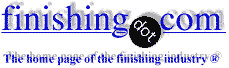
-----
Platinum plating on silver Q&A Problems & Solutions
Q. One of my clients does platinum plating over silver on a jewellery article. Black spots are appearing through the surface layer. What can cause these? Is there a general cause for them, do I need to get the article and get more information? I do not know if an interlayer has been applied before the Pt, in fact I only have their word that the top layer is Pt!
I look forward to any suggestions.
David Jarvisanalytical services - Sheffield, South Yorkshire, UK
2004
A. Electrodeposited Platinum is so stressed that it is always cracked. Silver will come right through the cracks and show up as black tarnish on top of the platinum. Use an under-layer of bright nickel instead of bright silver. Your plater should know better.
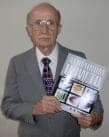
Robert H Probert
Robert H Probert Technical Services

Garner, North Carolina
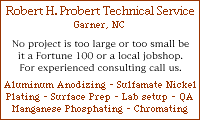
Q. Nickel cannot be used as an underplating in the UK because of the restrictions placed on it by the European Directive 94/27/EC. This is the case for articles in close and prolonged contact with the skin. If Ni is available then it may cause contact dermatitis and may lead to a prosecution in the UK. Are there any other recommended barrier layers that can be applied?
David Jarvis [returning]analytical services - Sheffield, South Yorkshire, UK
2004
A. Palladium, gold, to mention a couple.
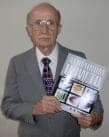
Robert H Probert
Robert H Probert Technical Services

Garner, North Carolina
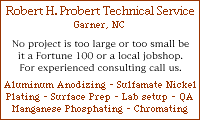
![]() |
A. Nickel barrier layers are prohibited in jewellery in the EU as they can cause "nickel itch" which is dermatitis. One alternative is copper-tin alloys (bronzes) such as miralloy. I would think the original problem is due to a porous coating of platinum. This can be overcome by using a thicker coating (expensive) or a suitable barrier layer such as Cu-Sn. Alternatively, porosity can be reduced by using pulse plating of the platinum, but it will not totally eliminate it for thin coatings. ![]() Trevor Crichton R&D practical scientist Chesham, Bucks, UK A. Palladium should be a good barrier layer. Even a thin layer of Palladium will provide a dense non-porous layer and prevent diffusion. Many jewelery makers are now shifting from Ni to Pd as undercoat. Good luck. Karthik Thambiduraielectronic components - Norwood, Massachusetts |
A. Platinum plating on gold flash has good adherence.
Vanajambika Jeyakumar- Chennai, India
A. Oxidising gases and formaldehyde can cause black spots on silver, as can acidic fine particles from fly ash (coal burning). Diesel and gas fumes could also be the culprit.
This could be the result of nearly pollution ... have them check their local environment.
- Chamois, Missouri
2006
Q. Hello,
I'm the R&D Bench Jeweler at a small manufacturing company in the midwest. We make laser engraved keepsakes, precious metal jewelry in sterling and various gold karats and colors. Hopefully I'm giving sufficient information here.
We recently installed a new larger plating plant which has included a switch from a final finish in Rhodium to a Platinum finish. Our Rhodium line is small with 1.5L tanks and uses a 12 hook rack. The new plant has 15L tanks. We haven't been able to complete our switch to the new line due to some persistent issues on the final product.
Besides the degreaser and neutralizer, we have Palladium (we had to introduce this back into the line), Platinum and Flash Yellow Gold. The original plan had been for Platinum and the Yellow Gold. (The Gold isn't a problem. We plate brass display pieces with Palladium and then the Gold. No issues there.)
We are plating Sterling alloys (getting more information on exactly what those are) and also 10K/14K White Gold. Almost everything is highly polished on the front surface and brushed satin finish on the back. The majority are flat stamped and die-struck pendants or charms. Some are hollow pendants and have curved (convex) outer forms or they are lockets with a satin (brushed) finish. The plating process is Degreaser>Neutralizer>Palladium>Platinum. The Palladium is plated at 2.0V for 2:00 minutes, the Platinum is 1.8V for 2:00 minutes. The rack is 32 hooks on 4 rows.
No issues show up with the White Gold, and the hollow products plate without issues. The flat pieces are where the problems started. Originally we were only going to plate with the Platinum, but these pieces would show streaks vertically up the face of the piece. I call them "hydrogen trails". The pieces have engraving on the front (a fingerprint) and the trails emanate from those deeper areas.
The metal our supplier uses has been problematic in other areas. These are separate issues from plating and another project for me to solve, but I think for some of the same reasons. Polishing shows a great deal of porosity which is odd on a struck item. Ultrasonic cleaning sometimes produces an etched pattern on the polished surface. We are talking to the vendor about the alloy and what is happening to the metal before we receive it. Maybe having an electrolytic reaction in the tank? Solution composition, heat or time may be factors.
Current thinking is that the engraving is exposing the more porous granular structure of the metal. Maybe material was caught in those crevasses and being ejected in the Platinum. We added Palladium as a strike coat to prevent that from happening. I was told the sterling is reacting with the sulfuric acid in the Platinum bath and forming a lot of hydrogen bubbles. The Palladium seemed to have solved the problem. We got about a week of production plating through the line, then other issues cropped up.
I had neglected to take pH readings on the Palladium bath and it had dropped to about 6.0, when it should be closer to 8.0. I didn't know ammonia
⇦ on
eBay or
Amazon [affil link] evaporated and the pH was sliding down the scale. I fixed that with Potassium Hydroxide. Plating appeared to be fine after the correction. I use strips of Hull Cell
⇦ huh?
Panels to test the line before plating pieces. My usual test for pieces is to put about 6-8 on the rack and see the results.
When we started production again, we decided to go with 12 pieces in case we did see problems. Each run had 1-3 pieces with the hydrogen trails again! The Palladium was supposedly preventing that from happening. We tried neutralizing between the Palladium and Platinum with no change. I plated 8 pieces and had no flaws. I plated 10 pieces and had some with faint trails.
Fortunately we still have the Rhodium line set up. However I have to solve this because we don't want to order more Rhodium and want to take that line down. We can't hop back and forth forever. I am very frustrated because things work and then they don't.
My questions are:
What exactly is happening with the sterling and Platinum reaction?
Would the number of pieces matter- more resistance?
I'm not sure which way to go in solving this. I'm guessing that the tiny deep crevices in the engraving are not fully plating in the Palladium. But do I increase time, raise the voltage or change the voltage/time in degreaser?
RFQ: I'd like to find a plating consultant with experience in these alloys and jewelry manufacturing. Any insight is appreciated.
- Lee's Summit Missouri
February 23, 2023
privately respond to this RFQ
Ed. note: As always, gentle readers: technical replies in public and commercial replies in private please (huh? why?)
Q. Unfortunately I don't know if I can capture a picture since I can't see the pits with the naked eye. I have to use a jeweler's loupe. (Yes we are that picky.)
I've been tweaking the voltage up on the strike coat (Palladium) bath from 2.0V to 2.15V so far. We are plating sterling silver and white gold pendants and charms. I've posted bout the problem we're having with the sterling pieces. Tweaking the voltage is one of the variables I can play with.
Plating Pd 2:00 minutes at 2.15V, Pt 2:00 minutes at 1.8V.
I'm starting to see tiny pits after the Platinum bath on a few pieces. The pits aren't round, they stretch a tiny bit in one direction. It almost looks like scratches. The pieces we plate are different shapes, but the size of a jewelry pendant.
I've noticed the amperage fluctuates considerably in both baths. I thought maybe the pieces moving slightly on the rack due to the current from the pump. Most pieces hang from a jump ring, which means the piece can move a lot.
I also seen the Platinum rectifier has tiny jumps in the voltage from 1.8V, to 1.82V while plating. Is this OK or possible source of some problems?
Thank You,
R&D Bench Jeweler - Lee's Summit Missouri
February 27, 2023
A. Hi Ruthanne, sorry I'm taking so long to get back to you. I don't have the chance to get on the site as much as I'd like to.
To answer your last question, the voltage fluctuations are not great enough to be a concern. What concerns me is the substantial fluctuations in amperage, which will naturally affect voltage anyway. Sounds like your pieces are losing contact with the hooks on the rack due to solution movement, or there may be a loose connection in the hook / rack connection. You can check the conductivity with an ammeter on the Ohm setting. Hold one lead at the point where the rack attaches to the cathode, and the other on separate conductive scrap piece on each hook. I like using copper. The resistance reading will tell you if there's a problem. The solution movement may be facilitating the bad connection. Hope this helps.
- Cazenovia, New York USA
March 18, 2023
Q, A, or Comment on THIS thread -or- Start a NEW Thread