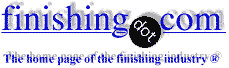
-----
Matte Silver Plating Q&A. Problems & Solutions. QQ-S-365
Q. I have to silver plate Aluminum 6160-T651 and Invar 36 to be used in high frequency telecommunications equipment. Should the base metal be plated with electroless nickel or copper and why? Will these migrate through the silver? I had parts that came in certified QQ-S-365
[from DLA]
. The chromate makes them unusable.
1) It there an in-house test we can do to tell which parts have the chromate and which have bare silver?
2)Can we strip the parts and re-plate them to the same desired finish?
Is there a protective finish that will degrade the conductivity less than chromate? Is matte finish more conductive than the bright and semi-bright?
- Palo Alto, California
2000
A. Dear Steve
For high frequency telecommunication parts a matte finish is better than a bright or semi bright. The best is a silver bath without any organics or metallic (except silver naturally) components. The deadening of high frequency current strongly depends on the conductivity of the surface so any passivation you use will increase deadening. Regards Marcus
- Sachseln Switzerland
2000
Q. Hello Marcus Hahn,
Just want to know if the silver plating QQ-S-365D Type 3 Grade B can have a nickel undercoating? If so, what is the preferred thickness? How do I test on silver after finishing?
Thanks and best regards,
Tony
I.E.T.I - Manila, Philippines
2005
Anti-Tarnish Finish for Silver - Electronics
2000Q. I am an Mechanical Engineer in the electronics industry and I am looking for a long term Anti-tarnish finish for silver. The application is on connector contacts. Base metal is Beryllium copper, finish is currently
1. Nickel plate 100-200 microinches per FED-QQN-290 (replaced by AMSQQN290)
.
2. Silver plate 50-125 microinches per QQ-S-365.
3. Then 2 Minute anti-tarnish immersion in Tarniban.
I found that Tarniban is a temporary anti-tarnish finish, mostly for prolonging shelf life.
I know that QQ-S-365, grade A requires a tarnish-resistant treatment of chromate. Would this be the best finish for electrical contacts and the body of test connectors that are handled often?
- Kent, Washington USA
A. Hi Chris. I'm not a contacts/connectors engineer, but I don't know why a flash of rhodium plating over the silver would not be an ideal anti-tarnish treatment for connector contacts. If long life is required, maybe silver plating then nickel, then rhodium. These days one needs to worry about suggesting hexavalent chromium conversion coatings on parts "that are handled often".
Regards,
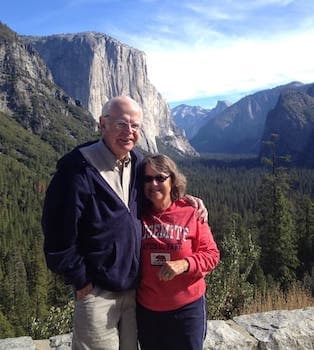
Ted Mooney, P.E. RET
Striving to live Aloha
(Ted is available for instant or longterm help)
finishing.com - Pine Beach, New Jersey
What is the Silver QQ-S-365? How do I test on silver after finishing
Q. Our silver finishing process is a 2-step procedure. I would like to know of the Silver QQ-S-365 test and how to perform it on some of our product after the finishing process to gauge its tarnish resistance.
Eagerly awaiting any suggestions, info or thoughts.
Thanks,
Jody Coyote - Eugene, Oregon
2005
A. Hi Israel. It's not exactly a test; QQ-S-365 [from DLA] is a Federal Specification and you can download and read it. Only platings with supplementary chromate anti-tarnish treatments (Grade A) are tested for tarnish resistance, and such treatments are probably inappropriate for anything having to do with jewelry.
If you need tarnish resistance you are probably limited to rhodium plating or organic clearcoats.
P.S: That spec was cancelled in 2001, with a note that "Users may consult ASTM B700"
Regards,
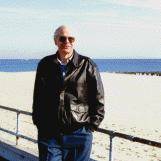
Ted Mooney, P.E.
Striving to live Aloha
(Ted is available for instant or longterm help)
finishing.com - Pine Beach, New Jersey
Q. I am not in the plating business myself but my company manufactures electronic microwave (waveguide) components that need to be silver plated per spec: QQ-S-365 [from DLA] Type 2 Grade A.
The quality of the plating is very critical to meet the electrical performance of my product. We are dealing with 2 or 3 local plating shops and the quality varies between them although all say they fully comply with the specification. One new supplier asked me if the underplate should be sulfamate nickel or electroless nickel (base material being invar), I had no clue. Also, when the finish is matte I know the parts won't work well. I read that Type 2 Grade A means semi-bright finish with anti-tarnish, is there a better way to specify it? I know these may be trade secrets but my goal is to develop at least 2 reliable suppliers that I can turn to when I need this done fast and well.
Thanks
Millimeter Wave Technologies Inc. - Montreal, QC, Canada
2005
A. From what you say it looks like you are giving enough information for your platers to produce a consistent product. You may want to state a maximum roughness, this may help to make the product even more consistent.
You should also note that QQ-S-365 was cancelled in February 2001 and that the recommended specification to use is ASTM B700 (came straight off STINET, no secret inside information here). Don't know a lot about the ASTM, I haven't read it, but for future contracts you may wish to review this specification and see if it meets your needs.
As for undercoat, my preference is for electroplated nickel, electroless nickel should be perfectly acceptable though, preferably with a low phosphorus content. This part comes down to what you are used to using, I have always used an electroplated undercoat, hence my preference.
Aerospace - Yeovil, Somerset, UK
2005
A. I would agree with Brian that an electroplated nickel would be a good underplate. As for the surface finish, it will vary between plating shops, the main reason for this, is that different plating shops will use different suppliers for their plating solution, and so the chemical makeup will be different, i.e., brighteners and additives.
If you are getting a very dull, matte finish perhaps their plating solution was low on brightener that day? One of the components we make and plate is for smoke alarms, and they specify the finish must be "Bright and free of blisters"
Perhaps your company would benefit from a visit to the local plating shops to explain the components application and that it needs to have a bright finish and not dull; they will then know for next time they are plating to check their brighteners. Just some advice from my past experience with different finishes from different plating shops. Hope it helps you to understand a bit better why finishes of the same type still vary visually.
HV Wooding - Kent, UK
2005
A. I would suggest using a cyanide copper strike, followed by an acid copper for brightness (silver doesn't stick to nickel very well) this will eliminate adhesion and most likely brightness problems.
Gene C Johnson- Tucson, Arizona
2006
Multiple threads merged: please forgive chronology errors and repetition 🙂
Q. What is the spec for QQ-S-365 [from DLA] type I Grade B? I m a supplier in Asia and I'm currently looking for the detailed description for this type of silver plating. Please advise me on it. Thanks a lot!
Heather Huang- Taiwan
2005
A. Hello Heather,
The US government's ASSIST (Acquisition Streamlining and Standardization Information Site)web page is a great resource for finding those strange specs with a SS or QQ or LL, etc.
I ran a quick search of QQ-S-365 and a result came back that said revision D was discontinued in 2001:
http://assist2.daps.dla.mil/quicksearch/basic_profile.cfm?ident_number=50980
Notice the document refers you to ASTM B700.
Good luck,
G. J. Nikolas &Co.,Inc.

Bellwood, Illinois
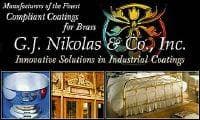
2005
Silver plating over silver electroform - decorative articles and figurines
April 26, 2009Hello !
We are engaged in silver electroforming. We form the metal over a wax mandrel - silver plate it to approx. 250/300 microns - dewax the article to get a hollow silver article.
We are not facing any problem in this process.
My problem begins after dewax. We offer a matte finish.
To achieve the matte finish we sandblast the article and then electroplate silver over silver in a cyanide bath (160/170 KCN - 25/20 AG - 80/90 Carbonate + Silver brightener and starters) to get the final finish.
We do the following process for electroplating (after the article is electroformed):
1. Sand blast
2. Clean with DM water
3. Strike silver (4/5 V - 30 seconds)
4. Plate silver (0.5 volts - 2/4 AMPS. for 5-8 minutes)
We are getting yellow and sometimes black spots after electroplating. We want to achieve bright plating on the surface.
Please advise how to correct the process.
Thanking you in anticipation.
With Kind Regards,
plating shop employee - Bhavnagar, Gujarat, India
Matte silver bath problem
Q. Dear All,
I am having a problem in my silver plating bath which is a typical potassium cyanide bath with no brighteners used because the requirement is Matte finish, quality was fine all these days and bath was idle for two days, later when we resumed the production we found the plating coming very bright a glossy finish like and peels off,
we checked the carbonates also it is 70 gpl .
we use silver strike also to avoid immersion coating.
what might be the cause? will the carbonates results in such a bright finish? followed by plating peel-off?
employee - India
December 29, 2010
A. Hi Sam,
Carbonate tolerance normally can up to around 150 g/l. The problem could be due to organic drag-in, free cyanide, pH and/or temp out of control.
Regards,
David
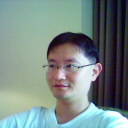
David Shiu
- Singapore
December 30, 2010
Q. Looking for anti-tarnish plating per QQ-S-365 that can withstand high temperature up to 450 °F and that is applied anodically.
Brijesh Patel- LA, California, USA
January 19, 2018
Hi Brijesh. Please detail your situation. It is hard for me to understand why it is a necessity that the anti-tarnish coating you want must be applied anodically :-)
Are you an end user seeking a plating shop to apply this coating on your parts? Are you a plating shop looking to buy this process chemistry so you can apply it? Are you a generic chemical supplier trying to supply something to plating shops similar to what they are currently buying from others? Thanks.
Regards,
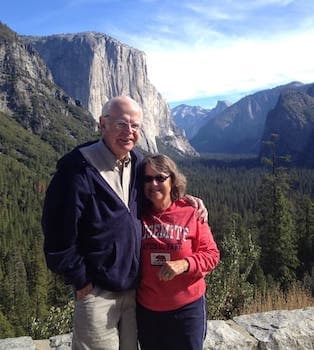
Ted Mooney, P.E. RET
Striving to live Aloha
(Ted is available for instant or longterm help)
finishing.com - Pine Beach, New Jersey
January 2018
RFQ: Thanks for your reply. I am end user seeking a plating shop to apply this anti-tarnish coating on parts.
After plating part per QQ-S-365, some area of part is painted with black paint that needs baking at 450 °F for proper adhesion. With my little understanding of anti-tarnish plating, I believe most organic type anti-tarnish plating are applied by dipping process and usually disintegrates or evaporates at approx. 170 °F. I believe anti-tarnish plating applied through anodic or electrolytic process tend to have high temp tolerance and that is why I am looking for anti-tarnish plating that is applied through anodic process.
- LA, California, USA
January 22, 2018
by Biestek & Weber
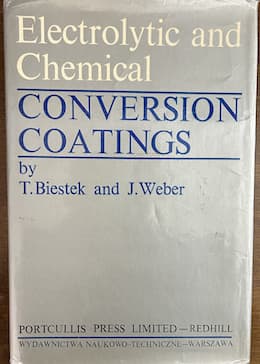
on AbeBooks
or Amazon
(affil link)
A. Hi again. Biestek & Weber says that electrochemical chromate conversion coatings on silver are indeed thicker and more stable. I don't have any experience with exposing them to 450 °F but I also don't have any reason to suspect that electrochemical chromate coatings can sustain that temperature. As a point of information the work is cathodic, not anodic, for these treatments. Good luck!
Regards,
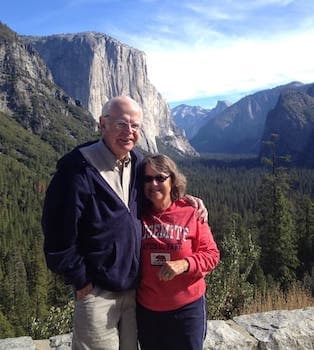
Ted Mooney, P.E. RET
Striving to live Aloha
(Ted is available for instant or longterm help)
finishing.com - Pine Beach, New Jersey
Q. I would like some help with silver plating. I need to be able to plate an even, matte, white finish. I am fairly new in the field of plating, only having done some simple homemade copper and nickel plating. I know the high quantity finish I am looking for will require extensive surface preparation and masking, as well as some experimentation.
The main hurdle is however the solution to plate a white silver deposit. Is there special chemistry involved or is it as simple as modifying the voltage or current density to get the desired finish? I have looked around to find solutions that will plate as I desire however they all seem to contain brightener to get a "bright" silver finish.
Any help or guidance would be greatly appreciated,
- Trenton, Ontario, Canada
May 27, 2020
A. Hello Liam,
Sorry I'm getting back to you so late, I was on vacation. Have you contacted a precious metals supplier for electroplating? There are non cyanide silver plating solutions that can produce a matte finish. Most platers have been getting away from cyanide based solutions, but they will also produce a matte finish without the use of brighteners. What you have to consider is the brightness of the underlying metal, especially if the silver coating is very thin. A thin coating is a direct reflection on whatever the underplate is. Matte Nickel is a good barrier plate in this case, with ample plating thickness of course. The nickel will prevent diffusion of deposits into the silver layer after a short period of end use. Good luck!
- Winston Salem, North Carolina USA
June 14, 2020
Q, A, or Comment on THIS thread -or- Start a NEW Thread