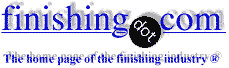
-----
Masking/stripping when chromate conversion and anodizing on same part
Quickstart:
A common need is for a single aluminum component to have anodizing in some areas but chromate conversion coating (Alodine & Iridite are trade names) in other areas. Consequently, a common question is which should be done first -- what is the proper sequence of operation?
Read on to learn that doing the chromating first may be the more robust process in the general case because precision masking will adhere better to a chromated surface than to a bare aluminum or anodized surface, but depending on the machining needs and machining sequence, anodizing first may be the better answer. By the end of this exhaustive discussion by industry experts, you will confidently know the best approach for your particular situation ...
Q. We have aluminium (usually 6082) that undergos machining, then black anodising, then post machining, followed by Trivalent chromate conversion on the newly exposed aluminium. I suspect that the part is being totally submersed in the chromate as we are finding issues with the anodising after the part has been cleaned in Acetone. The part becomes discoloured. Could the non-specific application of the chromate be the reason? What effect would the chromate have to the black anodising? I deduce from previous threads that the correct process would be to mask all the black anodising and selectively apply chromate conversion coating to the exposed aluminium?
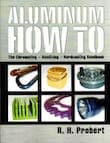
Aluminum How-To
"Chromating - Anodizing - Hardcoating"
by Robert Probert
Also available in Spanish
You'll love this book. Finishing.com has sold almost a thousand copies without a single return request :-)
Louis Kaltenrieder
Mechanical Design - Gauteng (South Africa)
January 20, 2025
A. Hi Louis,
If the acetone or chromating process is discoloring a properly anodized and sealed finish, then you'll have to change the sequence as you have described or as others suggest in this dialog. However, that's a big if. It seems very possible that the anodizing is not properly sealed, because acetone should not harm it.
I would suggest that you conduct some good seal quality testing on some parts after anodizing because your present sequence is the simplest and most economical if it works, and some experts in this thread tell us that it should be fine 🙂
Luck & Regards,
Ted Mooney, P.E. RET
Striving to live Aloha
(Ted can offer longterm or instant help)
finishing.com - Pine Beach, New Jersey
Q. Thanks Ted.
From prior experience I get the impression that the Chromate conversion coating over the anodising is causing some sort of reaction (?) with the anodising, maybe some sort of leaching process? We have followed this same process before but the whole part (including black anodising) was never totally chromated, but only applied to the bare aluminium surfaces (so masking used). Was hoping someone might have an explanation as to what is happening.
Mechanical Design - Gauteng, South Africa
A. Hi again Louis.
Some people feel that chromate will be deleterious to the anodizing, others claim that in their experience it is not a problem.
What I was trying to say is that if the anodizing is not properly sealed, other materials like acetone or chromate can certainly be expected leach it, and this may account for the differences in viewpoints.
So, before giving up on the process, the seal quality must be tested.
Luck & Regards,
Ted Mooney, P.E. RET
Striving to live Aloha
(Ted can offer longterm or instant help)
finishing.com - Pine Beach, New Jersey
A. Chromate conversion coating process usually includes the etching/deoxidation step before chromating. It certainly could leach the color of anodize.
Alex SirotaPlating Engineer - Lod, Israel
Multiple threads merged: please forgive chronology errors and repetition 🙂
Chromate, mask and anodize without stripping chromate first?
Q. On many jobs we chromate (aka Iridite or Alodine), then mask, then strip off chromate & then either hardcoat or anodize.
For a specific job, we are questioning what would happen if we anodize directly over a chromated surface, without stripping the chromate first. What effect would the chromate have on the resulting clear anodize?
- Long Island City, New York
2001
A. Good question Dave. I'm not really sure on that one. I may have to try it myself. One concern I would have would be dissolving a lot of hex-chrome in my anodize tank.
I am a little curious as to why you wouldn't want to remove the chromate prior to anodizing ... is it a finish, or a tolerance issue? Like your shop, our S.O.P. is to remove the chromate prior to anodizing. We really haven't noticed any finish, or dimensional issues arise from this practice.
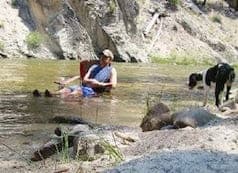
Marc Green
anodizer - Boise, Idaho
Does chromating aluminum first cause soft and powdery hardcoat?
Q. We have an aluminum part that had a chromate conversion coating applied and then some surfaces were black hard coat anodized. Can the anodization be done properly over an Iridite coating? If so, how will that hard coat differ from anodizing bare aluminum? The reasoning was that the internal sealing surfaces needed a thin surface treatment and the external surface needed a more durable surface treatment because it will be in seawater. The sealing surfaces were masked for the anodize. The black coating (if it is a hard coat anodize) looks soft and powder like. At least not a typical hard coat I've seen.
Any info is appreciated.
Treatment &
Finishing of
Aluminium and
Its Alloys"
by Wernick, Pinner
& Sheasby
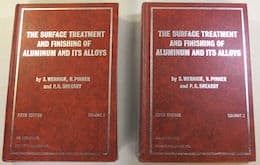
on eBay or Amazon
or AbeBooks
(affil link)
- St. Petersburg, Florida
2001
A. Hi Michael. You don't anodize on top of chromate conversion coating, but the pretreatment sequence for anodizing will likely strip the chromate such that you are anodizing onto bare aluminum. We appended your inquiry to a thread which shows the overall sequence to be common -- if it's done right :-)
I'm not clear on why your anodizing is soft and powder like, but it's not an inherent problem in the sequence; but perhaps the chrome you are stripping in the process is contaminating the tanks sufficiently to spoil their performance.
Regards,
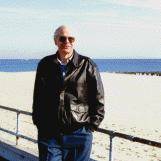
Ted Mooney, P.E.
Striving to live Aloha
(Ted can offer longterm or instant help)
finishing.com - Pine Beach, New Jersey
Multiple threads merged: please forgive chronology errors and repetition 🙂
Alodine after Anodizing
Q. Are there any limitations to Alodining over anodization? My application calls for black anodization (which is non electrically conductive) over 90% of the part for cosmetics and abrasion resistance, but the remaining 10% of the parts surfaces must be electrically conductive. To accomplish this, I plan on masking these surfaces during anodization, then Alodining the entire part.
Thanks
- San Jose, California, USA
2001
![]() |
A. Sean, - Santa Cruz, California, USA A. This operation is done very often. I would suggest a non-chrome material that will do the same thing as the Iridite/Alodine products. Might be a perfect fit for California. ![]() Drew Nosti, CEF Anodize USA ![]() Ladson, South Carolina ![]() A. Sean, - Palo Alto, California A. I've done it both ways, and prefer to chromate (Alodine) first, mask, THEN anodize. Depending on the type of masking you are doing (taping, painting); the chromated surface helps the adhesion of the maskant, especially for paint masking. ![]() Marc Green anodizer - Boise, Idaho |
Q. I have a machined aluminum 6061-T651 housing which needs a conductive coating (chromate conversion clear Iridite) for electrical purposes but also a hard anodizing to strengthen a few large fine tapped threads. Can I mask the part and perform both operations? I would prefer not to mask the part and perform a single finishing operation to both harden the threads and promote conductivity. Any suggests?
Thanks very much,
Jon Gallant- Ottawa, Ontario, Canada
2003
A. Hard anodizing will not strengthen threads. It will increase the wear resistance. That said, hard anodizing would not rank high on my list for threads since there is a rotational crushing effect that I think will cause the hard coat to not last well. If this is internal threads, why not heli-coils? If it is external, why not electroless nickel? But, in answer to your question, you are going to have to mask at least once. Typical is to chromate, mask and then anodize. The exact procedure will depend on the shop and the part. There is no 100% answer.
James Watts- Navarre, Florida
Q. We manufacture aluminum parts in various alloys, 1050, 5083, 6082, 7075 and Casting 357. The parts are sulfuric acid anodized and partly chromate conversion coated per MIL-C-5541 Class 3 for low electrical resistance in some areas (A).
Generally parts are supposed to be chromate conversion coated (Alodine 1200 or 1500) all over, then masked in Areas (A), and coating stripped from unmasked areas. Finally unmasked areas are anodized and masking removed.
One of our subcontractors claim that they have problems with masking (leakage, using lead tape) and stripping without using strong alkaline solutions like sodium hydroxide (due to long masking time) They want to mask and strip in deoxidizer within 10 minutes after drying of the chromate conversion coating.
Please recommend materials/procedures for:
1.Masking (usually flat surfaces around grounding points and mounting surfaces)
2.Stripping bath (type and immersion time).
3.How long (minimum) should the chromate "cure" before masking, and what is the maximum delay from chromating to stripping for a given stripping bath.
4.Our subcontractor suggests to "reverse" the process, i.e., mask the Areas (A), anodize the part, remove masking, and finally chromate the complete part (also on top of the anodizing) What will the effect be on the anodizing in this case? (corrosion resistance, etc.) Is this an acceptable practice in the aerospace industry?
- Kongsberg, Buskerud, Norway
2005
A. Dear Ola
I have a better idea, if it is possible on your parts.
Anodize the whole part and then machine the areas where you want electric conductivity. After this you chromate the part.
Best regards
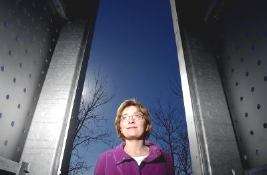
Anne Deacon Juhl
- - Trustrup Denmark
A. Chromate is still a gel at 10 minutes and masking is going to remove parts of that coating. Look at the tape when you take it off. If it is properly masked, the chromate can be removed in a caustic cleaner tank or some acid tanks without much problem. If they are having leakage problems with lead tape, they are not burnishing the tape edges with a wood or plastic stick. Leakage should be minor with lead tape. I would expect more problem with vinyl tape. There will always be a trace of leakage, but that tiny amount should not be a factor on an aerospace part.
I am not in love with chromating over anodizing as even a non etch cleaner will slightly attack the anodize. The acidity of the chromate tank is not going to help it either. If it passes salt spray on an every lot basis, it might be OK. The OEM procedure must be followed. What do they say?
- Navarre, Florida
A. I think your supplier is correct. His suggested process is easier, and will likely produce better quality. There are plastic film tapes which will hold up well in anodizing. Chromate conversion coating can be done after anodizing with no effect on a properly sealed anodize coating.
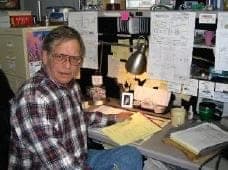
Jeffrey Holmes, CEF
Spartanburg, South Carolina
A. Ola
1 If the part is properly chromated, most plating tapes will adhere properly if not excessively aged. Lead tape (3M #420 or #421) adheres best with its' natural rubber adhesive but does NOT produce sharp edges as it deforms when firmly pressed down. Polyester tapes will produce cleaner edges. Once again, the surface must be clean- perform an acetone
⇦ on
eBay
or
Amazon
[affil link] Warning! Flammable!
wipe before taping to be sure.
2 & 3 If the chromate is not subjected to excessive heat during the drying process, it usually can go at least over night without interfering with the strip process. Process some coupons and age them, 1, 2, 3, days and then strip to test. Most chem films will 'cure' in 24 hours.
We have used NaOH (a readily available commercial blend) to strip chromate as well as anodize. The bath must be in good shape- not a lot of dissolved Al. We run ~10 oz/gal @ 125 F (removes Al at the rate of .0001" per surface per minute).
4 We would expect the 'reverse' process to produce more failures. The chromate is what allows the 'mask' to adhere. An alternative would be to anodize all over, machine off areas to be chromated, and then chromate. We do this on Type III Class II SEALED(!) anodize with no effect on the anodize (aerospace application). Not sure the effect on unsealed coatings.
Hope this helps.
anodizer - Colorado Springs, Colorado
Can chromate serve as a resist for hard anodizing
Q. Our company has a customer that wishes to have selective anodize on an item that is chromated to MIL-C-5541, will chromate serve as a resist to the anodize process?
John BradshawProcess Eng. - Fort Pierce, Florida
November 25, 2009
![]() |
A. NO, the anodic sulfuric acid will deteriorate the chromate. You must mask the chromate, or mask for anodizing and chromate afterwards. Tobler lists a long line of maskants. ![]() Robert H Probert Robert H Probert Technical Services ![]() Garner, North Carolina ![]() A. No it won't. Typically one would chromate the entire part, then mask the areas you wish to remain chromated, then anodize. ![]() Marc Green anodizer - Boise, Idaho |
Q. Follow up on selective anodizing -- will powder coat serve as a resist. Part is complex and difficult to maintain a uniform coating.
John Bradshaw [returning]Process Eng. - Fort Pierce, Florida
A. Although there are probably some powder coatings that would not hold up, I'm confident that there are some that will. I've seen powder coating successfully used as a resist for decorative chrome plating in a process cycle that included electrocleaning, cyanide copper plating, and hexavalent chrome plating, so I certainly think it can withstand the anodizing process. But how will you get it off -- or are you implying that the powder coating would stay on as a permanent finish?
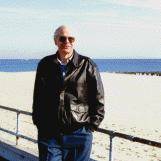
Ted Mooney, P.E.
Striving to live Aloha
(Ted can offer longterm or instant help)
finishing.com - Pine Beach, New Jersey
Hardcoating first, then chromating?
Q. Does anyone have any experience with properly sealing a hardcoat anodize surface to protect it during a chromate conversion process? I am a mechanical engineer working on an aluminum (6061-T6) electronics enclosure. The inside of the enclosure is finished with a chromate conversion coating to provide a good ground path, and the outside is dyed (black) hardcoat anodize finished for abrasion resistance and aesthetics. We are currently having a "brick" hard coated and then machining the complicated interior features before sending the part back out for the chromate conversion coating.
The problem that is arising is the need to seal the anodize to protect it during the chromate conversion process. I have read that sealing the hard coat softens the oxide layer, reducing the benefit of having a hard coat in the first place, but have not been able to find to what extent it is softened. Since we are machining the parts after the anodize, I am concerned that the finish will be marred if softened too much. I've read that cold sealing will lessen the softening effects, but I haven't been able to find specific information on chemicals/temperature to use for this process.
Mechanical Engineer - Hanover, Maryland, USA
September 20, 2011
![]() |
A. Unless the areas to be conversion coated are of an extremely complex geometry, and difficult to mask... have you considered having the part conversion coated first, and then have the appropriate areas masked from the anodizing process? ![]() Marc Green anodizer - Boise, Idaho A. Since you state that your hardcoat is dyed black, it would seem to me that your finisher is already sealing your part in order to keep the dye inside of the pores, rubbing the part with an acetone ⇦ on eBay or Amazon [affil link] Warning! Flammable! soaked wipe would prove this very easily. A proper seal should allow the hardcoat to survive through a very mild chromate cleaning cycle, and subsequent chromate with no problem. If sealing the part raises concerns over the hardness of the part, have your anodizer run a 4x4 panel through the process and have it Taber tested to ensure it will still meet your requirements. Jordan SomervilleFinishing Jobshop - York, Pennsylvania Q. I have a couple additions to my question. I learned that some of our anodized "bricks" have already been made, without the sealing step. Some of these have also already had the interior features machined into them. Is it possible to seal the anodize without harming the bare aluminum on the machined surfaces so we can still do the chromate conversion step? I assume we can mask the bare aluminum, but the purpose of doing the steps in the "backwards" order (anodize, machine interior, chromate conversion) was to remove the need to mask the intricate interior features. - Hanover, Maryland |
Q. Thank you Marc and Jordan for your responses, they have been very helpful. I added some more information above about my problem, but I'll further clarify and answer your questions.
The reason we are chromate conversion coating after the anodize is because the interior features are very difficult to mask. We've made these pieces in the past with the proper method (chromate first, anodize last) and when we could find a shop even willing to do it, the cost of the masking was the majority of the cost of the entire part.
The reason for the hardcoat is only to protect the finish during post machining. Use in the field should not require a particularly rugged finish.
For the existing pieces, although they were dyed, they were not sealed. I have been speaking with our finishing shop and they tell me that sealing a type III anodize will not set the color and will not protect the finish through the chromate conversion step but sealing a type II anodize will do both of those things. This is the opposite of what I've read and doesn't make particular sense to me, but I could be wrong. Is there a difference between sealing a type II and a type III anodize?
I have some parts that were hardcoated about a week ago and have been sitting on a shelf inside since then. Is there any problem with sealing those after they have sat like that? I assume parts that were hardcoated, machined, and sat with bare aluminum cannot be sealed due to the exposed aluminum, is that true?
Last, as I asked in my update above, the pieces that have been through the entire process (hardcoat (no seal), machine, chromate conversion) have definitely lost their color, but could the hardcoat have otherwise been harmed?
To respond to your rant Marc, I agree completely and would also say that during school I would have benefited from some time in a machine shop for similar reasons. But to defend myself here, I did not design this enclosure originally and have only been tasked with making it cheaper to produce. I did specify "cold sealed" for the hardcoat on the drawing due to my initial research, but that information was not sent on to the finishing house.
- Hanover, Maryland
A. No worries on my "rant", Nathan...wasn't specifically referring to you. As a matter of fact, over the last several years I've had the absolute pleasure of working with a mechanical engineer who's one of the brightest guys I've met..and has helped me solve many a problem created by engineers that...shall we say...didn't think finish first.
Anyhow, about all I can say is this. I hardcoat, 10's of 1000's of parts a year, a lot of which either require masking, or a machining step afterwards, or both. All of them are sealed, as they are used in a plasma/corrosive environment. From your last post, it really sounds to me as if the sealing step would be more of a benefit, as opposed to a detriment.
If indeed your masking requirements are that complex, I would seal the coating, post machine, and then conversion coat. If your coater can't seal his hardcoat to withstand a simple conversion coat process, then find another coater.
The big key here is, to make sure your post coating machining process does not subject your parts to dings and the like. Your machinists have to be careful, especially if there are a lot of sharp edges/corners on the part. If there are, and that's what you're concerned about getting damaged, then it wont matter if the coating is sealed or not. Anodizing, while extremely abrasion resistant.. is a very brittle coating. It takes very little effort to knock the coating off of a sharp 90 degree edge.
I'll also add, that my company makes quite a few parts that are Type 2 anodized, that are also sealed, and require a secondary machining operation. No problems at all, and I say again..as long as the machinists are CAREFUL while loading, and unloading the parts from the mills/lathes.
Out of curiosity..could you attach a picture of the part in question? Might help me a bit.
There are many different sealing processes available to anodizers. And it is possible that your current coaters sealing process for a type 3 Class 2 coating may not be adequate to prevent damage to the coating during a conversion coating process afterwards. However, it definitely can be done.
Properly sealing a type 3 coating to withstand a conversion coating process may require more time in the sealing bath, and/or variations in the anodizers operating parameters. Again, I say...it can be done. And yes, there is a difference between properly sealing a type 2, and a type 3 coating.
To your other question "has the hardcoat been harmed". Probably not, just a simple loss of color, which is to be expected on a type 3, class 2 coating which hasn't been sealed. The actual coating itself should be just fine as long as aesthetics aren't a huge concern.
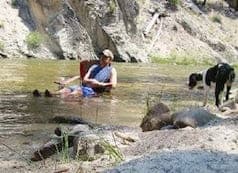
Marc Green
anodizer - Boise, Idaho
Q. Is Chem-film ever under the anodizing?
I seen a few requests for chemfilm and anodize processing without any masking requirements. Supposedly, there is a new MIL spec requiring this. Does this make any sense? Can a chemical conversion layer exist under anodize? Does this improve corrosion resistance?
Any information would be appreciated. Thanks.
- Oxnard, California, US
February 18, 2014
A. Hi Robert. We appended your inquiry to a long thread offering you many perspectives on what is involved when a component is partially chem-filmed and partially anodized -- but I can't imagine any possibility of chem-film under anodize since anodizing is a process that converts the aluminum on the surface to aluminum oxide.
Regards,
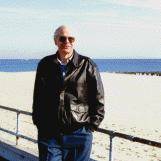
Ted Mooney, P.E.
Striving to live Aloha
(Ted can offer longterm or instant help)
finishing.com - Pine Beach, New Jersey
A. Although it wouldn't surprise me that our government would come up with a spec that's not practical, no you can't do this. Basically for the reason Ted stated. However, chromate conversion is allowed under the MIL-A-8625 / MIL-PRF-8625 [⇦ this spec on DLA] F spec as a touch-up procedure. Perhaps that's what you're referring to.
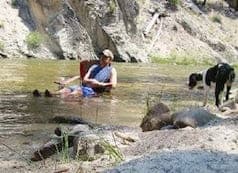
Marc Green
anodizer - Boise, Idaho
Yeah, it's just being flowed down from some of our customers more recently. It used to be a once in a year type callout, but I've seen it about 3 times this month. I thought the same as the thread responses but also considered maybe there's something that I might not know.
- Oxnard, California, US
Q. We also do a lot of parts requiring chem film mask and anodize type II or III. My question is, if parts are chem filmed prior to masking and anodize, how do you dye and seal in the secondary operations without exceeding the 140 degree temperature limits for chromate coatings? Is this an area of concern for Nadcap. Also, if chemfilm is done after anodize, what can be used to prep the surface prior to masking?
Puzzled in CT
aluminum anodizing - Oxford, Connecticut USA
March 25, 2014
A. David, here's my 2 cents. Typically when dealing with duel coatings like you mentioned, the conversion coating with be used for electrical contact reasons, and to prevent the Al from oxidizing... not corrosion resistance. It's my understanding it's the corrosion resistance that becomes affected when subjecting the conversion coatings to higher temperatures.
You're typical dye baths operate around 150 °F, No worries there. I imagine you're sealing in a mid-temp Ni acetate, or similar, perhaps 170 °F - 180 °F? Of course you could use a "cold" seal that operates at lower temperatures, but in my opinion, it's an inferior seal, and quite honestly, I'm sure you don't want to add another bath, when it's really not necessary.
If you're certifying to 5541F, there is no requirement for it to be subjected to heat prior to sending your test panels. Apply the conversion coat, send your panels for testing, pass...boom, you're done. You've met the spec requirements. Same goes for the 8625F spec.
All you're doing is what's being asked for on the print, I assume. If the engineer calls out for coatings that could potentially fail due to his/her lack of coating knowledge due to subsequent processing, or even use in the field...well, to be blunt, that's not your issue. You've sent your panels, you've passed the test showing you're applying the coating properly, and you've received your certification.
Since the duel coating appears to be a common practice for you, and if you're not having failures in the field, and most importantly, the customer is happy with your product... then quite honestly, I'd just keep on keeping on with what you're doing, and not try to open a can of worms which could possibly create additional work and expense for you.
Conversion coatings and anodizing have been applied on the same part for many, many years...it's even allowed as a touch up on 8625 F, and I seriously doubt that any NADCAP auditor will ever ask you to show that your 5541F coating passes the test requirements after application of an anodized coating.
Let sleeping dogs lay, my friend...UNLESS you have customer complaints. Then you can bring up the concern of subsequent processing potentially affecting the coating properties. I don't believe that 180 °F in the seal tank is going to have a significant measurable impact on conversion coatings used in the field.
As to your question about applying the conversion coating after anodizing...I would avoid that one.
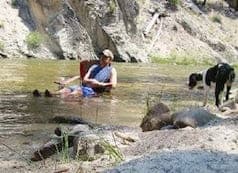
Marc Green
anodizer - Boise, Idaho
Marc, Thanks for your response.
After re-reading the mil spec I may have been over thinking this one. 6.11 refers to temperature limits on unpainted surfaces, so I should be fine if I consider masking as painting. Would you agree?
Dave
- Oxford, Connecticut USA
March 28, 2014
Q. Hi,
I work in the aircraft treatments department.
On certain parts it calls for Alocrome and anodise on same part. We mask with aluminum tape then chromic anodise . The problem we have is the leaching of anodise under the tape, and having to orbital the face to be Alocromed. This is both costly and time consuming, and a pain in the neck to all concerned. Any help would be most helpful.
In my work it requires that we mask part with lead tape 1st, then anodise, remove tape and mask for prime paint. Remove tape and locally Alocrom area that has not been anodised after paint. We can't do this without making a mess of part, staining paint, and taking a long time and costly. Any advise please.
thanks rod
- wigan england
April 27, 2014
A. Hi Rod. We appended your question to a thread here that discusses the situation in detail. After you have digested it, please get back to us with remaining questions. Thanks.
Regards,
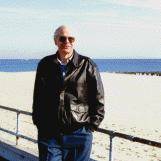
Ted Mooney, P.E.
Striving to live Aloha
(Ted can offer longterm or instant help)
finishing.com - Pine Beach, New Jersey
A. Chromate first all over, mask the chromate area, strip and anodize. The 40 volt chromic anodizing attacks the edge of the maskant more than the 20 volt anodize. Use the best quality maskant. Do not use lead tape. Use plastic tape, well mashed down. There is one maskant leader in our industry but I cannot name him here.
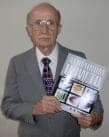
Robert H Probert
Robert H Probert Technical Services

Garner, North Carolina
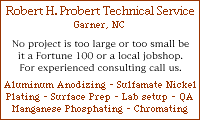
Hi ted,
I have digested it as you said. I've only been doing job 6 months so not that much of an expert. But have tried different methods and I just deoxidize the component, rinse, and just Alocrom the bit that needs doing, mask with foil tape, strip, then anodize. Seems to be working , but I'm still learning. Thanks for advice given by all on here.
p.s.: Like someone said on here the planning people don't always think it through, do they?
Thanks
Rod
- wigan england
Q. I have an anodized aluminum part that we had to add a machined chamfer on one of the ID holes on the part (which removed the anodizing). Can I re-anodize the part to cover the machined surface without stripping the anodizing first? Can I Alodine the part over the existing anodizing?
Kelley Posey- St. Louis, Missouri, USA
May 28, 2014
A. Hi Kelley. We appended your inquiry to a thread which discusses the alternatives in depth. I would say, no, you can't anodize the machined area; but yes, you can Alodine it to repair this part (although it's probably not the best sequence for production work which involves anodizing and Alodining).
Regards,
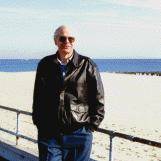
Ted Mooney, P.E.
Striving to live Aloha
(Ted can offer longterm or instant help)
finishing.com - Pine Beach, New Jersey
A. Spot anodizing certainly would be an option, although the color may not match the original anodizing. Alodine (chromate conversion) as a touch up, is permitted under Mil 8625F, albeit the coating properties of chromate conversion processes are not the same as anodizing.
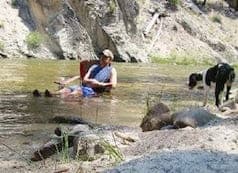
Marc Green
anodizer - Boise, Idaho
Anodizing over Chem Film?
Q. I have received a specification from an aerospace customer that requires a 2-step finishing sequence on a machined Aluminum chassis:
A. Chem Film (5541, Type II, Class 3)
B. Anodizing (8625, Type II, Class 2), interior surfaces optional
Exterior mounting surfaces (i.e. the "feet") are to be Chem Film'ed, but no anodizing, so I'm interpreting that those areas must be masked prior to anodizing.
My question is can anodizing be applied over top of Chem Film or must the Chem Film be stripped prior to anodizing?
My first thought was that the specification required the final finished coating stack-up to be Aluminum/Chem Film/Anodizing. An alternate interpretation is that they are only specifying the process sequence, not the finished coating stack-up. Chem Film first, mask off of the exterior mounting surfaces (and optionally the interior surfaces), then proceed to anodize, including any necessary preparation steps (such as stripping of the Chem Film from unmasked areas). The resulting finished coating stack-up would be Aluminum/Anodizing on all exterior surfaces and Aluminum/Chem Film on the exterior mounting surfaces. Interior surfaces could be either.
Any thoughts? Thanks for your help!
OEM - Cranbury, New Jersey, USA
August 20, 2014
A. Hi Mark. We appended your inquiry to a thread which discusses the options when chem film and anodizing are required on the same part. A given area of the part is not both anodized and chem-filmed, in either order; rather, it's one or the other.
Regards,
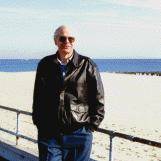
Ted Mooney, P.E.
Striving to live Aloha
(Ted can offer longterm or instant help)
finishing.com - Pine Beach, New Jersey
A. Process steps should be as follows:
1. Alodine entire part
2. Mask area to remain Alodined
3. Anodize (strip Alodine in anodizing pretreatment) and seal.
4. Remove masking from surfaces to remain Alodined.
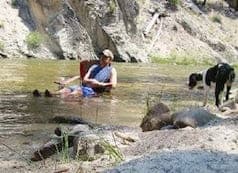
Marc Green
anodizer - Boise, Idaho
Chromate conversion then anodising?
Q. Hi
I have been asked to provide a finish on Aluminium of Chromate Conversion then Hard Anodising. There are no masked areas and there is no post machining. In other words no need for electrical conductivity.
I just don't see the reason for Chromatic Conversion at all. Am I missing something?
Thanks in advance
- China
October 22, 2014
![]() |
A. Does not sound to me like you are missing anything. Not even a threaded hole to plug? That would be the only thing that I can think of, but even then, it wouldn't make a lot of sense. ![]() Marc Green anodizer - Boise, Idaho A. Hi Johnathon, Aerospace - Yeovil, Somerset, UK |
A. I did have one thought on this. Perhaps at one point there was some masking needing done for electrical contact, and that was later changed, but the print wasn't properly rev'd/amended.
However, as you describe it now, it makes no sense. Definitely worth a phone call to your customer.
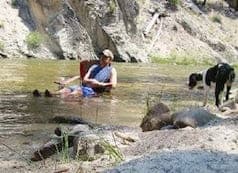
Marc Green
anodizer - Boise, Idaho
A. From my experience it is a mistake in the drawing. Usually Chromate conversion coating comes under the masking area. As you mentioned no change made after changing coating requirements or masking requirements
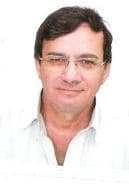
Yehuda Blau
YB Plating Engineering and Quality - Haifa Israel
Anodizing and chromate conversion coating and lacquer all on the same part
Q. Hello,
I am new to posting here but thought I would throw 2 pennies into the frackus. I have worked in coatings for some years and have some hands-on experience with 5541 and 8625 and coating on top of them. Recently the company I currently work for got AS9100 and in the mix we got thrown a client to try to do some work for. The part that we sampled from them has three different processes, coating wise, performed to it. It has an anodize in most areas, a chemical conversion coating in others and a "varnish" for the sake of electrical insulation on others. I had used this coating before and was therefore somewhat familiar with it.
The client claims that they have a problem with the coatings flaking and peeling after they machine areas of the part adjacent to the coating. I am not a subscriber to ever machining next to a coating line unless the coating is designed for it, which this is not. I made it clear that after we applied the material, got adhesion and met the specs then it was there's to be done with as they so pleased but our job was done. They agreed and our coating process went off without a hitch ... UNTIL ... the coating started peeling after conversion coating.
I am familiar with conversion coatings as well and have a good deal of knowledge on the process and the chemistries. My first thought is that during the conversion coating process the part is being dipped in an alkaline cleaner, an acidic desmutter and an acidic hexavalent chrome based material, probably all at elevated temperatures and adequate times for effectiveness.
My thoughts are these:
1. This varnish was not meant to be used this way, it is probably being degraded by the chemicals.
2. During desmutting there are materials like silicone and copper being removed from the surface of the aluminum that was freshly exposed during machining. This fresh aluminum is right up against our coating so as material is removed from that edge so is our coating exposing an area to peel.
Anyone else have any experience in this?
Thanks
- Chicago, Illinois, USA
August 31, 2015
Q. We have a supplier who chromate conversion coated the whole lot of parts (in this case it is a heatsink extrusion) after the part was masked and black anodized. The quantity is 600 each.
This resulted in a part with a blue tint instead of black.
My requirements for anodizing are for electrical resistance mainly while the masked non-anodized areas maintain electrical conduction.
My question is, are these parts compromised by this process?
We know that the correct process is to conversion coat first, then mask the areas that do not need anodizing, then anodize, followed by removal of the masking.
Astronics AES - Advanced Electronic Systems - Kirkland, Washington USA
July 27, 2017
A. Hi Adrian. To be clear you are saying that the process, which was supposed to be chromate, mask, anodize, unmask ... was actually done instead as mask, anodize, unmask, chromate?
Although several different things can cause the bluish color, one of them is the anodizing not being thick enough. You should probably do a thickness test in the blue area and make sure it meets your minimum rather than assuming that the chromating caused the blue discoloration and did no other damage to the anodizing. The blue color could also have been caused by the chromating process bleaching/leaching the dye out of the pores, indicating that it is no longer properly sealed if it ever was, so a seal test is probably called for.
Even if you ignore the aesthetics, I think you are right to be very cautious about whether the finish will meet your needs when it wasn't done right -- so a range of tests should be done.
Regards,
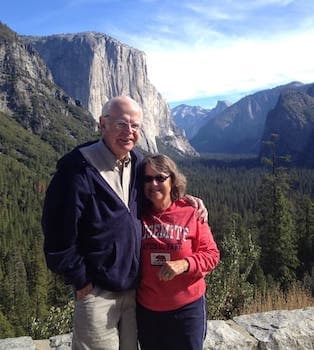
Ted Mooney, P.E. RET
Striving to live Aloha
(Ted can offer longterm or instant help)
finishing.com - Pine Beach, New Jersey
Thanks for your response Ted.
In order to perform thickness measurements we would have to bring in parts from our China supplier which would be time consuming.
Our needs for these parts are immediate and dealing with testing the coating plus allowing the bluish tint is not an option for us at this time.
We have asked our supplier to strip the anodize off, and proceed with the correct process sequence of conversion coat, mask, anodize, de-mask.
My main concern after this is dimensional as the stripping operation will remove some material off the heatsinks. Hopefully our tolerances will accept the resulting part dimension changes.
Astronics AES - Advanced Electronic Systems - Kirkland, Washington USA
A. Hi again. If the parts are stripped with chromic-sulfuric acid rather than caustic soda, you'll lose no additional aluminum, only the aluminum which was consumed by the anodizing process, which is roughly 50% of the anodizing thickness. Since the parts are black, I'd guess that is about 0.0006" of anodizing, for a net loss of about 0.0005" per surface -- but measurement and/or specs are a hundred times as good as a guess.
Too bad there are no anodizers in the USA :-)
Regards,
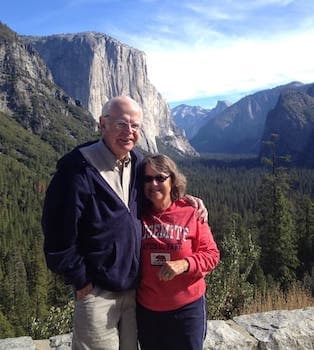
Ted Mooney, P.E. RET
Striving to live Aloha
(Ted can offer longterm or instant help)
finishing.com - Pine Beach, New Jersey
Which one to do first on same component: Chemical Conversion or anodising?
Q. Our customer expects both anodising (MIL-A-8625, TYPE-2, CLASS-2) and Chemical Conversion coating (AMSC5541, CLASS-1A, CLEAR) on same component. We are confused about which process will be done first? Customer is also not clear in this case. Which process to take first in this case?
Tamil vazhudiEngineer - Coimbatore, Tamilnadu, India
May 22, 2018
Ed. note: This RFQ is outdated, but technical replies are welcome, and readers are encouraged to post their own RFQs. But no public commercial suggestions please ( huh? why?).
A. Hi Tamil. We added your question to a long-running thread on the subject. It sounds to me like the ideal way to do it is to anodize the whole component, then do the machining, then conversion coat the freshly machined area.
If that isn't possible, other sequences have been described, but I think they all involve masking. Marc Green's reply of August 22, 2014 would seem to be the straightforward way.
Regards,
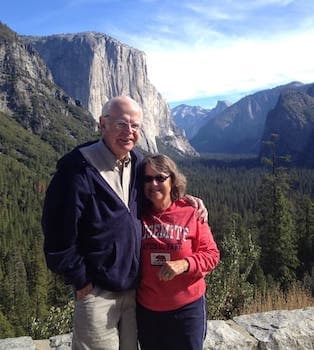
Ted Mooney, P.E. RET
Striving to live Aloha
(Ted can offer longterm or instant help)
finishing.com - Pine Beach, New Jersey
Conversion coating removal harmful to anodized parts?
Q. I must remove chromate conversion (MIL-DTL-5541) coating from Aluminum 7075 parts, which have been anodized as well. (Chromate in spots, anodize in others) Most methods to strip the conversion involve immersion in a caustic bath. What will the impact of the caustic soak on the anodized neighboring coatings on the same part?
Robert HutchisonProgram Manager - Pittsford, New York
May 22, 2018
Ed. note: This RFQ is outdated, but technical replies are welcome, and readers are encouraged to post their own RFQs. But no public commercial suggestions please ( huh? why?).
A. Unfortunately, devastating. The caustic bath will quickly destroy the anodizing.
Luck & Regards,
Ted Mooney, P.E. RET
Striving to live Aloha
(Ted can offer longterm or instant help)
finishing.com - Pine Beach, New Jersey
Anodise encroachment into chromated area
Q. I have an aluminum plate "Aluminum alloy 6061-T6511" that I have anodized with Sulfuric anodize MIL-A-8625 Type II, Class 2, black, on that plate I also have surfaces that can only be coated with Chem film MIL-DTL-5541, class 3. Is there a visual standard out there that would define the amount that the black anodize finish is permitted to bleed onto the surface finish with the chem film MIL-DTL-5541?
Chuck Jeschelnigquality manager - Mentor, Ohio USA
September 4, 2018
A. Hello Mr. Jeschelnig,
I am not aware of such a reference with visual guides (similar to the ones that exist for adhesion testing). This isn't to say that one doesn't exist, but we do double processing with masking as a MAJOR percentage of our overall parts throughput (it's one of our shop's specialties) and nothing like that has ever crossed my path.
The tolerances for edge bleed should be right on the customer print if it is important to them- sounds like they are not, or you wouldn't be looking for a standard.
If you're having issues with the customer rejecting parts for such, I'd get with their purchasing/engineering folks and get a written agreement as to what constitutes acceptable edge bleed. And of course they will say, "well, NONE!!!" And then the fun begins, and the next thing you know your inspector is going crosseyed from squinting into a Micro-Vu all day...
Good luck!
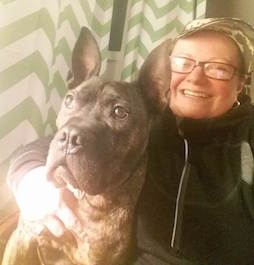
Rachel Mackintosh
lab rat - Greenfield, Vermont
Chromatizing on anodized surface
Q. Already a component is anodized and some part of it needs to be conducting. Can local chromatizing be done on already anodized surface. If so suggest the product and procedure.
Dr. Deepashri NageLarsen & Toubro - Mumbai, India
August 16, 2019
A. Hi Dr. Nage.
The anodizing is non-conductive and adding a chromate step will not change that. If you need conductivity you will need to strip the anodizing before doing the chromating.
Luck & Regards,
Ted Mooney, P.E. RET
Striving to live Aloha
(Ted can offer longterm or instant help)
finishing.com - Pine Beach, New Jersey
Q. I want to do a protective coating "Sanchem Safegaurd cc3400" for protection against corrosion on my Al6063 alloy product. After protective coating, I want to anodize it to improve heat radiation. I will have to mask some areas to ensure its electrical conductivity. Tape masking remove cc3400 coating which is my issue. Is there any other conversion coating equivalent to cc3400 more compatible with Anodizing? Is there any way to stop peeling of protective coating?
Kuljeet SinghEngineering design - India
February 28, 2020
A. Hi Kuljeet. I think you realize that you cannot anodize on top of a conversion coating, but I'll make that clear for other readers who might misread your question.
We appended your inquiry to a thread on the subject of how to best achieve an aluminum surface with portions anodized and portions conversion coated. After reviewing the thread, feel free to ask clarifying questions. Good luck.
Regards,
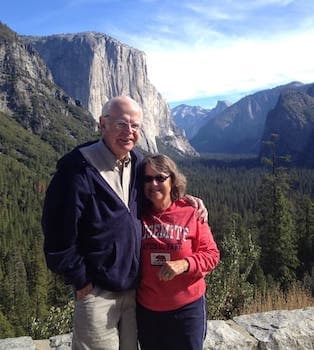
Ted Mooney, P.E. RET
Striving to live Aloha
(Ted can offer longterm or instant help)
finishing.com - Pine Beach, New Jersey
![]() |
A. Kuljeet - GREEN MOUNTAIN FALLS, Colorado Q. Thanks Mr. Ted, So my idea is to improve radiation emissivity of electronic housing by anodizing. Meanwhile, I also need protection against saline environment (as in coastal areas) due to which I thought of using Sanchem cc3400 conversion coating. Vihaan Networks Limited - gurugran, haryana, India |
A. Hi Kuljeet. Anodizing offers as much corrosion protection as conversion coating, and usually more. But anodizing is electrically non-conductive whereas conversion coating can be conductive.
Regards,
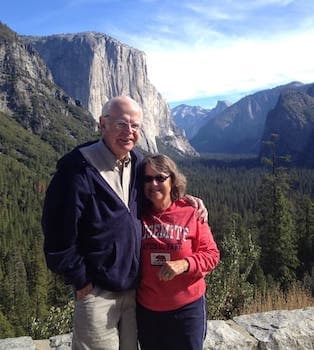
Ted Mooney, P.E. RET
Striving to live Aloha
(Ted can offer longterm or instant help)
finishing.com - Pine Beach, New Jersey
Q. Thanks for help Mr Ted. One last question, for connectors I need conductive surface at connector-housing interface. These areas will be masked while anodizing. So these local areas will have no corrosion resistance. Is there any treatment for these local areas to protect against corrosion?
Kuljeet Singh [returning]Vihaan Networks Limited - gurugran, haryana, India
A. Hi again, Kuljeet. I'm not sure if we're having a language difficulty, and you've now decided that you don't want to do what is the subject of this thread, after all, or what :-(
But to take it from the top one more time, when you need corrosion resistance on aluminum, and you need part of the surface to be conductive and part of it to be insulating, you anodize the areas you want to be insulating and you chromate conversion coat the areas that you want conductive and corrosion resistant. And you do it as described in this thread. Good luck!
Regards,
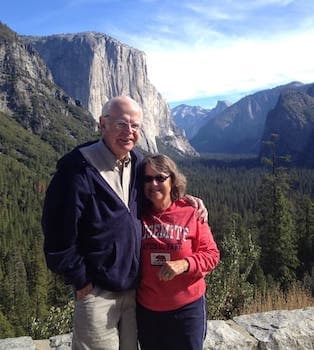
Ted Mooney, P.E. RET
Striving to live Aloha
(Ted can offer longterm or instant help)
finishing.com - Pine Beach, New Jersey
Q. We have some aerospace parts that receive chromic acid anodize per MIL-A-8625 with hot water seal and chem film per MIL-C-5541, class 1A, plus the standard epoxy prime. The engineering does not mention any masking for either the anodize or the chem film, only a location for the dry lubricant per MIL-L-46010 type 1. Is there any interaction between a dry film lubricant and either chem film or anodize that would indicate that one or the other surface treatment should be applied to dry film lubed area?
More generally, the Anodize + chem film + prime processing step is common enough in this engineering ecosystem that they have a dedicated processing code for it, even if it has now been deprecated for future use. (P08C01 if you've ever done work for Beechcraft before). From what I've been able to research, applying the chem film to a sealed anodized surface shouldn't damage it, but what (if any) benefit does it offer over chem film or anodize alone? In my prior experiences, it's either one or the other unless an electrical bond is necessary, but that would be a class 3 chem film coating in specific areas and not 1A as called out. We've shipped other parts with the same processing without having our vendor mask prior to applying the chem film and haven't had them rejected so I'm more curious than anything as to why this would be SOP.
Buyer - Wichita, Kansas
February 7, 2022
finishing.com is possible thanks to our supporting advertisers, including:
Q, A, or Comment on THIS thread -or- Start a NEW Thread