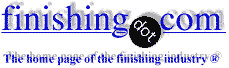
-----
What exactly is Solder Plate?
We have a request from a client in the electronics industries to provide a Solder Plate, apparently its an alloy of Tin and Lead. Can you give me some information. What exactly is Solder Plate? I have done some research and found two baths; Fluoborate bath and MSA
(Methane Sulfonic Acid. Which is better for our application? What about waste treatment, etc for the Lead. \
Our client doesn't do any soldering on the parts, they need this for good (low) contact resistance and I believe because they clamp the part to some cables, so they also need ductility. The part is a Brass clamp and requires a Copper underplate according to their spec's. They say we can't use bright Tin since it heats up above
250°C when in use. (the plated electronic component).
Thank you for all your help,
plating shop - MONTERREY, NUEVO LEON, MEXICO
2004
See question 29224.
Tom Gallant- Long Beach, California, USA
2004
2004
Sir;
Tin/Lead provides better solderability than bright tin. I recommend Kushner Electroplating School training on Tin-lead and bright tin so that you may have a better understanding of the two processes. A nickel strike under layer for tin-lead is generally better than copper. It provides better solderability.
Regards,
- McAllen, Texas
Thank you for your help, Tom and Joel, but our client doesn't do any soldering on the parts, they need this for good (low) contact resistance and I believe because they clamp the part to some cables, so they also need ductility. Please check my original inquiry. What do you recommend for this application? What about Lead Free Tin Plating?
Thank you again for your help.
plating shop - Monterrey, Mexico
2004
Hi,
You should really ask your client to review the Spec. Solder Plate is usually 63/37 Tin Lead alloy, for your info the eutectic or melting point is 182c far below the 250c requirement. He needs to specify the alloy required which will change the melting point. Hope this is helpful.
metal reclamation - Belleville, Ontario
2004
Q, A, or Comment on THIS thread -or- Start a NEW Thread