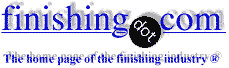
-----
Ideal surface roughness of gravure cylinder for printing on different substrates
Q. I work for a printing company and we have our own in-house cylinder making facility (Rotogravure-shaftless) for which we have a workshop, plating shop and electromechanical engravers to carry out engraving on copper plated cylinders. In order to improve our printing results I am interested to know what is the ideal roughness to have on chromed cylinders after polishing. Following are the parameters we follow for cylinder preparation:
Base cylinder: Mild Steel.
Copper Hardness: 195 to 205 HV.
Chrome Thickness: 6 to 8 microns plated with 125 A/dm2 at 60 °C.
Chrome hardness on 300 micron copper (one side): 800 to 850 HV.
We are using 3M 30 micron paper on our polishing machine with a head pressure of 0.6 bar to get a crosshex pattern.
Roughness achieved: 0.20 to 0.25 Rz.
Substrate used for printing: Polyester, BOPP, PE and Paper.
We have 3 rotogravure printing presses, with press speed range as below:
- Machine #1: 130 to 150 m/m.
- Machine #2: 180 to 220 m/m.
- Machine #3: 200 to 300 m/m.
If some one could answer my question I would really appreciate it.
Thanking you in advance.
plating shop employee - Gujrat, Punjab, Pakistan
2005
Dear sir,
How are you!
According to your question, I will discuss with my technical engineer. And I am glad to know you and I wish we can keep communication in future.
- Dongguan, Guangdong, China
2006
!! I am a consultant cum manufacturer of machinery for chemical engraving process. Our products are plating baths, conveyor type exposing machine, and ring coating machine. I am interested in the answer of the question.
Thanking you, with regards,
- Ahmedabad,Gujarat-India
2007
A. The Ideal roughness after chrome plating is:0.35 to 0.40 Rz. If it is more OR less then it creates problems in the cylinder. In my view it is ideal that I do the experiment.
Arun Deshpande- Mumbai, India
March 2, 2008
A. Hi,
The appropriate roughness should be between 0.3 to 0.6 microns.
Regards,
- Martinez, BsAs, Argentina
October 29, 2010
![]() |
did you got your answer Amit kothari- nagpur August 16, 2022 A. Hi Amit. It appears to me that Farooque got his answer from both Arun Deshpande and Daniel Boaglio. But we have hundreds of readers for each poster so if you feel you have some additional information to contribute, please do. Luck & Regards, ![]() Ted Mooney, P.E. RET Striving to live Aloha (Ted can offer longterm or instant help) finishing.com - Pine Beach, New Jersey |
Ideal Roughness of Cylinder for Aluminium Foil Printing?
Q. Dear sir,
I am working with pharmaceutical and flexible packaging house. We have our own in-house electronic engraving cylinder-making facility of Daetwyler made & Polishmaster of the same. We are facing a serious problem regarding cylinder roughness, and seeing lots of wastage due to cylinder grounding and color wash. We have a instrument for cylinder roughness testing with Daetwyler Polishmaster, but no one in our organisation is able to use it. Is there anyone to please help me out by guiding me how to use it, and what is the ideal surface roughness of gravure cylinder for aluminium foil (hard foil & soft foil) printing job?
Assistant Manager, Production - DAMAN & DIU, INDIA
November 24, 2013
Rotogravure cylinders parameters for cold seal applications
Q. According our own experience we see that roughness of cylinders for rotogravure printing should be roughly between 0,35-0,45 for the standard inks we use (Flint + mixture of ethyl acetate + ethanol). But when it comes to cold-seal print (water base, different viscosity) are these parameters enough or you would advice higher roughness?
Thanks a lot,
Technologist of rotogravure printing machines - Slovakia
June 10, 2015
Q, A, or Comment on THIS thread -or- Start a NEW Thread