp.
5) Zinc ammonium chloride flux at 160 °F (quadraflux). Heated by flue gas and hot water boiler using titanium coils.
6) Molten zinc in kettle with at least depth/width ratio of 1.5. (Dry Kettle). High velocity end fired with natural gas.
7) Possible quench with white rust inhibitor to pass salt spray test.
All tanks lined or made from poly plastic except steel caustic tank. Divided containment pit under tanks. Sulfuric acid reclaiming crystallizer. Cranes suitable to lift universal racks.
Regards,
Galvanizing Consultant - Hot Springs, South Dakota, USA
A. Dear Sir,
For Galvanizing plant in UAE, you should follow following step.
First one tank of acidic degreaser which is used in room temperature, then 2 Acid (HCl) tanks , then 1 Rinsing water tank with use of sweet water, and then finally Hot Flux tank, after that you required drier or hot plate area and then Galvanizing kettle, after Galvanizing kettle you should required one water quenching tank and one passivation tank.
Gunatit Builders

Manjalpur, Vadodara, Gujarat
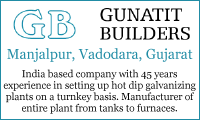
2006
In response to the fellow from India and his recommendation to use HCl:
The use of HCl causes:
1) High cost to dispose of spent HCl
2) Contamination of the flux and higher zinc usage
3) Excessive plant corrosion likely causing roof replacement
4) Preheating of fluxed product costs energy
5)High disposal costs for rinse water and contaminated flux.
A sulfuric plant does cost more for energy; the plant initially costs more because more equipment and tanks are required. In the long-run the sulfuric plant is more environmentally friendly and many sulfuric plants galvanize on a lower per pound basis. This is my experience.
Regards,
Galvanizing Consultant - Hot Springs, South Dakota, USA
My reply to my friend from U.S.A.
He explains problems of using HCl, but I visited all of the Gulf plants specially in U.A.E., and HCl is easily available source over there and it's very cheap to use. It's true that if we use Sulfuric acid at 150 °F the heat will help us -- a better way but cost of heating and increase of pickling tanks as well as shed size also increase due to more tanks and in U.A.E. cost of land are too high; that's why we suggested HCl.
To heat flux at 60 to 70 °C from flue gases will not be very effective as flue gas heat will not be sufficient to heat the flux as well. It's better to have a heat exchanger to heat flux.
Regards.
Gunatit Builders

Manjalpur, Vadodara, Gujarat
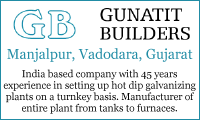
2007
A. 1- Degreasing with alkaline solution at 70-50 °C
2- Rinsing with demineralized water
3- annealing in a HNX atmosphere at 950 °C
4- Coating with molten zinc that contains 0.2% Al
5- Passivation by chromating or phosphating
6-Drying at 90 °C
- Iran
2006
A. The choice of acid is usually an economic one dependent on supplies in the place of the plant.
Almost every Galv plant in Europe, and certainly every one in UK uses HCl. It does have some disadvantages, but these can be overcome.
Rinsing before fluxing (sometimes twice) with the old rinse water being used to make up acid tanks (hence no disposal cost), and buffers in the flux (e.g., Tegoflux) can largely overcome the problems of HCl. H2SO4 has its problems too.
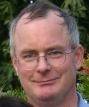
Geoff Crowley
Crithwood Ltd.
Westfield, Scotland, UK
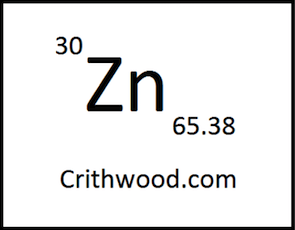
2006
In the electroplating industry the acid wars are long since over, and HCl won!
When I started my career in 1967, hot sulfuric acid pickling was less common than cold HCl, but I did see it here and there (acid-proof brick and all), and even designed a few plating lines with it. But I'm fairly well traveled and haven't seen hot sulfuric acid pickling in an electroplating plant since the mid 1970s; I'd say it's extremely rare and maybe extinct :-)
Regards,
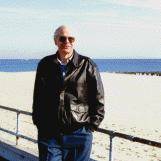
Ted Mooney, P.E.
Striving to live Aloha
finishing.com - Pine Beach, New Jersey
2006
A. Sir,
My recommendation to you is that if you are looking for a mid level investment modern galvanizing plant you go for the following--
1. ACID Based Degreasing Tank.
2 TWO stations of Pickling (HCl tank).
3. 1+1 Rinsing Tanks.
4. Flux Tank (heated by waste flue gases.
5. Drying Oven
6. Galvanizing furnace.
7. Quenching Tanks & Passivation Tank.
You can also go for Caustic based Degreasing & sulfuric based Pickling but it requires more initial investment & HCl can be Neutralized
- Vadodara, Gujrat, India
June 29, 2008
A. STEPS FOR HDG PLANT
-ALKALINE CLEANER (DEGREASER)TANK 160-180F
-WATER RINSE- (2 -TANK )
-HCl ACID PICKLING TANK -20-25 %V/V
-WATER RINSE
-ZINC AMMONIUM CHLORIDE FLUX SOLUTION
-PARTS DRYING CHAMBER
-MOLTEN ZINC BATH
-CENTRIFUGAL DRYER TO REMOVE EXCESS ZINC
-QUENCH TANK CONTAINING CHROME SOLUTION
-HOT DRYER OR DRYING CONVEYOR SYSTEM
- TORONTO-ONTARIO-CANADA
A. For hot dip galvanising plant for small scale, the first stage is acidic degreaser of 10%.
Why acidic degreaser? Because after degreasing there is no requirement for water rinsing, you directly dip job into pickling tank that is HCl, and then water rinsing. After that dip this job to fluxing solution (zinc ammonium chloride the ratio is 300 grm/ltr. Temp. 80 °C.). After fluxing you have to make this job dry or use hot flux (ammonium chloride & glycerine solution Temp. 90 °C.). After hot fluxing dip this job in molten zinc bath 450 °C. Then dip in running water for quenching. And then you dip in dichromate solution. Follow this procedure and you will get very good quality.
- Pune, India
October 10, 2008
Q. Hi ...
Which is better for Hot Dip Galvanizing -- Acidic Degreaser or Alkaline one? and how many rinsing tanks are required in both cases ?
Also, How many rinsing tanks are required after Pickling stage ?
Thanks,
- Shuaiba, Ahmadi, Kuwait
April 18, 2011
A. Sirs:
I vote caustic because in the case of sulfuric it gives three times the pickling speed once the workpiece is in the acid. It is NOT possible to use a rinse tank after acid degrease because iron(II) phosphate precipitates in the acid degrease rinse and fills the rinse tank with sludge. Generally, galvanizers do not test and control acid degrease (e.g., test free acid, iron +2, zinc phosphate, and total dissolved "load.") I tested several acid degrease tanks and many had 0 acid content. At best acid degrease does a small amount of pickling due to the phosphoric acid content. In any case caustic or acid degrease are becoming more difficult to dispose of.
Regards,
Galvanizing Consultant - Hot Springs, South Dakota, USA
April 20, 2011
A. Dear Arshed,
My opinion on the advantages and disadvantages of the 2 Degreasers:
i) Alkaline (normally NaOH)
- Need heating (high cost)
- Relatively better degreaser
- Needs at least 1 rinsing tank after degreasing
- Needs to be disposed of every year or so
- Carry over into Pickling Tank will neutralize acid
ii) Acid Degreaser
- No heating needed (significant cost saving)
- Relatively poorer degreaser
- No rinsing tank needed after degreasing
- Suppliers claim no disposal needed, unlike Alkaline
- Reduces pickling time
- Weak acid, less hazardous for workers
- Cost for Acid Degreaser Tank might be more expensive
Based on the above, you can analyze your need and make you own choice.
Regarding Rinsing Tanks after Pickling, most will suggest 2 tanks with cascade rinse. You will also find a variety of special rinsing systems in the market (sprays, filtration, etc.)
Regards,
- Selangor, Malaysia
Q. This is all very good information! I'm wondering, however, what a small plant would cost to build and commission in North America? When I say small, I'm thinking of a plant that could handle a piece twenty feet long by ten feet wide. (I'm only assuming this would be a small plant) Thank you.
Nick Gurney- Halifax, Nova Scotia, Canada
April 19, 2011
![]() |
USD 5m at least ![]() Geoff Crowley Crithwood Ltd. Westfield, Scotland, UK ![]() April 20, 2011 April 20, 2011 Sir: Galvanizing Consultant - Hot Springs, South Dakota, USA |
Q. Further to the question regarding the cost of starting a small galvanizing operation. What would be the estimated cost for the prep kettles and the molten zinc kettle, including heating, etc. for kettles with the dimensions 5 ft x 25 ft x 4 ft?
From my research, it appears there would be 5 prep kettles and possibly two molten zinc kettles required. I would appreciate any information as to the materials used for fabricating and coating these kettles also.
Finally, any thoughts regarding environmental considerations, facility corrosion mitigation, etc. would be helpful.
- Nashville, Tennessee, USA
December 30, 2011
A. Cheryl,
your questions require much more detail than this type of forum is sensible for. Would you base a business investment decision on posts on the internet? I hope not.
That said there's some valuable advice and sources of info here among the extensive readership.
The preparation tanks are not referred to as kettles, perhaps tanks, or tubs, depending on language variants.
A typical lineup of a galv. plant is:
Degreaser tank, holds caustic soda ⇦liquid caustic soda in bulk on
Amazon [affil link]
solution, is heated.
Acid tanks. Either dilute hydrochloric or sulfuric acid, usually ambient temp. Then one or two rinse tanks (clean water), and a flux tank; heated, aqueous solution of ammonium chloride and zinc chloride mixture.
Next is zinc kettle, lastly optional quench tank for cooling galvanized steel.
The prep tanks need to be very robust. At least, some use steel plate tanks lined inside and out with fibreglass. At the more robust (and expensive) side are fully fibreglass, fully polypropylene or similar. They need to be very mechanically robust.
The zinc kettle is a specialist tank. Never heard on anyone making their own very successfully! Typically 50 mm plate special steel (mild steel useless), and encased in a special gas fired furnace. This whole setup needs careful design if its to be effective metallurgically and cost effective. You should expect 10 years uninterrupted operation from a good one, but <2 years from a poor one.
The number of acid tanks is typically 5-6. The tanks should all be same internal dimensions.
There are suppliers of all these advertising on this site.
Building. If using HCl (which acid depends on availability more than anything else, typically HCl in Europe, H2SO4 in Americas) then building corrosion is an issue. Frame, purlins and cladding are all susceptible. Use corrosion protection, or materials that don't corrode. For example timber purlins far better than steel.
You can't do any of this cheaply!
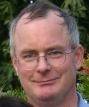
Geoff Crowley
Crithwood Ltd.
Westfield, Scotland, UK
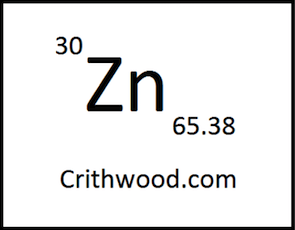
Q. Hi there.
I would like to have information on how to test the degreaser, acid, flux and passivation baths. I more or less know how, but would like to know the right way of testing these baths, etc. I could go for training if I knew where to go, any help on this would be very much appreciated.
Thank you.
Denzil
galvanizing - Bellville, Cape Town, South Africa
July 26, 2012
A. Denzil,
I visited a galvanizer in Cape Town thirty years ago. The galvanizer that I worked for in JBRG wanted me to collect a flux sample from this galvanizer. The flux was very orange with much precipitate of iron (Fe+3) hydroxide (likely too high of pH). The guy running the place would not let me take a sample and I thought he would throw us out.
Acid degrease has many problems. If reject product or galvanized racking fixtures are put into acid degrease then zinc will dissolve and make the acid degrease not work properly. Also the iron (+2) builds, while the phosphoric acid concentration goes down. Almost no galvanizer takes proper care of acid degrease. For testing-- The phosphoric acid is determined via standard base with proper indicator. The dissolved zinc via EDTA with proper indicator and buffer with sodium oxalate to mask the calcium and magnesium in "hard" water. The density of the acid degrease needs also to be be measured about every month. The fate of the phosphate (into the acid and then the flux) could present problems.
For HCl the acid is tested by standard base and proper indicator. Under about 2% to 5% acid slows pickling too much. Iron (+2) is tested via hex chrome with proper indicator and buffer. Higher iron (Fe+2) speeds pickling. Zinc in acid is tested via EDTA with proper indicator, buffer, and oxalate to mask calcium and magnesium. Zinc in the acid very much slows pickling. It is extremely important to have an effective inhibitor at the right concentration in the pickling acid. Inhibitor testing is available for all acid inhibitors and it is simple and quick. With a good inhibitor at the correct concentration, pickling is fast, the acid lasts a long time, and there are few fumes in the plant. Of all the acid inhibitors that I have tested, very, very few are good.
Flux testing includes wetting agent, ACNV (bake and shake in plant), baumé,' temperature, iron (+2), spectrum of all non-volatile impurities (e.g. sodium, potassium, lead, nickel, manganese, aluminum, etc.), pH, sulphate (when pickling with sulfuric acid),etc.
For chromate quench, the hex chrome concentration is tested via color comparison the known concentrations. The pH is tested via proper color indicators. Total dissolved solids is determined via a conductivity meter. Sodium dichromate works best for hex chrome quenches, whereas chromium trioxide (chromic acid) badly stains the product. Chromate quench is dangerous because hex chrome is volatile and gets into the air. In some parts of the world chromate quench is not allowed, in other parts of the world it is required on specific products (e.g. rebar or guardrail, etc.). At a distance of 3 feet from a chromate tank I measured 1,700% the allowable hex chrome when the product was at 200C.
For many years, I put on 4 1/2 day workshops here on the ranch. With my new inventions and contracted clients, I no longer have time to do so. If I start up workshops again it will be for contracted clients only. Also I only sell dropper bottle test kits to contracted clients.
I enjoyed my work in South Africa and I learned much.
Regards, Dr. Thomas H. Cook, Hot Springs, South Dakota, USA
Galvanizing Consultant - Hot Springs, South Dakota, USA
Q. We are expanding our present operation of manufacturing steel boxes for Japan electricity company by setting up an in-house hot dip galvanizing facility. We would like to avoid pre heating the work before dipping in zinc by the use of an oven.
In what way can we avoid the hot oven yet get the work heated before dipping in zinc?
- Colombo, Sri Lanka
August 8, 2012
A. Sir:
Just properly use quadraflux at 71 °C.
Regards,
Galvanizing Consultant - Hot Springs, South Dakota, USA
![]() |
Q. I would like to start a galvanizing small scale plant in Gujarat, India. Would like to know technical steps for galvanizing. Manish Patel- Gandhinagar, Gujarat, India August 29, 2012 Hi cousin Manish. Please do me a favor ... I run this website and am constantly working to improve it. I can't see it through your eyes and am trying to understand why you would take a question which has been answered, explained, debated, clarified, and resolved ... and then simply copy and paste the opening question again? Maybe you are trying to ask salespeople to contact you? Please clarify. Thanks! ![]() Ted Mooney, P.E. Striving to live Aloha finishing.com - Pine Beach, New Jersey September 2, 2012 |
Q. Dear Sir,
Good Morning, I am RVK Patnaik from India, we have a galvanizing plant. We are facing a problem; can you please advise us how to short out the same.
PROBLEM: WHILE PREHEATING THE MATERIAL (20 FEET ANGLES), WE ARE DOING IN BUNCH (20 NOS.) WHILE PREHEATING BOTTOM MATERIAL IS DRYING BUT TOP MATERIAL IS NOT DRYING. DUE TO THIS LITTLE BIT OF WETNESS, WHILE DIPPING IN GALVANIZING TANK ZINC IS CONSUMING MORE. HENCE WASTE % IS GOING UP.
- Hyderabad, AP, India
September 26, 2012
A. Dear Patnaik;
Can you tell us what temperature is your flux? What type of drying unit do you have? And what temperature? How many minutes do you do drying?
Does your flux have any contaminant like magnesia? Do you use wetting agent in your flux?
And what kind of "bunch" is it? Can you take a photo and upload? [Ed. note: e-mail it to ]
If you answer these questions I can help you better.
- Ankara, TURKEY
Q. Dear Sir
Thanks for your response.
Q. Please note that this is transmission tower parts (angles, channels, etc.) galvanizing unit. The tower parts are stacked,bundled for preheating before dipping in hot zinc bath. The jobs are first cleaned by dipping in HCl acid and then further processing is done, like bleaching, etching, etc. Finally the parts are cleaned by hot water and kept for drying, then we are required to heat before dipping in zinc bath. The heat of Zinc bath fumes is also used to heat the jobs, but not that effectively, hence seek your help.
Regards
RVK Patnaik
- HYDERABAD, AP, India
October 3, 2012
A. Sir;
I don't really understand what do you refer by bleaching and etching and hot water cleaning. And why they bundle in drying. Don't they do jigging at the beginning?
Normally HDG pretreatment steps are; degreasing, pickling with acid, rinsing, fluxing and drying.
60 °C of flux will give good drying results even with poor drying unit.
galvanizing - Ankara, TURKEY
October 4, 2012
Dear Sir,
Thank you very much for your reply.
Q. Temperature in flux is 60° to 90°. Drying unit it is open MS platform; heat will be provided from bottom. One bundle of MS Angle / Channel will be 2MT. It will take for drying 30 to 45 minutes.
Degreasing, pickling with acid (HCl 30% diluted), and Fluxing is Gallonflux (Zinc Chloride 75% + Ammonium Chloride 25%).
Our problem is while drying the material on MS open platform, bottom material is drying but top material is not drying.
- HYDERABAD, AP, India
October 6, 2012
![]() |
A. Sir: Galvanizing Consultant - Hot Springs, South Dakota, USA October 8, 2012 A. Sir; galvanizing - Ankara, TURKEY October 9, 2012 |
Readers: although this particular thread wanders all over the place, we have hundreds of threads about specific galvanizing issues. We suggest that you search the site for topics closely related to your questions because potential responders may not find your questions in this gordian thicket :-)
Q. Kindly suggest a way so that during HDG no spurting* takes place (other than drying, as we are using drying oven at temperature 60 °C).
* -- Spurting indicates that if moisture is on surface of part to be galvanized, and it is dipped in hot dip bath, there occurs a vigorous reaction with a lot of noise and molten zinc comes out of that bath and makes working condition unsafe.
- Jaipur, Rajasthan, India
December 17, 2012
A. This "spurting" is a reaction of water on the steel turning very quickly to steam, and in so doing increasing its volume a lot.
While you have the two components of this reaction, water and heat, you can't avoid it, its a physics thing!
And of the two, the only one to be removed is water. You can't galvanize cold, so only drying the steel is left.
There are things you can do to assist drying.
Get your flux chemistry right
(getting it wrong can put a hygroscopic mixture on the steel which will absorb moisture from the atmosphere, making the problem worse).
Allow enough time, between flux and zinc immersion.
A good system is that work sits drying, between flux and dip for two dipping cycles. If your dip cycle is say 15 minutes, then each dip would get 30 minutes drying time.
Have some temperature.
Heated dryers are a luxury. If you have one, that's a benefit, but not everyone has them, and successful dipping can be done easily without. Get flux temp high (70 °C is ideal). Leave steel in the flux for >2 minutes. This heats it enough to dry when it comes out.
Manage the splash.
The splash is only dangerous to those exposed to it, so if you can't stop the splash, then protect the people. A fume/splash canopy, inside of which the dipping takes place, means that the splash is contained.
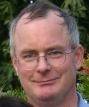
Geoff Crowley
Crithwood Ltd.
Westfield, Scotland, UK
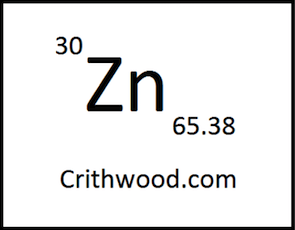
Q. Dear sir, can I get the design of the canopy as suggested by you so that I can implement in my galvanizing plant?
SURESH KUMAR [returning]- Jaipur, Rajasthan, India
December 20, 2012
A. There's no one single design for such a canopy. If you intend retro-fitting a dipping canopy it should be specifically designed to fit.
In a cross shop plant, they can be fitted to overhead cranes, or mounted on the ground next the bath.
In long shop plants, more commonly mounted on the ground.
Most have extraction of fume to a bag filter system. They can have armoured glass fitted so that the operator can see in.
The advertisers of plant and equipment on this site can help you. I'm not a plant builder, rather a plant operator.
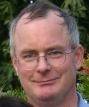
Geoff Crowley
Crithwood Ltd.
Westfield, Scotland, UK
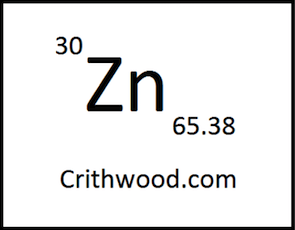
December 20, 2012
Q. Hello,
What a great page for newcomers to the world of galvanising!
I am in the plastic fabrication industry and am considering a small setup for parts that we make to complement our plastic products. The max size I need will only be 500 mm wide x 3000 mm long and 1000 mm deep. Being in the plastics game we can manufacture the tanks easily from PP. Appearance of the finished galvanised parts is not a concern whatsoever, corrosion resistance is the sole purpose. We do not need quick turn around times for the process, drying times, cooling times, etc., can be long. My very simple questions are: can you put a figure on this type of setup? And can you recommend anybody in Australia that I could meet with to help further?
Thank you
- Victoria, Australia
January 2, 2013
A. Hi Paul. Galvanizing plant designers, suppliers, and installers tend to work internationally. Please consider contacting the supporting advertisers listed in the banner at the bottom of the page, as only when people like them are willing to pay the bills are these pages which you are complimenting possible.
As robust a corrosion-fighting process as galvanizing is, there may be more practical corrosion-proofing approaches, like electroplating, for limited numbers of small parts.
Regards,
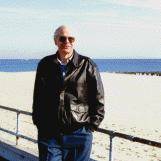
Ted Mooney, P.E.
Striving to live Aloha
finishing.com - Pine Beach, New Jersey
January 2, 2013
Q. Hello sir, I am starting a Hot dip galvanizing, hard chrome and blackodize shop in Surat city. But I have no more knowledge in this area. So give me some good ideas.
Gosai Jaydip- Surat, Gujarat, India
February 1, 2013
9th Edition, Vol. 5
"Surface Cleaning, Finishing & Coating"
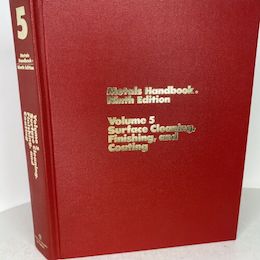
on eBay or Amazon
or AbeBooks
(affil link)
Hi Gosai. If you have no knowledge of these technologies, I would suggest that you start with the ASM Metals Handbook Vol. 5, "Surface Cleaning, Finishing, and Coating" which will introduce all of those topics.
Regards,
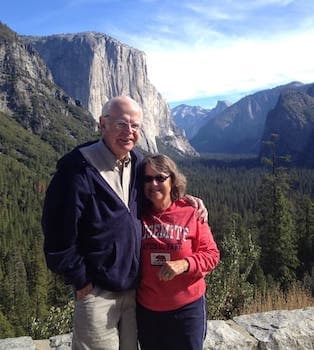
Ted Mooney, P.E. RET
Striving to live Aloha
finishing.com - Pine Beach, New Jersey
December 2017
Q. Please give the ratio of Molten Zinc, NaOH, HCl, Flux Solution For Hot Dip Galvanizing.
Kush Patel- Ankleshwar, Bharuch, India
December 20, 2017
Hello Kush. Apologies but that's an awfully broad question which can't be quickly dispatched on this thread. We have multiple threads, each one with thousands of words, on the suggested ratios for the Molten Zinc tank, the NaOH cleaner, the HCl strength, and the Flux composition. Please search the site and add follow-up questions to those topics if you have continuing questions. This is something that is going to take at least a couple of days of your time. Good luck.
Regards,
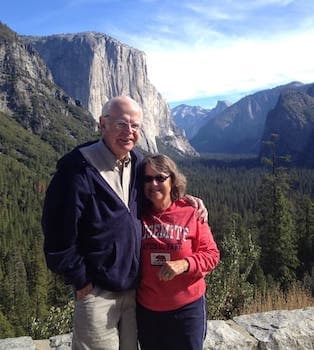
Ted Mooney, P.E. RET
Striving to live Aloha
finishing.com - Pine Beach, New Jersey
December 2017
Q. We are going to start a hot dip galvanizing plant for street light fixtures (12.5 m length and 30 cm diameter) in Arab Republic of Egypt and we need you to provide us with the technical steps for galvanizing.
Regards
- Cairo, Egypt
March 15, 2019
A Guide to process Selection & Galvanizing Practice"
by M. J. Hornsby
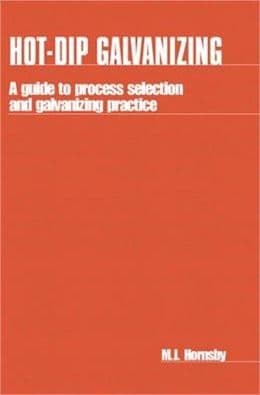
on eBay or Amazon
or AbeBooks
(affil link)
A. Hi Abdelhamid. That was the starting question of this long thread, and was asked & answered 13 years ago and several times since :-)
At this point, please pose a specific followup question about the answers that were offered, and you'll hopefully get a response. But please recognize that if your company has no people experienced in galvanizing, you will have to retain a consultant or purchase turn-key from a supplier. I don't think you will be able to design a galvanizing installation based on internet information. Good luck!
Regards,
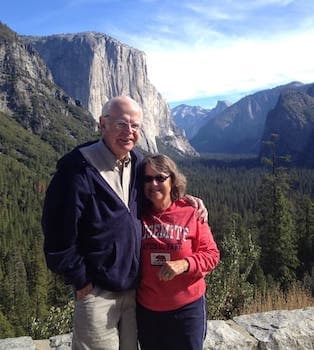
Ted Mooney, P.E. RET
Striving to live Aloha
finishing.com - Pine Beach, New Jersey
Q, A, or Comment on THIS thread -or- Start a NEW Thread