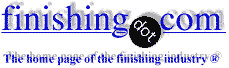
-----
How to Mask for Hardcoat Anodize
finishing.com is possible thanks to our supporting advertisers, including:
Quickstart:
Some readers may want a quick Intro to Aluminum Anodizing to understand what chromic acid anodizing and hardcoat anodizing are about.
It's difficult to reliably mask for selective hardcoat anodizing; one technique is to chromic acid anodize first then machine away the chromic acid anodizing in the desired areas. Read on ...
Q. Hello Guys,
I'm a chemical engineer and recently working on aerospace parts which requires both Type III Hard Anodizing and Type I CAA, that some area requires Type III and other area requires Type I.
We have problem on arranging these 2 anodize processes, like which would be the first while facing some masking issue.
But by chance I heard that this could be achieved by first anodizing with Type I on the whole surface of part, then mechanically remove the area to be anodized for Type III, finally direct anodize the part for Type III, without any masking on the anodized type I coating.
Do you guys have any experience on this method and I'm also concerned about does the further hard anodizing with sulfuric acid have any bad effect on the type I CAA coating?
looking forward for your reply and have a good day!
- Shreveport, Louisiana
January 11, 2022
adv.
Yuri, I believe that we can help you with this problem. Please give us a call at 888-218-7227. www.maskcoat.com
Jeremy
Mask Coat LLC

West Monroe, Louisiana
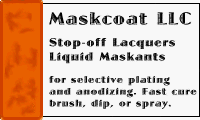
Q. Castings undergo rough machining-FPI-Chromic Anodizing- Machining-Masking + Hard Anodizing.
White patches are observed after Hard Anodizing
• Machining parameters and quality of coolant and water has been checked and found OK
• Masking found adequate and there is no Seepage of HA
Would like to know what could be the reason?
- Bangalore, India
December 4, 2024
⇩ Related postings, oldest first ⇩
Quickstart:
Aluminum is often 'chromate conversion coated' as a corrosion resistant final finish or as a pretreatment for painting or powder coating. The process actually involves many steps, usually including alkaline cleaning, etching, deox/desmut, the chromate conversion step per se, and water rinses between each step.
MIL-C-5541 / MIL-DTL-5541 / MIL PRF-5541 is the most commonly cited spec. "Alodine" and "Iridite" are proprietary trade names from two suppliers of the process chemistry. "Chem film" is a slang term for the process often used in the USA.
Q. We have two stamped Aluminum parts(90 mm x 70 mm) that we are hard anodizing in a custom color. We need to make electrical contact in two areas. The contact pad size is 2 mm in dia. Is it possible to Alodine ⇨
then mask the contact areas and then hard anodize? What is this going to do to cost? Would it be easier/cheaper to Alodine the inside surface and hard anodize the exterior surface? Are there other was to have electrical contact on a hard anodized part with out the aluminum oxidizing?
- Sunnyvale, California, USA
2002
![]() |
Don't forget the principle of anodizing (chromic or Type II) as a maskant for hard coat. Anodize in Chromic, grind off where you want to hard coat, then grind off where the chromic was left on. ![]() Robert H Probert Robert H Probert Technical Services ![]() Garner, North Carolina ![]() A. There are Electroless Nickel Baths available that plate a deposit 60 RC+ hardness. Electroless Nickel is electrically conductive has the same hardness as hardcoat and much better lubricity and frictional properties. Electroless nickel is usually more expensive than hardcoat. If you are going to have to do two different coating process with anodise and Alodine then electroless nickel may be very cost competitive. Also if you are coloring the hardcoat it is not as hard as it could be. Todd Osmolski- Charlotte, North Carolina, USA A. Hi Don, Yes! "Alodining", masking and Hard anodizing is routinely performed. Conversion coating the substrate not only provides excellent adhesion of the masking but is also a good corrosion inhibitor. Bill Grayson- Santa Cruz, California, USA |
Multiple threads merged: please forgive chronology errors and repetition 🙂
Q. Help! :-)
My company manufactures aluminium prismatic components for the aerospace industry. We currently employ a brown wax mask in order to prepare parts for the hard anodizing process. However, the application and removal of the wax is time consuming and is thought to be causing acid attacks on the component during its removal.
Can anybody out there recommend an improved mask that may assist us?
Many thanks for your time.
- Wolverhampton, England
2002
A. Ian,
Check if your folks 'reuse' the wax by putting the wax from the de-wax tank back into the wax tank. If they do you may well of found your problem. We use wax and have no problems, but we never 'reuse' the wax and never put wax removed from cut back operations back in the wax tank.
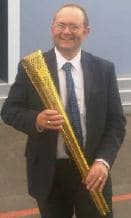
Martin Trigg-Hogarth
surface treatment shop - Stroud, Glos, England
A. Ian, apart from waxes there are organic resin "Stop-offs" available from most of the larger Metal Finishing Suppliers.
Good luck.
Melbourne, Victoria, Australia
Thanks for your help guys.
- England
A. Chromic Anodize or Type II conventional sulfuric acid anodize first, seal very well, grind off the areas to be hard coated, then hard coat anodize. The chromic acid anodizing will mask adequately. AES Proceedings 1958, Dr Harold Weisner then of Bendix Kansas City.
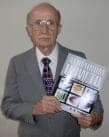
Robert H Probert
Robert H Probert Technical Services

Garner, North Carolina
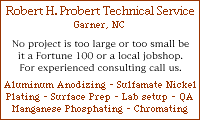
A. Have you tried to use a masking disc, such as aluminum or lead foil discs? They can be cut to shape and will hold up well in your process. There are various polyester and vinyl tapes that can also do the job, though the quality of the vinyl is important, and the cost of polyester can be prohibitive.
Ty Sarajian- Brookfield, Wisconsin
Q. I am a Sales Engineer working in the Anodizing Field. I am working with a customer who is doing Hard Coat Anodize. We are looking for a product to dip the parts in to mask & then cut away what area we need hard coat anodized. We tried one masking supplier, and too hard to remove masking (not an option). Does anyone have any suggestions how to mask a medium size part entirely & then cut out a small groove to be hard coated? Thanks for the input!
Cliff ShephardSales Engineer - Charlotte, North Carolina
2004
A. Basically, there is no dip process that will not have some anodize thru thin spots or pores and still be "easy to remove". Wax is an option, but not a good one. It would help if you could be a little more specific about the part. Medium sized means something to only you. Why not send a picture with a couple of dimensions?
Also, which product did they try. While that product may not have been satisfactory to your user, there are a number of similar products that also will not work. With no idea, how can anyone comment. I do not think that Ted will mind a brand name in this case as it will be more generic than specific. Especially since you have not said that it was bad, just that it did not fit a client's particular need. There might be other masking alternatives than a dip process.
- Navarre, Florida
A. Put down some tape where you want the anodize; mask the part; cut the mask along the sides of the tape; peel off tape. You may need a strong tape depending on the mask material. Either Kapton or glass-cloth tape are some that come to mind.
Tom Gallant- Long Beach, California
A. Cliff,
I don't know if this will be an option for you but it is something I know that works. First of all realize that there is no good masking for anodize of any type.
Begin by chromic acid anodizing the part all over and seal with nickel acetate. Use any convenient method, i.e., tape, wax, thermocote, paint, to mask off the areas not to be hardcoated. Remove the chromic acid anodize by etching and Hardcoat as normal.
If the chromic anodize in the hardcoat area is skim cut by machining then no other masking material would be needed. The sealed chromic anodize will act as the mask.
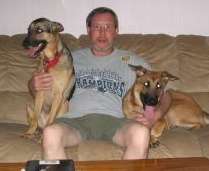
Tim Hamlett, CEF
- West Palm Beach, Florida, USA
A. Hello,
I am a tool designer for a company in the States that specializes in making precision molded products for selective surface treatment. Aviation in particular is our bread & butter. I just happened to stumble on this thread. I apologize for being vague or if this post is invasive but I just did not see any recommendations for custom hard tooling in the responses.
Regards,
- Avon Indiana
February 4, 2010
[editor appended this entry to this thread which already addresses it in lieu of spawning a duplicative thread]
Q. HOW CAN I PROTECT ALUMINUM FROM HARD ANODIZE(TYPE 3) USING CHROMIC ANODIZE(TYPE 1)?
PLATING SHOP EMPLOYEE - ISRAEL
December 8, 2010
[editor appended this entry to this thread which already addresses it in lieu of spawning a duplicative thread]
Q. I have a component that needs Type II (SAA) anodizing & Nickel acetate sealing for certain area and the remaining area must be Type III (hard) anodized.
I need masking material for both the processes and Process sequence (Which anodizing must be processed first?).
- INDIA
October 6, 2011
Treatment &
Finishing of
Aluminium and
Its Alloys"
by Wernick, Pinner
& Sheasby
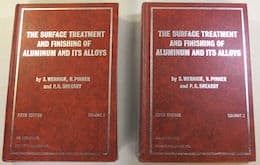
on eBay or Amazon
or AbeBooks
(affil link)
Q. Hi Guys
We currently use wax as a selective mask prior to hard anodise of 2000 series aluminium aircraft components, however this is a time consuming process as the parts are complex. We are looking at trying to use chromic anodising as a maskant prior to hard anodise instead. i.e. chromic anodise all over, skim the bore to bright metal, then hard anodise. Does anyone have any experience of this process?
Any advice would be much appreciated.
Thanks in advance.
Barry
Manufacturing engineer - Birmingham, UK
June 21, 2016
![]() |
Q. Wax for hard anodise process? Hi Barry can you recommend a supplier of the low temperature wax in the UK please. alan clayton- chester February 10, 2023 A. Hi Alan. If you checkmark the RFQ box on your posting your contact info will be available to suppliers and others for private commercial contact. |
A. Hi Barry. That approach is common, and we've appended your question to a thread which addresses it. It is also mentioned in thread 14483. Good luck
Regards,
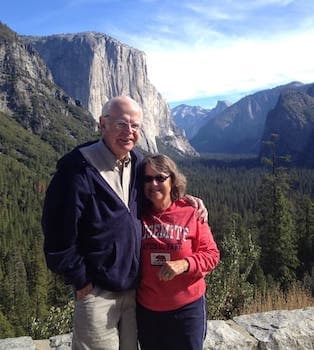
Ted Mooney, P.E. RET
Striving to live Aloha
(Ted can offer longterm or instant help)
finishing.com - Pine Beach, New Jersey
Q. Hi Ted
Thanks for your response. In one of your letter links Robert H. Probert outlines the process and references "AES Proceedings 1958, Dr Harold Weisner, then of Bendix Kansas City". Probably a long shot, but would you know how to find a copy of the relevant section of these proceedings?
Regards
Barry
Manufacturing Engineer - Birmingham, UK
June 23, 2016
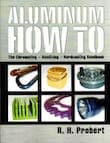
Aluminum How-To
"Chromating - Anodizing - Hardcoating"
by Robert Probert
Also available in Spanish
You'll love this book. Finishing.com has sold almost a thousand copies without a single return request :-)
A. Hi Barry. You could ask Robert; it wouldn't surprise me if he had a copy rather than just the memory of a 50+ year old paper. You could inquire of www.nasf.org, but I doubt they retain proceedings of that age. Worldcat.org can find stuff like this.
New Brunswick Plating [a finishing.com supporting advertiser] holds a Huge plating library, probably the world's biggest, and I am confident they have it, but they are in the plating business not the library business, so I probably tick them off by even mentioning it.
But maybe this free advertising of their technical expertise (the world's best diecast plater, for one) will compensate them for the hassle it may bring them :-)
Regards,
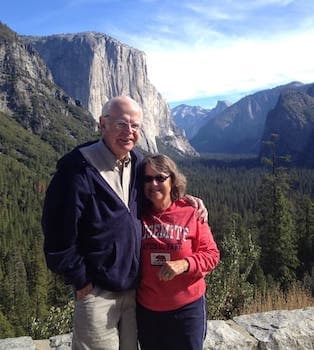
Ted Mooney, P.E. RET
Striving to live Aloha
(Ted can offer longterm or instant help)
finishing.com - Pine Beach, New Jersey
Q. Hi,
We trialed this method on test discs using chromic acid anodise as a mask. It was not a complete success. I suspect the hot DI water seal we used was the issue. We trialed each of 4 discs at 8, 15, 25 & 60 minutes seal respectively with varying levels of success. The first three all had small spots of hard anodise all over the chromic anodise with varying frequency. The last one had a very light film of it in patches. Question - could anyone advise if another type of hot seal i.e. nickel acetate would do better? Any advice would be much appreciated.
Barry
Manufacturing Engineer - Birmingham, England
A. Yes, Alcoa also said in 1956 Aluminite book, that hot water over 15 minutes deteriorates the coating, and I cannot persuade the Mil spec writers to change it. Boeing recognized this problem and came out with their dilute chromate seal. Alcoa also said in 1956 that the hot water does not deteriorate if a very small amount, they said how much, of chromic acid is added to the seal. Any way, it is still very difficult to get the coating sealed well enough to withstand the hard coat condition. If you will send your address, I will go to the copy store and copy several pages of Dr. Weisner's paper. He first presented the paper in an Atlanta AES conference in 1958, and again later at the national convention. And I had dinner with him that night. No better paper on hard coat has ever been published.
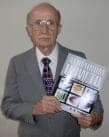
Robert H Probert
Robert H Probert Technical Services

Garner, North Carolina
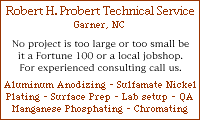
Hot glue for masking type III anodize
Q. Wondering if anybody has tried hot glue for type III anodize? If so, what were the results and what kind of glue was used?
Isaac KissingerMasker - Philadelphia, Pennsylvania
November 24, 2018

Q, A, or Comment on THIS thread -or- Start a NEW Thread