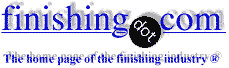
-----
How to Remove calcium from Nickel Plating Solution

⇦ Tip: Readers want to learn from your situation;
so some readers skip abstract questions.
Q. Hi, dear sir.
You say we should raise nickel plating solution to 75 °C.
The nickel plating additives when temperature goes up of 65 °C. start breaking down and they give organic contaminants to nickel plating solution.
Is it the correct way for remove calcium?
Chemical engineer - Iran
June 14, 2022
A. Hi Mohammad. Yes, high temperatures are destructive to the addition agents in nickel plating solutions, and it is likely that they will have to be rebuilt.
But that does not change the fact that calcium contamination is a problem which must be addressed, primarily by never adding raw water to a nickel plating tank, only demineralized water; and secondarily by treatment when necessary. Your shop may be able to safely and legally do the sodium bifluoride treatment described at
www.pfonline.com/articles/nickel-electroplating
in lieu of the one described on this page, but it seems that any calcium removal regimen is rather radical and will probably require carbon treatment and rebuilding of the organic addition agents. Second opinions welcome :-)
Luck & Regards,
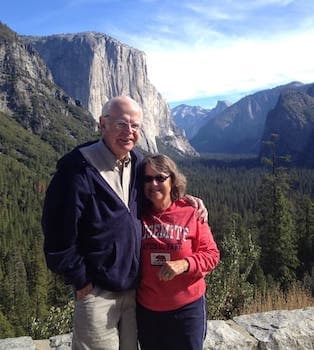
Ted Mooney, P.E. RET
Striving to live Aloha
(Ted can offer longterm or instant help)
finishing.com - Pine Beach, New Jersey
Ed. update: Surf's down dude! That article was moved behind a registration-required wall. Few websites are willing to stand with us in the fight to save the no registration, surfable WWW.
⇩ Related postings, oldest first ⇩
Q. Please help us by suggesting a suitable way to remove Calcium from 10000 liters of Nickel Sulphate solution.
The Calcium present is about 1 gm per liter in the 10000 liters Nickel + Sodium Sulphate solution.
Can you please suggest a suitable method?
Nickel India - India
2006
A. Dear Abhishek,
A more effective procedure is to heat the solution to approx. 165 °F (73 °C) in a separate storage tank. This procedure should not be performed in the plating tank as tank walls, anode bags, and other associated equipment in the plating tank will be coated with insoluble calcium sulphate. (Although the calcium coating will redissolve when the temperature is lowered, the effectiveness of the treatment is reduced significantly.) The treatment procedure is as follows:
1. Pump the plating solution to a suitably lined storage tank fitted with heat and mixing capabilities.
2. Heat the plating solution to 160 - 165 °F (71 - 73 °C) and agitate the solution.
3. Maintain the temperature for at least 16 hours, preferably 24 hours, minimum.
4. While still hot, filter the solution back to the previously cleaned plating tank.
5. Clean the filter before re-using in the plating solution. Not performing this step will result in redissolving the calcium sulphate from the filter.
electroplaters - Mumbai, Maharashtra, India
A. Surely calcium sulphate is very insoluble, at least much less than 1 g/l, so it should precipitate out by itself. I suspect you are using tap water to make up your solutions; this is not a good idea and will cause problems, so use either DI or RO water
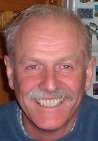
Trevor Crichton
R&D practical scientist
Chesham, Bucks, UK
2006
Trevor is more knowledgable about nickel plating than me, and is correct both regarding the need for DI or RO water, and the solubility limit of calcium sulphate.
However, from my reading it appears that at concentrations of several hundred ppm, calcium sulphate can form very small, almost invisible needle shaped crystals which will cause plating problems ... and which may remain suspended rather than sinking. These can be difficult to filter not just because of their small size but due to their tendency to dissolve at slightly lower temperatures and precipitate at slightly higher.
The aim of the treatment is to raise the temperature to decrease the solubility, and to filter, thus assuring solubility of the remaining calcium at lower temperatures.
Luck & Regards,
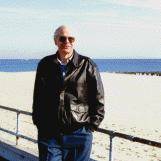
Ted Mooney, P.E.
Striving to live Aloha
(Ted can offer longterm or instant help)
finishing.com - Pine Beach, New Jersey
A. Hi,
I agree with the hot filtration at 73 °C. However, the filter cloth and paper used on the pressure filter must be suitable for fine filtration. Secondly, the tank solution must be filtered for at least 3-4 hours in the same auxiliary tank. Yes, change the filter papers, new cloth and then reuse in the main tank.
It should be checked if calcium is being introduced in the main tank from precleaning of the plates/cathodes . If so, there are other processes to be used for pre-cleaning.
Happy plating,
Rajiv Kulkarni- Pune, India
2006
Q, A, or Comment on THIS thread -or- Start a NEW Thread