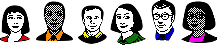
world gathers for metal finishing
Q&As since 1989
-----
Procedure for electropolishing stainless steel

Q. Hello,
I am manufacturing flexible shower hoses from SS201 and SS304
Please guide me to start the process of electropolishing
Which tank to use PP or PVC
Proportion of phosphorus and sulfuric acid
Which material to use as cathode
Which material to use for jigs
Is there any additives to be used
Is etching required before or just degreasing.
Thank you
- Cairo Egypt
September 12, 2023
A. Hi again Azeez.
Personally, I'd go with a fiberglass tank, but polypropylene is acceptable as long as you are aware of its flammability.
There is no "right" proportion of phosphoric to sulfuric acid, but 2 to 3 parts phosphoric to 1 part sulfuric is a common mix.
Lead is probably the most reliable cathode material although others are used depending on solution composition.
Jigs can be copper.
As for additives there are almost endless available electrolytes.
Etching is not required.
But there are week-long training courses in stainless steel electropolishing, and the introduction to electropolishing in the Electroplating Engineering Handbook [on
AbeBooks or
eBay or
Amazon]
is more than 20 pages. You asked for the "complete process" on this page 3 years ago, and I don't know whether you've done some serious investigation and are now down to these specific questions, or if you're still just starting to learn about it.
I think step 1 is to have an experienced electropolishing shop do some samples for you of both the 201SS and 304SS so you have a good idea of what is achievable; otherwise you may give up on improvement too soon, or expect miracles that no one has yet achieved :-)
Luck & Regards,
Ted Mooney, P.E. RET
Striving to live Aloha
finishing.com - Pine Beach, New Jersey
Hello sir,
I appreciate your immediate response and thanks for your advice.
I am going to do trail with my product first as you advised and will let you know of the results with photo
Thanks a lot.
Manufacturer - Cairo Egypt
September 15, 2023
⇩ Closely related postings, oldest first ⇩
Q. Hi. What's the best way of electropolishing stainless steel?
frank sarrazit- sheffield
1999
A. Hi Frank. Your question isn't specific enough to be answerable within the confines of the forum, Frank, because explaining the process takes about 20 pages. Please see the chapter about electropolishing in the Electroplating Engineering Handbook [on AbeBooks or eBay or Amazon] ; it's excellent and quite complete. But if that text isn't readily available, the Metal Finishing Guidebook, and ASM Metals Handbook Vol. 5 have pretty good introductions. Then please come back here and ask for clarification on anything you're having trouble with. Thanks.
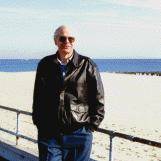
Ted Mooney, P.E.
Striving to live Aloha
finishing.com - Pine Beach, New Jersey
A. If you can give me more information on the specifics of what you are doing we may be able to help.
David Crocker- Valencia, California
Q. I am trying to solve an electropolishing problem with T304SS wire (0.187" dia). We are experiencing random problems with electroplating wire shelves, wherein some of the wires come out with a "frosty" surface. SEM/EDS has not identified any contaminants, and metallography of cross-sectional samples reveals that the "frosty" areas appear to be corroded (i.e., substantially amount of metal loss re: the good electropolished wires). Is there something with the bare wire that I should look for? Thanks,
JIM CIRILLITESTING LABORATORY - NEW CASTLE, DELAWARE
1999
A. Hello Jim. What you are describing (frosty look, loss of metal) sounds like etching. I believe that the two most common causes are the current density too low and water in the electropolishing solution. But there may be other causes -- unfortunately it's always easier to do one thing wrong than everything right :-)
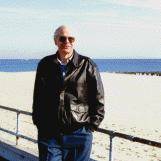
Ted Mooney, P.E.
Striving to live Aloha
finishing.com - Pine Beach, New Jersey
A. Do not electroclean before electropolish, soak clean only. Look for excessive solution movement, this will break down the "viscous layer"; the magic layer necessary for EP to take place. Also if you are doing wire goods remember SS is a lousy conductor, is the article picture framing?
Hope this is helpful.
Jon Quirt- Fridley, Minnesota
Q. Why would you not Electroclean before Electropolishing? Pardon my ignorance, but that seems counterintuitive.
Scott MerrittEastman, Georgia
June 10, 2012
Q. If Electro-Polishing is passivation, why passivate? Should passivation be completed before electro-polishing? Can nitric passivation before Electro-polishing accomplish adequate pre-cleaning necessary for electropolishing? What is the best method to pre-clean before electropolishing and what chemical, acidic or alkaline?
Mike Cochara- Springfield, Missouri
1999
A. Hi Mike. Electro-polishing inherently passivates, and obviates the need for separate passivation. I would not passivate wither before or after.
Prepare by alkaline soak cleaning; nitric acid is not an effective cleaner for dirt, oil, and greases.
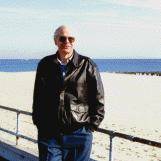
Ted Mooney, P.E.
Striving to live Aloha
finishing.com - Pine Beach, New Jersey
Q. Is it necessary to put a 316 SST weldment through pickling if it gets bead blasted prior to electropolishing?
Oswaldo Rangel- London, Ontario, Canada
2000
A. Hi Oswaldo. I don't believe so.
Luck & Regards,
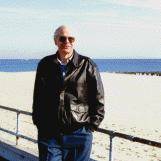
Ted Mooney, P.E.
Striving to live Aloha
finishing.com - Pine Beach, New Jersey
Q. I have Electro Polishing Machine. I am doing the polishing work on stainless steel for home products, i.e., steel glasses.
My problem is as follows:- I mix sulfuric - 50 kg & phosphoric 100 kg. and the temp. to make water hot is 60 to 80 degrees. and the time takes around 25 minutes. But after doing all this I can't get the perfect shine / brightness on glasses.
Can you give me the solution for this whereby I can get the perfect shine and less consuming time?
Please help me in this regard. It will be my great achievement Sir. Awaiting your reply.
Regards,
Dhiresh Chauhan- Mumbai, Maharashtra, India
2001
Hi, Dhiresh. Unfortunately, there are about 20 pages of things you must do right, including proper cleaning, proper formulation, proper temperature, proper racking, proper agitation, proper current density, proper procedure to exclude pre-cleaning rinsewater ... which conspire to make it difficult to guess which one or ones were missed. But it seems like you have a pretty good understanding of the process, so my first thought is that the shape, position, and racking of the glasses is causing trouble. Please try your best to electropolish a simple flat shape first and let us know the result. Good luck.
It is always difficult to process anything the shape of a water glass because anything other than exactly horizontal racking either causes excessive process solution carryover, or traps air and thus prevents proper processing.
Regards,
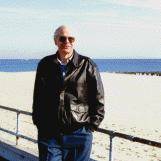
Ted Mooney, P.E.
Striving to live Aloha
finishing.com - Pine Beach, New Jersey
Q. Hello,
Somebody can recommend me how to build electropolish laboratory in my factory?
- Tel aviv, Israel
May 9, 2013
A. Hi Michael. The process sequence is quite easy: soak clean, double rinse, electropolish, double rinse. But it's not easy to do right if you have no prior experience, although the Electroplating Engineering Handbook [on AbeBooks or eBay or Amazon] will be a big help. There are companies like Metal Coating Process Corp. who specialize in educating people on electropolishing, and other companies like Russamer Lab [a finishing.com supporting advertiser] who license their knowledge and processes. Good luck.
Regards,
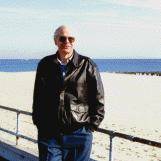
Ted Mooney, P.E.
Striving to live Aloha
finishing.com - Pine Beach, New Jersey
Why passivate after electropolishing?
Q. If you electro-polish a part then passivate it, what good would it do?
Herb schmoyercommercial metal polishing - bath Pennsylvania
June 15, 2017
A. Hi Herb. One reason for doing so would be to comply with specs; there are some which require it. A second possible reason is improved corrosion resistance. Traditional thought was that electropolishing provides excellent passivation without need for further treatment, but some feel that citric acid passivation after electropolishing improves upon it. We'll wait for someone who advocates for that to make their case.
Regards,
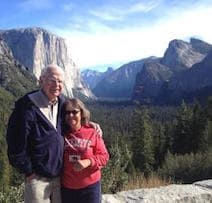
Ted Mooney, P.E. RET
Striving to live Aloha
finishing.com - Pine Beach, New Jersey
A. Herb,
Lots of folks say that electropolishing passivates stainless, but then we always have to be careful about the word "passivate", because it means a lot of different things depending on what process and what material you are talking about.
Electropolishing (or mechanical polishing for that matter) creates a very smooth surface, which is good for corrosion resistance.
A nitric or citric acid bath removes iron from the surface, which is also good for corrosion resistance.
If you remove the iron from a very smooth surface (i.e. polish followed by acid dip), then it is DOUBLY good for corrosion resistance!
But note that just one or the other may be perfectly sufficient depending on the application.
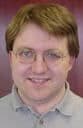
Ray Kremer
Stellar Solutions, Inc.

McHenry, Illinois
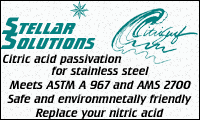
Non-uniform chrome finish on stainless steel parts
Q. Our finisher recently sent us parts with non-uniform chrome finish. The parts consist of a formed stainless steel rod TIG welded atop a stainless steel tube. Our finisher is of the opinion that the rod is not stainless steel, but we have confirmed that it is.
As seen in the attached photo, the chrome appears to have adhered fine to the tube and weld, but not to to the rod.
Any ideas how/why this might occur? Thank you in advance!
employee - Bryan, Ohio USA
January 9, 2020
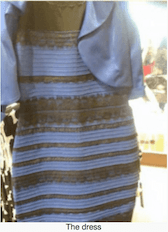
A. Hi Jon. Pictures can be deceiving, as the world knows from the famous gold & white dress which my son insists is blue & black. But your component looks to me like it has not been plated at all. Are you implying by "chrome finish", and by which thread you posted your inquiry on, that your finisher was supposed to nickel-chrome plate it? Or was he supposed to electropolish, manually polish, or what?
"Stainless steel" is a very broad description of the material of construction, and you should probably try to find out what types of stainless steel the rod and tube are, and to get at least a general description of what the alleged finishing process is. But personally, I'd probably retain a finishing consultant if I was in your situation.
Regards,
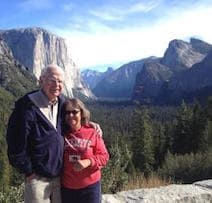
Ted Mooney, P.E. RET
Striving to live Aloha
finishing.com - Pine Beach, New Jersey
! Ted,
Thank you for your response! I did some quick checking, and you are absolutely correct - these parts are to be electro-polished.
Ironically, it is a mixed lot. Some parts have the bent rod polished fine, while others are not polished at all. We have even found one part which is electro-polished halfway across the bent rod, to just past the weld. The remainder is the unpolished grey look.
- Bryan, Ohio USA
A. Hi again Jon. Myself and other readers would like to help, but finishing is like anything else: We might possibly be able to assist your electropolishing shop in a small way if they told us exactly what steps they were doing and if we were 100% sure of the alloys ... but unfortunately it can be impractically difficult to try to guess what went wrong only from a picture of the end result :-(
Was the rod black before you shipped it? Did anyone do any heat treatment after the welding? Why are the parts electropolished -- only for looks, or for corrosion resistance, or for cleanability/hygiene? Can you send one unsuccessfully polished part to another electropolishing shop to see what they say and achieve? You can search the site for "electropolish stainless steel" to learn more. Thanks.
Regards,
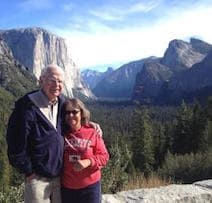
Ted Mooney, P.E. RET
Striving to live Aloha
finishing.com - Pine Beach, New Jersey
Q. I am manufacturing SS flexible hose made of SS291 and 304
And I need to know the process of doing electropolishing to get mirror finish. I want to start with small tank of size 120 cm x 80
Please anybody could guide me with the complete process.
As I am new to this field.
Thanks,
Azeez
- Cairo. Egypt
December 9, 2020
A. Hi Azeez. You need to mechanically prepare the component, then properly clean and rinse it, then electropolish it. Unfortunately, I don't know exactly what "new to this field" means; but you're not going to learn to electropolish solely from a response to your question here. You can start with the previous Q&A's on this thread, search the site with the term 'electropolish stainless', and consult the 22-page chapter in the Electroplating Engineering Handbook [on AbeBooks or eBay or Amazon] for current density, solution concentration, and some other tips ... but it will still hard to do without knowledgable hands-on instruction.
Luck & Regards,
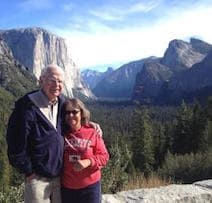
Ted Mooney, P.E. RET
Striving to live Aloha
finishing.com - Pine Beach, New Jersey
Try https://www.worldstainless.org/Files/issf/non-image-files/PDF/Euro_Inox/Electropolishing_EN.pdf. There you can find download free booklet on electropolishing of stainless steel...
Hope it helps and good luck!
- Zagreb Croatia
February 3, 2021
Hi,
I am an engineering student. I am working with an LCA project, which is about comparing two different types of steel.
I have some issues to find the correct data for electropolishing stainless steel.
I have a sculpture which is made only of stainless steel.
The surface area is 5m2.
The dimensions are L100 x W200 x H230 cm.
So my questions are,
How many liters of water, sulfuric acid and phosphoric acid shall the tank contain?
How many kWh is added to the tank?
How much nitric acid is added to the post-treatment stage?
I hope you can help me to answer these questions. :)
Student - Denmark
October 25, 2022
A. Hi Anders. You can look at Charles Faust's US patent 2,334,698, bath No 5, at patents.google.com, which is a sulfuric acid and phosphoric acid formulation claimed to be satisfactory for both 3xx and 4xx stainless steels.
The process tank should be big enough to allow at least 15" of free space below, 6" above, say 6" or more on each end, and 12" or more on each side (to accommodate clearance, and cathodes).
I don't see a need for an actual nitric acid post treatment, but a dip in dilute nitric acid can often improve rinsing
I assume that this is a hypothetical project, and you're not actually attempting to electropolish a sculpture. But if you are, be warned that it's not as easy as it sounds, so you would want to do significant experimental work with smaller parts first, then with scrap of this size before risking an actual sculpture.
Good Luck!
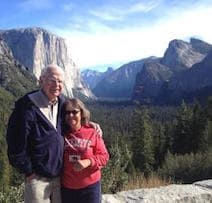
Ted Mooney, P.E. RET
Striving to live Aloha
finishing.com - Pine Beach, New Jersey
Q, A, or Comment on THIS thread -or- Start a NEW Thread