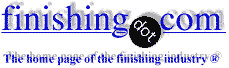
-----
Brush Plating Repair-repairing chipped plating
Here is my situation and progress thus far, any comments or suggestions would be greatly appreciated. We have small EN plated parts, (similar to a small spool of thread, without the thread, silicon iron substrate.) The parts get chipped or dented during assembly. The chips and dents then require plating repair with brush plating. The chipped area cannot be glass beaded, sandblasted or stripped and re-plated because they are assemblies at this stage. I have been successful at plating repair with the following procedure and passing a salt bath test using brush plating but not consistently.
My process: Inspect chip under microscope. Sand chip with 280 grit sandpaper as to smooth the chip into existing EN plating. Use scotchbrite
⇦ on
eBay or
Amazon [affil link]
also to blend chip. Activate, (not de-plate), chipped area with brush plating using a solution consisting of water, sodium chloride, and hydrochloric acid. Activate repair area for 10 seconds. Following activation, immediately nickel plate repair, (brush plate), area with solution of water, nickel sulphate, citric acid
⇦ on
eBay
or
Amazon [affil link] and formic acid for about 2 minutes. Activation and plating voltage set to 5.5 volts. Following nickel brush plating, rinse with water.
Can anyone elaborate on this? Is there a better solution that will fit my requirements? Remember I cannot sandblast, glass bead or strip and re-plate. I think brush plating is the only option.
Thank you very much.
Manufacturing Engineering - Wallingford, Connecticut, USA
2004
Gary,
Brush plating repair is a excellent method to use, but remember all activation steps mus be done with cathodic current. Use also a Scotch Brite on the electrode. I like to use sulfuric acid as a pretreatment step so you can see some gassing, rinse and than follow by a nickel strike.
Good Luck,
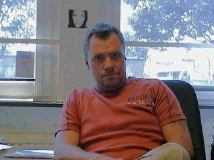
Anders Sundman
4th Generation Surface Engineering
Consultant - Arvika,
Sweden
2004
The chipped area and EN itself is very difficult to activate during reverse plating. It tends to develop a black smut and is very difficult to re-plate with brush plating. Are there any other alternatives to surface activaton? I have been activating in plating mode or anodic current.
Gary Petrillo- Wallingford
2004
Gary,
I have described an activation method for EN in letter 17724. Yes you are right about reverse current will develop black smut.
Regards,
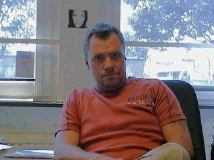
Anders Sundman
4th Generation Surface Engineering
Consultant - Arvika,
Sweden
2004
Hello Gary,
You are correct to blend the chipped EN, this will avoid a step or void in the plated surface. The next step is to prepare both metals in the repair area for plating. This may involve using an etching step followed by an desmutting step to remove any black smut that may form on the etched surface. After desmutting, an activation step, using forward polarity is performed to insure the nickel is active and ready to accept a plating deposit.
Following this you should use a solution that has been formulated by a experienced brush plating company. Many years of testing and experience result in plating solutions that have the ability to peform the task you require. With the correct surface preparation along with the correct nickel plating solution, a repair process like yours should be fairly routine. After all, repairing parts such as yours is a big part of our industry.
Good luck,
- Valencia, California
2004
Q, A, or Comment on THIS thread -or- Start a NEW Thread