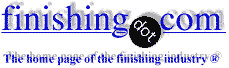
-----
Problems in cyanide copper plating

Q. We are doing bright cyanide copper plating for 'iron core' used in relay. Our customer requirement is 3-5 µm thickness. We are facing problem of discoloration and blackish marks on copper. We are also doing anti-tarnish treatment after plating but with no satisfactory results.
PIYUSH JAINBusiness Owner - ROHTAK/HARYANA
May 11, 2023
by Larry Durney
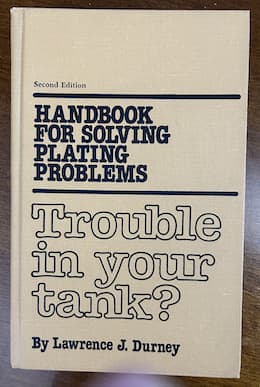
on eBay or Amazon
or AbeBooks
(affil link)
A. Hi Piyush,
Please send photos to mooney@finishing.com for posting here, and give us some idea of how often these black marks occur, whether there is any pattern to them (low current density, HCD, bottom of tank, top of tank, etc.) and how long after plating. Unfortunately there can be a good number of causes from solution contamination or improper makeup, to poor preparation of the surface, to cyanide bleedout, to blackening by sulfur
⇦ on
eBay
or
Amazon [affil link]
in the local atmosphere, to poor anti-tarnish application. Readers may be able to help you, but without more info the scattergun ideas that can be offered probably aren't a very efficient troubleshooting method :-)
Luck & Regards,
Ted Mooney, P.E. RET
Striving to live Aloha
(Ted can offer longterm or instant help)
finishing.com - Pine Beach, New Jersey
⇩ Related postings, oldest first ⇩
Copper is Building Up in Cyanide Copper Plating Baths
Q. I work for a company that operates a three large 56,000 liter copper cyanide electroplating baths. The bath operates using soluble copper anodes contained in titanium baskets.
The problem we are finding is that the anode efficiency is greater than the cathode efficiency resulting in a build-up of copper in the bath. This build-up of copper we are finding has a detrimental effect on the quality of the plated components.
How do I maintain the copper balance in the bath?
Any suggestions would be appreciated.
What is OFHC copper?
Regards
- UK
2001
A. You may try to use insoluble steel anode instead of copper anode.
OFHC means Oxygen Free High Conductivity.
- Hong Kong SAR
A. We vary the anodes. We use three baskets on one side of the tank and one anode basket on the other side with two steel anode sheets. Our copper levels remain very consistent with this method.
Angie Molnar- Canada
Cyanide copper plating is dark/black in HCD area
Q. We recently upgraded to a larger copper strike bath. Since doing so we have had a difficult time getting the bath to plate as well as it did before. Instead of making up new solution we used 55 gal of another companies plating bath. They insisted it was working well. We had an analysis done of the bath after putting it together and found the copper cyanide was high and the free cyanide low. Therefore we added enough sodium cyanide to get the free cyanide into range. We did this in slow increments as to avoid having a high free cyanide as well. When we turn the current to about half of what we did before the black/dark spots on the high current areas is reduced but also the plating time is much longer to get a good color and thickness on the substrates being plated. Is there any chance there was a contaminant in the solution we used that could be causing this?
Current tank size is 450 gallons. 55 gallons of used solution was added to make up the difference of tank sizes.
We will be installing mild steel anodes to help reduce the copper cyanide level.
Thanks.
employee - New Castle, Indiana, USA
May 17, 2011
A. I would check the carbonate level. High level decreases efficiency which could show up as low plating in the lows. A good carbon treatment never hurts but copper strikes are very tolerant of organic contamination.
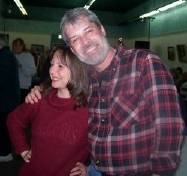
Trent Kaufman
electroplater - Galva, Illinois
Update.
We have had better success since adding Sodium Hydroxide. I understand that many platers use this in their cyanide copper strike but we have always ran it at very low quantities usually for pH control. Analysis always read 0.0 oz/gal. Now we have bumped it to 0.6 oz/gal. The plating is still not the salmon color we were used to but the thickness and smoothness of the deposit is much better. The darkness and black on the high current areas are no longer present.
Q. Any idea on why the need for sodium hydroxide in order to get better results when we didn't use it in the past?
pH was reading 11 before we even added the sodium hydroxide.
- New Castle, Indiana, USA
Q. We run a cyanide copper flash process and are getting a blackish deposit which seems thinner than usual at the high current density on parts and test panels. The copper content is mid range at 49 g/l and the cyanide level is just above mid range at 32 g/l. We have changed all the anode bags and peroxide treated potential iron contamination.
I'm running out of ideas fast and would appreciate any thoughts on this!!
Thanks
- Poole, Dorset
November 24, 2011
A. Hi Emily,
Problem could due to too high carbonate content (> 120 g/l) which reduce cathode efficiency, or organic/sulfur contamination. Perform carbon treatment or bath dilution may help.
Regards,
David
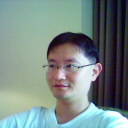
David Shiu
- Singapore
Thanks,
We have been filtering through a carbon filter for 4 days. There is a marked improvement. I will also test the carbonate level to make sure this is not an issue.
- Poole, Dorset, UK
The problem has been solved on Brass components with carbon filtration but not on Steel. I have since tested the carbonate level and found it to be 102 g/l. So in the lab have performed a half dilution and a Hull Cell
⇦ huh?
. It looks much better on both materials.
- Poole, Dorset, UK
Q. We use Copper cyanide bath for copper flashing on steel parts. Recently, in my absence from plant we are experiencing a problem. What used to take 2 minutes now takes 10 minutes to plate. Concentration of free cyanide is 2.4 oz/g, pH is about 12 and carbonate 36 g/l. Please help me resolve this problem.
Veena Mandlay- Carpinteria, California, USA
January 8, 2013
A. Hi Veena.
The free cyanide/pH/carbonate contents sounds about right. Two questions come to mind.
1. What is your copper cyanide content?
2. Is this a 'sodium' or 'potassium' base cyanide copper bath?
- Penang, Malaysia
Q. Mr. Cheah,
I have the same doubts you have about Copper Cyanide content but I don't know how to determine that. I was thinking of adding a little portion of Copper Cyanide in the bath to see if there is any improvement. I have carbon filter in the bath which is helping little bit. Also my bath is Sodium Cyanide base. I appreciate your help.
- Carpinteria, California, USA
A. Hi Veena.
1.Copper Cyanide content can be determined by titration.
Take 2 ml of sample solution. Add 15 ml of conc. Nitric Acid. Heat to blue color (this to be done in an exhaust hood). Add 100 ml of DI water. Add conc. ammonia
⇦ on
eBay or
Amazon [affil link] to blue color. Heat to 140 °F. Add PAN indicator. Titrate against 0.1M EDTA. Color change from purple to green.
CuCn ( oz/gal ) = ml x 5.971 x M
2.Take care when adding Copper Cyanide . An addition of 1 kg CuCN needs an addition of 1.1 kg Sodium Cyanide with no increase in free cyanide.
Good Luck.
- Penang, Malaysia
Thank you Mr. Cheah. My tank is getting better.
I have another problem in my Nickel Sulfamate tank. I'm getting some black/burned spots after electrolytic plating. And specially where the parts get in contact were current is passing. Most component in my tanks are at an optimum level except Nickel which is between 11.5-12.5 oz/gal. I performed carbon treatment, added stress reducer and plated dummies before plating good parts. My plating is on 1030 steel and I copper flash before nickel plate. Please advise. Your answers are always so useful.
Thanks,
Veena
- Carpinteria, California, USA
Q. I have a related Question I wish you can help me, I made a small in my lab as a test I wanted to simulate the plating unit in my factory the bath consisting of cyanide copper bath, a flash one of (120 g/L CuCN) and (138 g/L NaCN) and it went very well, but when I add 40 g/L NaOH to simulate the thick deposit bath the anode became black and passive ! it only works fine if I lowered the current but if I did the deposited layer become similar to flash bath so what is the advantage ! is there something missing !? it just work properly in the factory plating unit so I hope you tell my what have I done wrong
Ahmed Samir- Cairo, Egypt
March 3, 2013
A. Good day Ahmed.
I think that you have a formulation problem.You might want to look at these formulations as a guide.
General Purpose strike:
CuCN - 30 g/l
NaCN - 48 g/l (Total Cyanide)
FNaCN - 11.25-15 g/l(Free Cyanide)
NaOH - 3.75-7.5 g/l
Na2CO3 - 15 g/l
Rochelle - 30 g/l -Aids in anode corrosion and adjusts Cu Metal Conc. and acts as a grain refiner)
pH - 12.5-13.5 Use Dilute Acetic/NaOH to Adjust
Strike-Plate Bath:
CuCN - 42 g/l
NaCN - 52 g/l
FNaCN - 5.7 g/l
Na2CO3 - 30 g/l
Rochelle - 60 g/l
Ph - 10.2-10.5
Hope this helps.
Regards,
- Toronto, Ontario, Canada
(you are on the 1st page of the thread) Next page >
Q, A, or Comment on THIS thread -or- Start a NEW Thread