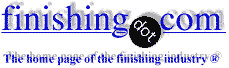
-----
Blotchy MIL-A-8625
2004
Q. We recently manufactured a batch of parts from 6061-T6 that were anodized to specification MIL-A-8625 / MIL-PRF-8625 [⇦ this spec on DLA], Type III, Class 1, 2.0 mil coating thickness. The finished part exhibits surfaces parallel to the original rolled surfaces that are covered with small (0.1-1.0 mm) irregular light colored splotches. The defects appear to be lamellar because the sides of the part, which were normal to the rolled surfaces, exhibit the defects as parallel thin lines. We are desperate to get these parts to our customer but don't know if this is a problem in the raw material or the finishing process; help please?
(pictures added 10/30/04)
- Leander, Texas
A. Dear Michael
This appearance could be due to a high voltage during the anodising process. You could try to strip one part and then processing it with a voltage below 35 V.
Anne
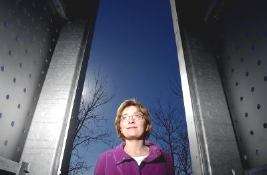
Anne Deacon Juhl
- - Trustrup Denmark
2004
A. It could also be work hardening. Aluminum that has been extruded or rolled but not then annealed (or properly annealed) will often have a localized increase in the hardness (work hardening). This will show up as anodizing defects like you describe. If this is what's happening; the solutions would be to use stock that has been properly annealed, anneal it yourself, or size your stock so that the entire surface can have the offending work hardening machined off. I'm not sure how deep the work hardened areas will be.
Paul Yursis [deceased]- Columbia, Maryland, USA
Ed. note: it is our sad duty to advise of the passing of Paul Yursis in August 2005.
Here is a brief obituary by Mike Caswell.
![]() |
Q. Additional information: The product is assembled from a body made from Hulett 6061 T-6 plate and a .12-inch diameter, pressed-in plug that is made from a different supplier's 6061 T-6 round bar. The surfaces of both materials, the body and the plug, exhibit the defect. Photographs are available Michael Davenport- Leander, Texas 2004 A. Now that I see your pictures, I see what you mean, not what I envisioned. Annealing issues don't look like that. That looks like one of the alloying metals (one that won't anodize) somehow precipitated out of the mixture during rolling. I haven't seen that before, but I'd still guess that its a material problem, not an anodizing problem. Perhaps someone else here has seen this before? The laminar quality of the edges is what throws me. Paul Yursis [deceased]- Columbia, Maryland, USA Ed. note: it is our sad duty to advise of the passing of Paul Yursis in August 2005. |
![]() |
A. Dear Michael Thank you for the very useful pictures. This could be a chloride contamination of the electrolyte. Have you tried to remove the anodic layer. If you do that carefully you could see if the pitting is valley or hill. If is is valley the problem could be due to a AlMg-intermetallic phase which is more easily dissolve than the aluminum matrix. If it is a hill it could be due to poor degreasing. ![]() Anne Deacon Juhl - - Trustrup Denmark 2004 A. Under magnification (sorry I don't have a photomicroscope) the defects are plainly corrosion sites. The ones on the planar surfaces are irregularly shaped and are much more deeply corroded than the ones on the edges. The ones on the end of the plug (a 6061 T-6 plug from a different manufacturer's round bar) are more deeply corroded than the defects in the material surrounding the plug. With very few exceptions, the defects on the edges are much shallower than those on the planar surfaces and are predominately elongated parallel to the path of the machining cutter. Michael Davenport- Leander, Texas 2004 |
Q. Hi Anne,
The corrosion sites are pits, not built-up areas. The pits on the planar surfaces (top and bottom) are much deeper and more irregular than the pits located on the edges (e.g. the surface that includes the pressed pin). The defects on the edges are strongly striated, running roughly parallel to each other along the direction of the finish machining operation and are not nearly so deep as the defects in the top and bottom surfaces. I think it is an important clue that the pin isn't made from the same lot of material as the body it is pressed into, but is still marked by striations running parallel to the machining operation. A question: what are the implications if the effect is caused by an AlMg-intermetallic phase? Does this imply a material defect or a process defect?
Michael Davenport- Leander, Texas
2004
A. To me, this looks like a simple case of Mic-6 (cast tooling plate)being etched (perhaps heavily) prior to anodizing (a definite no-no). That particular tooling plate is loaded with SI, which does not anodize. Are you 100% sure there wasn't a material-ordering mistake? I'd almost bet a Christmas dinner on it.
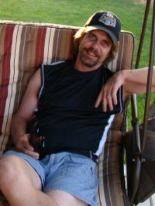
Marc Green
anodizer - Boise, Idaho
2004
A. To follow up, I worked in a job-shop for about 10 years, and I wish I had a nickel for every time we got a job in from a machining outfit where this mistake has occurred. A lot of the time, it was due to a machinist grabbing his stock, and not paying attention to what he/she was grabbing (this stuff is clearly marked tooling plate), either that, or they noticed the difference, but didn't think it would make a difference. The way to make this stuff look decent after anodizing is to inform your coater of the alloy, and make sure they don't etch prior to coating. Machinists love this stuff, due to its ability to hold flatness, and its machinability. But, as an anodizer, I can't stand it. Reworking this stuff is almost impossible.
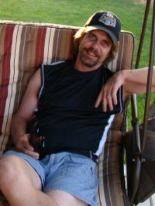
Marc Green
anodizer - Boise, Idaho
2004
Q. I appreciate your observations Marc, but I know that this is not cast tooling plate. First, the parts were machined in-house and we maintain strict lot control. Secondly, because we thought that perhaps our system had failed and someone DID slip up and substitute cast tooling plate, we tested a sample of the anodized parts and verified that the material was a wrought alloy. So, we went back to the drop remaining from the production run to see if we could learn anything from the manufacturer.
Hulett, a South African mill, manufactured the material. As you're probably aware, Hulett was recently accused of dumping plate on the US market and sued by Alcoa. Cheap plate? Perhaps Hulett had a process problem that somehow affected the alloying ingredient dispersion, causing (like Anne suggested) an intermetallic phase that preferentially etched out during the anodizing process. I did a reasonably thorough web search though and found no references to anyone having problems with the Hulett material (with the obvious exception of Alcoa--for different reasons).
Michael Davenport- Leander, Texas
2004
A. Hi Michael
I think Marc is right about the silicon but you sound as you are totally sure about the alloy. The AlMg-problem is also a material problem which could be diminished a bit with a heat treatment and then a very slight etching.
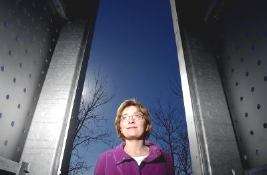
Anne Deacon Juhl
- - Trustrup Denmark
2004
![]() |
A. Michael, I'm not familiar with Hulett material, all the parts we manufacture, and hardcoat, are spec'd to be Alcoa. What does your coater say about this issue? A good coater will recognize bad material right after the etching step. It does sound like the Hulett material is very suspect, though. A very simple test that your coater can perform is to strip one of these parts. If the smut left behind is very tenacious to remove in his desmut tank, you can almost bet SI is the contaminate (unless he's using a desmut tank formulated for castings). ![]() Marc Green anodizer - Boise, Idaho 2004 2004 Q. I want to thank Ted Mooney and Finishing.com for providing this forum and Anne, Paul and Marc for their time and thoughtful responses. The jury is in and the process is indicted. We sent two test coupons, one from the suspected lot and one from a different lot, to four anodizers who specialize in hard coat anodizing. Except for differences in color (said to be due to process temperature differences) all four companies produced acceptable product. I am including photographs; hopefully they'll make it with the posting.
- Leander, Texas |
A. Well, Michael, I guess I stand corrected. Lets see.. how does turkey, yams, stuffing, mashed taters, green bean casserole, rolls, and an apple pie sound for Christmas Dinner!
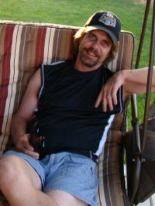
Marc Green
anodizer - Boise, Idaho
2004
A. looks like galvanic corrosion to me? Are your racks insulated from the tank (no metal on metal)in each step of the process? This usually occurs in the post anodize phase of processing.
Dwight Franke- Conroe, Texas
July 14, 2009
Q. Dear Sir,
After we have anodized the part, the 6061-T6 aluminium surface appeared to have "chicken pox" as per attached picture. Current and voltage ramp up was normal and material found ok. Can you advise what is the root cause? Thank you.
- Penang, Malaysia
February 18, 2013
Q, A, or Comment on THIS thread -or- Start a NEW Thread