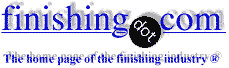
-----
Plating of Rare-earth Neodymium Magnets
Q. We're looking for a process to clean, activate and plate either copper or nickel on neodymium magnets such that the plating is adherent. We can get plating onto them but it peels with little effort. Any advice would be appreciated.
Milton Stevenson, CEF- Syracuse New York
February 12, 2021
A. Hi Milt. I went through the site and consolidated all the threads I could find on plating onto Neodymium. I don't have answers but there is a lot of food for thought here now. I'm guessing from reading here that vacuum impregnation is highly desirable; that a common sequence is Ni-Cu-Ni and that it's purpose is to better seal the porosity.
In another discussion (thread 0792) a reader reports that they've been commissioned to strip and replate because the electroless nickel is peeling. This page from a supplier asserts that the plating must be done before the magnet is charged, but I have no easy way of knowing if that is true or sales pap.
Luck & Regards,
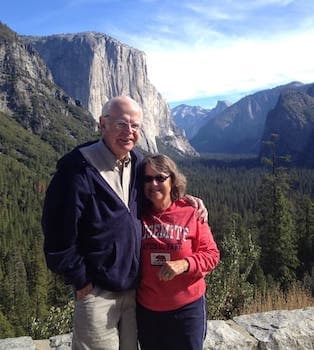
Ted Mooney, P.E. RET
Striving to live Aloha
(Ted can offer longterm or instant help)
finishing.com - Pine Beach, New Jersey
February 2021
⇩ Related postings, oldest first ⇩
1998
Q. Wanted: Electroplating Technology for Neodymium-Ferrite-Boron(Nd-Fe-B)
We are Ningbo Ningshing Corp.(Ningbo Import and Export Corp.), we are planning to set a new electroplate factory for Nd-Fe-B plating, our government also support it very much.
This is one kind of Magnets, and used for Hard-drives (called VCM use), CD-rom, Motors, speakers...
In China, the annual turnover of Neodymium magnet is more than 1000 Tons. But until now, most of the factories could not do coating well enough.
Our factory is using Nickel coating, as the Neodymium-Ferrite-Boron is sinterws like powder metallurgy, the molecule is different from the usual metal. Our products rejected several times by oversea customers due to the coating problem.
Some experts told me to try coating double deck, copper first, then Nickel. But I do not know how the techniques.
We hope somebody can sell us this field technology. Would anybody give me some suggestion and technical support?
Sun Yi-Chun- Ningbo, China
A. I don't know about the need for a copper undercoat, but I would think that even this would not properly seal the porosity in sintered metal objects. Have you considered vacuum impregnation?
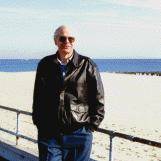
Ted Mooney, P.E.
Striving to live Aloha
(Ted can offer longterm or instant help)
finishing.com - Pine Beach, New Jersey
1998
A. We have investigated numerous coatings suitable for this application and have concluded that electrophoretic painting is the preferred option. We use a special pre-treatment route to achieve this.
Robert W Bayston- Cheltenham, Gloucesteshire, UK
1998
A. Our shop has successfully Loctite impregnated powdered metal parts for many years. The reasons for impregnation would include: Improved coatability, Sealability, Increased machinability, Added strength, Solvent resistantce, and Adhesion properties. We have a rather large customer that we impregnate Iron-Boron-Neodymium magnets for: solvent resistance is their main concern. The process calls for proper materials, cleanliness, proper vacuum/pressure/durations, proper cleaning process, and possibly a post cure.
Gene Muenchausen- Madison Hts., Michigan
1998
A. I agree with Gene. Impregnation will greatly improve the coatability of your parts. Good luck!
Joe Babcock- Ann Arbor, Michigan
2000
Multiple threads merged: please forgive chronology errors and repetition 🙂
Q. We presently have NdFeB magnets plated prior to placing them into a magnetic assembly. Is it possible to have the magnet assembly plated after it is assembled and magnetized? We are looking at using nickel plating followed by a hard chrome plating.
Marshall Carner- ERIE, Pennsylvania
1999
A. Hello Marshal,
I have Electroless Nickel plated magnetized assemblies without affecting the magnet in any way. I don't know if the DC current in Nickel & Hard Chrome will affect your magnet.
Is this for hard disc drive assy's?
regards
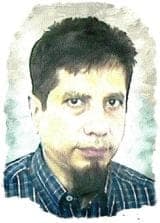
Khozem Vahaanwala
Saify Ind

Bengaluru, Karnataka, India
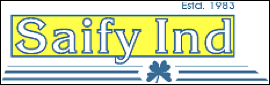
1999
Plating on Samarium Cobalt Magnets
Q. Plating on rare earth samarium Cobalt, SmCo, magnets. I am currently working on plating Samarium Cobalt, SmCo, rare earth magnets for aerospace applications. The magnets are not magnetized at this point. The plating specifications calls for .002-.0025" of high phosphorous electroless nickel over a woods nickel strike. The magnets are activated with 3% v/v of sulfuric acid for 2-3 minutes. I'm looking for any information concerning the plating of SmCo.
Dave Mahoney- Cheshire, Connecticut,USA
2000
A. That sounds fine, you could also try, if you have trouble with adhesion, anodic etch in the Wood's strike (use a separate tank and solution) anodic in the sulfuric 25% HF pickle anodic/cathodic in 30% sulfuric Best regards, Tom


Tom Pullizzi
Falls Township, Pennsylvania
2000
Cadmium Plating of Magnets
Q. We manufacture solenoids for a line of valves for the semiconductor industry. Currently, we are using a black oxide finish on all the magnetic parts. This finish tends to corrode easily in the harsh environments these valves see. Could we use, say, a gold cadmium plate finish to provide better corrosion resistance w/o effecting the magnet properties of the steel parts?
Jeff Schwenksolenoid mfgr - Laguna Hills, California, USA
2004
A. This question is multi-faceted. Yes, you could electroplate the solenoids, although it will add a couple to a few ten-thousandths of an inch to the dimensions. The effect on magnetism should be minimal; i.e., it doesn't change the magnetism, but it does keep other things a few ten-thousandths of an inch away from the magnetic surface.
Some plating baths have filters and some, including cadmium, often don't. But good anode bags and efficient filters are extra important when you put a magnetic object into solution because metallic fines are prevalent.
Cadmium is no longer commonly and casually plated because it is a cumulative toxin. You probably should be thinking of a zinc alloy plating (zinc-nickel, zinc-iron, zinc-cobalt, tin-zinc) or electroless nickel.
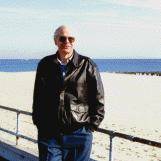
Ted Mooney, P.E.
Striving to live Aloha
(Ted can offer longterm or instant help)
finishing.com - Pine Beach, New Jersey
2004
2004
A. I AGREE WITH TED REGARDING THE MAGNET PROPERTIES. SOME OF THE ZINC ALLOY SYSTEMS THAT TED MENTIONS MAY BE TOO EXPENSIVE OR MAY JUST BE OVERKILL. TODAY THERE ARE AVAILABLE TRIVALENT CHROMATES FOR ZINC PLATING BATHS. OUR TESTING ON 1010 PANELS IN ACCORDANCE WITH ASTM B117 NEUTRAL SALT SPRAY OFFERED RESISTANCE UP TO 150 HOURS TO WHITE RUST (CORROSION) AND 264 HRS. TO RED RUST.THIS WAS AT A THICKNESS OF .0002" MIN. OF ZINC FOLLOWED BY THE BRIGHT BLUE/CLEAR TRIVALENT CHROMATE. THIS CHROMATE ALSO ELIMINATES THE ENVIRONMENTAL CONCERNS ASSOCIATED WITH TOXIC HEXAVALENT CHROMATES, WHILE MEETING THE AUTOMOTIVE AND EUROPEAN DIRECTIVES TO ELIMINATE HEXAVALENT CHROME.
AS AN ASIDE, THE HIGH CORROSION RESISTANCE IS NOT AFFECTED BY TRADITIONAL BAKING CYCLES IF REQUIRED, AND OTHER EXPOSURES TO HEAT ASSOCIATED WITH CURING PROCESSES TYPICAL IN PAINTS, POWDER COATS AND RUBBER MOLDING, AS WELL AS SERVICE CONDITIONS. THE ONLY QUESTION HERE IS AND TED HAS ADDRESSED THIS BEFORE, THE COLOR OF THE CHROMATE IS CONSIDERED CLEAR. SOME HEADWAY IS BEING MADE TO PROVIDE A YELLOW TO WORK WITH THE TRIVALENT CHROMATE.
Michael SwaskoSaporito Finishing Company

Cicero, Illinois
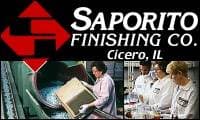
Plating magnets with titanium or stainless steel
Q. Hello
I wish to ask how titanium nitride and stainless steel can be applied to neodymium iron boron magnets. I'm doing this for a ninth grade science fair project on what materials would work well protecting a magnet from kinetic force and friction but yet be very thin (~1 mm). The magnets are neodymium iron boron magnets, the strongest permanent magnets, and therefore can easily destroy themselves. They also oxidize quite easily so the coating needs to protect against this as well. Also important is how I would obtain these materials. Typically, these magnets are coated with nickel, or epoxy.
student - Orlando, Florida, USA
2005
A. Hi Michael. Neither titanium nor stainless steel can be electrodeposited, so electroplating of hem would be out. It probably is possible to PVD (physical vapor deposition) coat the magnets with titanium nitride, although there is a warning in thread 44884 that the required high temperature may destroy the magnet.
You apparently want to apply a thin coating as a sort of shrink-wrap to hold the magnet together, though -- so you probably want a material which will do a good job of that. Nickel is often electrodeposited that way with great mechanical properties, for record and CD stampers, flexible bellows, screening, and radio telescopes for space. I don't think a titanium nitride coating would match it. But if you need a coating stronger than nickel, so that your project advances the state of the art, a properly deposited nickel-cobalt alloy would probably have even better properties. You might see if NiCoForm [a finishing.com supporting advertiser] can offer you some advice on that.
Regards,
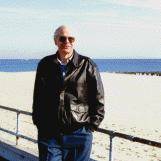
Ted Mooney, P.E.
Striving to live Aloha
(Ted can offer longterm or instant help)
finishing.com - Pine Beach, New Jersey
Multiple threads merged: please forgive chronology errors and repetition 🙂
Chemical interaction between rare earth magnet material and electrolytic Ni plating
Q. I'm working for a magnet manufacturer and I would like to discuss a very technical question concerning the chemical interaction between a rare earth magnet material alloy (NdFeB) and Ni electrolytic plating. It seems that the weakest bonding in a magnet-NiCuNi-glue system is the bonding between Ni and magnet material. Can anyone explain to me the chemical background of the Ni plating? What exact chemical substance bonds to what magnet particle when doing an electrolytic NiCuNi plating onto a NdFeB magnet. To me it seems that an Ni+ ion or an NiPO4 complex interacts somehow with the NdFeB metal alloy. The alloy is sintered, in other words the metal compounds are pressed and the bonding is strengthened by melting the metals onto each other. I must say that my specialty lies in magnetism theory and that I know only roughly about the chemistry of NdFeB magnets.
Can anyone explain me in more detail about how the Ni plating interacts with the NdFeB alloy on a microscopic level? Your help is much appreciated!
electronics mfgr - Schijndel, Noord-Brabant, Netherlands
2006
A. Submicroscopic (atomic) level. Your question deals with metallic bonds, affinity among different metal atoms, Van der Waals forces. These are present at the boundary. On the other hand, oxides, organics and other non-metallic species will reduce or sometimes totally destroy these bonds.
Guillermo MarrufoMonterrey, NL, Mexico
2006
Need to determine best type of plating on NdFeB magnets
February 10, 2011Q. Hello,
PROBLEM
I have a company that imports 5 mm magnetic spheres for playing / puzzle purpose. I'm having difficulty finding the right supplier, because many suppliers have different ways of plating. Because I don't know much about plating, I don't know what to look for and what questions to ask.
TECHNICAL INFORMATION
- Neodymium / Iron / Borium magnetic (NdFeB) core (N35 grade, approx. 5200 Gauss factory rating)
- Spherical shape
- 5 mm diameter
- A strong pull makes them subject to heavy impacts when two spheres hit each other. The impact area is small, due to their spheric shape.
REQUIRED PLATING PROPERTIES
So, the plating should have the following properties:
- Impact resistant
- Great reflection / metallic look
- Resistance to finger grease which is typically a little acid.
- Smooth appearance
Below the following question are some of the different types of finishing my supplier offers. I gave my remarks to each type of finishing.
MY QUESTION
What are your opinions on the layers of plating and what questions regarding the plating process should I ask potential suppliers to find the ones that have an excellent plating process?
---------------------------
Nickel coated item
No additional coating except the base Ni-Cu-Ni coating. Looks good, although it happened to me once that a small chip of coating came off.
Black Nickel coated item
Is this post-treated NiCuNi, or are there alternate ways? They do call it black nickel. From up close, the black plating looks uneven in some places; it is not really smooth. Also they give me black fingers when playing with them
Silver
Looks good, according to the manufacturer this is actually a NiCuNiAg plating. I'm aware that silver is a soft metal and is not very resistant to abrasion.
Gold
Also looks good. This is a NiCuNiAu plating (24 carat). Here goes the same as the silver item; gold is soft so it can fade and maybe even wear off over time.
Copper
NiCuNiCu... Quality is very poor. Color isn't even copper-red, more pink-like. Doesn't chip off, but surface looks cracked. Fairly easy to wipe off the color even with my fingers.
Zinc
NiCuNiZn... More durable than the copper one, but the surface also looks cracked. Color is quite bright blue. Not a nice metal finish.
Buyer - Rosmalen, NB, Netherlands
A. I would look at electroless nickel. There are some that are fairly ductile. They will fingerprint a bit.
Rhodium would seem to be a good choice, but it is expensive. Also, not many platers have larger tanks because of the material cost.
- Navarre, Florida
February 10, 2011
Need pinhole-free plating
Q. I need to plate a neodymium iron boron magnet to keep it from corroding. And it needs to be pin-hole free. We are currently trying to use a NI/NI process but keep getting pin holes.
Does anyone have any suggestions?
- Elk River, Minnesota, USA
January 6, 2010
A. Troy,
Must admit that I do not know anything specifically about neodymium-iron-boron alloy, but your results sound as if you have a pre-cleaning issue.
What pre-cleaning/activation are you doing prior to plating? You talk about Ni/Ni plating, is this an indication of nickel duplex layering, Electroless nickel over electrolytic nickel (or vice versa), or just nickel strike followed by a Nickel overcoat (either electro or electroless).
Personally, I would ensure the parts are properly pre-cleaned prior to plating (degrease, soak cleaner, possibly an activation stage prior to plating). I would then consider using a high phosphorus electroless nickel plating to 1-2 mils thick.
Hope this helps to get you going in the right direction.
Aerospace - Yeovil, Somerset, UK
February 18, 2010
----
Ed. note: Readers, please see other entries on this thread where it is suggested that porosity in the sintered metal is a problem dealt with via vacuum impregnation and/or a layer of copper plating between the two nickel layers.
Why Ni-Cu-Ni plating of NdFeB Magnets?
Q. A common plating technique for NdFeB magnets is a triple layer Ni-Cu-Ni electrodeposit. What is the purpose of the Cu sandwiched between the two layers of Ni?
I have asked several suppliers and their "experts" and have received lots of detail about the benefits of Ni, but little regarding the Cu - nothing more than "it's the industry standard/protocol".
I have posed my own reasoning/theories including adhesive (Ni-Ni) vs. cohesive (NdFeB-Ni and Ni-Cu) strengths as a function of coating thickness but all have been ignored.
Any help would be much appreciated!
R&D Engineer - Crawley, West Sussex, UK
August 24, 2018
A. Hi Ryan. I have no experience or inside knowledge about why Ni-Cu-Ni is used, but I have heard mention that the material is sintered and tends to create porosity problems ... so for a wild guess I'll venture that the copper helps to seal any porosity voids in the first layer of nickel plating :-)
Luck & Regards,
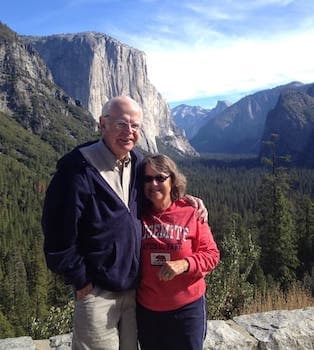
Ted Mooney, P.E. RET
Striving to live Aloha
(Ted can offer longterm or instant help)
finishing.com - Pine Beach, New Jersey
Q, A, or Comment on THIS thread -or- Start a NEW Thread