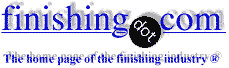
-----
40 volts vs 22 volts
Q. I have had mixed success getting test panels (2024) to pass the salt fog corrosion test (336 hours) when processed as MIL-A-8625 / MIL-PRF-8625 [⇦ this spec on DLA] Type I @ 40 volts. However, the panels pass beautifully @ 22 volts. All chemistry, temps, pH are closely monitored etc. I have tried several seals at the 40 volt with none consistently succeeding. Any ideas? Is it possible that the anodize is simply "burning" at the 40 volt setting? The coating weights at 22 & 40 volts are very similar, in fact less than 50 mg/ft2 apart (40 volts just slightly more). Also, is there any reason a Type I Class 1 process can't be run at 22 volts vs 40? I can't find any spec that ABSOLUTELY must have 40 volts.
Garrett Beane- Phoenix, Arizona, USA
2004
![]() |
A. Para.3.4.1 of MIL-A-8625F specifically states that "Type I coatings shall not be applied to aluminum alloys ... when the total allowable contents of nominal alloying elements exceed 7.5 percent." According to my references and calculations, 2024 meets this limitation and should not be anodized to Type I but rather to Type IB at 22V. Chris Jurey, Past-President IHAALuke Engineering & Mfg. Co. Inc. ![]() Wadsworth, Ohio ![]() 2004 A. Garrett, "22V" and "40V" is completely meaningless in any setup other than the one you are using. The anodizing current density (what actually does the anodizing) could be anything. We need to know the current densities that 22V and 44V correspond to in your tank, or the actual current applied to each part and their surface areas, and we can calculate it. If everything else stays the same, 40V would be 45% more current than 22V. The coating thickness should be 45% more in the same time period, ignoring dissolution effects for the moment. The fact that the coating densities appear the same with a 45% change in current density is very suspicious. Paul Yursis [deceased]- Columbia, Maryland, USA Ed. note: it is our sad duty to advise of the passing of Paul Yursis in August 2005. |
A. I recently had 2024 failures with chromate in your neighborhood. Panels from three companies absolutely would not pass chromate salt spray any-which-way-we-tried. Panels from a fourth company breezed through with typical shopwise sloppiness. So go try another panel source. 2024 is very tricky. Age alone affects salt spray resistance. At least look at the panels with a 10X loop and circle the original pits. Also look for chlorides in the anodizing solution.
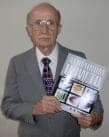
Robert H Probert
Robert H Probert Technical Services

Garner, North Carolina
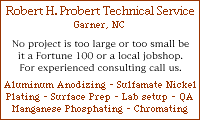
2004
Q, A, or Comment on THIS thread -or- Start a NEW Thread