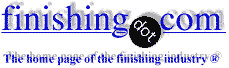
-----
Copper Electroforming problems
Quickstart:
Electroforming is actually the same process as electroplating. If the purpose of the project is to build a component with the process, rather than to simply deposit a thin coating of another metal on it, we usually call it electroforming. Waveguides, bellows, copper foil, and hollow gold earrings are examples of electroforms.
Q. Are there any Electroforming experts around?
I'm running a small tank, 50 gallons of nominally UBAC R1 process. (OMI-Enthone-Selrex).
Production pieces are microwave waveguide structures, typically a mandrel that is a half inch dia. rod, maybe 3 inches long, to be plated with .25 inch copper on all surfaces (finished dia. 1 inch typical.
Mandrel is 6061 Al, zincated, Ni, pure gold at 300 micro inches. I've been going straight into the acid copper with the gold plated mandrel, no CuCN flash (as we once did).
At times this process has worked perfectly. Parts are agitated back and forth on a walking rod, few inches per second. Bath is pumped, filtered, jetted onto the submerged parts. NO BUBBLED AIR, due to lab ventilation limitations.
Problems we continue to encounter are:
1. Bubbles on the pieces, trapped on horizontal surfaces. We're low current, 10-15 ASF typically (process should handle 50-100 ASF). Just a few days ago I added about 10 ml of "Cu Bath Makeup Solution" to the tank, this greatly reduces, almost eliminates the bubble problem. (this addition is based on a "mistake" from some years ago, adding the Cubath makeup to the UBAC R1 bath. I'm guessing a surfactant in the makeup helps shed bubbles.)
2. BUT after adding the Cubath makeup, and several days of excellent performance, my current work piece started to show grainy deposition in higher current areas, and even on the vertical flats.
My question is just general---Help, what are we doing wrong, what can we do for better, smoother electroforms? Is air bubbling considered essential for thick electroforms and we've maybe just gotten lucky sometimes? Our bath has been analyzed, adjusted, and plates beautiful bright copper.
Thanks for any help and suggestions,
Nat'l Radio Astronomy Observatory - Charlottesville, Virginia
2006
A. An eductor agitation system ⇦ on eBay or Amazon [affil link] should definitely be an improvement over cathode rocker agitation if it is not yet incorporated (you make reference to a "jetted" system but I'm not clear on exactly what that comprises). A current of 10-15 ASF is not all that low for electroforming, and good agitation allows good current density. I'm not sure if that wetter can break down into deleterious reaction products, but it sounds like that may be the case. Not claiming to be the electroforming expert you were looking for :-)
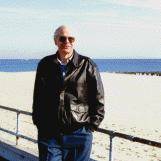
Ted Mooney, P.E.
Striving to live Aloha
(Ted is available for instant or longterm help)
finishing.com - Pine Beach, New Jersey
![]() |
Q. Thanks Ted, Nat'l Radio Astronomy Observatory - Charlottesville, Virginia A. Thanks. It is possible to install a recirculating pump and a discharge pipe as an agitation device. If, instead of just drilling holes in that pipe, you install plastic nozzles in the holes, you can both steer that agitation and get a far greater degree of agitation because the nozzles are designed to use a venturi effect for much better efficiency. They are on my mind because I just finished rewriting the "Solution Agitation and Mixing" chapter of the Metal Finishing Guidebook to recognize their growing popularity. ![]() Ted Mooney, P.E. Striving to live Aloha (Ted is available for instant or longterm help) finishing.com - Pine Beach, New Jersey A. Gerry, I presume the bubbles are forming on the inside surface of the electroform (i.e., on the outer surface of the mandrel) and the copper forms around them. If this is the case, I would suspect the problem to be inadequate surfactant in your bath. You need to carry out an analysis for surfactant - if you cannot, the supply house will be able to. A quick check would be to see if the surface tension of the bath is in spec - this should be given in the Process Operating Sheet. ![]() Trevor Crichton R&D practical scientist Chesham, Bucks, UK |
Q. Thanks Guys, that's useful stuff!
Am I right in assuming that thick walled copper Electroforming will probably always require a commercial make-up and brightener system?
We are setting up a new tank now, with a rotary table and piece rotator system and a tbd eductor setup.
Thanks again,
Nat'l Radio Astronomy Observatory - Charlottesville, Virginia
A. Brighteners and additives give brighter and harder deposits but almost always induce some stress and high temperature detrimental effects. For really thick EF, a very pure and straight copper sulphate ⇦ on eBay or Amazon [affil link] solution gives a shell very much like a part machined from solid copper stock.
Guillermo MarrufoMonterrey, NL, Mexico
Q. Thanks for the valuable replies. A google on "plating eductors" brings up useful resources on that topic. As far as acid copper bath goes it looks like you can always start with just copper sulphate+ acid + chloride (if needed), see if the results are acceptable, and if not then consider commercial additive systems. I think that's the course we'll follow.
Regards,
Nat'l Radio Astronomy Observatory- Charlottesville, Virginia
A. This sounds like it could also be a rinsing issue. Make sure the gold is completely rinsed and then dip in 20% H2SO4 before you load into the UBAC. Also, go in dead and then charge with the actual current required. UBAC is notorious for pitting so you might want to consider a different bath additive system or a strike in additive free acid copper for 1 hour. Good luck
Russell Richter- Danbury, Connecticut, USA
Q. Still fighting with my copper Eform tank.
Per earlier posts, I added a small amount of "Cubath Makeup" to our UBAC R1 copper tank to try and cure a trapped bubble problem. By small I mean less than 10 mL in a 50 gallon tank. This had fixed a similar problem in the past.
Once again it seemed to eliminate the bubbles, but now I'm picking up nodules at the bottom corners, even with current at 8 ASF.
Brightener level seems to be fine, any comments or suggestions?
Thanks,
Gerry Petencin [returning]Nat'l Radio Astronomy Observatory - Charlottesville, Virginia
A. Do you perform a Hull Cell
⇦ huh?
test? Do not make any addition of carrier/makeup without seeing in the Hull Cell that it helps! Addition of make up you can spot with the Hull Cell. Do not add too much!
According to my experience, electroforming with UBAC is much better with the following concentrations:
120 g/l copper sulphate + 180 g/l sulfuric acid.
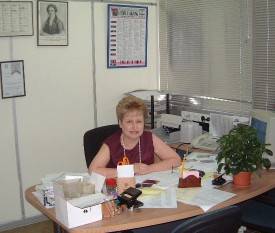

Sara Michaeli
Tel-Aviv-Yafo, Israel
A. At first look, I thought that it was just a high current density nodule which you could use a shield or preferably a robber to fix the problem. Possibly by moving it further from the anode.
Then on the second picture, it appears to be a plated folded box. Would guess that you have some previous chemical leaking out of the folded area that is accelerating the plating in that area.
How can you get by with the lack of plating under your hanger wire?
The one spot on picture 2 side is probably caused by a burr or a spec of abrasive or junk embedded in the surface of the metal.
- Navarre, Florida
![]() |
A. Very interesting photographs - a picture is worth a thousand words. My first thoughts are that most of the nodules occur at high current density areas, namely on the corners of the box. This can be solved by using a robber that follows the edges of the box and will reduce the local current density. The single nodule on the body is probably due to an inclusion or something on the mandrel, but what is interesting is the apparent thickness variation around the nodules on the corner - I have seen this type of effect before and it is due to a disrupted flow pattern of the electrolyte. In this case, it could be due to the nodules. It is clear that keeping the bath in spec is very important to this application, so routine Hull cell testing is essential for good process control. ![]() Trevor Crichton R&D practical scientist Chesham, Bucks, UK
Nat'l Radio Astronomy Observatory - Charlottesville, Virginia |
A. If possible, try putting a radius on all of the edges. It really cuts down on the high current density areas. Since the back corners did not nodule, I wonder if you might have set the part down on a unclean surface and got a few grains of abrasive or micro chips imbedded on the corner edge. If that did not cause the problem, then I would pay very close attention to anode locations and fluid circulations.
James Watts- Navarre, Florida
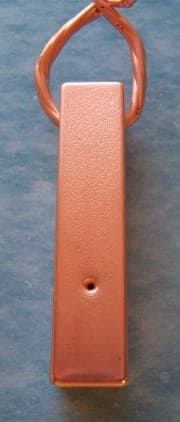
One more photo here, and thanks to you all for helping resolve our Eform problem. Our latest test (scrap) piece came out great, the only change being that I followed Russell Richter's suggestions.
I'd been taught to go into the copper tank hot, but maybe that initial high current density can initiate dendritic growth? And even though we were doing thorough water rinse and avoiding any contact with the piece before hitting the bath I can see where that final rinse Russ suggested, in H2SO4, would normalize the piece to the tank and eliminate drain down or other contamination.
The earlier test piece was started at 8 ASF and had corner problems, this latest piece was at 9 ASF and looks as nice as anything we've ever done.
Lesson learned? Don't get so fixated on chemistry that you're not even thinking about procedure. Again, thanks for the thoughtful replies and for this forum.
Nat'l Radio Astronomy Observatory - Charlottesville, Virginia
Mandrel material for Electroforming a thick layer of copper
Q. Hi,
please help me about electroforming a 3 mm thick layer of copper. What material I should use as a mandrel? Stainless steel , aluminum or something else? Which one is better with a H2SO4 and copper sulphate solution? Thanks.
- Germany
August 26, 2017
A. Hi Oliver. Either should be okay for many applications, but what drives the selection is probably not the chemistry, but other factors:
• An application where stainless is preferred is in repeated mandrel use like in copper foil making, where the hardness and durability of a stainless belt is useful.
• An application where aluminum is preferred is if the shape of the part prevents mechanical removal of the mandrel such that it must be dissolved away.
Regards,
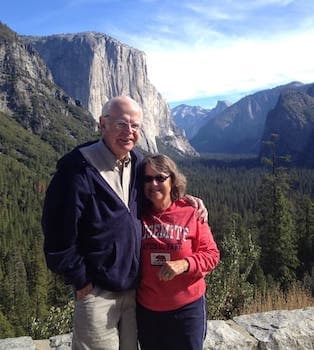
Ted Mooney, P.E. RET
Striving to live Aloha
(Ted is available for instant or longterm help)
finishing.com - Pine Beach, New Jersey
How to avoid dendrites while electroforming
Q. Just recently I upgraded my plating tank to accommodate electroforming larger pieces. I ran the bath for a total of about 30 hours and decided the anodes and bags needed rinsing. I rinsed them under tap (well water) and let them dry completely. Upon re-setting my tank and adding brightener, I ran another bath which resulted in dendrite formations on my pieces.
The only thing I recall doing differently is rinsing the anodes/anode bags/cages and adding brightener. Would anyone be so helpful as to advise me any troubleshooting I may do to avoid these deposits. Below is my complete set up.
SET UP
7 Gallon Tank
Midas Copper sulphate
Midas Proprietary Brightener
Agitation
Anode - Phosphorized Copper, nuggets
Anode Cage
Anode Bags
Thank you!
- Clarkston, Michigan, USA
September 22, 2017
adv.: Supplier of Copper Anodes, Nickel Anodes, Bismuth Metal, & Other Metal Products for Industry & The Arts
Q, A, or Comment on THIS thread -or- Start a NEW Thread