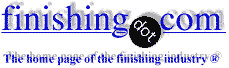
-----
Problem in copper plating over brass: poor adhesion
Q. Dear Sir or Madam,
For the meantime, I have a question of you, that when I electroplate copper over a brass sheet and when we cut it in press cutting, or we do the holes, the whole plating area is becoming peels out/up and in case of bending that sheet it also shows the same results. Please answer me how can I improve my plating to do further bending and cutting, etc.
Thank You,
Electroplating & Powder Coating - Riyadh, Saudi Arabia
2004
A. Hello cousin Imran. You haven't given us much info about your process yet, so it's difficult to begin. It could be that the plating is brittle due to contamination, but more likely that the cleaning process wasn't adequate. You should probably run Hull Cell ⇦ huh? tests with fresh brass panels and see if the plating is brittle or if it adheres well as you bend the test panels. Best of luck.
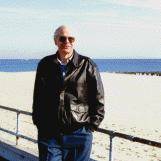
Ted Mooney, P.E.
Striving to live Aloha
(Ted can offer longterm or instant help)
finishing.com - Pine Beach, New Jersey
2004
A. Are you giving the brass a copper cyanide flash before using acid copper sulphate? I might also mention that I use an acid cleaner rather than an alkaline one, before attempting plating on brass or copper. I prefer sulfamic acid for that purpose. The cyanide copper plating provides the adhesion. Of course, go in hot electrically.
Vincent E Summers- Charlottesville, Virginia
2004
2004
A. Mr Imran Mushtaq,
Here is the sequence for Copper Plating Brass sheet. Please note: GOOD Cleaning is extremely important.
Soak clean in Cleaner for 3 to 7 minutes 60 to 70 °C
Cathodic Electroclean in cleaner at 30 ASF for 2 minutes or less. 60 °C
Anodic clean in cleaner for 20 - 30 seconds at 60 °C 40 ASF.
Rinse x 2 times in clean water
Acid activate in Sulfuric acid 5 to 7 percent for 20 to 40 secs.
Rinse in DI water
25 gpl Sodium Cyanide Pre Dip. 10 secs..
Strike in a dull cyanide Copper strike solution at 4 to 6 volts for 2 to 5 minutes at 45 °C.
Rinse twice after Dragout.
Activate in 4 to 5 % Sulfuric acid for 20 seconds
Rinse in DI water
Plate acid Copper at 4 to 5 volts as needed.
Dragout
Rinse twice in City water.
The activation in Sulfamic acid suggested in another response is acceptable, but it must be rinsed well so it does not carry over to the plating bath. Please note that Plating peels off when the base has not been cleaned or activated sufficiently well.
Regards,
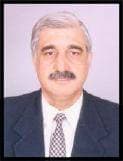
Asif Nurie [deceased]
- New Delhi, India
With deep regret we sadly advise that Asif passed away on Jan 24, 2016
Bright Acid plating of cartridge brass - blisters
September 23, 2014Q. I'm trying to determine the root cause of a bright acid plating issue on 260 cartridge brass parts. The parts are blistering and from what I've been told this is the process:
1. Degrease step with electrolyte (60-80 °C, 60-100 g/ltr)
2. Rinse & 2nd rinse
3. Sulfuric Acid (5-15%)
4. Rinse & 2nd rinse
5. copper sulphate
⇦ on
eBay or
Amazon [affil link] (200-250 g/ltr) / sulfuric acid (3-5 g/ltr)
6. Rinse & 2nd rinse
7. Tin sulphate (17-25 g/ltr) / sulfuric acid (8-12%)
8. Passivation 50-70 g/ltr, 40-60 °C
9. 4 separate rinses
10. Postbake at 300 °F, 1 hour
Is there anything that should be corrected? There have been a few attempts to fix the problem but I'd rather have some expertise on the matter. Any help is appreciated, thanks
Hobbyist - Chicago, Illinois
by Larry Durney
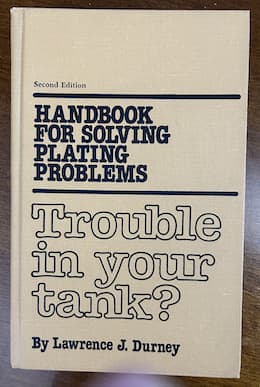
on eBay or Amazon
or AbeBooks
(affil link)
A. Hi Tom. I'm not sure from the way you worded this whether you are saying that you are doing the plating yourself or not. Does "from what I've been told this is the process" mean that someone else is doing the plating and has relayed this info to you, or does it mean this is the process you are running yourself and from what you've been told it ought to be the right process? Similarly with "there have been a few attempts to fix".
It's important to know because it is for practical purposes impossible to troubleshoot a plating process that someone else is running somewhere else. The first and most important step in troubleshooting, walking the line, is absent.
But we have appended your inquiry to a thread on the same subject, which should give you some basic ideas. Also, plating processes are generally not actually made up of basic chemicals like copper sulphate and sulfuric acid, but are purchased as proprietaries from suppliers who give you technical data sheets covering how to run them (temperature, concentration, current density, titration procedures, etc.)
Please get back to us with any further questions or data. Thanks.
Regards,
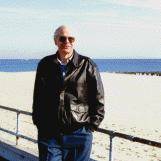
Ted Mooney, P.E.
Striving to live Aloha
(Ted can offer longterm or instant help)
finishing.com - Pine Beach, New Jersey
September 2014
Copper plating a brazed joint
Q. I made a copper picture frame (16" square with 1/4" thick copper, 1 1/2" wide) and brazed the mitered corners with a silicon bronze rod.
Can I electroplate the corner joints using a copper sulphate solution so that the surface color matches the rest of the frame? What voltage is suggested?
Douglas Eglenamateur blacksmith - Kokomo, Indiana, USA
December 23, 2017
A. Hi Douglas. I think there is no chance at all of plating the corners to match the rest of the frame, but that plating the whole frame is certainly a possibility.
You will not get 'proper' adhesion by plating a consumer-friendly copper sulphate plating solution onto brazing, but you might get enough adhesion for a picture frame. A better approach is probably to nickel strike the frame before acid copper plating it.
After you have cleaned it as best you can, and wearing gloves, scrub it with scrub brush ⇦ on eBay or Amazon [affil link] and a paste of warm water with a lot of powdered pumice ⇦ on eBay or Amazon [affil link] and a little dish detergent, then rinse it before attempting to immediately plate it. Something like 3 volts should be okay, and make sure you have an alligator clip attached so it goes in hot. If it comes out a nice dark copper color but isn't bright, you should be able to buff it to brightness. If it comes out salmon colored, the plating isn't really right, but you just might be able to warm it up with Brasso ⇦ on eBay or Amazon [affil link] . Let us know how it worked. Good luck.
If this is your first attempt at plating you should, of course, try it on scrap copper and brazing rather than your creation first.
Regards,
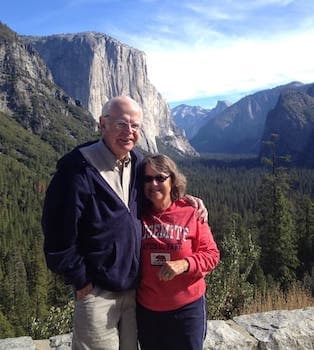
Ted Mooney, P.E. RET
Striving to live Aloha
(Ted can offer longterm or instant help)
finishing.com - Pine Beach, New Jersey
Q. I haven't tried your suggestion yet although I'd like to, because I don't know how to proceed with a "nickel strike". I found the forum post about someone wanting a simple recipe for nickel plating (topic 1298) and came away stunned by the complexity and hazards posted by the experienced moderators. My interp is that I shouldn't even try to do a nickel strike (but maybe that is different than a 'simple nickel plating recipe'). How to proceed to try to recover my frame appearance?
Douglas Eglen [returning]- Kokomo, Indiana, USA
January 17, 2018
A. Hi again Douglas. Electroplating doesn't involve a fixed amount of complexity, it's a matter of what you want to do, how well, and for who. Although brain surgery or playing a Franz Liszt composition at Carnegie Hall is very hard, any mom can change a band-aid and any child can be taught to plink out "Twinkle, Twinkle".
Similarly, any 3rd grade child can zinc plate a penny in a couple of minutes from simple instructions and with no chemicals more dangerous than vinegar ⇦in bulk on eBay or Amazon [affil link] ; but if you want to nickel-chrome plate a thousand aluminum or ABS pieces per hour and warranty them, you need to be quite knowledgeable. And just as there are nurses aides in medicine and municipal bands, there can be intermediate levels of plating knowledge & skill.
The dangers can also depend on scale; hot caustic cleaning solutions are needed if you want to plate thousands of parts per hour. But if you have only one piece, simple scrubbing with pumice as previously described above can be done instead of using those hot dangerous chemicals.
The easiest approach to plating is simply to find a plating shop to do it; but if you are an artist who wants to do the work yourself, it's not impossible. But it's easier if you just buy the plating baths and let someone else worry about how to formulate them; for the small amounts of chemicals you need, you can find someone who offers supplies to hobby platers.
As noted you may not need a nickel strike, but if practice pieces prove that you do, and can't buy it pre-made, search this site for "Wood's Nickel Strike" and you'll find everything you need to know. Again, practice how to do the strike, then practice going right from the nickel strike to copper plating, with just quick rinsing in between. When you can do it on scrap, you're ready to try it on your frame. Good luck.
Regards,
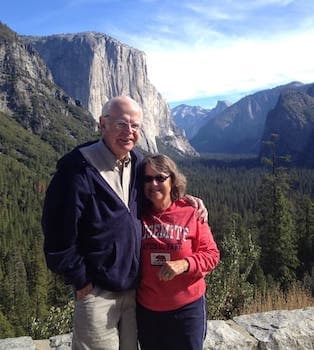
Ted Mooney, P.E. RET
Striving to live Aloha
(Ted can offer longterm or instant help)
finishing.com - Pine Beach, New Jersey
January 2018
Q, A, or Comment on THIS thread -or- Start a NEW Thread