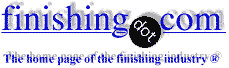
-----
White rust in zinc plating with blue passivation
Q. We are doing zinc plating with blue passivation for fan tray base fabricated in CRS. we observed development of white rust (black dots also) on the surface after 3-4 days. We checked plating thickness and it is measured above 15 microns, then we performed salt spray test (ASTM B117) for one sample from same lot, as per result white rust observed at seventh hours of test.
Our customer requirement is ASTM B633 TYPE 2 SC3 (should withstand 96 hours SST).
Please suggest any process improvement to achieve the above requirement and possible causes of this defect.
note: we packed and kept each part in polythene bags .
- COCHIN, KERALA, INDIA
2005
Hi, Byju. Traditional old-fashioned blue chromates were rated only 24 hours, not 96 hours. If you are trying to replace this with home-brew trivalent coating without a topcoat, it's possible that it could fail in 7 hours if not operated perfectly.
We don't whether this process ran perfectly for years until yesterday at one extreme, or whether your shop has never successfully plated any parts before at the other extreme -- but inadequate chromating would be my first guess. Please tell us more about your chromating process. Good luck.
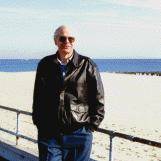
Ted Mooney, P.E.
Striving to live Aloha
(Ted can offer longterm or instant help)
finishing.com - Pine Beach, New Jersey
![]() |
Ted is right, you cannot get 96 hours in salt spray test with a thin blue chromate. You can get it with a thick trivalent chromate with a sealer. ![]() ![]() Sara Michaeli Tel-Aviv-Yafo, Israel 2005 There are trivalent chromates available with or without top coat to meet your requirement of 96 hour sst life. These process are already proved in large scale production level. Contact chemical manufacturer. If you prefer to use hexavalent, use top coat to enhance corrosion. Packing: avoid polythene and use cb box. ![]() P. Gurumoorthi electroplating process chemicals - Chennai, Tamilnadu, India 2005 |
Byju/Ted
Yes. It is possible to get 96 hrs white rust SST. Use trivalent blue from reputed suppliers. They claim 150 hrs but 100 hrs is achievable. give a top coat- 150 hrs is minimum and can stretch to 200 hrs.
By the way Byju, what process have you adopted such as cyanide/Noncyanide/Acid chloride Zinc.
If you are more specific I can help you in a better way.
Byju, it so happened that you belong from my home town and that is very exciting. WHAT A SMALL WORLD !
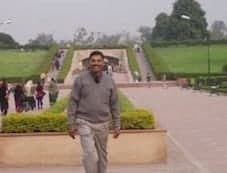
T.K. Mohan
plating process supplier - Mumbai, India
2005
2005
Thanks, P; thanks, TK. Yes, the pressure to develop good RoHS-compliant coatings has indeed resulted in the development of trivalent chromates that offer more salt spray resistance than the 24-hour requirement of older specs. I appreciate the update.
But the question wasn't really whether it is possible to purchase a trivalent chromate that is rated for 96+ hours; it is why he is getting only 7 hours, and my first guess remains that, either due to low quality of the system or poor operation (including inadequate rinsing of the zinc plating), his chromating is the problem. His next issue indeed might be to find out from the supplier (if this is not home-brew) what this particular chromate is "supposed to" be capable of when well operated. Thanks!
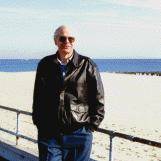
Ted Mooney, P.E.
Striving to live Aloha
(Ted can offer longterm or instant help)
finishing.com - Pine Beach, New Jersey
2005
Ted,
I guess Byju is using traditional Hex chromate with out topcoat. Improper conc. and dip time may have resulted in thin layer and very low SST result. I would recommend Trivalent blue chromate with topcoat with proper process control as follows:
1. Zinc plate
2. Drag-out
3. rinse
4. rinse
5. Nitric Acid dip(0.5-1.0%v/v if plating bath is Acid chloride. up to 1.5% if Alkaline or cyanide bath. Dip time 5 to 10 secs.(Hourly monitoring of the strength of HNO3 found useful)
6. rinse
7. Tri-blue chromate -pH(most important), conc. and dip time has to be strictly followed as per Data Sheet
8. rinse
9. rinse(preferably hot water at 50-60 degree)
10. Top coat (pH, Concentration, and dip time to be followed as per data sheet.
11. Hot air dry.
12.Do not handle or pack till 24 hrs. Subject to SST only after 24 hours curing.
All rinses have to be changed frequently. Continuous flow rinse preferable.
Good luck, Byju !
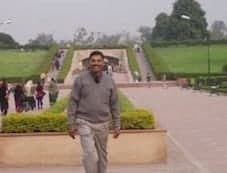
T.K. Mohan
plating process supplier - Mumbai, India
----
Ed. note: thanks again, TK.
January 7, 2011
I'm new to the electroplating field, coming from Pharmaceutical; I find it exciting / interesting; yet experience here seems crucial.
I have followed your dialog and wish to add the following:
I have performed RoHS Trivalent chromating on Fe treated by Zinc (cyanide process) (ASTM B633 type V) and passed 72 hr salt spray with Fe plates. Yet this same process failed with Bolts and washers.
How could I improve the process?
1. HNO3 dipping = 20 sec
2. Should I add more time in passivation to increase layer thickness?
3. I thought of using sealer to enhance corrosion resistance (organic based). Should I rinse between the passivate and sealer? will it assist if rinsing water will be 50 °C?
I highly appreciate your experienced comments
Take care
Shay
Coating factory Chemist - Carmiel Israel
Hi, Shay
I doubt that the problem is in the chromate step. My guess is that the zinc plating is too thin because the hardware items are harder steel (higher carbon) than the steel plates. Cyanide zinc is known for poorly plating on high carbon steel due to an issue with hydrogen overvoltage. Please check the thickness of the zinc plating.
If you decide to apply a sealer, yes, there should be rinsing after the passivate, and slightly warm would be good -- but 50 °C is probably too hot and will wash away some of the conversion coating.
Regards,
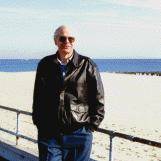
Ted Mooney, P.E.
Striving to live Aloha
(Ted can offer longterm or instant help)
finishing.com - Pine Beach, New Jersey
February 21, 2011
Dear TED, thanks for the time you took to answer to my question; I find your site excellent and resourceful.
My process: RoHS on cyanide Zn coated bolts.
Since cyanide Zn process does not plate well on high carbon containing steel,
1. Would you suggest alkaline Zn or FeZn plating? I have access to these processes!
2. You claimed that the Zn plating was too thin, what would be the max coat that will not affect the screwing functionality of the bolts and nuts?
3. With respect to the sealer could you recommend a good sealer?
I wish to thank you for the excellent site you maintain. I have spent hours reading the comments. This was of substantial help.
Kind regards
Shay
Coating factory Chemist - Carmiel Israel
Hi again Shay.
1. Acid zinc is usually used for high carbon steel. (In the old days a flash of cadmium was done before the cyanide zinc, but that is not RoHS compatible). I suspect that alkaline zinc will suffer the same issue as cyanide zinc, but I don't know about the zinc-iron.
2. I doubt that even .0005" would be an interference problem, but I'd bet you don't even have .0002". Bolts and nuts have a lot of surface area so they require high amperage or extended plating time. Half an hour would be an average plating time, and up to an hour is sometimes used for .0005"
3. I believe in using proprietary products. Whatever supplier is providing the trivalent chromate should offer a compatible sealer.
Good luck. Regards,
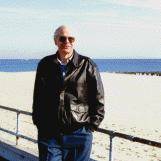
Ted Mooney, P.E.
Striving to live Aloha
(Ted can offer longterm or instant help)
finishing.com - Pine Beach, New Jersey
February 21, 2011
Q. Hi,
Please let me know, Is it possible to pass 96 hr SST with below said spec.
"Zinc plating with trivalent chromium passivation blue color 5-8 microns thick"
RFQ: And let me know, If any plater is available from Bangalore to met 96h SST with above spec.
Regards,
networks - Bangalore
April 16, 2012
Ed. note: This RFQ is outdated, but technical replies are welcome, and readers are encouraged to post their own RFQs. But no public commercial suggestions please ( huh? why?).
A. Dear Mr Basavaraja,
adv.
In response to your RFQ for a plater at Bangalore, I offer the services of my plating shops. Please get in touch.
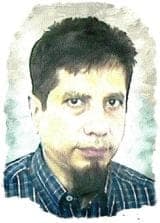
Khozem Vahaanwala
Saify Ind

Bengaluru, Karnataka, India
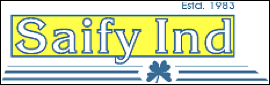
June 7, 2012
Q.
Dear Sirs,
Please suggest the curing time, required atmosphere, packing materials and checking methods for adhesion, peel off test for the components electroplated with acid zinc.
- Pune, Maharashtra, India
May 14, 2012
A. Hi Ajay. Please try to use the site's search engine because each of your questions is the topic for a long discussion thread here or a chapter in a plating text. Please find the best thread about each of your topics, as they have all been discussed at some length and it will probably be better to read the multiple opinions already expressed than to rely on a single quick and partial answer. Good luck.
Regards,
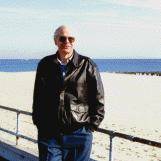
Ted Mooney, P.E.
Striving to live Aloha
(Ted can offer longterm or instant help)
finishing.com - Pine Beach, New Jersey
May 15, 2012
Q. sir,
I am working in a Sheet metal company. we have a problem for a recent project.
Material is CRCA 1.5 mm thk, D grade, IS 513.
1. The part is getting rusted and hence white patches are coming after plating (Zinc plating, blue passivation)
What we can do to avoid the rusting.
- Bangalore, Karnataka, India
September 30, 2012
A. Hi Athul.
We appended your inquiry to a thread which may begin to answer it for you. There are dozens more threads on the topic here if you try the search engine. You may alternately wish to retain a plating consultant, as it does take either a very long time and/or highly detailed knowledge to sort through the many open questions that your inquiry implies: substrate condition, thickness of plating, adequacy of the chromate conversion coating, drying, storage conditions, expected life, environmental conditions in your shop, etc. Good luck.
Or pick what you guess is the biggest cause of the problem, tell us about it, and we can hash it around here. Thanks.
Regards,
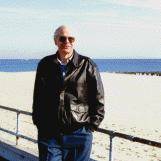
Ted Mooney, P.E.
Striving to live Aloha
(Ted can offer longterm or instant help)
finishing.com - Pine Beach, New Jersey
October 1, 2012
Blue Zinc Plating on EG material
Q. Hi All,
I found my part with coated blue zinc finishing on electrogalvanized material rusty after 3 month after process. Do you have any idea how this happened? Is it due to parts not fully cleaned.
Supplier Quality - Nibong Tebal, Penang Malaysia
January 29, 2018
A. Hi Luqmanul. We appended your inquiry to a thread about similar problems. The thing is, plating does not outright stop corrosion, it just slows it; so there are many possibilities … even including that the plating is perfect but environmental conditions meant it could not survive. What are the parts and what specification number were they supposed to be plated to please?
Regards,
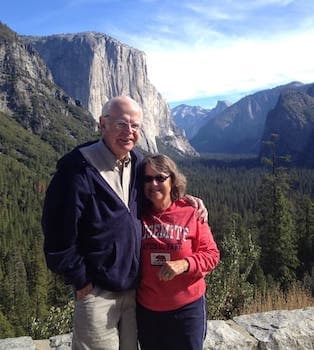
Ted Mooney, P.E. RET
Striving to live Aloha
(Ted can offer longterm or instant help)
finishing.com - Pine Beach, New Jersey
January 2018
White Powder Showing after Zinc Electroplating
Q. Good Day Sir,
We have 6000 Lt Acidic Tank for Electro zinc Plating on Long threaded Rods. On drying, finish has like powder on thread.
Please advise what to do.
Owner - Ludhiana. Punjab, INDIA
July 2, 2018
July 2018
? Hi Varun. May we infer that after the zinc plating you have a trivalent chromate conversion coating and a sealer and good rinsing? Have you been plating for a long time and this issue suddenly popped up? Thanks.
Regards,
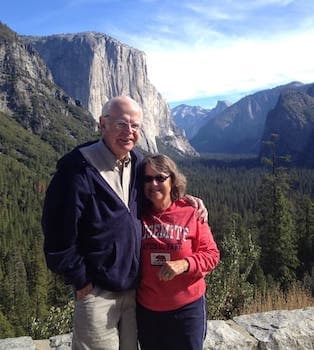
Ted Mooney, P.E. RET
Striving to live Aloha
(Ted can offer longterm or instant help)
finishing.com - Pine Beach, New Jersey
A. Dear Varun,
Normally the problem is because of poor rinsing and holding design in the jig.
Improve the rinsing, and design the part holding method to avoid solution carry-over.
Thanks
- Electronics City, Bangalore, India
July 21, 2018
Q. I have acid zinc solution. After the plating there is white spots on the metal welded piece. I tried many times but it doesn't go. Please give me the solution to this problem.
Pandu khandagale- Mumbai, India
July 28, 2018
A. Hi Pandu. In addition to this page we have four or five other threads on the subject of white spots on zinc plating which you might want to review by trying the search term "acid zinc white spots" in the google custom search engine. But please send some photos of the problem to for posting here so we can see what you are referring to and narrow down the possibilities. Thanks!
Regards,
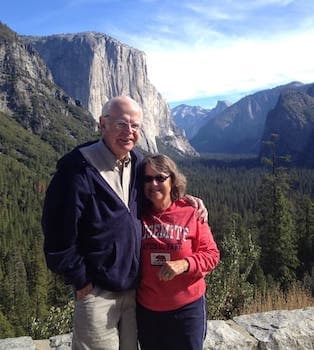
Ted Mooney, P.E. RET
Striving to live Aloha
(Ted can offer longterm or instant help)
finishing.com - Pine Beach, New Jersey
July 2018
Q, A, or Comment on THIS thread -or- Start a NEW Thread