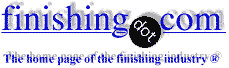
-----
Construction Anodizing Tank - Materials? Agitation?
2004
Q. I have a few questions regarding type II anodizing equipment. I have been getting mixed results and before I commit myself to one thing, I would appreciate some advise. Thank you in advance to all who participate.
I'll start by providing everyone with some background information in regards to my situation. I am quite new to the world of anodizing, its chemistry, its process and its fundamentals. I will assure you all, however, that I have been doing a great deal of research into the field and have successfully produced consistent parts on a hobby scale in my garage (and yes Ted, environmental issues are certainly a concern of mine). Currently I am looking for a reasonably priced printing of "The Surface Treatment and Finishing of Aluminum and Its Alloys" which I am sure will put to rest many of my questions and concerns. In the meantime, I turn to you people.
I intend on fabricating my own processing tanks. Now before some of you jump on the wagon, I should mention I have a fair bit of experience fabricating such things. I do have a few concerns when it comes to the materials utilized in their construction. I have been told by a few people that polypropylene should be utilized throughout the entire line in regards to tank construction. This is not something I disagree with, however, not being particularly educated on the characteristics of polypropylene, I fear that the sealing process (operated around the 200 F mark) will place the polypropylene under immense stress and possibly failure. Am I wrong with my assumption? Should 316 stainless steel be used to construct this high temperature tank?
In short, what I am asking is this. If you people were going to purchase new processing tanks, what would each of the following tank be constructed of :
1 - Pre-treatment
2 - Etching
3 - Bright Dip
4 - Desmut / Deox
5 - Anodizing
6 - Coloring
7 - Sealing (nickel acetate)
With tank construction out of the way, I now have concerns about each tank's method of agitation. I feel that circulation of fluid is the most efficient means of agitation but as I mentioned before, I am quite new to this. Mechanical and air agitation are certainly options. My concern with air agitation is its potential to "chill" a bath in which I am heating and with regards to mechanical agitation, as I said this is a lab scale line of very limited size (3'length x 1' width x 1.5' depth). I fear that mechanical agitation may consume too much of the tank space. To make a long question short, if you people were going to set up a brand new type II anodizing line, which method of agitation would you utilize for each of the tank listed above?
I thank you all for your help here. These are questions that I have been struggling with for weeks now. My gut instinct tells me to use polypropylene for all of the tanks with exception to the sealing bath, where I should use 316 stainless steel. Help? Thanks!
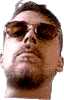
Daniel DeGueldre
anodizing shop entrepreneur - Ste. Anne, Manitoba, Canada
A. Your choice of tank materials is close to okay, but polypro is no good for the bright dip, which should be 316L stainless and double walled for its 200+ °F temperature. Please try to see a bright dip tank because it's really nasty and you should know what you are getting into so you can plan accordingly. Most beginners would pass on bright dipping for the first few years :-)
For a benchtop installation I'd go with air agitation based on overall cost.
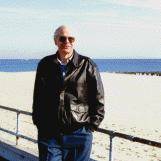
Ted Mooney, P.E.
Striving to live Aloha
(Ted can offer longterm or instant help)
finishing.com - Pine Beach, New Jersey
2004
First of two simultaneous responses -- 2004
Q. I thank you for your advice Mr. Mooney. You have set me at ease a great deal. It is always nice to hear that your gut feelings are, at least, not incorrect. I of course wasn't thinking clearly when I included the bright dipping tank into the polypropylene category. It was in a sense, a brain fart at best. Thank you for clearing that up. Is my face red yet?
Secondly, I am somewhat familiar with the nastiness of the bright dip bath. I had mixed a small batch (2 gallons) a few months ago and did some experimenting with it. Indeed, as you have warned me here (and as I was warned at the time) it is certainly not something to be taken lightly. Air purification and a fume scrubber is at the very least essential. Not a fun cocktail for even the most professional of users I would assume. None-the-less, I still intend on furthering my experiments with it.
This brings another question to mind, a question I will ask in a new post but will propose it here first. Does anyone have any details on how a fume scrubber works. As you may have guessed it, Mr. Joe-Handy over here intends on building his own. Any information is greatly appreciated. Thanks all!
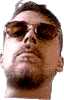
Daniel DeGueldre
anodizing shop entrepreneur - Ste. Anne, Manitoba, Canada
Second of two simultaneous responses --
A. The bright dip tank needs to be a double wall tank and the weld rod should be an ELC grade of 316.
If you adequately support the tanks, rotationally molded tanks are the best buy for the buck. Low temp tanks can be polyethylene. The seal tank needs to be polypropylene. Wood that is oil based paint will stand up to work for years. The seal tank needs full plywood support that is banded by 2X4s. 2X4s at the top and bottom will work well for the other tanks. A third mid band would help the tanks keep their shape a lot longer.
Mechanical agitation, by hand, is adequate for all of the tanks except rinse and anodize. Oil free air works best there.
James Watts- Navarre, Florida
2004
A. Hi everybody. First of all I'd like to write that PP lined tanks for sealing are sufficient. But If I might advice you I would use any special chemicals for sealing process to decrease the needed operating temperature instead. There are many special products on the market at least in Europe. Those agents mainly on the basis of nickel (II) acetate allow you to decrease the sealing temperature to approximately range of 20 to 25 °C (68 - 77 °F). This will save you money for heating and ownership cost for special high temperature resistant equipment.
Marek Cihlar- Roznov p.R., Czech Republic
March 18, 2009
Q. Which grade of SS should be preferred for construction of tanks to be used for hot alkali etching or neutralisation with nitric acid during anodizing process?
Rajabhau Kalbandhe- Nagpur, Maharashtra, India
September 14, 2012
A. Hi Rajabhau.
I'd probably prefer vinyl ester fiberglass, but I think type 304 Stainless is probably sufficient.
Regards,
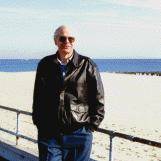
Ted Mooney, P.E.
Striving to live Aloha
(Ted can offer longterm or instant help)
finishing.com - Pine Beach, New Jersey
September , 2012
Q, A, or Comment on THIS thread -or- Start a NEW Thread