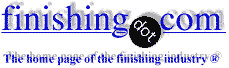
-----
Need a coating better than Titanium Nitride (TiN)
Q. Thin dense chrome vs titanium nitride?
Evaluating coatings 17-4PH DH1150, doubled aged stainless steel that is seeing pitting corrosion due to chlorides in oil and gas application. Would like input about thin dense chrome vs. titanium nitride on high tolerance parts.
- New Caney, Texas
A. Chrome is highly sensitive to chlorides. Not recommended
Bill Marrufo
- Monterrey Mexico
March 10, 2022
⇩ Related postings, oldest first ⇩
Q. I'm searching for a surface treatment for mold knock-out pins made of H-13 that can stand up better than Titanium Nitriding. The pins see temperatures in excess of 500°F and need to be self lubricating. We are molding small parts and the present coating breaks down after a short cycle allowing the pins to scratch. I've tried a few of the higher profile brand name coating processes without much success.
Bob H [surname deleted for privacy by Editor]- Essex, Connecticut
1999
A. Hello, Bob.
Titanium Nitride has taken over some of the applications formerly associated with hard chrome plating and has proven better sometimes, but not always! Have you tried chrome plating -- which offers not only hardness and wear resistance, but lubricity and low coefficient of friction as well?
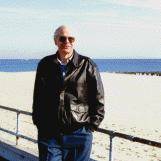
Ted Mooney, P.E.
Striving to live Aloha
(Ted can offer longterm or instant help)
finishing.com - Pine Beach, New Jersey
1999
A. As far as hard coatings go TiN is really the bottom of the barrel. Other coatings that might work better for you include TiAlN, AlTiN, Aluminum oxide. Maybe CrN or CrC. Most all of these are available through the larger coating houses.
If this is for a die casting operation and the pin surface is in contact with the molten aluminum at some point then I would definitely suggest using Titanium boride if you can find a supplier but otherwise use CrC.
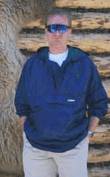
John Davis
- Berthoud, Colorado, USA
1999
A. Are you sure a coating is necessary? Our research shows that a lot of the galling created in mold knock out pins is created when the retained austenite in the pins transforms to martensite. All heat treaters leave between 9% to 20% retained austenite. The martensitic crystal is larger than the austenitic crystal and the part grows as the austenite is transformed by the heat and vibration of molding. Since there is very little clearance in ko pins, the part seizes.
Cryogenically treat the mold and pins. This will convert the retained austenite to martensite, stabilize the mold metal, and will increase the wear resistance of the moving parts of the mold and the gates and runners. We have achieved excellent results for our customers by just doing this. However, a coating added to the pins before the cryogenics will work synergistically with the cryogenics.
- Streamwood, Illinois
1999
A. The suggestion of using a Titanium diboride or Chromium carbide coating appears to be a sound one. Have you tried electrospark sputter deposition of these coatings? Some of our clients with screw machine collets, where galling is common, have benefited by this process.
Ram K. Iyengar, Ph. D.- Littleton Massachusetts
2000
Have you considered coating with diamond-like carbon (PECVD), then ion-implant using a few hundred KeV nitrogen ions? One ends up with a nitride/carbide layer within the surface which is in compression, not tensile, so is not dependent on the young's modulus of the substrate. Dislocations further into the bulk metal are 'pinned'. The result is a very hard, wear-resistant surface with good release properties. I had this done for a mold to produce microtitre high-density wells in the UK 4 years ago. Should be companies in the USA too.
Bob Sunderland- Northwood, England
2001
![]() |
? Many many moons back, Bob H of Essex, Connecticut wrote: - Littleton Massachusetts March 28, 2009 Hi, Dr. Iyengar. Sometimes we readers have a fairly interactive discussion with the original inquirer; sometimes they get back to us months or years later. But over twenty thousand people visit this web site each day; it's no graveyard. Some readers are forbidden by company rules from posting -- but certainly they profit from reading solutions to problems that echo their own. ![]() Ted Mooney, P.E. Striving to live Aloha (Ted can offer longterm or instant help) finishing.com - Pine Beach, New Jersey March 28, 2009 |
Mold coating to prevent Polyethersulfone adhesion
Q. I'm having problems injecting Polyethersulfone. It presents adhesion to the mold, causing the final product to break on key points. Do I need to apply any kind of counting to the steel, such as Chrome plating or Titanium Nitride?
Marcello Iliescu- Figueira da Foz, Portugal
November 25, 2016
Hi Marcello
You should ask your supplier of PES for advice. The problem may be in the mold design or molding conditions; temperature,pressure etc. It is unlikely that we can help you on line.
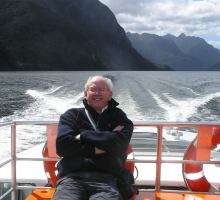
Geoff Smith
Hampshire, England
November 26, 2016
A. Hi Marcello,
Can you try silicone spray
⇦ on
eBay or
Amazon [affil link]
as a release agent?
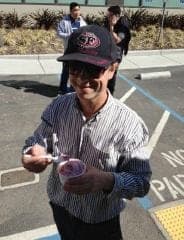
Blake Kneedler
Feather Hollow Eng. - Stockton, California
January 1, 2017
February 13, 2017
A. Best permanent release coatings are (from fair to excellent):
Plain high phos electroless nickel
TiN
Regular hard chrome (flash)
Thin dense chrome
Electroless nickel composite with Teflon particles.
Also, if you need to paint, glue or weld something on top of your molded parts do not use silicon release agents.
Finally, review you draft, search for deformations, negatives, etc.
Good luck!
"Respectful Mexico/USA dialogue" - Monterrey, mexico
Thanks cousin Guillermo.
Regards,
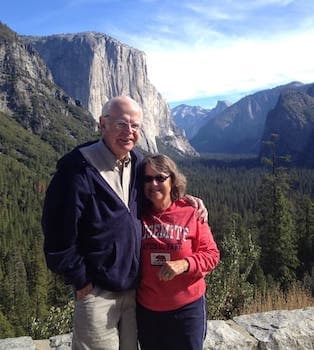
Ted Mooney, P.E. RET
Striving to live Aloha
(Ted can offer longterm or instant help)
finishing.com - Pine Beach, New Jersey
February 2017
Q, A, or Comment on THIS thread -or- Start a NEW Thread