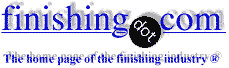
-----
Tin plating: how to improve Salt Spray hours and high humidity corrosion resistance?

this text gets replaced with bannerText
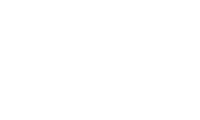
Q. We have a customer who uses Tin plated parts for energy meters which they get a life of 5 years for the coating. This they want to enhance to 10 years. The criteria is Tin should not corrode. The base material is mild steel and Brass, Tin plated 4 -5 micron with a Copper under coat for 4 - 5 micron.
Whether the specified thickness of Tin and the type of underlayer are good enough for the enhanced coating life without corrosion.
Also suggest the test method for simulation / acceleration test to confirm the given product works for the expected period.
Thanks
chemical company - Bangalore, Karnataka, India
January 25, 2023
A. Hi Abubacker
I'm probably not understanding the phrasing of your question because if your customer is presently getting 5 years of life with the current system, how could they possibly get double that life without changing anything? :-)
But we've appended your inquiry to a thread which I believe has the answers you seek.
Reading between the lines of Danny Neidel's posting, if 5 microns gives them 5 years of life, 12 microns can probably be expected to give them 10 years, although I don't really understand the corrosion conditions / environmental conditions the tin plated components will be exposed to.
Luck & Regards,
Ted Mooney, P.E. RET
Striving to live Aloha
(Ted is available for instant or longterm help)
finishing.com - Pine Beach, New Jersey
⇩ Related postings, oldest first ⇩
Q. We have had a problem with a faulty batch of battery contacts demonstrating surface rust. The contacts are meant to be 5 micron nickel plated tin plate. For our immediate production requirements, someone has suggested replating the contacts with Tin with another 5 micron plating. 2 questions.
1. Where can I find a technical document that recommends tin plating thicknesses for high humidity environments? (I need to prove that this will correct the problem and not result in further failures in the field).
2. Is tin plating over nickel plating OK?
Thanks, I will be very grateful for a reply!
Ben Jacksonmedical equipment supplier - Melbourne, Victoria, Australia
2003
A. Hi, Ben.
Although tin plating over nickel plating is possible and is done, I think you will find that tin plating is not as corrosion resistant as nickel plating. If the original nickel plating was not corrosion resistant enough, replating with tin instead of nickel should not be expected to improve the situation. I don't think you will find the documentation you seek because corrosion resistance depends on so many different factors.
The problem seems to me to be that the nickel plating was not free from porosity despite the fact that it was spec'ed as reasonably thick. You say the components are "battery contacts"; if we're talking batteries for electronics in a benign environment, I'm having trouble understanding what went wrong that they are rusting. But if this is for some sort of battery exposed to the environment, 5 microns is not a lot of plating. Good luck.
Regards,
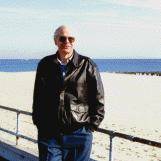
Ted Mooney, P.E.
Striving to live Aloha
(Ted is available for instant or longterm help)
finishing.com - Pine Beach, New Jersey
Multiple threads merged: please forgive chronology errors and repetition 🙂
Q. Can Pure Acid Tin obtain 240 hours in Salt Spray Tests? How can we achieve this requirement? Our client requests this and normally we plate to 24 hours, but not 240. The part is made of steel and processed in barrels, we don't know if we need to apply an undercoat of copper or nickel (thickness?) and what Tin thickness, as well as a chromate or sealer. Please advise regarding the best procedure.
Thanks for your help.
Sergio EnriquezJob shop - Guadalaja, Jalisco, Mexico
2004
A. Dear Sergio,
Yes, it can resist 240 hr in SS per ASTM B117. It depends on thickness and porosity of the tin layer. Tin will protect steel only if it is pore-free. Where that is not the case, the iron becomes anodic and strong corrosion follows.
According to ISO 2093 coatings are classified in four categories; group 4 extremely demanding conditions, group 3 demanding cond., group 2 moderate cond. and group 1 mild cond. Over steel the following thicknesses are required : 30, 20, 12 and 5 micron. Corrosion resistance can be improved by a copper-strike interlayer.
Test for porosity with Kesternich test (included in ASTM B545) or ferroxyl test, plate some test parts and check corrosion resistance in the salt spray chamber to set up process parameters.
Danny Neidel- Guadalajara, Jalisco, México
Q. Dear Danny,
Thanks for your help. I'm not familiar with ISO 2093. What salt spray resistance is expected for each service condition 4, 3, 2 and 1 with the thicknesses mentioned?
We plated the Steel part with copper, then 8 microns of Tin and a chromate and got only 144 hours? Any recommendations? What about the use of sealers?
Gracias por tu ayuda,
Sergio
Job Shop - Guadalajara, Jalisco, Mexico
A. Hi Sergio,
In the standard mentioned you need to plate 30 micron (group 4), 20 micron (group 3), 12 micron (group 2) and 5 micron (group 1).
To reach 240 hours in salt spray over steel you have to plate at least 20 micron. Chromates avoid staining in the parts, but it doesn't improve really corrosion resistance. If it is permitted (parts are not soldered after plating), you can use a organic sealer or lacquer. That is easy to make for rack parts, small parts in barrel tend to stick with each other. An organic sealer improves corrosion resistance 2-3 times, commercial products are available from local vendors.
I hope that's helpful.
Saludos
Danny Neidel- Guadalajara, Jalisco, Mexico
Danny,
Thanks for your help. I'll try with the 20 microns and a sealer.
Thanks again
Sergio Enriquez [returning]Job Shop - Guadalajara, Jalisco, Mexico
Q. Hi!
Our company has reel-to-reel plating of Au Ni, SnPB,& Ni finishes. Early this year, we plated a Sn-Ni finish on some electronics parts (Cu base). Plating specification is Sn = 2µm & Ni - 1.5 µm. Our practice on our finished products is to have a certain corrosion testing - High Humidity High Temp (HHHT) & Saltwater spray Test (SST). But we always encountered NO GOOD corrosion result in Sn plating when subjected to SST wherein development of black dots or discolorations were observed. HHHT result got no problem. Are Sn-Ni plated items appropriate for this kind of testing (SST)? Is this result after its corrosion test normal? Please advice.
Thanks ahead.
electroplating - Cebu City, Philippines
July 8, 2008
A. Hi Dianne,
Salt Spray test is not normal for tin coatings. Salt Spray test is a typical corrosion test for zinc or zinc alloy plating. Tin is not a common corrosion protection on parts that are exposed to severe environmental condition. For your application where tin is plated on components/parts NOT exposed to environmental condition, salt spray test may not be relevant.
- Laguna, Philippines
A. Hi Dianne,
You don't mention the Salt spray test duration? But with the thickness that you mention, I don't think that the parts will sustain even 24 hours.
Moreover, with the thickness as you mentioned, this part only can be used in an indoor and dry environment (no condensation can occur). So, if you do Salt Spray test, it's normal if the result is failure.
- Batam, Indonesia
Q. Dear Sir,
This is regarding the constant failures of the tin plating in our fasteners that we procure from our suppliers. These fasteners (nuts, bolts and screws) are made up of mild steel and are tin plated at another supplier's end.
Now, the problem of rust after some time has been reported from our esteemed customer and we are unable to come out of it after we have maintained the plating thickness up to 12 microns also. These fasteners are failing in salt spray test constantly. Now, the salt spray test is done for 48 hours and pics of the pieces found after it are attached.
My queries are as below,
1. Is it correct to conduct the SST on tin plated parts ?
2. If yes, then how to overcome 48 hrs. of SST ?
3. If no, then how to test the durability of tin plating ?
Please help on the above such that we may overcome the same.
Hope for a quick reply from your side.
Regards,
engineer - Noida, U.P., India
May 23, 2011
A. Hi Rishabh.
As you see, we appended your question to a thread that pretty much answers it for you. But if you now have more questions, please get back to us. Thanks.
Regards,
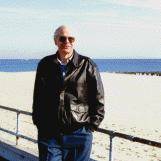
Ted Mooney, P.E.
Striving to live Aloha
(Ted is available for instant or longterm help)
finishing.com - Pine Beach, New Jersey
Q. I am doing some electronic assemblies which have sheet metal parts.
Base material is CRCA, and then after doing Tin plating I am unable to get salt spray life more that 5 hours.
But our customer needs salt spray life more than 72 hours.
Please guide .
- Pune , Maharashtra , India
July 27, 2012
A. Hi, Nilesh.
As you see, we appended your inquiry to a similar thread. As you will read, you are going to require rather thick tin plating to solve this problem, and possibly an organic sealer if the specs permit. But your current 5 hours may also indicate that you are not processing the parts quite correctly; the plating needs to be free of porosity.
Regards,
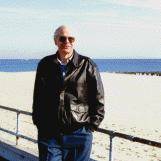
Ted Mooney, P.E.
Striving to live Aloha
(Ted is available for instant or longterm help)
finishing.com - Pine Beach, New Jersey
Q. Dear sir,
I am facing a severe rust issue on tin coated sheet gasket parts. This part is assembled in between engine exhaust manifold and elbow, and also a similar part is assembled in between elbow and silencer.
1) What's the SST life of tin coated part?
2) Is it advisable to do Aluminum coating over tin coated sheet to enhance SST life?
3) Our requirement is 240 hours SST?
4) Can we do Heat resistant black paint over tin coated sheet gasket part?
Please suggest to improve SST of tin coated sheet gasket?
Regards,
- CHENNAI , TAMIL NADU , INDIA
July 10, 2014
Q. If we have Tin plated (5 µm) on brass, then how much hours of Salt Spray Test to be recommended?
As our result I got Rust within 96 Hours -- How to Improve it?
- Pune, MH, India
June 24, 2017
Q. Please can anyone help me ...
My question is whether Electro-Tin over Copper can Pass the SALT SPRAY TEST per MIL-STD-202, Method 101 [link is to free spec at Defense Logistics Agency, dla.mil], Condition B?
We already tested several time and the result is not successful even with 24 HOURS test, we plated the parts with 0.000400" MATTE ELECTRO-TIN per ASTM B545 OVER 0.000100" COPPER per SAE AMS2418, maybe you can give me some suggestion. Thanks in advance
Eury DEL ORBE- Long Island City, New York, U.S.A
April 24, 2018
A. Hi Eury. There are a number of open questions:
Condition B is 48 hour salt spray, but doesn't define what constitutes passing vs. failure; that you need to determine from ASTM B545 or another spec. Are you sure your actual minimum thickness is 0.0004" as required by B545 SC2? Danny notes, and the literature does too, that you are pretty susceptible to porosity and thus galvanic attack at this thickness; bumping it up even a little can reduce porosity. Are you applying a chromate or an organic sealer, or nothing on top of the tin?
Regards,
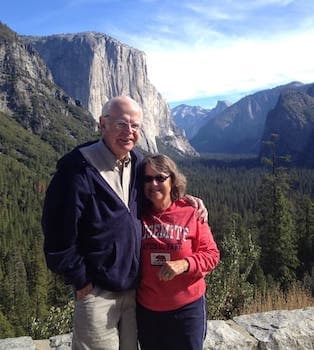
Ted Mooney, P.E. RET
Striving to live Aloha
(Ted is available for instant or longterm help)
finishing.com - Pine Beach, New Jersey
Q. Hi TED , thank you so much for you response, yes our parts are plated 0.000400" Tin over 0.000100" copper on brass metal. No we aren't using any sealer, our parts should pass salt spray test of 48 hours. As I said before we tried several times but test result is not successful, after test was found Abnormal Nicks, Pitting -- looks like tin plating layer came out; Then how much hours of Salt Spray Test for tin to be recommended? or which type of sealer you recommend.
How to Improve it? any suggestion will be very appreciated. regards Eury
- Long Island City, New York, U.S.A
A. Hi again. Sorry, but after 2 postings I still don't know your situation, so it is difficult to respond. I assume you are from the plating shop not the buyer, i.e., you are doing this plating yourself to someone else's requirements? And you know that the thickness everywhere is no less that 0.0004"? The substrate is cold finished steel? And you are experienced in tin plating but have just never salt spray tested it before? You are conducting the salt-spay testing in house? Do you do any other testing of your work, such as adhesion testing, perhaps bending the parts over a mandrel?
Do you do any soldering of the parts? Successful soldering in itself can be a good adhesion test and indicate that the surface is not oxidized or soiled, since poor pretreatment will certainly cause porosity and corrosion.
48 hours is probably not unreasonable for 0.0004" deposits; but you won't pass if there are pores in the plating due to excessive surface roughness, poor cleaning, poor activation, or poor plating practices. Generally the plating process supplier who is selling you your tin plating chemistry and pretreatment chemicals can advise you what sealers they suggest -- is your process MSA or stannate or what? Thanks!
Regards,
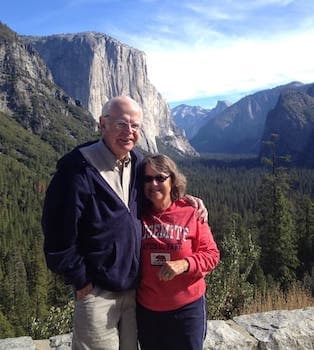
Ted Mooney, P.E. RET
Striving to live Aloha
(Ted is available for instant or longterm help)
finishing.com - Pine Beach, New Jersey
Q. I am coating Tin metal on MS 0.6 mm and 0.8 mm material and my thickness specification is 8 microns minimum.
My customer requirement for salt spray is 45 Hrs without WHITE RUST but every time I conduct the salt spray test, the specification which is given by customer is not met.
Is it possible to meet the above salt spray specification with 8 Microns of Tin?
Please guide.
Will be waiting for your valuable addition.
Quality Engineer - Bangalore, India
October 18, 2021
A. Hi Rajesh. You added your question to a thread which already contains some great info on the subject. I've personally never heard of testing for white rust on tin plating, but hopefully a more knowledgable reader will chime in. If there is such a thing, it would have to be prevented with some sort of post-treatment or topcoat. Please send some pics of this white rust to mooney@finishing.com for posting here if you can.
What constitutes passing or failing a salt spray test is usually defined by the specification. What specification are you plating to?
8 microns is less than the 12 microns required for even moderate service, so it's not a lot of thickness. And it's important to realize that tin plating is a barrier-layer coating, not a sacrificial coating like zinc plating. So, whereas pores and porosity in zinc plating may not be a major issue, they are crucial in tin plating because if the environment "sees" any steel base metal, the tin plating will galvanically force the underlying steel to rust.
It is normal for specifiers and shops to have acquired, due to previous experience with zinc plating, a mindset about salt spray testing along the lines of x thickness equals y hours. I would urge you and your customer to take a quick look at thread 1744. It's about salt spray testing of stainless steel, but it conveys an important idea: whereas salt spray testing of zinc galvanically "wears through" the coating, salt spray testing of stainless steel and barrier-layer coatings like tin plating is more a case of finding or not finding a defect.
Because of this pinhole and porosity situation, the shape of the parts and their surface condition can seriously affect corrosion resistance and salt spray results. If your customer claims and demonstrates that other shops pass their requirement with 8 microns, there may be a need for you to mechanically finish the parts before plating.
Luck & Regards,
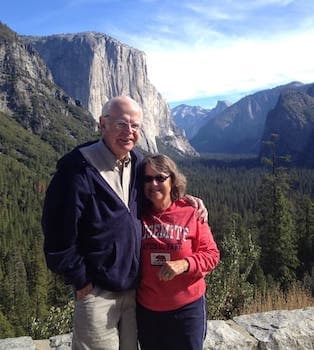
Ted Mooney, P.E. RET
Striving to live Aloha
(Ted is available for instant or longterm help)
finishing.com - Pine Beach, New Jersey
Sir, thanks for your valuable addition on the topic and for the detailed explanation.
It is great that you are sharing your knowledge to future generations, and I sincerely appreciate that.
Best Regards,
Quality Engineer - Bangalore, India
Q, A, or Comment on THIS thread -or- Start a NEW Thread