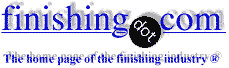
-----
Nickel on nickel plating problem with sulphamate strike
Q. Poor Adhesion of Electroless nickel on Sulfamate Nickel
I have a part with relatively large surface area (10 SF) in a 30" x 18" x 3 " rectangular pattern.
The part is soldered copper which goes through the following cycle: Soak, HCl, EC, Pickle in phosphoric acid based proprietary solution, Cyanide copper strike, Sulfamate strike, High-phos EN.
I am having terrible adhesion difficulties between the sulfamate layer and the EN layer. Through a ton of work and elimination of variables I am fairly confident that the issue is occurring in the sulfamate tank. For instance, when I run the parts through another sulfamate tank, they have perfect adhesion after EN. Further, the adhesion trouble seems to be confined to, or at least degrees of magnitude worse in the high current density regions of the bath.
Hull Cell
⇦ huh?
looks good. Main chemistry of tank is within parameters. Deposit on parts has good cosmetic appearance. Adhesion is awful.
Anyone have any ideas or experienced anything like this?
- St. Louis, Missouri
May 12, 2021
⇩ Related postings, oldest first ⇩
2004
Q. I am trying to set up a nickel sulphamate strike to continue plating on a nickel part after it has had some machining done to it. I am using the Barrett nickel sulphamate recipe found in the Barrett documentation and continuing the plating in a Barrett nickel sulphamate bath. The strike seems to plate well but doesn't stick to the nickel. I must use copper tape to fixture the piece and the strike works very well on the copper. I have tried to scotchbrite the surface and acid etch to gain adhesion to no avail. All of the operating parameters are within the recommended spec. which would be 42% nickel, 1.2% HCl, 4 oz/gal boric acid, SNAC 2.7 oz/gal and DI water bal. Any ideas on improving the adhesion? Thanks for the help.
Mark Joelfabricator - Duluth, Georgia, USA
A. Unless you are proceeding under the guidance of a highly experienced plating consultant, Mr. Joel, I would not recommend trying to formulate your own solutions based on old literature. Tremendous strides have been made, and the usual way to proceed is to simply buy a modern proprietary process from a plating process supplier.
I don't have in front of me the documentation you are referring to, but the formulation you printed doesn't sound to me like an activating strike suitable for getting good adhesion on old nickel. If you want to go with home-brew, I'd suggest a Wood's nickel strike instead, but there are proprietary sulphamate nickel strikes that should work. Good luck!
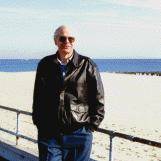
Ted Mooney, P.E.
Striving to live Aloha
(Ted can offer longterm or instant help)
finishing.com - Pine Beach, New Jersey
2004
![]() |
2004 A. From one Georgia boy to another, The Barrett Sulfamate Strike is not strong enough to activate old nickel plate. Furthermore, at the low pH the SN radical converts to ammonium ion and sulphate very quickly. To plate onto old nickel, first remove the organic soil, then remove the tenacious old nickel oxide with 50% HCl, then strike in 2 pounds per gallon nickel chloride and one quart per gallon HCl. Use Rolled Depolarized anodes because they are inefficient like you want in a "strike". Then with a very quick rinse, do not stop to look, go straight into the Plating sulfamate plating tank (and here you may use efficient "S-Rounds). ![]() Robert H Probert Robert H Probert Technical Services ![]() Garner, North Carolina ![]() A. Oxidized nickel is very hard to plate ! There is a lot of literature on cleaning and activation, but none of them work very well in comparison to stainless. The sulfamate strike is functional for something that does not require a lot of activation , plates at a much higher pH, with a lot less internal stress, so you can put on a thicker strike in a lot less time. You very probably will have bouts with adhesion if you do not use a high acid-low nickel formulation of Woods Nickel Strike. The simplest way to get a good activation of nickel is to clean it and then etch in a nitric-hydrofluoric acid mixture. The formulation will require some experimentation to have one that works in a reasonable time without being too fast or removing too much stock. Temperature makes a world of difference on a critical formulation. James Watts- Navarre, Florida 2004 |
A. Nickel on nickel adhesion problem properly electroclean, water rinse, acid dip, then woods strike i.e.,nickel chloride and hydro chloric acid,water rinse, then plating, then good luck.
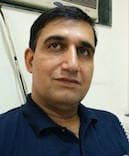
Ajay Raina
Ludhiana, Punjab, India
2004
A. Ted is right. I too am not acquainted with the Barrett process, but the formulation you give looks very benign to say the least. To reactivate nickel you need a very good cleaning system followed by a good etch. Use a Woods nickel strike to put fresh nickel down, although you can use an etch based on sulfamic acid ⇦ on eBay or Amazon [affil link] . I would personally suggest you contact a good plating supply house to sell you the required process, as formulating your own systems without a great deal of experience in the subject will only cause you more problems.
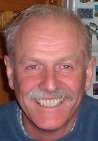
Trevor Crichton
R&D practical scientist
Chesham, Bucks, UK
2004
Q. I'm a mechanical engineer, not a finishing expert by any means. The nickel plating on nickel battery contacts seems to be separating - it makes a crinkling sound when pressed. Another thread on nickel-over-nickel problems suggests additives to the first layer may make it inactive. I'm hoping you could review the material and finish notes, point out and potential problems, and recommend a better way to state it or an alternative, proprietary process.
Thanks for your help,
Rob Campbell
Material: Nickel 200 (commercially pure (99.6%) wrought nickel)
Finish: Electroless nickel per MIL-C-26074, class 1, grade b (500 u-in) over Woods nickel undercoat
- Manchester, New Hampshire, USA
July 30, 2010
Q. A little more information: The part is a battery contact. The base part is .01" thick.
The part is lollipop-shaped, with a tang .75" long and .1" wide. If I bend this tang just 15-degrees, I feel and hear the plating snap and separate. It is that fragile.
Thanks,
Rob
- Manchester, New Hampshire USA
August 4, 2010
A. Old Ni is hard to activate. One trick that usually works is to make the part anodic for 1 minute and then reverse the leads and use the nickel strike as normal. This works for both the woods nickel strike and a sulfamate nickel strike.
Of course normal cleaning and pickling should be done first
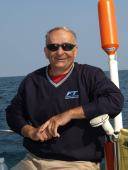
Pat Mentone
St Paul, Minnesota
August 9, 2010
A. Apparently the sulfamate strike is not strong enough to activate your old machined and heated nickel plate. Switch to a Woods Strike. Also be sure to dummy and carbon treat all incoming sulfamate concentrates as they are not purified like they used to be.
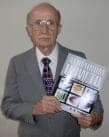
Robert H Probert
Robert H Probert Technical Services

Garner, North Carolina
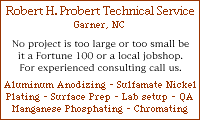
August 10, 2010
Q, A, or Comment on THIS thread -or- Start a NEW Thread