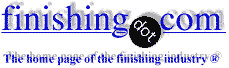
-----
Zinc plating thickness vs. salt spray resistance

Q. Hello guys, this is Charlie from China, I'm a project manager at a machining shop here. Recently we got an enquiry zinc plated parts to pass 720-hr salt spray test, is it even possible to achieve?
Charlie Wangproject manager - Guangdong
September 13, 2023
A. Hi Charlie. Few things are completely impossible, but if something needs 720-hour salt spray why specify zinc plating? Please ask the inquirer if zinc-nickel plating (or some other zinc alloy) is acceptable, and get back to us.
Luck & Regards,
Ted Mooney, P.E. RET
Striving to live Aloha
(Ted can offer longterm or instant help)
finishing.com - Pine Beach, New Jersey
A. Hi Charlie,
It's possible but very hard to obtain. We make some specialty bolts for VW with 600 hrs of NSS, but they have 15 microns of zinc, a thick trivalent iridescent chromate and a sealer plus a fixed friction coefficient lubricant. More than that resistance, as Ted mentioned, I would look for organometallic coatings or zinc-alloy plating.
Hope this helps!
- Cañuelas, Buenos Aires, Argentina
October 26, 2023
⇦ Tip: Readers want to learn from your situation;
so some readers skip abstract questions.
Q. 720 hours SST Zinc plating.
How many microns Zinc plating?
Business - Jamnagar (India)
March 10, 2024
Tip: This forum was created to help build camaraderie through sharing tips, opinions, pics & personalities.
The operator & those readers who want that might not engage with anonymous posters.
⇩ Related postings, oldest first ⇩
Q. I work for a leading auto component manufacturer.
In one of the components, my customer wants a minimum of 120 hours of salt spray before appearance of red rust.
My designer has specified 13 microns thick zinc plating with blue chromate passivation. Will this plating specification meet the customer's requirement of salt spray test.
automotive component - Bangalore, Karnataka, India
2004
on eBay or Amazon
or AbeBooks
(affil link)
A. This is an interesting question, Mr. Chandrasekar, and we thank you for it.
I'll start by saying that 13 microns is the correct thickness to specify for "severe" exposure (as opposed to "mild", "moderate", or "very severe"). So, unless the application is for "very severe" exposure, you did good.
You cannot specify hexavalent chromates for future auto application, and probably not even for current projects, so you are limited to trivalent chromates, which are blue anyway (chromate means Cr04--, so strictly speaking "trivalent chromating" is an oxymoron, but people accept the term).
Because trivalent coatings do not offer the protection of hexavalent chromates, it is quite widely accepted today to apply a silicate, zirconium, wax, water soluble lacquer, or other topcoat/post dip after the chromate. This is the point at which your spec is probably incomplete, because you need something on top of that trivalent chromium but you haven't specified what.
Zinc plating with a trivalent chromate and a high quality proprietary topcoat/final dip should last 120 hours if properly applied. Salt spray testing is not really a prediction of field life, but a QA measure to be applied by the plating shop to make sure things didn't go sour in their process.
A final thought is that zinc alloys like zinc-iron, zinc-nickel, and tin-zinc are more corrosion resistant than plain zinc and may be appropriate for the part in question. Automotive designers seem to specify 8 microns of zinc alloy far more often than 13 microns of zinc.
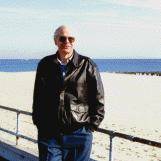
Ted Mooney, P.E.
Striving to live Aloha
(Ted can offer longterm or instant help)
finishing.com - Pine Beach, New Jersey
A. Mr Chandershekar,
It is entirely possible to achieve 120 Hours to white rust with 13 microns of zinc , which is passivated with a yellow or greenish blue film . Current environmental needs dictate the absence of Hexavalent chromium. The yellow is banned. A blue chromate dyed yellow will take care of the needs for a yellow finish.
A better alternative is the greenish film which is trivalent chromate and has excellent SST performance to white rust and subsequent red rust.
However, as Ted Mooney has pointed out a Zinc Iron alloy is the better route to achieving consistently high SST hours to red rust. Cost will remain affordable with Zinc Iron plating which is a simple Alkaline bath . Let me know what you decide.
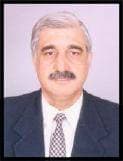
Asif Nurie [deceased] [deceased]
- New Delhi, India
With deep sadness we acknowledge the passing of Asif on Jan 24, 2016
Q. Hello,
What is the color that is most acceptable for trivalent thick passivation and that which will give the best corrosion resistance (at least 96 hours to white corrosion)?
This question arises since different company standards give different colors like Silvery color with yellowish iridescence, Silvery with greenish pink, etc. Some standards accept any iridescent color. Anyone to clarify on this?
Thanks
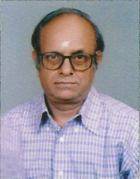
Subramanian Ramajayam
consultant - Bangalore, India
2007
A. These days I think you really must exclusively plan on trivalent chromating for the future, Ramajayam. All of the new high performance baths are proprietary, unfortunately. The thick-film baths proprietary baths produce a yellowish color, the thin-film baths a bluish color as far as I know. But since they are proprietary, I can't promise that.
It isn't clear what your position or your company's position is, or where you fit into the chain. Good luck.
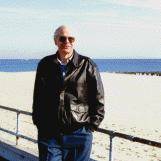
Ted Mooney, P.E.
Striving to live Aloha
(Ted can offer longterm or instant help)
finishing.com - Pine Beach, New Jersey
Q. How much plating thickness is required for Zinc Trivalent plating to withstand 150 hrs of salt spray testing.
Atul Pardeshibuyer - Pune, Maharashtra, India
January 23, 2008
A. Hi, Atul.
Actually the thickness of the zinc plating can be irrelevant because, although the zinc plating prevents red rust, it is the chromate conversion coating and any subsequent top coats that prevents the initial white rust. Talk to your trivalent chromate conversion coating supplier about whether their coating will withstand 150 hours.
There was a famous saying in Vaudeville comedy: "Don't tinker with a good line", which meant that if something is working, don't try to tweak it! The point of salt spray testing is to insure consistency, so there is no value in tweaking the number of salt spray hours up or down a little because the point is consistency & predictability, and tweaking will lead to playing around with process control factors instead of holding them consistent, achieving the opposite of your goal. If you can't get 150 hours, then stick with 96 hours -- don't fool around trying for an intermediate value.
Good luck.
Regards,
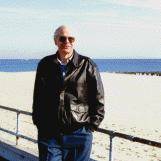
Ted Mooney, P.E.
Striving to live Aloha
(Ted can offer longterm or instant help)
finishing.com - Pine Beach, New Jersey
Q. Hello sir,
How much salt spray test hours for zinc blue plating material [min]? Any standard available?
- Bangalore Karnataka, India
June 23, 2014
A. Hi shanmuka. Before the days of RoHS-compatible trivalent chromating, the standard hours to white rust for the ubiquitous iridescent hexavalent yellow chromate was 96 hours to white rust. If you have no other standard to go by, that's what I'd suggest.
Specifications are available from many organizations; ASTM B633, "Standard Specification for Electrodeposited Coatings of Zinc on Iron and Steel" is active and well-maintained, and if you are not plating automotive parts with their own specs, it is probably a very good choice. You may also want to obtain ASTM B201-80, "Standard Practice for Testing Chromate Coatings on Zinc and Cadmium Surfaces". Good luck.
Regards,
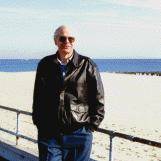
Ted Mooney, P.E.
Striving to live Aloha
(Ted can offer longterm or instant help)
finishing.com - Pine Beach, New Jersey
A. ASTM B695 gives, for mechanical plating and mechanical galvanizing, the salt spray hours as a function of thickness. (See Table 1.) The salt spray hours for electroplated zinc are approximately equal.
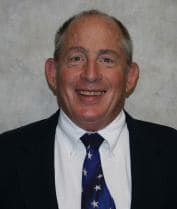
Tom Rochester
CTO - Jackson, Michigan, USA
Plating Systems & Technologies, Inc.

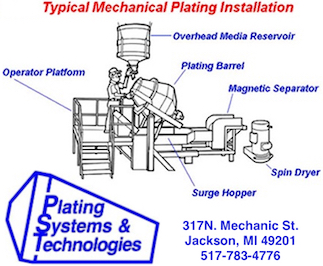
A. The chromating is responsible to stop the white rust. The zinc thickness has no effect on the white rust.
The red rust is a function of the zinc layer thickness. The thicker the layer, the higher is the protection against the red rust
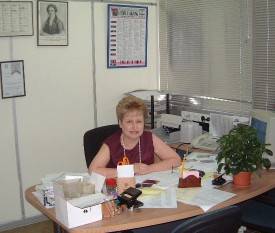

Sara Michaeli
Tel-Aviv-Yafo, Israel
Q. Dear,
How many microns is required for 96 hours salt spray test.
Thanks
trading - Riyadh ksa
November 24, 2014
A. Hi Rizwan. Even 5 microns of zinc (ASTM B633 "Mild" service condition) will deliver 96 hours to white rust if the chromate conversion coating is done well. But selecting the zinc plating thickness based on salt spray hours may be wrong thinking. You should probably determine whether the service condition is "mild", "moderate", "severe", or "very severe", and base the zinc plating thickness on that. Good luck.
Regards,
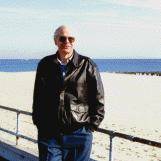
Ted Mooney, P.E.
Striving to live Aloha
(Ted can offer longterm or instant help)
finishing.com - Pine Beach, New Jersey
Q. How to calculate salt spray test vs. life in plating?
Suppose salt spray life is 48 hours to white rust and 96 hours to red rust, then --
What is life in outer atmosphere and how to calculate?
Eletroplating - Rohtak Haryana India
November 29, 2014
A. Hi Alakh. That question has been asked and answered here a dozen times, and elsewhere a thousand times, but the answer remains: there is no reliable relationship. Salt spray tests are not intended to predict real life except in this indirect sense: if the salt spray life declines, something went wrong with the processing, so the real-world life is also likely to not meet previous expectations either.
In real life, zinc coated objects can slowly build a corrosion-resistant, glassy, zinc carbonate skin from a slow reaction with the tiny amount of carbon dioxide in the atmosphere. This doesn't happen in a salt spray test, so designing for salt spray hours is not the way to improve real life. Once you have a process that delivers a satisfactory real-world life, you check the salt spray hours periodically to make sure nothing has fallen apart in the processing.
48 hours to white rust is not enough, and indicates that the processing is not up to today's standards. 96 hours to white rust should be the minimum for any modern chromate, and some are significantly better; 150 hours is not unusual. For typical outdoor exposure (severe) you should probably have 13 microns of zinc plating or 8 microns of a zinc alloy.. Good luck.
Regards,
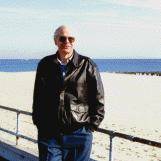
Ted Mooney, P.E.
Striving to live Aloha
(Ted can offer longterm or instant help)
finishing.com - Pine Beach, New Jersey
Q. Sir,
I need a plating on a low carbon steel, where the weather is extremely salty.
What plating do you suggest? My client needs surface to be look like silver aesthetically.
pattern & engg. Works - Mumbai, Maharashtra, India
January 24, 2015
A. Hi. A zinc alloy plating like zinc-nickel or zinc-cobalt should be good. Tin-zinc is more expensive, but probably looks a bit more like silver. Good luck.
Regards,
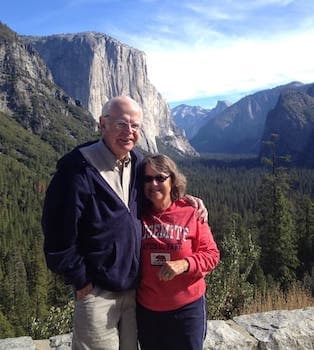
Ted Mooney, P.E. RET
Striving to live Aloha
(Ted can offer longterm or instant help)
finishing.com - Pine Beach, New Jersey
Q. Time until white corrosion appears 1.5 weeks and time until base metal corrosion appears 4 weeks. It can be possible for trivalent yellow passivation in electroplating? If it's possible please tell us the required plating thickness.
Gopi RAJA- TAMILNADU, India
February 14, 2015
? Hi Gopi. If a question isn't well understood, the answers will be ambiguous or misleading ... so, apologies but I don't quite understand the question :-)
Are you saying that you want 252 hours (1.5 weeks x 7 days x 24 hours) of resistance to white rust in ASTM B117 salt spray testing? And you want 672 hours of resistance to red rust? That's a very tall order.
Regards,
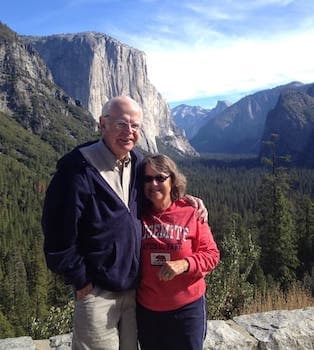
Ted Mooney, P.E. RET
Striving to live Aloha
(Ted can offer longterm or instant help)
finishing.com - Pine Beach, New Jersey
Q. I am working with Earth equipment company.
Continuously we are facing an issue of SST failure, During the analysis part will be verified by different labs and both the labs showing testing parameters are the same but results are different.
Need support in details for verifying testing parameters and anything.
- Pune, panjab, India
July 15, 2015
A. Hi Sameer.
1. How do the parts perform in the real world? That's what is critical.
2. Have both labs provided certification of exactly what spec they are testing to, and it is the same? What spec is it?
3. Some variation is to be expected, but your posting is rather vague. Please give us some numbers like: what is the plating spec, what is the substrate, how many hours are you expected to get, how many hours does lab #1 say, and how many hours does lab #2 say?
Thanks & Regards,
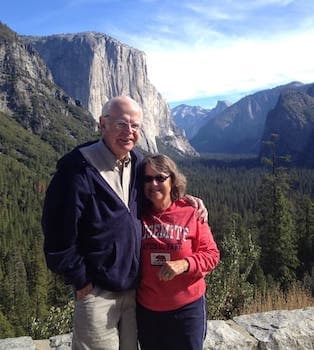
Ted Mooney, P.E. RET
Striving to live Aloha
(Ted can offer longterm or instant help)
finishing.com - Pine Beach, New Jersey
Q. Dear sir,
We have Zn plated screws with black trivalent passivation; but it quickly formed white rust in our product; part tightening with screw driver; it failed SST within 60 hours for white rust as against the spec of 96 hours; kindly give suggestion on this issue.
- Bangalore,Karnataka, India
September 27, 2015
Q. Is there any relation between ED thickness and salt spray time? I mean the more thickness the longer salt spray time?
For passing 1000 hours salt spray without red rust what is your suggestion for the thickness of ED process?
- Esfahan, Iran
October 27, 2015
A. Hi Hadi. I assume you're still talking about zinc plating and "ED" means the thickness of the electrodeposit? (To some people, 'ED' means electrodeposition paint).
Yes, the corrosion resistance to red rust is proportional to the thickness of the zinc plating (although it's also dependent on the effectiveness of the chromate conversion coating). However, it is most common to run the salt spray test only to the appearance of white rust (failure of the chromate conversion coating), and to base the zinc thickness on the severity of the exposure (13 µm for severe exposure, 25 µm for very severe exposure) rather than salt spray hours. Besides the general non-indicativeness of salt spray testing, it is particularly non-indicative for heavy zinc coatings because in the real world they gain much of their corrosion resistance from the slow build-up of inert and impermeable zinc carbonate reaction products which cannot form in a salt spray test.
It may be a better idea to employ 8 µm or 13 µm alloy plating like zinc-nickel or zinc-iron rather than 25 µm of plain zinc if 1000 salt-spray hours is to be the judging criteria. Good luck.
Regards,
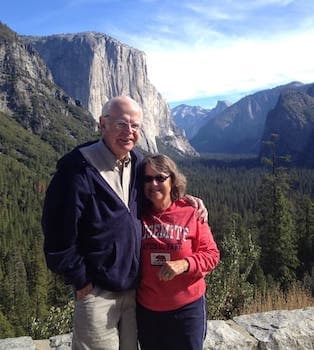
Ted Mooney, P.E. RET
Striving to live Aloha
(Ted can offer longterm or instant help)
finishing.com - Pine Beach, New Jersey
Will 8 µm Zinc Plate pass 96 hour salt spray?
Q. Will 8 microns of zinc plating, with a clear trivalent chromate, pass a 96 hour salt spray?
Salt spray requirement is no red corrosion of steel base metal.
Salt spray test is 5% neutral salt spray per ASTM B117.
- Lakehurst, New Jersey
December 29, 2015
A. Hi Rade. Yes.
Regards,
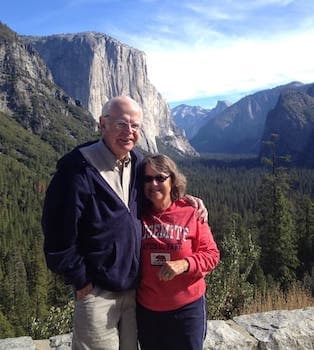
Ted Mooney, P.E. RET
Striving to live Aloha
(Ted can offer longterm or instant help)
finishing.com - Pine Beach, New Jersey
Q. What would be the plate thickness required for zinc plating with clear passivation of ISO 2081, grade B block to achieve a salt spray life of 120 hrs. white rust?
Amit Satardekar- Mumbai, Maharashtra, India
January 27, 2016
A. Any thickness of zinc plating, even the minimum 5 µm will survive 120 hours if: the substrate was properly mechanically prepared; and it was properly cleaned and activated; and it was properly zinc plated; and it was properly trivalent chromated with a proprietary chromate and the topcoat recommended by the supplier; and the shape of the component is such that it can get proper plating coverage .... and the process is under control. Good luck.
Regards,
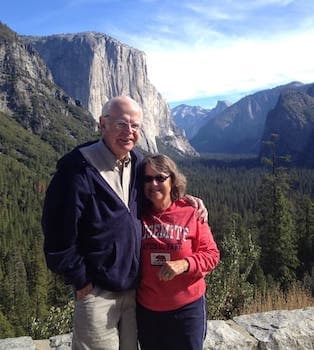
Ted Mooney, P.E. RET
Striving to live Aloha
(Ted can offer longterm or instant help)
finishing.com - Pine Beach, New Jersey
Q. Hi,
I wanted to confirm the steps for salt spray test. My customer has randomly picked up a bolt from a lot that we had supplied and sent for salt spray test. There might be chances of problems in material handling which might lead to the bolt not passing the salt spray test. Do we have to give an altogether different part taken from the plater and submit the same to the customer for salt spray test purpose?
fasteners - Pune, Maharashtra, India
June 27, 2016
on eBay or Amazon
or AbeBooks
(affil link)
A. Hi Shrikant. You should be plating to some particular specification, and that specification will usually dictate the procedures for sample size and sample selection. Good luck and get back to us with the spec if you wish.
Although some plating shops feel that it's easier to not have to abide by any particular specification, if you are not plating to a specification you are constantly exposed to a complicated contract dispute because there are no actual grounds by which to claim whether the plating is satisfactory or not.
Regards,
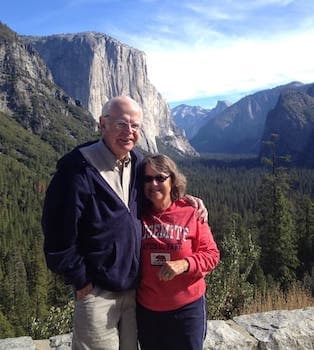
Ted Mooney, P.E. RET
Striving to live Aloha
(Ted can offer longterm or instant help)
finishing.com - Pine Beach, New Jersey
Q. Our company did Zinc Plating on CRCA Test panels and performed Salt spray Test of on it.
Technical Details :
1) We did Zinc Plating on panels as per ISO 2081-Fe/Zn12/A.
2) SST specification : Neutral salt spray corrosion resistance of zinc plus chromate conversion coatings before basis metal corrosion (red rust) begins shall be equal to or more than 120 Hours.
After Testing we get the test results and we observed black spots, black staining and white rust on both sides of 1 test panel out of 3. Remaining 2 test panels found OK.
So by observing above whether plating panels passed or failed in SST?
3) Also report does not have any conclusions like panels are passed or failed in SST. For same point, we made contact to our Salt Spray Testing Lab, they want "Criteria" to pass or fail the test.
We already told lab that please proceed as per ASTM B117, ISO 2081, ISO 10289 Clause 6.1 & 6.2 ...
So is this sufficient for conducting SST and giving conclusion?
Please give answer.
Design & Development Engineer - Kolhapur, Maharashtra, India
November 24, 2016
A. Hi RutuRaj. ASTM B117 is a specification for how to run a salt spray test and what features are required of the test cabinet. It will not tell you what constitutes passing and failing.
Sorry that I don't have a copy of ISO 2081 at hand, but it may tell you what constitutes passing and failing, what lot/sample sizes to use, etc. Usually, black spots or discoloration are not considered failure, but white rust usually is -- but it depends on the spec.
Regards,
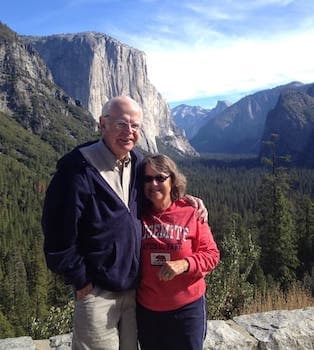
Ted Mooney, P.E. RET
Striving to live Aloha
(Ted can offer longterm or instant help)
finishing.com - Pine Beach, New Jersey
How do I properly specify zinc clear, yellow, or black chromate for 96 hrs ss protection on steel alloys?
Q. 1) I believe the following will get what I need for the yellow or black chromate, but is this the proper formatting?
ZINC PLATE YELLOW (or black) AND BAKE, RoHS, Fe/Zn13, TYPE VI, SC3, PER ASTM B633 (NO HEXAVALENT CHROMIUM), 96 HOUR SALT SPRAY MINIMUM.
2) Clear is Type V, but according to Table 2 in B633 that only provides 72 hrs. But how come Table 2 can identify the level of protection when a specified service condition is not taken into account? Will the specification of SC3 give me that or can I specify SC4 give 96 hours protection?
3) Would I use the same specification for ductile iron? If I need to specify the particular zinc and aluminum alloys to be able to answer this question, I can provide that.
4) Are the colors actually a sealer or just a dye?
5) In what cases would want to specify a chromate conversion or is that the same?
product engineer - Portland, Oregon, USA
January 4, 2017
A. Hi Scott.
1. That sounds okay to me.
2. Service condition and thickness of plating are related: SC3 (severe) requires 13 microns of plating as you imply. But the salt spray hours you mention are before white rust, and that is a function of the chromate conversion coating, not the thickness of the zinc plating.
3. You could probably use the same spec for ductile iron substrates, but the spec reads "... on iron and steel", so you can't use it for aluminum or zinc substrates.
4. Where the colors come from is an interesting question, the answer to which varies as the years go by. Hexavalent chromium is yellowish, so until a decade ago or so, yellow was just the color that chromate conversion coatings were. Most 'thin film' trivalent chromates are clear, so dye is sometimes used where yellow is required. Most thin film chromates use a 'sealer' after them. My understanding is that the 'thick film' trivalent chromates are yellow and don't use a subsequent 'sealer'. But trivalent chromating is so heavily proprietary that it's hard to offer clear cut answers.
5. The chromate conversion coating is the source of the coloration, and zinc plating is invariably chromate conversion coated.
Regards,
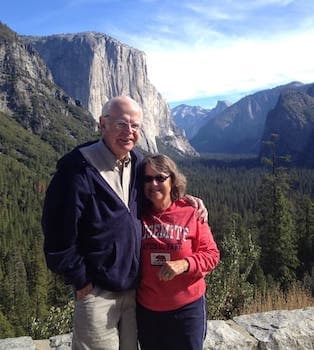
Ted Mooney, P.E. RET
Striving to live Aloha
(Ted can offer longterm or instant help)
finishing.com - Pine Beach, New Jersey
(you are on the 1st page) Next page >
Q, A, or Comment on THIS thread -or- Start a NEW Thread