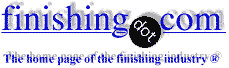
-----
Blisters of sulphamate nickel plating after sintering

Q. We plate a copper flange with Sulphamate Nickel (70-100 microinch) and sinter it in dry hydrogen at 800 °C. I am getting roughness ( small blisters) on the surface after sintering in Hydrogen. We use a local plater for this process and getting inconsistent results from batch to batch. We supply the copper after annealing at 875 °C. Is there anything I can do with sintering or annealing temperature to correct this or should I look for another plater?
Sara Mathew- San Jose, California, USA
2004
![]() |
? I am a little confused. Does your term "sinter" mean that you apply the heat and pressure after plating on a solid substrate, and if so, why? Or is it that you produce the copper flange by powder metallurgy and then sinter the part again after it was plated? Guillermo MarrufoMonterrey, NL, Mexico 2004 A. One likely cause is caused by insufficient cleaning prior to annealing. Baked-on surface contaminants are very difficult to remove. Be sure to thoroughly clean the copper before annealing. Another possible cause is insufficient cleaning by the plater prior to plating. Another is hydrogen entrapment. To solve this one, bake at a low temperature, 275 °F for about 1 hour to remove hydrogen before sintering. ![]() Don Baudrand Consultant - Poulsbo, Washington (Don is co-author of "Plating on Plastics" [on Amazon or AbeBooks affil links] and "Plating ABS Plastics" [on Amazon or eBay or AbeBooks affil links]) A. The problem is that the part is not completely clean. There is also a remote possibility that it has been over etched. The plater could probably experiment with other cleaning or etching solutions to find something that will work better. You can help by providing an annealed part that has less oxidation. This means a clean vacuum furnace or a reducing atmosphere furnace with an inert gas cool down for both. 875 °C seems like a high temp for an anneal cycle on copper. James Watts- Navarre, Florida |
A. We have seen blisters on copper that has been fired if it is not oxygen free copper. It might have nothing to do with the plating at all but the base material. I would try your exact same processes but with oxygen free copper and I'm betting it will be successful.
Ben HartfordDesign/Plating Engineer - Larens
February 25, 2025
Q, A, or Comment on THIS thread -or- Start a NEW Thread