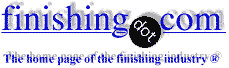
-----
Solutions to Problems in Plating on Aluminum (ADC12)
Quickstart: It's usually not possible to electroplate directly onto aluminum
⇦ why?. So a zincate immersion plate is the first step.
This thread covers the best pretreatment steps for electroplating on aluminum, troubles & solutions in doing so, and selection of aluminum alloys to plate onto. Read on ...
for Shops, Specifiers & Engineers
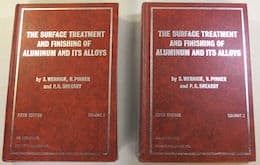
avail from eBay, AbeBooks, or Amazon
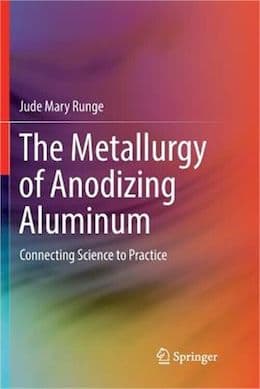
avail from eBay, AbeBooks, or Amazon
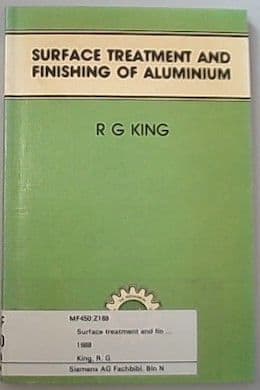
avail from eBay, AbeBooks, or Amazon
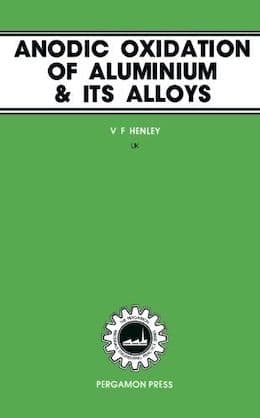
avail from eBay, AbeBooks, or Amazon
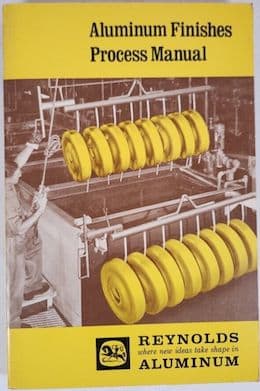
avail from eBay or Amazon
(as an Amazon Associate & eBay Partner, we earn from qualifying purchases)
Q. I would like to kindly ask you which aluminium alloys are more troublesome to process electrochemically or which ones should not be processed?
Milosz Fialkowski- Bydgoszcz kuj-pom
November 21, 2023
A. Hi Milosz,
The easiest way to look at it is that aluminum processing works on aluminum, rather than its alloying ingredients, so generally the high silicon alloys (most castings) are troublesome, as are the high copper alloys. Although electroplating on aluminum is arguably more difficult than anodizing it, at least the surface will be that other metal, whereas when anodizing aluminum you are trying to make the aluminum alloy itself somewhat attractive looking and it's difficult or impractical on some castings.
I would guess than 6061 is the most commonly anodized and plated alloy and probably the first choice. High strength alloys 2xxx and 7xxx will be more troublesome, but castings often cannot be attractively anodized and can be difficult to plate.
Luck & Regards,
Ted Mooney, P.E. RET
Striving to live Aloha
(Ted can offer longterm or instant help)
finishing.com - Pine Beach, New Jersey
Q. PLEASE SHARE NICKEL / ANTIQUE BRASS PROCESS DETAILS ON ALUMINIUM DIE CASTING PART (ADC12), PLEASE SHARE PROCESS TIME IN EACH BATH. PLEASE MENTION ANY CRITICAL BATH WE NEED TO TAKE CARE SPECIALLY.
Vishal ShiroleDEVELOPMENT - Pune , Maharastra , INDIA
October 30, 2024
A. Hi Vishal.
We appended your inquiry to a thread which already addresses a lot of it for you, but obtaining a complete process sequence in exacting detail would require retaining a plating consultant. Your process supplier might be willing to process a few sample parts for you in return for your business.
I assume you will also want a clearcoat over the antique brass? Please study the thread, then introduce yourself and your situation so we know what you are already familiar with, and pose specific questions or followups to previous answers -- and I'm sure you will get excellent answers. Thanks!
Luck & Regards,
Ted Mooney, P.E. RET
Striving to live Aloha
(Ted can offer longterm or instant help)
finishing.com - Pine Beach, New Jersey
⇩ Related postings, oldest first ⇩
Q. Our plating supplier is having a difficult time plating a decorative aluminum part (die-cast ADC12 material, part size 2.4" H x 5.4" W x 9.1" L, nominal wall thickness 3-5 mm, part weight 570 grams). The final plated finish is an antiqued Brass or Nickel, but we are rejecting 31% of finished goods in IQC inspection due to some pitting and white "chalky" material build-up in corners of the parts. The plating supplier is blaming the pitting and chalk build-up on the die-cast suppliers materials, saying that the material is not pure. The die-cast supplier claims that the material is ADC12 (not recycled) and the parts arrive at the platers with a mirror polish/buff finish (no visible pitting). The problem is I don't know enough about the plating process to solve the problem ... is it the material, is it the plating process, or a combination of both? According to the plater here is the process for the finish on the aluminum part:
1. Clean (ultrasonic) 2. Rinse x 2 3. Nitric Acid bath 4. Rinse x 2 5. Aluminum Sealer bath (quick dip, chemical bath, no current) 6. Rinse x 3 7. Neutral Nickel bath 8. Rinse x 3 9. Semi-gloss Nickel bath 10. Rinse x 1 11. Gloss Nickel bath 12. Rinse x 3 13. Brass bath 14. Rinse x 3 15. Black Nickel bath 16. Rinse x 2 17. Color Sealer bath 18. Rinse x 2 19. Pure Water Final Rinse
I questioned why the plater used Nickel, not Copper, as the first base metal plating bath (my experience in the past has always been Copper first). He said that 'Neutral Nickel' is best in this application. Based on the above process, is there anything that stands out as a potential culprit regarding the pitting & chalking issue? For now the work-around is to use a heavy Copper bath, post polish, then proceed with the Brass plating process.
Edmund Farmerlamp mfgr. - Stamford, Connecticut, USA
2005
A. I have no idea what an aluminum sealer dip is. Without a zincate step, I am surprised that you do not have an adhesion problem. Zincate followed by an alkaline electroless nickel is an excellent process for aluminum.
James Watts- Navarre, Florida
A. The preplate cycle seems to be wrong. If the Aluminum is a casting, then your nitric acid is not good enough. You have to add fluorides as well and for some castings should include also sulfuric acid!
Aluminum sealer - not familiar with this very odd term. It should be a zincate! On top of it, one should use a double zincate, meaning the first dip 60-90 sec, a dip in CLEAN 50% nitric acid and then a second dip in the zincate for 15-25 sec.
Neutral Nickel - what is it? It should be a neutral electroless nickel or a cyanide copper. There are some special zincates that enable direct nickel plating but it is not always safe.
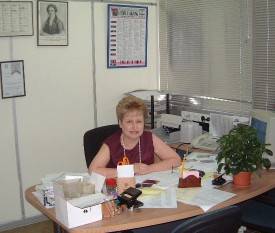

Sara Michaeli
Tel-Aviv-Yafo, Israel
A. Process seems strange with so many nickels.
Also color buffed aluminum has oil in it, that may come out in plating process, but normally shows as bad adhesion.
Light blisters are normally a sign of zinc.
Pitting may be excessive brightener, excessive air, or tank contamination.
Whiteness may be burn if it is on high spots and outer edges nearest anodes.
Blisters from air are normally on undersides. If all over check brighteners.
polishing - Belfast, Maine, USA
A. Edmund, in ADC12 aluminium alloy there is a high content of silicon; therefore the job shop must use ammonium fluoride to dissolve the contaminants after the alkali pickling. I can see also that he uses nitric acid; that's nice. He also uses a sealer which I believe is a zincate. I think the problem can be solved by a dip in ammonium bifluoride solution.
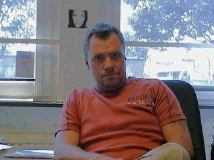
Anders Sundman
4th Generation Surface Engineering
Consultant - Arvika,
Sweden
A. Hi,
Edmund, we have similar problem with decorative plating on aluminum parts (small aluminum cast). We apply instead of cyanide copper an electro nickel (pH 5,0 2-3 A/dm2). Probably our Ni-bath is like yours, neutral Ni-bath.
Our process
1.clean
2.rinse
3.alkali pickling (temperature 80 °C, NaOH )
4.rinse
5.Nitric acid + 10%HF
6.zincate bath
7.rinse
8.nitric acid wo/HF
9.zincate bath
10.rinse
11.Ni bath pH5
12. rinse
13.gloss Cu bath
14.rinse
15.gloss Ni bath
16.rinse
17.Cr bath
We had a problem with pitting on finished parts . Too deeply polished parts (inside, the casting had different structure) and too high pH in the first Ni bath were the reasons of pitting. Furthermore we changed the air stir in the first Ni-bath. Air strongly mixed the bath and exactly flows around the parts.
Best regards
- Krakow, Poland
2005
A. Dear Farmar,
I hope 'sealing of aluminium' means zincating.
Plating Aluminium which contains silicon requires a very precise degreasing and rinsing. First see that your cleaners should be non silicated. Be sure of even your desmutting and re-zincating. See that your cleaning chemicals are not etching the die castings. I agree with other platers, you can sure some etchants with nitric dip, only for proper bonding of zinc on your job.
There are many platers who are plating direct Semi Bright Nickel over zincating, but your metal seems to be not fit for this process. Some metals are difficult to plate but not impossible. I suggest, use Copper Cyanide and Bright acid copper after zincating. Since these Copper has a good adhesion and good leveling properties. I think your metal requires uniform leveling and uniform throw all over the current densities after zincating.
For pitting, if your Hull Cell
⇦ huh?
and other analysis of you baths are ok, then I recommend please concentrate on your pretreatment, quality of rinsing water, proper maintenance of your electrolytes, timely clear out contaminations, organic as well as inorganic and filtration. And sometimes your metal supplier may be filling the pinholes, jalla and sori defects by impregnation which gets removed when you degrease them or dip in acid.
All The Best!
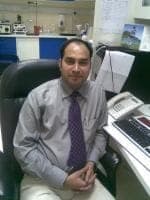
Shafiuddin A. Mohammed
metal coating shop - Dubai, United Arab Emirates
September 20, 2008
...
A. Hi again,
I read Edmund's posting. He is zincating on casting aluminum two times. That will build a bridge on casting aluminum and involves bad rinsing water and contamination from the pretreatment steps in the aluminium substrate. Pure aluminium is an alloy; there you can use 2 and 3 zincating steps, but never on casting alloy.
Regards
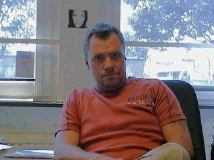
Anders Sundman
4th Generation Surface Engineering
Consultant - Arvika,
Sweden
April 3, 2013
![]() |
To Anders Sundman,
I am 100% sure that Anders knows that pure aluminum is not an alloy. And now that I study his posting I can see that he was trying to say that the aluminum alloys which are rather pure can accept double or triple zincating, whereas casting alloys cannot (probably because the HNO3 dip implied between the two zincates attacks the other ingredients in casting alloys too aggressively). Thanks also for the illuminating info on the origin of the words "Aluminum" and "Aluminium". Of all the courses I took in college, I found "Philosophy of Language" the most fascinating and share your appreciation of language. But words do morph; as an American I use "aluminum" because it is used universally here, although I do see that most British and Indian posters write "aluminium". ![]() Ted Mooney, P.E. Striving to live Aloha (Ted can offer longterm or instant help) finishing.com - Pine Beach, New Jersey |
Q. Hi there, I have an aluminium high pressure die cast part that is currently electroplated and I'm getting some random issues with surface finish. It looks like there is some chemical reaction happening under the surface coating. Sometimes it looks like pitting other times it just looks like corrosion. It can be wiped off, but sometimes reappears when it is outdoors for a long time.
The alloy is ADC10 and the process we are currently using is:
- Ultrasonic Wave Cleaning
- Zincate (displacement Reaction) 0.5 - 1µ
- Ni Plating 5 - 10µ
- Cu Plating 20 - 30 µ
- Ni Plating 5 - 10 µ
- SnCo Plating 0.05 - 0.1 µ
- Cr3 Plating 0.15 - 0.2 µ
I was wondering if there was a process to put the cast parts through before the plating process.
Do you have any advice to prevent this type of surface defect?
Many thanks,
Mike
Mike James
- Sydney, Australia
March 14, 2013
A. Hi,
I think the ultrasonic cleaning can do that as the plating can build a bridge over the aluminium area, and in the aluminium substrate some pretreatment will stay left.
Regards
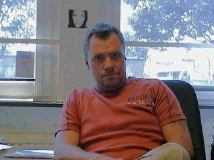
Anders Sundman
4th Generation Surface Engineering
Consultant - Arvika,
Sweden
Q. Hi Anders,
Thanks for the response. Do you have any suggestions as to how to eliminate this issue. It's actually very similar to the chalky effect that Edmund references in his first post.
Any help would be greatly appreciated.
Regards,
Mike
Mike James [returning]
- Sydney, Australia
A. Hi Mike,
Cast aluminium should only be zincated one time, and also take care when you etch the parts. Both etching and zincating will make some pores in casting aluminium. And in the pores it will involve dirty contamination from the pretreatment steps. Also the pretreatment steps are important because of what is in the alloy in the aluminium casting.
Try to translate on the library here on finishing.com what I have written about aluminium.
Regards,
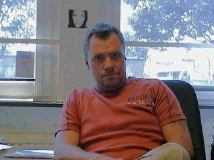
Anders Sundman
4th Generation Surface Engineering
Consultant - Arvika,
Sweden
A. It may be porosity in the casting that is causing your problem. A possible solution is to try a double zincate process. Or, if it is porosity related, then baking the parts at low temperature before plating, or an anaerobic sealant may help.
Lyle Kirmanconsultant - Cleveland Heights, Ohio
A. Cast aluminium is a problem to electroplate and needs to be carefully treated, because solutions can get trapped in the porous structure of the casting. Firstly, you need to treat the casting with a zincate treatment and then I would suggest you fill the pores and bridge any surface spaces with a high throwing power copper. The thickness of the copper will in part depend on the casting porosity. I am not convinced that nickel will have adequate throwing power and if you are using a nickel strike, it will probably be based on chloride, which is a potential disaster area for uncoated aluminium. You should also ensure the parts are extremely well washed between these initial stages and as Anders says, ultrasonics may be beneficial.
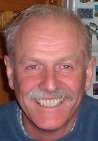
Trevor Crichton
R&D practical scientist
Chesham, Bucks, UK
Q. Hello:
We have some parts that are manufactured out of 6061 AL, with integral Tellurium Copper inserts. Imagine a .5x6x6" piece of AL, with a 2x2" center section made of the Te-Cu, with a seamless transition from the AL to the Cu (no gaps). The customer wants to electroless nickel plate the entire part. My concern is the different pre-process requirements for AL vs. the copper. Can this be done? Anyone have any experience with EN plating of a two-metal part like this? Many thanks in advance for any help!
Joe Osborn
Manufacturer - Novato, California
April 17, 2014
A. Hi Joe. Sorry, I have no experience with this, and can't find reference to it in my texts or on-line. But we appended your inquiry to this thread because I think the process will start with zincating and then copper plating of the aluminum, followed by electroless nickel on everything. Copper is not catalytic to electroless nickel, so you will have to "spark" it first (apply electricity for a second or two).
I'm sure you well know that plating or chemically processing an assembly of different substrate materials is invariably a bad idea -- but if there is no way around it, I think it can probably be done. Good luck.
Regards,
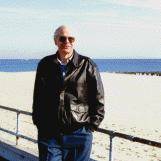
Ted Mooney, P.E.
Striving to live Aloha
(Ted can offer longterm or instant help)
finishing.com - Pine Beach, New Jersey
Q. I got some aluminum plating done and it came back discolored and sticky. Does anyone know what went wrong -- was it what I did or the platers?
kurt bailey
- sun valley California
July 18, 2014
A. Hi, Kurt. A plating shop is supposed to do good plating, not discolored and sticky plating, so our first thought must be that the plating shop probably did something wrong. If you can give us some facts like what you did and what you asked the plating shop to do, a less superficial answer may be possible.
Luck and Regards,
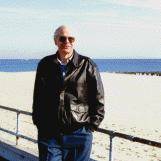
Ted Mooney, P.E.
Striving to live Aloha
(Ted can offer longterm or instant help)
finishing.com - Pine Beach, New Jersey
![]() |
Is ADC12 aluminum non-recyclable?Q. I'm researching a project for work. Can anyone tell me if ACD-12 aluminum is recyclable or has any conservation benefits? I see some areas it is, and others it's not. A. Hi Melanie. According to Regards, ![]() Ted Mooney, P.E. Striving to live Aloha (Ted can offer longterm or instant help) finishing.com - Pine Beach, New Jersey Ed. update: The above link is now broken. Thankfully, the wonderful Internet Archive preserved a copy here
Q. Hi Ted, A. Hi again. I don't know what you mean by "break down the same", and sorry but there's no way anyone can say whether you can "use the same stats/facts" when we don't know what stats you want to apply or to what circumstance you want to apply them. Clearly you won't easily find stats showing what percentage of people put their broken ADC12 castings from their old cars in with their cans and cardboard for curbside recycling; still, they may well take them to the scrapyard; and manufacturers of castings probably have regular arrangements for recycling. Please do your best to explain the details of your situation :-) Regards, ![]() Ted Mooney, P.E. Striving to live Aloha (Ted can offer longterm or instant help) finishing.com - Pine Beach, New Jersey |
What does "Zn Coverage" mean in Plating of Zn on Aluminum Extrusions
Q. What exactly is meant by Zn Coverage on Aluminium Extrusions? What is it unit for measurement and how it can be measured? Will an EDXRF do this job?
Raghunandana Subbanna
Customer Support Engineer - Bangalore, India
April 7, 2015
Hi Raghunandana. Either of us can look up the word "coverage" in a dictionary, but it doesn't help, does it? Sometimes it might refer to a requirement that there must be visible zinc plating everywhere on the extrusion, with no bare spots; sometimes it might dictate a replenishment schedule of how much zincate to add for every 1000 sq. foot of extrusion processed -- just as you might read on a quart paint can that it offers 100 square foot of coverage.
Unfortunately it is nearly impossible to have any assurance what some third party meant when we hear two words transcribed out of context like this. At this point neither of us knows what the requirement is, so it's not possible to say whether an EDXRF is of any value in determining compliance. Please try to figure out and explain the actual situation. Thanks.
Regards,
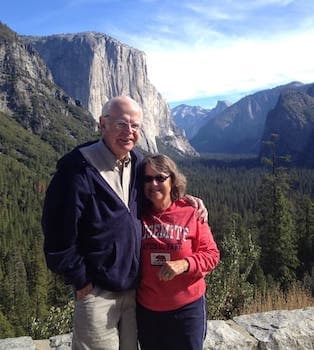
Ted Mooney, P.E. RET
Striving to live Aloha
(Ted can offer longterm or instant help)
finishing.com - Pine Beach, New Jersey
Q. I'm going to manufacture a die-cast A360 Aluminum part in China and they are telling me it can't be coated with clear zinc because the temperature of the zinc is too hot and it will disfigure the part. It's a housing part that will be matched up with a T6063-T5 heatsink which is going to be anodized. Can the part be coated with a clear zinc coating? Thank you in advance.
Gary Taverrite
- Sacramento California USA
March 17, 2018
A. Hi Gary. What function or process do you have in mind when you say "coated with clear zinc"? Even without language translation difficulties, "coated with clear zinc" sounds like it might have led to misunderstandings :-(
When *I* hear that phrase, I envision electroplating with zinc (which is silvery metallic in color, not clear) followed by a light blue or "clear" chromate conversion coating so the luster of the zinc plating is retained. Zinc electroplating and conversion coating is NOT a high temperature process, but others might envision something else.
I also have a little bit of a problem interpreting what you mean by "matched up with". Do you mean that you want the "coated with a clear zinc" component to look similar to the anodized part (it won't), or do you mean they will be connected together (they are not very galvanically compatible).
Regards,
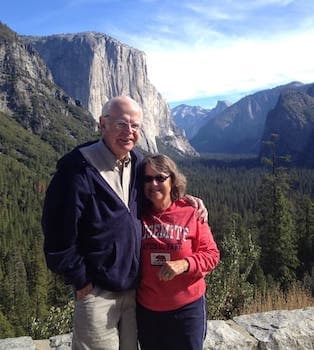
Ted Mooney, P.E. RET
Striving to live Aloha
(Ted can offer longterm or instant help)
finishing.com - Pine Beach, New Jersey
Q. Hi Ted - thank you for responding. Here is what it says on the drawing from my US customer.
MATERIAL: ALUMINUM A360 OR EQUIVALENT
FINISH: LIGHT SAND BLAST, CLEAR ZINC. ROHS COMPLIANT
I'm not sure how to interpret my China manufacturer's statement that you can't coat aluminum with a clear zinc costing. Furthermore my customer wants to know if I can get him samples of aluminum coated with the clear zinc in varying thicknesses -light - medium - heavy.
Sorry I'm a bit of a neophyte on this process. Thank you.
Gary Taverrite [returning]
- Sacramento California USA
A. Hi Gary. That drawing note doubtless means, as I described, zinc electroplating followed by a RoHS-compliant clear trivalent chromate conversion coating.
You can get a copy of ASTM B633 to understand all this better (although that spec actually covers zinc plating on steel rather than on aluminum); you will probably then interpret light, medium, and heavy as 5, 8, and 13 micron thick platings.
However, it's possible that your customer is also a neophyte and is hoping for a voice of knowledge & experience to chime in before the parts are plated. It doesn't sound like your manufacturer in China will be offering anything remotely like that (perhaps you're dealing with a broker of some sort rather than directly with a knowledgable plater). Further, although it is certainly possible to zinc plate aluminum, it is a rather uncommon finish. So it might be a good idea to phone your customer and understand each other a bit better. At the risk of being called jingoistic, I might also suggest that you consider getting those samples plated in California, where you are and where you can easily visit shops, and where every plating shop already understands that drawing note perfectly and knows exactly what to do :-)
Luck and Regards,
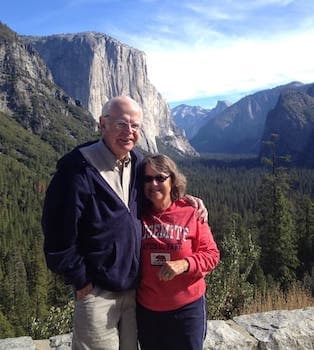
Ted Mooney, P.E. RET
Striving to live Aloha
(Ted can offer longterm or instant help)
finishing.com - Pine Beach, New Jersey
Thank you Ted. That is good advice and helps a lot.
Gary Taverrite [returning]
- Sacramento California USA
Pits in nickel-chrome plating on aluminum
Q. Hi,
I'm working on a project for my company where they plate Aluminium parts, but there is a problem with the plating. The finished product has all throughout the part little specs and some pits. We've tried different processes and checked if it was in the substrate or not, sometimes the pits where in the substrate and not in the plating, but mostly it is in the plating.
The alloy comp is a 6060 Al. Any idea what the problem could be?
Process is described here:
1.soak
2.rinse
4.rinse
5.soak
6.rinse
7.rinse
8.etch
9.desmut
10.rinse
11.rinse
12.zincate
13.rinse
14.strip
15.rinse
16.zincate
17. nickel strike 6v
18. semi bright Ni
19. high sulfur Ni
20. bright Ni
21. MPS
22. chrome activator
23. chrome bath.
Best Regards,
Jacob Lopez
metal plating - Noord-Brabant, Nederland
October 17, 2018
Pitting Problem in Chrome Plating of Die Casting Aluminum(ADC12)
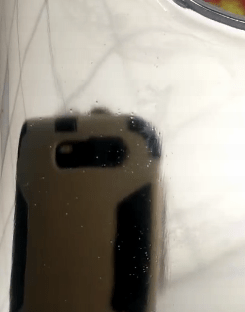
Q. Hi Everybody
We are die casting manufacturer based in china.Recently,we make die casting parts which request bright chrome plating. The problem we have on finishing is there are many pittings on surface of parts after chrome plating.
The parts use material ADC12 (similar to A380). No recycled material.
Mirror polishing (very fine buffing) is applied on the parts before plating.
The chrome plating supplier follows the procedure of chroming aluminum die castings.(Copper-Nickel-Chroming)
Is there anyone who can give us advice for the above problem?
Jason Huo
- China
December 14, 2018
? Hi Jason. Sorry but I have no idea what that pic is supposed to illustrate :-(
If the pits are small but varying sizes, shiny, and hemispherical, they are "gas pits" ⇦ huh?
But aluminum castings must also be totally free of porosity and cold shuts ⇦ huh? in order to plate pit-free. Good luck.
Regards,
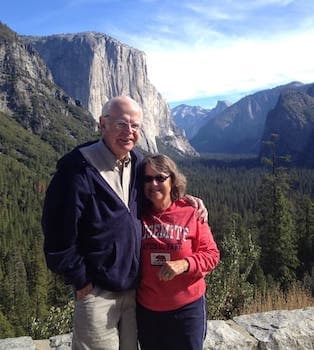
Ted Mooney, P.E. RET
Striving to live Aloha
(Ted can offer longterm or instant help)
finishing.com - Pine Beach, New Jersey
Q. Hi Ted
Thanks for your reply.
I think the reason you give is correct (hydrogen bubbles).
Please look at picture with care and you can see there are many tiny pits on surface.
Called Plating supplier and they told us that the pitting problem was caused by porosity (air trapped in castings).
1)There are not any pits left on surface of casting after mirror polishing. The surface finishing is very fine after mirror polishing. No shrinkage porosity, no cold shuts, no scratches.
2)The reason of problem given by plating supplier is that the air trapped underneath surface rises out like bubbles since the castings heat up gradually during plating. The pits were left on the surface after air bubble rise out.
Is their reason correct?
Best Regards
Jason
Jason Huo [returning]
Contracted Aluminum Die Casting Manufacturer - Cangzhou, Hebei Province,China
A. Hi Jason. I guess I am looking at a reflection of a camera phone and a chicken wire type pattern on your shiny surface? Your picture is not clear enough nor large enough to see the actual appearance of the pitting, but the close placements of the pits could be hydrogen pitting. And if the pits are shiny hemispheres, that's what they are.
Is it possible that the way the parts are racked, no air agitation ⇦ huh? hits this area of the part during nickel plating. Please ask your supplier what the surface tension of the nickel plating bath is supposed to be and how to measure it. Lack of wetter and/or poor agitation is one, but not the only possible, cause of hydrogen pits though.
You are confident that the parts were free of cold shuts and porosity before polishing?
Regards,
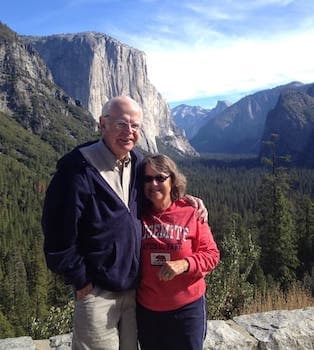
Ted Mooney, P.E. RET
Striving to live Aloha
(Ted can offer longterm or instant help)
finishing.com - Pine Beach, New Jersey
Q, A, or Comment on THIS thread -or- Start a NEW Thread