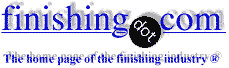
-----
How does Chromate Coating work?
Q. I am in need of some very basic information. Me and my group of engineering students are doing an environmental analysis of a bike. This particular bike is using Chromate coated steel pipes. So my question is: How does this work, and what are the environmental problems of this process? If anyone could be helpful, I would be most grateful (and I'm sorry for the bad English)
Janus H. NielsenStudent - Copenhagen, Sealand, Denmark
2004
A. The steel pipe is zinc plated and then chromated in order to give the pipe an attractive, corrosion resistant finish. The zinc plating offers sacrificial protection to the steel, but the zinc itself would quickly corrode and become an unsightly mess of white rust, discoloration, and pitting unless it is itself protected.
The traditional method of protecting the zinc was with hexavalent chromate conversion coatings. These form a number of corrosion resistant chromium-zinc compounds. Unfortunately, hexavalent chromium is carcinogenic; so there is great pressure to find substitutes. Some trivalent chromates are almost as good, and if afforded an additional step in the process, i.e., a topcoat sealer of silicates or other compounds, they may be just as good.
It is difficult to talk about substitute coatings in the abstract, because the reader and writer may not know what properties the design engineer was seeking. So it is good to hear that you are looking at the specific example of the tubing in a bike frame. Here conductivity is not an issue, tight-fitting clearances are not an issue, and a substitute could be paint.
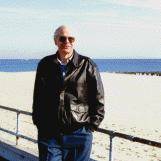
Ted Mooney, P.E.
Striving to live Aloha
(Ted can offer longterm or instant help)
finishing.com - Pine Beach, New Jersey
2004
Q. Ted Mooney's reply re. chromate finishes was very interesting. I have a surface conductivity problem with chromate finishes on zinc coated steel. What are the chromium-zinc compounds and are they conductive.
Ian JuniperOffice products - Harlow, Essex, UK
2004
A. All things are relative, but they are conductive. It is typical to use zinc plating plus chromate as a conductive finish on electrical fixtures for example.
The best I can do with the composition of the coating is to quote Eppensteiner and Jenkins "Chromate Conversion Coatings" from the Metal Finishing Guidebook: "... a complex mixture consisting largely of hydrated basic chromium chromate and hydrous oxides of both chromium and the basis metal. The composition of the film is rather indefinite because it contains varying quantities of the reactants, reaction products, and water of hydration, as well as the associated ions of the particular systems."
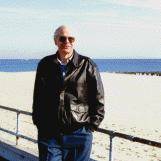
Ted Mooney, P.E.
Striving to live Aloha
(Ted can offer longterm or instant help)
finishing.com - Pine Beach, New Jersey
2004
Can we do chromate coating on a formed part made from E.G. CRS
Q.
While I know that a bare steel or iron part cannot be chromated, but can anyone explain WHY - in fairly simple layman's terms. My college chemistry is woefully full of moth-eaten holes due to non-use these past 30 years.
A customer has a formed bracket made from E.G. CRS sheared from a .05" thick sheet, and is curious as to why we cannot chromate it. I know the chemicals in the chromate bath will attack the steel/iron and consume it, apparently finds it quite tasty!
- Beaverton, Oregon, USA
September 11, 2018
A. Hi Chris. "Chromate" is slang or short for "chromate conversion coat" ... a process which converts a surface from metal to a mixture of "... hydrous oxides of both chromium and the basis metal". The reason you can't chromate steel is because steel does not react with those chemicals and get converted into the beneficial compounds and mixtures you are seeking.
Electrogalvanized (zinc plated) steel can, in theory, be conversion coated because the surface is zinc. And it may have already been chromate conversion coated at the time of electrogalvanizing. However, whether the plating is now fresh enough, reactive enough, robust enough (considering the exposed sheared edges), and aesthetic enough for you to chromate it is another question. I think zinc phosphate followed by powder coating is probably a more robust treatment plan.
Regards,
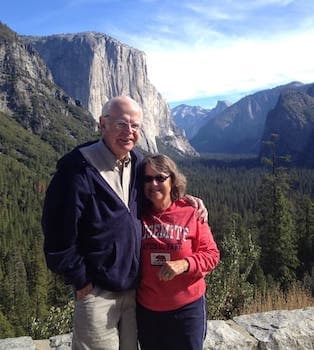
Ted Mooney, P.E. RET
Striving to live Aloha
(Ted can offer longterm or instant help)
finishing.com - Pine Beach, New Jersey
September 2018
Q, A, or Comment on THIS thread -or- Start a NEW Thread