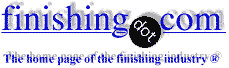
-----
Chromic Anodizing on Titanium Racks
1998
Q. In our recent experience in running 2024 aluminum through Type I chromic anodize is successful providing the rack is aluminum. But racking 2024 on titanium appears to cause pitting. Why?
Dissimilar metals and the high copper content of 2024 are obvious factors, but what is the specific connection?
Additionally, why does titanium maintain conductivity between runs without stripping while aluminum must be stripped between each load?
Regards,
M.A. PodlogarA. Mr. Podlogar,
You are actually experiencing a traditional problem in anodizing. In your case, pitting was mainly caused by galvanic effect between aluminum parts and titanium racks in the chromic acid solution with a certain amount of chloride ion. For some reason, your chromic acid has been contaminated with chlorides. Titanium has a more noble potential than aluminum, which leads to a galvanic cell in an electrolyte. Since the aluminum rack has almost the potential same as the aluminum parts, there is no galvanic effect between the aluminum parts and the aluminum rack. However, if chloride content is high enough, you will still encounter the pitting problem even if aluminum racks are used because chloride is very aggressive to attack aluminum base metal and anodized aluminum parts locally [please see topic 1541 for a discussion of chlorides in chromic acid anodizing]. Do not leave you racks in the anodizing tank without power or in the rinse tanks too long!
During anodizing, aluminum rack fingers are anodized along with workpieces, and aluminum coatings are nonconductive and relatively hard. As a result, it is necessary to strip the anodic coatings on the rack fingers for the subsequent anodizing use. In contrast to this, as long as a very thin and pore-free oxide forms on titanium rack finger surface, titanium fingers no longer anodize along with workpieces. Thin titanium oxide is still conductive due to electron-tunnel effect and also it is very soft. Furthermore, the thin titanium oxide on the rack fingers can be easily removed by loading and unloading. Therefore, it is not necessary to strip titanium racks for subsequent use.
Hope this can give you a little help.
Ling
Ling Hao- Grand Rapids, Michigan
1998
A. I'd like to add a few comments to add to Mr. Hao's advice. It should not be too difficult to determine at what point the pitting is occurring -- take parts off the racks after each step and inspect for pits. If indeed the pitting is occurring in the anodize tank, then chlorides are probably responsible. One reference I checked calls for .010 gm/l maximum chlorides. If chlorides are the problem, you may need to change your source of chromic acid, and get a chemical analysis from any potential source [please see topic 1541 for a discussion of chlorides in chromic acid anodizing].
The parts are most susceptible to galvanic corrosion in the rinse prior to anodize, where you have deoxided any atmospheric oxide, and the surface is as close as it can get to bare aluminum -- with copper present at the surface in the case of 2024. As Mr. Hao says, don't leave racks in rinse tanks (or any tank) longer than necessary, and especially this one.
Any anodizer should follow this axiom: all stainless or steel tanks should have have a pad of plastic or other non-conductive material at both ends of the tank where a rack would sit (not wood or other porous substance which would become conductive if it absorbs moisture). A Buss bar in contact with a metallic tank is guaranteed to have some galvanic current flow.
The pitting could be occurring in the seal bath. (Again, check parts before and after seal for pits). I experienced elimination of pitting of black dyed sulfuric anodized 2024 parts on titanium racks by hanging magnesium rods next to the racks- magnesium is even more anodic than aluminum, and robs the galvanic currents away from the parts. If the pitting is occurring in the seal, and if you don't have chlorides in your seal, this trick would probably work in your case. Hang the Mg rods on after anodizing.
Phil Johnson
- Madison Heights, Michigan
1998
A. The above comments really cover the story. I have used magnesium bars also for aluminum color anodizing on titanium racks, and they work well. Be sure that the mag bars do not contact the tank floor or sides. There is also a product that is available for this purpose which actually reverses the flow of electrons which are created by galvanic coupling reactions. I have seen it used and is called Pitstop. One must be sure to correctly size it to work. It is similar to a trickle battery charger. One further note, I have usually only experienced galvanic coupling in rinses when rinse tanks were used for staging purposes. Typically, the pitting that aggravated, was in the seals.
The pitting I have seen from chlorides occurred at 45 ppm, or 45 mg/l, during a 50 minute anodize cycle.
Ward Barcafer, CEFaerospace - Wichita, Kansas
1998
Phil is right. Your first two steps will need to be
(1) identifying the step at which the galvanic corrosion first appears
(2) putting a plastic pad at each end of your dye, seal, and rinse tanks. This pad will allow you separation between the tank and the bar of racks. These pads can be cut to an exact fit by your maintenance staff, and this is the least costly (and most likely) way to begin the process of eliminating the problem. I have experienced dissimilar metal corrosion (galvanic corrosion) before, and both times the problem was eliminated in a seal bath and a dye bath by the addition of pads.
I have also seen this problem before with 7075 being racked on Titanium for both Type I and Type II Anodizing.
Automatic Anodizing
Chicago, Illinois

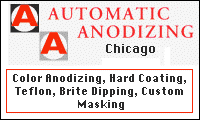
April 6, 2010
p
Multiple threads merged: please forgive chronology errors and repetition 🙂
Q. We try to adopt the use of Titanium racking in Chromic Acid Anodizing.
The problem is that the Titanium racks draw current by themselves, large amounts of current and the capacity of our rectifier is highly consumed by the racks.
Can you possibly give us some advise on how can we deal with this problem?
Zissis Vassilis- Athens Greece
1999
A. The best way would be to dip coat the racks in plastisol. Alternative would be to spray plastisol coat. That is a slightly different product. It is a pain to apply, but can be done if you exactly follow the instructions. It will require masking off part of your rack as it is moderately difficult to remove.
Other vinyl type pain on coatings may do ok also. Tolber, a div of Pyramid plastics, a div of Michigan chrome and chemical (Hope AR) makes a product called Super XP 2000 that is quite good. There is probably a similar product sold in Europe.
James Watts- Navarre, Florida
1999
Multiple threads merged: please forgive chronology errors and repetition 🙂
Q. What happens when titanium racks are used in chromic acid anodize? Do they draw current? A lot of current? If so, do the parts get less coating than they would on aluminum racks? Is it a bad idea to use titanium racks in chromic anodize?
Kent KesslerSeattle, Washington
1999
1999
A. My opinion.
1. Ti racks anodize with a very thin coating.
2. They draw current.
3. The amount is relative. If you have an excess of power supply, it just costs a few cents. If your power supply is marginal, you will occasionally not be able to ramp up the voltage without overloading the power supply.
4. The parts will get identical coating if the cross section area is large enough to carry the load. Ti is a poor conductor compared to aluminum.
5. Aluminum racks are cheaper but do not last anywhere near as long.
6. You generate more waste stripping aluminum racks than Ti.
7. I like Ti racks for all uses except large area parts, which Ti has a problem with its ability to carry the load. The cost and the wt of the rack becomes prohibitive.
- Navarre, Florida
A. I usually value Jim's "opinions" and his answer here once again hits the nail on the head. I'd just like to add that since titanium is a relatively poor conductor of electricity as compared to aluminum, titanium racks will actually draw less current than aluminum racks. Also, unless you are processing your parts through some highly active nitric/HF bath, after the first time through the anodizing cycle, the amount of current draw of titanium will drop off dramatically, as the titanium does develop an anodic oxide while the parts are anodizing. This oxide will get thicker each time through until it reaches a limiting point. This oxide is very brittle and easily scratches off at the contact points. Chromic acid anodizing is almost always done by voltage anyway, so your rectifier will automatically adjust itself to the proper current draw. I will add one comment about aluminum racks. The chromic acid anodic coating is very thin, as compared to sulfuric anodized coatings, and is therefore very easy to strip. Some anodizers make the mistake of putting racks in an etch bath for several minutes to strip, as is required for sulfuric anodize, but a chromic acid coating will strip in less than a minute. Leaving the racks in the etch longer dramatically reduces their life. A chromic-phosphoric strip solution, discussed several times at this site, will prolong Al rack life even more.
Phil Johnson
- Madison Heights, Michigan
1999
Q. Can I use stainless steel fixture to hold the part during chromic acid anodising?
S K Samy- Bangalore, Karnataka, India
April 6, 2018
A. Hi Samy. You had posted this question on a thread about anodizing of stainless steel, but I think you are actually asking about chromic acid anodizing of aluminum, not stainless steel?
As you will read here, either aluminum or titanium can be used for the fixtures (anodizing racks), but not stainless steel.
Regards,
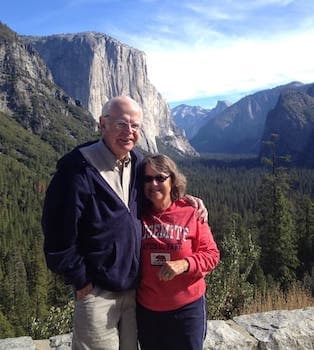
Ted Mooney, P.E. RET
Striving to live Aloha
(Ted can offer longterm or instant help)
finishing.com - Pine Beach, New Jersey
April 2018
Q, A, or Comment on THIS thread -or- Start a NEW Thread