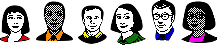
Metal finishing Q&As since 1989
-----
Converting zinc plating bath to zinc-nickel
March 28, 2021
Q. Dear all ,
My question is , is it posible to convert the present acid zinc plating bath into acid zinc nickel bath by adding required amount of nickel in the bath .
My zinc bath composition:
Zinc metal : 33 - 38 g /l
Chloride : 165 - 185 g /l
Boric acid : 38 - 43 g /l
PH : 4 - 5.3
Can anyone help me to modify my bath into acid zinc nickel bath please.
- Chennai India
March 2021
"Electrodeposition of alloys: principles & Practice"
by Abner Brenner
on
AbeBooks
or
eBay
or
Amazon
(affil links)
A. Hi Ganesan. If you are using a process from a supplier you, should probably ask that supplier for advice and the necessary steps. If you are using your own-in-house bath formulation, John Tennison-Woods says below that it's possible and not complicated; and on thread 28851 Goran Budija offers a formula for acid zinc-nickel so you can see what you would need to add to get there. You can also consult Brenner's Electrodeposition of Alloys for other formulations -->
Still, it is one thing to plate a single part in the lab via textbook info and trial-&-error, but quite another thing to operate a robust production-ready zinc-nickel plating bath without help and the proprietary knowledge of a supplier -- but you are certainly welcome to try.
Luck & Regards,
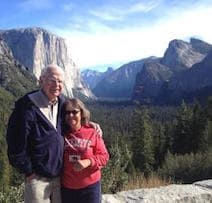
Ted Mooney, P.E. RET
Striving to live Aloha
finishing.com - Pine Beach, New Jersey
⇩ Closely related postings, oldest first ⇩
Q. European motor manufacturers are insisting that many vehicle components be zinc nickel plated and not acid or cyanide zinc plated. Can anyone please advise on an easy and cheap way of converting an existing acid zinc plant, both barrel and rack plating, to a zinc-nickel plant without having to dump and start over again. Is there a way of converting the solution over a period of time. Apparently there are 2 ways of doing zinc nickel plating. Which way in the best? We are in need of detailed technical assistance.
John Mattissonplating - South Africa
1999
A. `Dear Mr Mattison ,
Yes indeed there are two forms of Zinc - Nickel plating , one acid the other alkaline , and yes conventional acid Zinc can be converted to Acid Zinc - Nickel . the procedure is relatively simple , and control of the Nickel level is relatively simple . Have you not spoken to your local "Suppliers" about this? Best regards

John Tenison - Woods
- Victoria Australia
1999
1999
A. Dear Mr. Mattison:
I have not been to happy with any of the acidic zinc/nickel formulations that I have encountered, except for reel to reel strip line plating. The constant current density takes advantage of the fact that you will see higher nickel in the low current areas of complicated parts.
The alkaline baths on the market are not convertible from other processes. Cyanide Zinc can NEVER be used, as it forms Nickel Tetracyanide complex. As little as 30 PPM will totally destroy a bath.
There are several vendors selling zinc/nickel technology today. Be sure that the European firm tells you whether they want a low percentage or a high percentage for nickel co-deposition. The low plates at 5 - 9% Nickel; the High at 10 - 15% Nickel. In Europe, some automakers specify a bake at 120 deg.C. for 24 hours to the passivated zinc/Nickel prior to entry into Salt Spray testing. Then they want 240 hrs to white corrosion. A difficult feat for the low percentage.
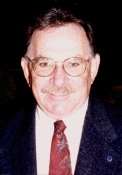

Ed Budman [dec]
- Pennsylvania
With deep sadness we advise that our good friend Ed passed away Nov. 24, 2018
Q, A, or Comment on THIS thread -or- Start a NEW Thread