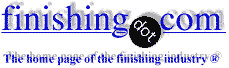
-----
Black passivation/chromate on zinc plating gets white rust
As per headline we have faced so many problem in Zinc with Black Chromating Layer, Major Problem is White rust appear in material in ware-house specially in rainy season, we have maintained 8 micron thickness of zinc in acid medium and this problem occurring mainly in Fasteners. We have taken all possible c'measure which would be somewhat responsible for white rust like:- we have control the iron ppm less than 50, fix up the dosage of Additive acc.to chemical supplier guidance in ml/1000 amp-hr, More frequent cleaning, maintained the conc. and pH, time according to chemical supplier technical data sheet, drying with maintaining the level of R.P.M < 400 along with 60 °C and digital time controller 3~4 minutes in Centrifugal-drier, then maintaining the curing time about 24 hrs. in open area,and dispatch in Closed vehicle and material pass the salt spray test at our hand & some out source lab. but always coming the problem at customer of white rust appear in packed poly-bag and failed in salt spray test. We have maintaining the spec. of white rust 72 hr. and red-rust of 240 hrs. Please suggest some technique by which we can avoid the discussed problem.
Anil Kumar KaushikPlating Shop Employee - Gurgaon, Haryana, India
2007
![]() |
A. As we know that the bright dip before black passivation solution contains nitric acid,which contaminates the passivation solution further if intermediate D.M.Water dips are not well maintained. Additionally after passivation, the components are to be washed thoroughly in D.M.Water before being dried in centrifugal drier at the temp. between 45 to 50 °C. - ghaziabad,UP, India 2007 2007 A. Anil, ![]() T.K. Mohan plating process supplier - Mumbai, India |
Q. My question is this:
We have farmed out plating of parts.
Parts are metal and plating is black zinc. However, during pick up of delivery to plating process, parts were wetted by rain inside the delivery truck and were not wiped immediately to dry off.
2 days passed and the parts occurs white rust.
My question is what is the possible cause of this?
Tri r - Philippines, Cavite
June 11, 2018
A. Hello Almira!
Black zinc (specially hex black chromate) is not a good corrosion resistant finish if not specified some topcoat, sealer or lacquer. My experience with acid zinc plating and ONLY hex black chromates isn't good, as I haven't seen more than 12 hours for white rust in neutral salt spray chamber test (ASTM B117).
I would say this is what this finish can withstand, and no more. If you specify any corrosion resistance, I think your supplier may have to make some adjustments to his process.
Best of luck!
TEL - N FERRARIS - Cañuelas, Buenos Aires, Argentina
June 13, 2018
Black passivation has chalking, pitting, atmospheric corrosion?
November 22, 2019Q. I'm located in Finland and producing components for automotive industry. We have steel parts that have nice looking black passivation, but after some time (a few weeks to a few months) they are showing white corrosion or chalking (we call it 'white rust'). The 'white rust' is normally forming on areas that are contact with outside atmosphere. Surface areas that are inside the component are still looking fine. What do you think could be the remedy for this problem?
Thanks
Saku UrponenQuality Engineer - Rauma, Finland
A. Hi Saku. Unfortunately, "black passivation" does not describe the underlying finish (zinc plating? zinc-iron plating? other?). I assume it is zinc plating or zinc-iron plating, and therefore we added your question to this thread.
When you say 'automotive components' I am not sure if you are a subcontractor for the automotive industry and are trying to supply OEM quality components, or you are offering automotive accessories which most people don't actually expect to last the full life of a modern automobile. My own feeling is that black passivation on exterior automotive components is unlikely to prove satisfactory for OEM components with exterior exposure on automobiles: road salt, gravel impingement, abrasion, and intense ultra violet exposure are major problems.
And in fact, the passivation (chromate conversion coating) is also worn off as well as exhibiting white rust. I am only looking at a picture, not a component, but from here it looks like the plating is chipped rather than pitted.
What can you tell us about the plating and passivation specification please?
Regards,
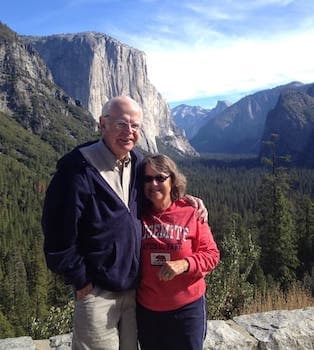
Ted Mooney, P.E. RET
Striving to live Aloha
(Ted can offer longterm or instant help)
finishing.com - Pine Beach, New Jersey
November 2019
----
Ed. note: We had enough questions about white rust on zinc plated components to make it a separate subject. So if you wish to read more, please see thread 26622, "White rust on zinc plated parts"
Q, A, or Comment on THIS thread -or- Start a NEW Thread