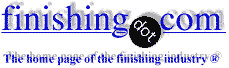
-----
Water-break test for cleanliness?
Q. Our plant does chemical cleaning and passivation of various aerospace components and within these processes we do a Water Break Test to ensure the parts are clean. The question has arisen, as to when in the process is the WBT to be done. Some say after the rinse following the alkaline cleaner and some say after the final cold rinse at the end of the entire process.
Is there an expert out there who can give me a definitive answer or a definitive spec?
Raymond Berryaerospace - Jackson, Michigan, USA
2004
A. Hi Raymond,
The water-break test is normally done after the rinse following the cleaning step. If your parts are not clean at this stage, then your passivation process may be adversely affected. You can perform the test after the final stage and you should still get a water-break free surface. But you won't know for sure whether the surface was perfectly clean following the cleaning step if you do the water-break test at the end of the line.
George Gorecki- Naperville, Illinois
A. Raymond, you have asked an interesting question. Having formulated and done trouble shooting on cleaning applications for over 20 years, I consider myself as somewhat of an expert in the field. My answer to your question would be the parts should be water break free at the end of the process. I would even go a step further and say the water break test should be done with pure water, not water from the process. The reason for this is the water from the process could potentially be contaminated with surfactants from the cleaning operation. These materials reduce the surface tension of the water and may allow the water to wet out and sheet on surfaces which are contaminated. It is very likely the rinse after the cleaning stage is contaminated with surfactants from the cleaning stage so it will general wet out better than the other rinse stages.
Roy NussTrevose, Pennsylvania, USA
A. Dear Raymond,
The water-break test is normally done after the rinse following the cleaning step to [indicate the need for] re-cleaning it if it still has any organic soils; but your rinse water must be very clear and not have any chemical contamination from the chemical cleaner tanks (surfactant). If you are not sure from that, you can take a sample out the line and check it by clear water.
Aly Gomaa- Cairo, Egypt
A. In my opinion both are valid answers. Only that Mr. Gorecki's emphasized the theoretical point of view while Mr. Nuss got into the practical aspects of the everyday situation. Conclusion: whether you do the WBFT in between or at the end, be sure to use the proper water. Indeed, when there is doubt about the test and if the base material tolerates it, a brief rinse with week acid water will neutralise alkalies and help wipe off surfactants, revealing hindered contaminants.
Guillermo MarrufoMonterrey, NL, Mexico
Multiple threads merged: please forgive chronology errors and repetition 🙂
Water break timing
Q. I need to answer to a NADCAP question for water break. They want us to specify the time we have to spend on each water break. According to them it is expected there is a defined minimum time that is required for the water break inspection. If anybody know, please let me know. We run small parts not bigger than two foot and regular size is half a foot long. Thanks
Simon Joshiplating - Baltimore, Maryland
2006
![]() |
A. It's your spec, so put in whatever time you want. 10 seconds is reasonable. ![]() Jeffrey Holmes, CEF Spartanburg, South Carolina A. WE JUST WENT THRU OUR NADCAP AUDIT AND THE CORRECT ANSWER IT'S - CHATSWORTH, California |
A. This may be a vague answer but according to physics, gravity helps the water blanket to break. Water will break easily on a dirty vertical surface (perhaps not over 2 or 3 seconds in my experience) whether a horizontal may take longer.
Guillermo MarrufoMonterrey, NL, Mexico
A. Maria, there is no correct answer unless you can quote a national or international specification, or a specification by the OEM or a buyer's spec.
James Watts- Navarre, Florida
2006
Q. Maria, Can you site a reference for the correct answer of 30 seconds?
Chris Jurey, Past-President IHAALuke Engineering & Mfg. Co. Inc.

Wadsworth, Ohio
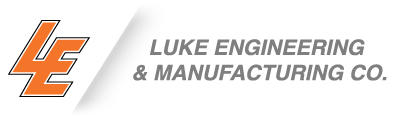
2006
A. All:
It is interesting that I was just reading a spec of phosphate TT-C-490
[from DLA]
and it has a mention of 25 seconds for water break test.
I agree that this must be plater's judgment and he just has to follow what he has written in his procedure but if you are following a certain spec. then you MUST follow the rules of that spec.
Thanks,
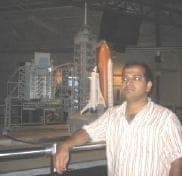
Hemant Kumar
- Florida, USA
![]() |
A. A slightly rough surface such as a fine abrasive finish will hold water without breaking far longer than a highly polished surface. 25 seconds would seem about right for a phosphated surface, but that will vary by the type of phosphate. James Watts- Navarre, Florida A. In our hometown the parts will dry out in 30 seconds! Sounds a little too much to me. Remember dew point. Guillermo MarrufoMonterrey, NL, Mexico |
A. If I am remembering correctly, ASTM F22 uses 1 minute as a guideline for the water break test.
Brigitte Arnold- Des Moines, Iowa, USA
A. I was mistaken. It's actually a 1 minute test per ASTM F22 as the previous response has stated.
MARIA PEREZ- Chatsworth , California, U.S.
A. The water break timing will vary according to porosity or roughness of finish, air temperature, temperature of water, atmospheric humidity, airflow over the part, and cleanliness of rinse water.
All are variables, so it is down to the plater to decide whether or not he is satisfied with the waterbreak timing.
plating. etc. - Belfast, Maine
A. Examples for these tests can be found in customer specifications or an ASTM F21 (atomization test) or ASTM F22 (water-break test) or ASTM B322 (general cleaning of base metals) or DEF Stan 03-2
NA if you only have barrel and/or automated lines.
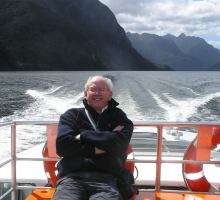
Geoff Smith
Hampshire, England
& ;I find this question and the responses very interesting!
There is probably nothing wrong, when specifying an atomizer test for a lab situation, to require that the water must not break for 60 seconds. But if this is mis-extended to a production situation, and we make believe that we can make the simple go/no-go water-break observation quantitative by counting the seconds to water break we're being silly. Guillermo and Steve are right. To claim that a surface that maintains a water break for 60 seconds is cleaner than one which maintains a water break for 30 seconds which is cleaner than one which held for 20 seconds would be ridiculous, and specs gone silly ... talking ourselves into believing we have a quantitative test when we have chaos.
To actually make a water-break test quantitative would require the use of an atomizer with a series of solutions of varying but known surface tension, so we could say that it holds at this surface tension and breaks at that surface tension rather than trying to count the seconds to water break in an atmosphere of unspecified humidity & temperature after a dip in non-analyzed rinse water at undefined temperature, on an undetermined surface topography on an unknown substrate. It's ridiculous to try to pre-specify the required seconds to water-break in an actual production situation. Sorry, but if anyone thinks that the seconds to water break indicates a different level of cleanliness, I call B.S. :-)
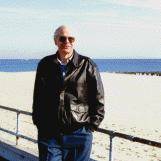
Ted Mooney, P.E.
Striving to live Aloha
(Ted can offer longterm or instant help)
finishing.com - Pine Beach, New Jersey
2006
Q. What are the expected results of the water break test after the next step in the process, i.e., passivation? I ask this because I use technology that allows me to paint or plate without the use of cleaning chemicals, phosphates or acid activation, but cannot pass the water break test after cleaning. I clean using distilled water with no chemicals and parts pass all clean tests but not water break -- how do I explain this?
Walter Johnson- Machesney Park, Illinois, USA
2006
A. I don't believe that a waterbreak-free surface is required for most painting, so maybe you don't really have much of a problem on that one.
For many decades a waterbreak-free surface has been considered a necessity for electroplating; so that one is pretty hard to get around. And I have to question your contention that the parts are fully clean if they fail what is, after all, a test designed to prove that parts are clean.
But maybe the test isn't really fair after all. Have you plated parts and then tried some extreme baking cycles to prove that they don't blister? Have you tried bending electroplated coupons over a small diameter mandrel? Have you smashed brittle parts and looked for chips of plating? Have you performed a "modified Ollard" adhesion test? If you can demonstrate proper adhesion, that really should do it, because proper adhesion is the driver that is requiring that clean surface. Good luck.
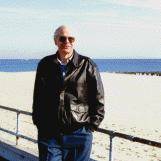
Ted Mooney, P.E.
Striving to live Aloha
(Ted can offer longterm or instant help)
finishing.com - Pine Beach, New Jersey
Q. In our plant we are doing chemical washing for removing the oil and grease on the surface of casting. Our process is degreasing (I) 1 minute washing , degreasing (II ) 1.5 minutes washing, water rinsing (I) 1 minute washing, water rinsing (II) 1 minute washing, and Passivation 1 minute washing. I want to know whether water break test done before passivation or after passivation which one will give perfect result for ensuring surface cleaning.
Jagadeesh- Chennai, India
February 21, 2012
A. Hi Jagadeesh. You want the part clean before passivating it, and water-break is really a cleaning test, so you check before passivation, while trying to avoid being fooled by any surfactants in the cleaning solutions, which lower the surface tension. So, after the last rinse before passivation would be the best time to test or observe. Good luck.
Luck & Regards,
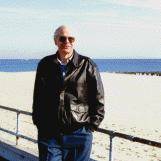
Ted Mooney, P.E.
Striving to live Aloha
(Ted can offer longterm or instant help)
finishing.com - Pine Beach, New Jersey
Q. How do I perform a water break test and what are the results to look for?
Allan Mcguireself interest - Cleveland, Ohio, USA
April 28, 2013
A. Hi Allan. It is difficult to answer your question because it's rather abstract. You haven't yet told us who told you to perform it, or why, whether you are doing it to plated parts, whether the parts are rack plated (or barrel plated such that you can't see whether there is a waterbreak or not), whether you must certify it or you are just wanting to use the test as an in-house aid, etc.
But I'll start with the general proposition, then maybe you can refine the question . . .
Electroplating is a process where one layer of metal is "grown" upon another metal, and for this to be done correctly and with full adhesion requires that the part be free of soils and oxide layers, so the metal grows on metal. Your cleaning process removes the soils, and one way to know that the soils have been removed is to look for any "beading" on the surface of the parts when they are lifted out of the tanks. If the part is free of organic soils, water will form a "sheet" on it, rather than wet and dry areas. Water should not "break" and leave any dry spot on the parts until it actually evaporates.
The previous discussion about when to look for this waterbreak largely has to do with the fact that cleaning solutions have surfactants (surface tension reducers) that can tend to "mask" the waterbreak. So, in production, the plater will not necessarily trust what he sees as the part leaves the cleaning tank, but what he sees when the part leaves the rinse tank after the acid activation dip.
But in addition to this "in process" observation, it is also possible to pull parts out of the line in mid process and perform more exacting water-break tests. There are standard waterbreak tests including ASTM F22. Good luck.
Regards,
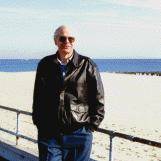
Ted Mooney, P.E.
Striving to live Aloha
(Ted can offer longterm or instant help)
finishing.com - Pine Beach, New Jersey
Cad plated parts are failing waterbreak test preparatory to priming
Q. We try to clean the cad plated parts with acetone or MEK before application of primer but test for waterbreak-free fails, why?
Houman zarkesh- Canada, montreal
April 26, 2017
A. Hi Houman. I have to apologize for my ignorance :-(
I haven't tried it and have no actual knowledge of it, but I don't think I would have expected that approach to yield a waterbreak-free surface. Can you tell us a little about the spec or requirement that cad plating be cleaned to waterbreak-free before priming? Thanks!
Regards,
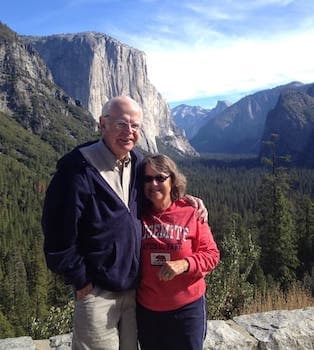
Ted Mooney, P.E. RET
Striving to live Aloha
(Ted can offer longterm or instant help)
finishing.com - Pine Beach, New Jersey
Q. Dear Expert, I am Siswahyudi from Bandung INDONESIA, need your advice:
On NadCap check list for electroplating they have this sentence:
"Were all production hardware and test pieces maintained wet, and was a waterbreak-free surface observed after the cleaning cycle?"
What the meaning of "Production Hardware", is it the Part or component that we process?
How about if we load a lot of parts, let's say 200 pcs loaded, must we check one by one for all of each surface of the part within 30 seconds? Can we check by random or use a test piece to be representative of those processed?
I am really grateful if expert could support the best answer by your experience during NadCap audit.
- Bandung, INDONESIA
March 6, 2019
A. Hi Siswahyudi
Production hardware refers to the parts you process that will eventually be used in aircraft.
The requirement to carry out a water break test is not decided by Nadcap, it is a requirement of your prime customer. Nadcap simply confirms that you are processing in accordance with your sales contract.
Water break must be confirmed on each and every part you process to confirm a clean surface suitable for further processing. If a part fails water break it will certainly have poor adhesion of the coating and probably fail in service if not detected at final inspection.
In service may mean a critical aircraft part at 30,000 feet.
Nadcap auditors fly in many aircraft and they have a personal interest in good processing!
But it is not difficult for a trained operator to view a rack of parts in a few seconds. A failed test is usually very obvious and it is much easier to re-clean a jig load of parts than to have them all fail later.
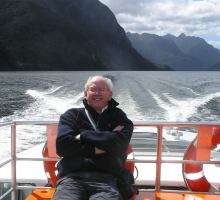
Geoff Smith
Hampshire, England
Hi Geoff Smith.
Thanks for your advice,
- Bandung, INDONESIA
Q, A, or Comment on THIS thread -or- Start a NEW Thread