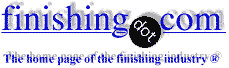
-----
Plating onto Magnesium? Q&A's

RFQ: Hello,
Looking for someone to do a 1 piece touch up on a part that is already machined and electroless nickeled. Part will be modified and then needs to be touched up. Looking for quick quote and quick turn around.
- Tucson, AZ
March 21, 2022
privately respond to this RFQ
Ed. note: As always, gentle readers: technical replies in public and commercial replies in private please (huh? why?)
⇩ Related postings, oldest first ⇩
Q. Does anyone have any experience plating (EN, in this case) onto magnesium? If so, could you recommend a process?
Ken Rosenblumfinishing shop - Minneapolis, Minnesota
1995
A. Hi, Ken. I don't have personal experience in this, but Atotech's MagENta process for electroless nickel on magnesium has a descriptive name that is very easy to remember, and may be a starting point to learn what is special about magnesium when it comes to EN plating. Other major vendors presumably also offer similar processes. Good luck.
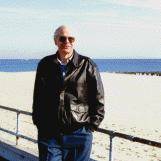
Ted Mooney, P.E.
Striving to live Aloha
finishing.com - Pine Beach, New Jersey
1995
Q. I am learning about how unstable magnesium is just in the air of a shop environment. We currently use a special oil between processes prior to dichromate to provide protection from reactions with moisture. Can anyone tell me if VCI bags will provide the right protection in lieu of the messier oils?
Eric Schneider1998
A. Eric,
My company does finishing of aluminum & magnesium, including dichromate, and mag anodize among others.
You are right about mag corroding very easy - sometimes parts will corrode in shipment from the mfgr. to us.
We always advise our customers when sending in Mag parts for processing that they should be packed with a light machine oil on the parts & desiccant packages should be used in the packaging to absorb moisture.
David A. Kraft- Long Island City, New York
1998
Q. What magnesium alloys are most used in automobiles?
What are some of the problems that occur with corrosion of magnesium alloys used in automobiles?
What are some of the solutions to these problems?
University of Arkansas, Engineering Research Center - Fayetteville, Arkansas
1998
A. Good corrosion and protective qualities are the responsibility of the casting maker. Packaging, preservation, and proper process control during melting all contribute to end quality.
Too often in the past, foundries have been their own worst enemy with regards to the prevention of corrosion.
New alloys of high purity corrode slower, since trace elements causing galvanic corrosion are reduced in these alloys. AZ91E is a good choice for prototyping auto parts that will have good corrosion resistance.
Mark A. Vecchiarelli- Enfield, Connecticut
1998
Chrome plating of magnesium AZ31B
Q. I am currently looking for a plating house that can chrome plate magnesium AZ31B alloy...Living near Spokane Wa., I have had numerous unsuccessful attempts from the local plating houses...Any help , please advise...AA
Arndt AndersonShark Byte Eng.
1998
Ed. note: This RFQ is outdated, but technical replies are welcome, and readers are encouraged to post their own RFQs. But no public commercial suggestions please ( huh? why?).
by G. G. Gawrilov
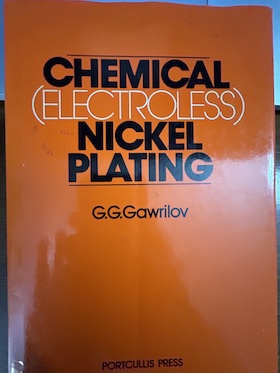
on AbeBooks
or eBay or
Amazon
(affil link)
A. I have some information on how to process magnesium. Maybe you can help your local platers get the process right. Let me know if you want the information.
What are these parts? Would it be worth it to ship them some distance to a plater who can do the job?
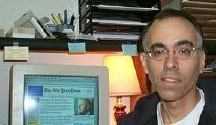

Tom Pullizzi
Falls Township, Pennsylvania
Q. I would be interested in the same pickling process and yes this would be worth it to me to send at a distance. The material is magnesium sheets measuring 48 x 144 inches and different size thickness from .032 to .063.
regards
bert lecuonahi-tech metals, inc
1998
Ed. note: This RFQ is outdated, but technical replies are welcome, and readers are encouraged to post their own RFQs. But no public commercial suggestions please ( huh? why?).
? I am just curious to know why is magnesium alloy chrome plated? Is it chromate conversion or just chromium.
Mandar Sunthankar- Fort Collins, Colorado
1998
Q. I'm having problems coming up with a process for plating over magnesium. I'm currently using a zincate (non current) for bonding. From there I am trying an alkaline copper strike then sulfamate nickel. The problem I am having is the copper is having bad adhesion on the zincate. Any help would be helpful.
mike crabtree- Raleigh, North Carolina
1998
A. Hi, Mike.
I can't guarantee it, but I think you'll have less problems with an alkaline electroless nickel strike between the zincate and the sulfamate nickel than you are having with the alkaline copper plating. Good luck.
Regards,
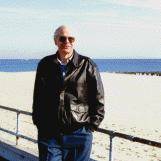
Ted Mooney, P.E.
Striving to live Aloha
finishing.com - Pine Beach, New Jersey
Multiple threads merged: please forgive chronology errors and repetition 🙂
Q. I have had some inquiries for plating on magnesium. Can anyone suggest some good sources for processing and some of the "Watchouts" attached to the process. My in-house library doesn't have much. Any help is welcome. Chris
Chris Hammer- WNY, New Jersey
1999
A. Don't forget that chips and shavings are flammable if you are doing any mechanical work on the parts. Magnesium parts must either be zincated or nickel plated, and in either case the zincating or nickel plating must be preceded by rather detailed pickling sequences. Volume 5: Surface Engineering of the ASM Metals Handbook has a great chapter on Magnesium Finishing--at least my ninth edition does.
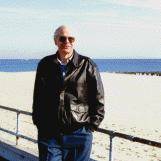
Ted Mooney, P.E.
Striving to live Aloha
finishing.com - Pine Beach, New Jersey
1999
Q. I would like more information on the electro plating of magnesium, also a supplier of mag sleeves for chemical etching. What is the annealing temperature for mag and the procedure to follow. Please help.
izak meyer supreme engravers - cape town. south africa1999
Q. I have been told that "there is a new magnesium alloy named AZ31X that is available in sheet which is more resistant to sea water atmosphere" Where can I have info on that ? Who is a supplier of that?
Gilles Saucier- Canada
1999
Q. I would like some information on corrosion resistant coatings for magnesium parts. Our company used to use magnesium for some engine components in the past (covers and other lightly stressed components), but corrosion was a massive problem, especially when parts became 'dinged' or scratched. What we are after is ideally a hard-wearing (or tough) corrosion resistant coating so that we might use magnesium components again. It would come into contact with air, de-ionised water, maybe water-glycol (engine coolant), fuel, oil etc.
I have seen a transparent gold coating, similar in appearance to TiN on some Italian motorbike mag wheels which looks very hard wearing, but I don't know where to start looking for this. The wheels were painted over the top of this, and so I don't know if the coating on its own would be sufficient.
It would be nice if the coating were very thin so that it didn't make too much difference to the fits of machined components. I would really appreciate any help that could be offered.
Wayne Ward- England
1999
A. Electroless nickel plating sounds like it meets most of your needs, Wayne.
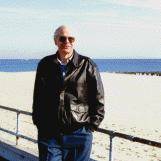
Ted Mooney, P.E.
Striving to live Aloha
finishing.com - Pine Beach, New Jersey
1999
1999
adv.
Luke Engineering offers a patented hard anodic coating for magnesium, Magoxid-Coat(R) which is significantly more wear and corrosion resistant than other widely commercialized anodic coatings for magnesium. A typical coating thickness is 25 µm (1 mil) with one half penetration and one half build-up. It can stand alone or be used as a paint base. A number of manufacturers of superchargers for drag racing use this hardcoating on their magnesium housings and end plates.
Luke Engineering & Mfg. Co. Inc.

Wadsworth, Ohio
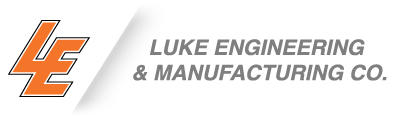
A. The gold coating on the Italian wheel might have been ZrN, used extensively for decorative coatings. It is very corrosion resistant if deposited correctly, i.e., by unbalanced magnetron sputtering. ZrN is also very hard and wear resistant, used extensively on cutting tools.
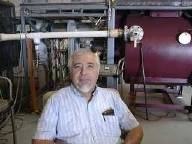
Jim Treglio - scwineryreview.com
PVD Consultant & Wine Lover
San Diego, California
1999
Plating onto Magnesium AZ91D
Q. My Chief Engineer recently asked me to search for information to coat magnesium AZ91D and it is for a major customer. Please help and advise what are the various methods and the best in the industries.
Alan Delonmicro electronics- Singapore
2001
A. There are two methods to plate Mg. One method is zincate, cyanide copper plate, than plate with whatever metal. Another method is to activate then Electroless nickel plate, then plate with whatever metal. Both processes use a cleaner and etch step.
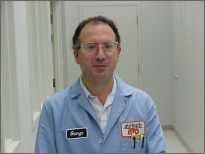
George Shahin
Atotech - Rock Hill, South Carolina
2001
Multiple threads merged: please forgive chronology errors and repetition 🙂
Plating Magnesium AZ91D for corrosion resistance, EMI shielding and decorative
Q. We are looking for ways and methods that are available in the industries to plate or coat Magnesium AZ91D for corrosion resistance, EMI shielding and decorative. Main application: microelectronics and mobile phone.
Chua Kok SiongNTU - Singapore
2001
A. One cannot plate magnesium out of aqueous solutions. The oxidation potential of the magnesium is too large. Clean magnesium will react slowly with water (mag wheels and mag parts are actually alloyed). You can try a dipping process.
Anthony Xidis- Minneapolis, Minnesota
2001
----
Ed. note: We read it that Chua wishes to plate onto magnesium rather than to electrodeposit magnesium.
A. AZ91D is used as diecast, so that has much micro pin hole during die casting process. The cast is observed as sponge structure by electron microscope. The porous structure is easy attacked by chemical in plating or aquatic phosphate treatment etc.
If you want to prevent the corrosion problems, should get sound structure. You can check by gravity measurement or by microstructure.
In my experience, the rolled sheet or extruded plate are better than diecast. For example, AZ31B or AM20 etc.
Simon KangHyung Kim- Suwon, Kyungki, South Korea
2003
Q. I am looking for acceptable plating techniques for magnesium die casted/thixomolded materials. Could someone please advise on this or provide some companies we could contact relative to this?
Barry Bowers- Binghamton, New York
2001
A. Depending on your finish requirements, there are several options for plating on magnesium. You should also contact your thixomolder directly with your specific requirements.
Jerry English- Schaumburg, Illinois USA
2002
Q. I am looking for a general guideline, or outline, of all the possible alternatives for coating and finishing magnesium alloys. Our goal is to use magnesium as a base metal for some of our products, which are designed to be both aesthetically pleasing and corrosion resistant.
The products will have potentially intricate design detail, and we will need to offer metallic finishes, dyed metallic finishes, and painted surfaces. There will potentially be dissimilar materials, so protection from galvanic reactions will be necessary.
A spread sheet of the possibilities would be nice, if anyone has one--or direction to a good resource on magnesium finishing would be very helpful. We would like to put together a test plan to evaluate all, or as much of it as possible, that is out there to help guide our decisions. At this time, cost is not an issue.
Davin S [last name deleted for privacy by Editor]Oakley - Foothill Ranch, California
2001
A. I reviewed some early work in "Finishing of Magnesium"


Tom Pullizzi
Falls Township, Pennsylvania
2001
A. Magnesium has been around a long time, Davin, but with the explosive growth in cell phones and portable electronic devices, interest has certainly been renewed!
Tom Pullizzi put together his excellent "Finishing of Magnesium"; Fred Pearlstein, in his usual fine style, covered anodic coatings for magnesium in "Selection and Application of Inorganic Finishes" in the March 1979 issue of Plating & Surface Finishing, discussing them as both final finishes and bases for paint. He found them to be "considerably more protective" than painted conversion coatings.
Another possibility is electroless nickel plating, mentioned earlier in the thread.
Finally, magnesium can be electroplated with any plateable metal you wish ... although the sequence to get there can be complex :-)
Good luck.
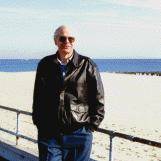
Ted Mooney, P.E.
Striving to live Aloha
finishing.com - Pine Beach, New Jersey
2001
by Dow Chemical Co.
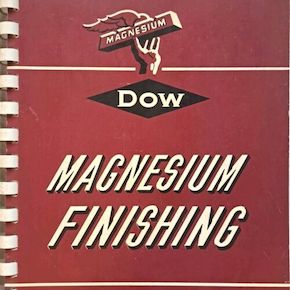
is sometimes available on
AbeBooks,
eBay, or
Amazon
... but if not, you can find libraries which have copies on WorldCat.org
(affil link)
A. Try the ASM Surface Engineering Handbook, it has a complete chapter on Magnesium surface treatment.
Good Luck.
S. Y. Yuen- Hong Kong, China
2001
A. Dow Chemical Co. did much of the early work on finishes for magnesium. Their handbook, "Magnesium Finishing", although old and out of print, is still a coveted bible to many finishers. It covers cleaning, etching, conversion coatings, anodizing, and plating. These Dow coatings are still widely used in industry today even though Dow has exited the business and the handbooks have not been available for many years. Recently, new anodic coatings have been developed for magnesium. These offer improved corrosion and wear resistance over those older coatings at competitive costs.
adv.
Magoxid-Coat®,produced in the United States, by Luke Engineering is one of these coatings.
Luke Engineering & Mfg. Co. Inc.

Wadsworth, Ohio
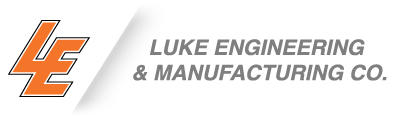
2001
A. Mg alloys can be protected in salt spray environment with pure aluminum coatings. Scribed samples coated with Al have survived ASTM B117 tests of up to 196 hours. This contrasts to less than 20 hours for the standard conversion coating. Still the coating must be completely hermetic, as the galvanic potential between Al and Mg is considerable. Thus the complex shape of a product could be a problem.
Howard Gabel- Santa Barbara, California, USA
2007
Q. Can anyone help with a prepping process for electroless nickel on magnesium? I understand that magnesium does not react well with any acids. I currently am plating nickel on aluminum. Can magnesium be processed on this line?
Regards,
Casey Weizel- Minneapolis, Minnesota, U.S.A.
2003
A. Hi, Casey
If the line includes zincating and an alkaline nickel strike, I think there's a good chance. Best of luck.
Regards,
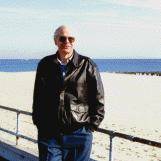
Ted Mooney, P.E.
Striving to live Aloha
finishing.com - Pine Beach, New Jersey
2003
Q. I hope to know about plating methods on magnesium. Could you tell me the plating methods?
Looking for good answer....
- ANSAN, EE, KOREA
2003
A. Magnesium can be plated by either using the zincate route or by direct plating. The zincate path uses an alkaline cleaner, followed by a chromic acid dip and another dip in phosphoric acid and fluoride. This is followed by a fluoride loaded zincate bath and Rochelle copper to about 5µm. The magnesium is then plated in electroless nickel.
The direct plating path is an alkaline soak, followed by a dip in 150 g/l CrO3 with a proprietary additive. This is followed by another dip in 15% HF at 25 °C and direct electroless nickel. The direct electroless nickel is a mixture of NiCO3/HF/ citric acid /NH3HF/ sodium hypophosphite/ NH4OH at about 85 °C
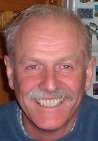
Trevor Crichton
R&D practical scientist
Chesham, Bucks, UK
Q. Thank you for the answer but I don't want to use HF. HF and NH4HF are very dangerous chemicals.
I'm looking for another methods.
Have a good day!
SE DO JANG [returning]- ANSAN, EE, KOREA
2003
A. Mr. Crichton is correct. Magnesium is a highly reactive metal and your ordinary cleaning and deoxidizing solutions cannot be used for magnesium. All the job-shop platers that I came in contact with use fluoride base predips, and use special electroless nickel containing fluoride to improve adhesion.
June Kimfine chemicals - Incheon, Korea
2003
Copper Plating on Magnesium is Blistering
Q. We are plating electroless nickel over copper-plated AZ-31B magnesium alloy. We've plated a certain machined housing about ten gajillion times and cannot get rid of the blistering problem. Same alloy, same customer, different housing and we have no blisters. We're degreasing with an alkaline cleaner, pickling with chromic acid solution (180 g/L CrO3), followed by an ammonium bifluoride/phosphoric acid activating solution, sodium phosphate/sodium carbonate/sodium fluoride "seal" and a fluoridated zincating process using zinc sulphate, sodium carbonate, sodium fluoride; pretty much the usual suspects, with the zincate temperature at 135 - 150. Any ideas on what we can do to get rid of the blisters? Is there a machining lubricant that is creeping out of the surface grain? I'm at my wit's end.
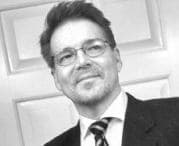
Randall Fowler - Fowler Industrial Plating, LLC
Cleveland, Tennessee, USA
2005
A. My guess is that the parts that blister have porosity. the smallest pores are often the worse because they entrap the first liquid they see. I suggest you try as the first step Hot, DI water
(Higher temperature than any other step in the process) about 30 seconds. Hot water will fill the pores and remain there throughout the processing, we hope.
If the parts have oil, a very light solvent followed by an alcohol rinse and dry. Then Hot DI water, etc. This process works well for castings of most metals.
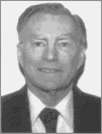
Don Baudrand
Consultant - Poulsbo, Washington
(Don is co-author of "Plating on Plastics" [on Amazon or AbeBooks affil links]
and "Plating ABS Plastics" [on Amazon or eBay or AbeBooks affil links])
2005
A. You said same alloy, same customer, different housing, no problem. How about the casting process and practice? Is it a fact that both parts are cast in the same way? Or could it be that one is cast in a permanent metallic mold and the other is sand cast? Or one needs a mold release because it's hard to eject and the other one ejects beautifully? Also, your suspicion of a cutting fluid contamination makes sense if it's not used in the part that gives no problem.
Guillermo MarrufoMonterrey, NL, Mexico
2005
Thanks to both of you for your advise. Our QC manager talked to the customer about the molding/machining process and we incorporated a hot DI and alcohol submersion procedure. End result; the parts were accepted. Once again, thanks a lot guys.
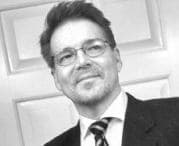
Randall Fowler - Fowler Industrial Plating, LLC
Cleveland, Tennessee, USA
2005
Is platinum the best plating for magnesium alloys?
Q. Dear Sir
I would like to know the best coating material on Magnesium alloys (AZ91D). Take for instance Nickel and platinum: what would be a best candidate for coating in characteristics and cost.
Yours,
Student - South Africa
2006
A. It is usually not possible to pick the best coating, Rasitilo, without considering the full host of circumstances & conditions. But nickel may as a general rule be more appropriate than platinum because, among other things, platinum is a precious metal more costly than gold, whereas nickel is not a precious metal. Some magnesium cell phone housings have been electroless nickel plated.
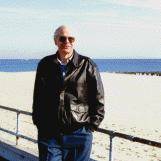
Ted Mooney, P.E.
Striving to live Aloha
finishing.com - Pine Beach, New Jersey
2006
Hard chromium plating of magnesium
Q. I have some machined magnesium parts that have a critical ID that was machined oversize. We're considering having the ID's hard chromium plated and then grinding them to size. Is this possible? I'm not sure if the magnesium is compatible with the hard chromium bath/process. If it is, then is there a special process that should be followed to accomplish our needs?
Blaine B. Boydcustomer - Eastlake, Ohio, USA
April 29, 2009
A. Whatever you do, it needs the blessing of the customer before you spend money on the fix.
If it is less than 0.003" on the diameter (0.0015" per side), I would choose EN because it is very uniform and would require little or no grinding. For chrome, I would not use less than 0.015 per side as your grinding setup needs to be nearly flawless in alignment to the original grind. Chrome dog bones on the ends and you will have quite a bit of grinding to do. Your grinders must be familiar with grinding chrome or they will use the wrong wheel or take too deep cuts and the chrome will probably peel.
- Navarre, Florida
May 1, 2009
A. Depending on the overall geometry of the part, how much metal you need to build-up and what your tolerances are, it might be possible to selectively brush plate that ID, perhaps even do it to size as-plated (no grinding or machining). The process is versatile and permits the deposition of a variety of metals whose chemical and mechanical properties can be selected to match or come closer to those of your base metal.
Guillermo MarrufoMonterrey, NL, Mexico
May 8, 2009
Blister issue on cyanide copper plated magnesium AZ91D
Q. Currently I had tried copper-EN plating on AZ91D.But after go through the pre-treatment the blister were appear during the immersion in the cyanide copper bath.Can anyone please advise why the blister appear during copper plated.
YC. samplating shop employee - KL, Malaysia
July 31, 2009
A. Don't forget that magnesium is not aluminium and only in some physical properties (mechanics, melting point, etc.) are the two metals similar, but their chemistry is quite different. For this reason, performance finishing methods are different. On the market, there are some technologies able to offer 1000 hours, or more, of salt spray resistance (Tagnite, Keronite, Anomag, SweetMag).
Aurel Crisan- Montreal, Quebec
May 26, 2011
Q. Will zinc immersion and copper strike make the surface of magnesium non-reactive so that I can coat other metals on it? I have tried with copper pyrophosphate, but it formed immersion coatings with zinc. Can you suggest some better methods?
Siddarth Kumar- Wichita, Kansas, US
November 5, 2012
Prep for Electroless nickel on Magnesium castings?
Q. I am looking for a dependable procedure to prep Magnesium castings for subsequent electroless nickel boron plating.
Chris Hammer- West New York, New Jersey usa
January 23, 2019
A. Hi Chris. Years ago Atotech offered their MagENta process. They might still, or their competitors might offer one. You're doing nickel boron rather than nickel phosphorous, but still the SDS or tech data sheet might offer a hint.
Other than that, we appended your question to a thread where Trevor Crichton seems to offer an authoritative answer to prepping the magnesium, but it does require fluoride. Good luck.
Regards,
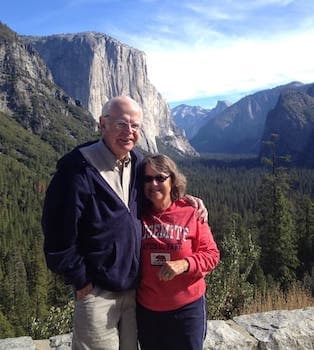
Ted Mooney, P.E. RET
Striving to live Aloha
finishing.com - Pine Beach, New Jersey
January 2019
Q. Hello everyone, I'm a hobbyist metal worker and looking into the idea of electroplating copper onto magnesium. Most of my electroplating experience is plating copper onto titanium, but if I understand things correctly my current method of using copper sulphate
⇦ on
eBay or
Amazon [affil links] in a weak sulfuric acid solution will not work due to the magnesium reacting with the acid. I had thought of neutralizing the acid in the solution and make an attempt but thought I would post a question here beforehand.
Is there any way magnesium can be copper electroplated in a normal shop environment?
- Grande Prairie, Alberta / Canada
November 25, 2019
November 2019
A. Hi Neil. I'm certainly not going to tell you it can't be done; it cam. But it is very difficult from at least four different perspectives which might discourage a nobbyist:
first, it requires dangerous chromic acid and fluorides in the pretreatment cycle;
9th Edition, Vol. 5
"Surface Cleaning, Finishing & Coating"
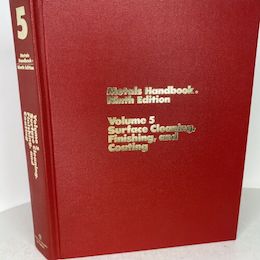
on eBay or Amazon
or AbeBooks
(affil link)
third, you can't plate acid copper onto the zinc because they are incompatible -- you must either use dangerous copper cyanide, or add the complexity of electroless nickel plating between the zincate and your copper;
fourth, the plating must be thick and pore-free or the magnesium will rapidly corrode because copper is so much more noble.
If you want to proceed anyway, you might get to a technical library for a copy of ASM Metals Handbook Volume 5, which has a 22-page chapter describing the difficulties and the solutions. Best of luck.
Regards,
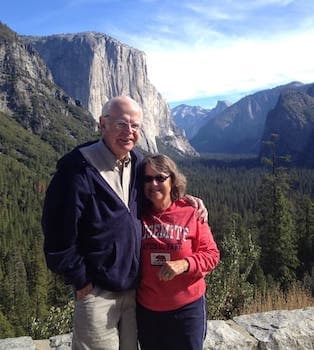
Ted Mooney, P.E. RET
Striving to live Aloha
finishing.com - Pine Beach, New Jersey
September 4, 2020
Q. Hi everybody,
it is a while I've been working in decorative electroplating but never had the chance of using Magnesium as base metal: now the time has come and I have very little knowledge of this metal and its behaviour (I always worked with brass and zamak ...).
What I would like to know, is whether it is possible to electroplate magnesium, and what would be the pretreatment needed to get the surface activated (as I suppose it is similar but not equal to aluminium?), then which plating steps are the most convenient.
Another thing I would like to know is what happens if the coating gets damaged and the magnesium underneath gets exposed.
Thank you so much for all the help you can give me about this subject, reference links to further explanations would be much appreciated!
Thanks again,
Elena
- Vicenza Italy
Q, A, or Comment on THIS thread -or- Start a NEW Thread