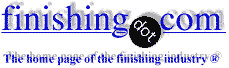
-----
Anodizing Aluminum for Artists
Current questions, newest first:
Q. I am a metal artist and discovered I really enjoy anodizing aluminum. Going to use in my steel, aluminum & plexiglass sculptures and jewelry. I recently purchased some 8-32 aluminum screws. I drill and tap 8-32 holes into my aluminum blanks and threading screw in and wrapping titanium wire around the screw before applying an aluminum washer and 2 aluminum hex nuts to squeeze wire and cover threads on screw. I don't want to anodize the actual threads but the exterior of the hardware I'm fine with.
My first question is, will the threads on my hardware remain un-anodized if I keep the threads covered? Second question is, if the external parts of my screws and nuts are anodized, will they build up more coating on second run or resist further anodizing?
- Indianapolis Indiana
February 28, 2022
A. Hi Jason. I can't fully picture what you say you are doing, but two problems are that
• threads are not watertight, so anodizing on the screw threads and inside of the nuts will be an iffy proposition
• aluminum is consumed in building the anodized film, then stripped in pretreatment, then more is consumed.
I think the real answer to your question is to find a cheap source and buy the screws, nuts, and washers in bulk and don't reuse them. Architectural anodizers frequently use aluminum screws to secure the extrusions to the anodizing racks, more or less like you are doing, but they discard the screws after each use.
Luck & Regards,
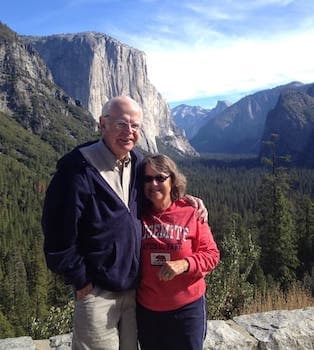
Ted Mooney, P.E. RET
Striving to live Aloha
(Ted can offer longterm or instant help)
finishing.com - Pine Beach, New Jersey
March 2022
Q. Re-anodizing a sculpture from the 1960s?
As they say on the radio: "long time listener; first time caller".
Need advice please, anything you've got. But specifically how to prep an old sculpture for a new anodizing or if that is even advised or possible.
I have been asked to quote the repair and restoration of an aluminum sculpture made of 5" aluminum square tube of unknown type, bent in various shapes and bolted together. It was anodized in the 1960s and has lived outside.
How do I prep it to send it to the wizards who do such things? Take it apart, clearly, but then what and how much of it?
Any advice y'all would be willing to offer would be helpful.
- Hudson New York
December 22, 2021
A. Hi Dave. I think photos would be a big help because I can't picture what you're speaking of. Is it aluminum color, or one color, or multi-colored? Since it's made of 5" square tube, it's probably pretty big. 5" square tubing is probably only available in two or three alloys and heat treatments, so it may not be that hard to figure out what alloy it is; it seems like most of it is 606x-T52 which ought to be readily anodizable. Does it look polished or scratch brushed?
Luck & Regards,
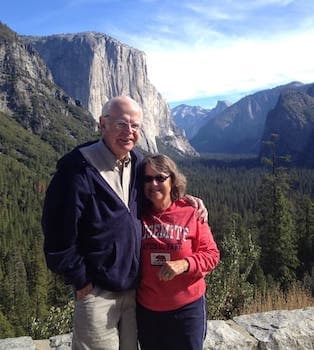
Ted Mooney, P.E. RET
Striving to live Aloha
(Ted can offer longterm or instant help)
finishing.com - Pine Beach, New Jersey
December 2021
January 5, 2022
Thank you for the reply -- this forum is the best!
Sculptor and Art Restorer - Hudson New York [returning]
privately respond to this RFQ
Ed. note: As always, gentle readers: technical replies in public and commercial replies in private please (huh? why?)
A. Obviously the sculpture needs to be broken down into parts that can fit inside the process tanks of whoever will anodize it.
Re-anodizing in this case can be a pain, so let me explain why (I speak from experience). The old anodize will need to be chemically etched off (this is the most efficient method) after which, if a different surface finish is required, mechanical finishing will need to occur before the part is anodized. This means you will need to send it out for stripping, refinish in house or outsource that too, and then send it back to the anodizer. Yes, one can grind off the anodize, but it is not worth the effort of trying to get all the nooks clean, and if any is left behind, it will compromise the anodize when the part is re-anodized. The plater will not be looking for left-over anodize on your parts and will not pretreat them accordingly to remove any leftover, when they do a standard pretreatment for anodize.
Next, the parts though big, may float in the anodize tank, if they are welded shut, which is a real buzzkill when you go to anodize something and it floats. The only way to really solve this for something so big, is to insure drainage and vent holes are placed on the part. Now anodizers also hate when customers have 6" tube weldments but place 1/2" holes for air vents and drainage. The holes should allow for near immediate drainage, so preferably 2-3" holes on 5" tube (at the ends of a section are fine). The anodizers will also need to try and rinse out any processing solutions between different tanks, out from inside the weldments, so the bigger the holes the better. Just remember, wherever the holes are placed, air and solution need to be able to enter and leave, so you cannot place all your holes on one side and expect the air to escape out of one as water enters the other. This may seem obvious, but you would be surprised with what people want to get anodized.
If you have any flat butt joints on the parts, or any cracks or porous welds which can wick solution into them, these will likely trap processing solution in them, that will leach out later, ruining a dyed finish immediately, with big white drips or streaks. This is also a bummer, so as general practice, minimize any such features. Also, if the welds are a different alloy than the tube (which they will likely be) they may anodize a slightly different color (this is unavoidable).
In regards to finish, a hard coat type III anodize at 2-3 thou, sealed with nickel acetate will give you a very robust corrosion resistant surface (or better, a duplex sodium dichromate and NiACE seal if you want it to be lime green and don't mind the chrome). Type II anodize is cheaper and is alright, but type III almost always comes out on top in terms of durability. In regard to dyes for outdoor use, one can use dyes with 10 or higher values for fade resistance (usually black shades) (your anodizer will know what they have), or use electrolytic colorants, which are fade proof, but I do not have any experience using them.
Lastly, if the sculpture has a clear coat lacquer or any polymeric finish on it, that will need to be blasted or chemically stripped off. Overall, both of which are tedious processes.
Hope this helped a bit with the ins and outs, let me know if you have other Qs.
Plating Engineer - San Diego, California
January 10, 2022
Man, I sure appreciate your help on this! The challenge is a daunting one -- namely make the thing look basically brand new, in spite of the fact that it has sat outside for 50 years (and really really really isn't brand new at all)
Add to that the fact that the piece is almost certainly worth a great deal of money.
(The only good thing about that, is that the costs of repairing/refinishing it are largely irrelevant to the client, who cares only that the repair and refinishing are flawless at the end).
Q. So I should ask another question: am I correct that for aluminum durability outside, anodizing is the only game in town? My perception -- and I may be wrong -- is that any type of sprayed finish over raw aluminum is going to look like hell inside a decade.
So it sounds like I need to find someone in the Albany NY area with a big enough anodizing tank to handle an 8' circle. Take the thing apart, get them to chemically strip the pieces. Then fix the pieces, then bring them back for anodizing.
And if the pieces are going to float, provide generous compensation for the added effort.
I'm not sure what protocol is on this forum for asking such questions, but does anyone have any recommendations for an anodizer in the Albany (or NYC) area with a tank big enough, who might be willing to do it?
Sculptor and Art Restorer - Hudson, New York
privately respond to this RFQ
Ed. note: As always, gentle readers: technical replies in public and commercial replies in private please (huh? why?)
A. It is difficult to judge from the pictures, but if it was sitting outside for this long, it is a good bet that it will have deep corrosion pitting especially at places that hold on to moisture (be it condensation or rain). If the pits are there, it will look like a mess after anodizing; those pits trap acid and will leak during sealing, and then with time you can expect it to corrode near those spots much quicker than when it was made new.
Hence I'd use paint, automotive, mix base to mimic the original texture/color when viewed from the average distance people used to see the structure, and then clearcoat it with additive that makes it look slightly matte, which is how I'd expect the original finish looked like new, this also allows you to treat the parts to any repairs necessary to get the smooth finish, which would be very difficult to do if the part would be simply stripped and re-anodized.
I wouldn't call the paint as the "cheap" option, rather the much more sensible one, it will be much easier to guarantee the result when compared to the re-anodizing option.
- Riga, Latvia
January 12, 2022
Wow! Thank you. I am so glad I asked. This forum really is a bright spot in an internet that is often anything but.
That sounds like good advice -- plus, painting I can do in my own shop where I have control over the quality of the job done. I will switch to another posting to ask advice on prepping aluminum for auto paint.
Artist and art restorer - Hudson New York
January 12, 2022
privately respond to this RFQ
Ed. note: As always, gentle readers: technical replies in public and commercial replies in private please (huh? why?)
February 8, 2022
Thank you all for helping out with this project; having a resource like this available is amazing.
RFQ: The client wants to re-anodize the sculpture, and money is no object. (I have an idea that the piece may be quite/astonishingly valuable, and needs to be kept as original as possible.)
A question then: I understand that acids from the anodizing will get trapped in any pitting from corrosion, correct? What if the entire thing were sanded by hand? Sand off all the anodizing and get to the very bottom of those little pits before proceeding. Cost is truly not a consideration on this job, so taking a literal month of skilled labor-billed shop time to do nothing but sand it isn't a problem at all.
If I delivered the pieces to the anodizer sanded totally clean, would it work to reanodize it?
I believe that this RFQ is open to the public at this point, and I badly need an anodizer in the New York/New England area able to anodize an 8 foot diameter circle. If anyone knows one, please DM me.
Thanks again,
Dave
Art restorer - Hudson, NY (upstate New York)
privately respond to this RFQ
Ed. note: As always, gentle readers: technical replies in public and commercial replies in private please (huh? why?)
⇩ Related postings, oldest first ⇩
2004
Q. I'm a sculptor and have started doing more wall hangings from steel--they're HEAVY! Would like to start working in aluminum but I would need to find some info on anodizing in a painting fashion where I can work with many colors. I once saw an article on art anodizing but can not find it so I know it is possible. Does anyone have information on where I would get started with this book, group, web-site etc?
Steve GrazianiArtist - Los Angeles, California, USA
The Sulfuric Acid Process"
by David LaPlantz
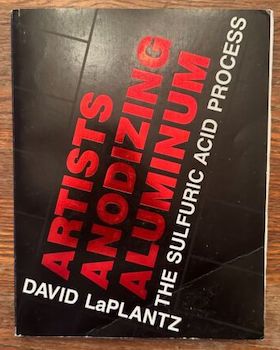
on eBay or Amazon
or AbeBooks
(affil link)
A. Artists Anodizing Aluminum by David LaPlantz is book for you!
Goran Budija- Cerovski vrh Croatia
2004
2004
A. Prior to anodizing you may need cleaning and polishing. For sulfuric acid anodizing you'll require:
1-sulfuric acid 10%v/v and a container
2-lead cathode
3-cooling to less than 20 °C
4-DC power supply of around 1.5A/sq dm
5-DI water for rinsing
6-DI boiling water for sealing
AND GOOD VENTILATION
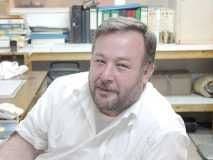
Khair Shishani
aircraft maintenance - Al Ain, UAE
A. Awhile back I was going to do anodize painting but after researching it I noticed that the color would fade way too fast to be acceptable for me. It's such a thin layer of pigment that UV exposure washes it out real quick. While I think it would work ok for cheaper art projects and still use anodizing for knife parts, picture holders, etc, I would hesitate to use it in a project where you want the color to last for years.
Jason Aube- Flint, Michigan
2004
A. Some anodizing colors, based on organic dyes, will fade with exposure to the elements. Other anodizing, based on metal salts, is used on buildings and doesn't fade for decades. However, it is also true that the more brilliant colors are based on the organic dyes whereas the colors based on metal salts tend to be more champagne, bronze, and brown.
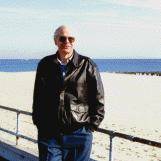
Ted Mooney, P.E.
Striving to live Aloha
(Ted can offer longterm or instant help)
finishing.com - Pine Beach, New Jersey
2004
Q. How to give aluminium a blue shade. I am an artist and designer; I just want to do some experiments with aluminium.
Bonny [surname deleted for privacy by Editor]artist - Goa, India
2005
A. Hi Bonny (full name next time please -- this forum is a place of camaraderie not anonymity). If you mean you just want to play around with different colors to check out the look, aluminum can be dyed; even 'magic markers'/'indelible markers' will work.
But if you want a lasting finish, the process involves anodizing the aluminum (which fills the surface with millions of microscopic 'drill hole' pores), then dyeing it in the blue shade of your choice, then 'sealing' it (which swells the tops of those pores, locking the dye in). Good luck.
Regards,
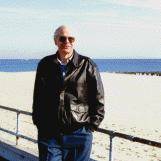
Ted Mooney, P.E.
Striving to live Aloha
(Ted can offer longterm or instant help)
finishing.com - Pine Beach, New Jersey
Q. Hi. I am a sculptor working in stainless steel using mostly 316 with a mirror finish. I have developed an itch reaction to chromium dust. I am considering changing to aluminum to avoid chromium. Is there any way to preserve a mirror finish on aluminum long term on large public art pieces? I looked into Everbrite [a finishing.com supporting advertiser] but it does not last indefinitely.
Thanks.
Cathal
Artist - Ireland
January 14, 2020
9th Edition, Vol. 5
"Surface Cleaning, Finishing & Coating"
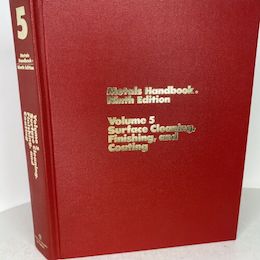
on eBay or Amazon
or AbeBooks
(affil link)
A. Hi Cathal. Proud to 'meet' you. Boy, do I have the world's best job, being free to sit home browsing the internet for whatever interests me, and having the nerve to call it 'working' :-)
A reflective finish on aluminum can be maintained indefinitely by anodizing, even in a tough environment. In the days before bright automobile bumpers went out of fashion, some were made of anodized aluminum to lower the weight, and hundreds of millions of streetlight reflectors have been made from aluminum and then anodized.
Aluminum is even more reflective than stainless steel or chrome, but because of this it has a slightly 'whiter' cast compared to the slightly 'blue' cast of stainless steel.
However, you might want to do a bit of studying regarding what aluminum alloy to use. While anodized aluminum (aluminum oxide and related compounds) is transparent, the alloying materials (copper, magnesium, silicon, etc.) must be removed from the surface by bright dipping or electropolishing, and the anodizing process brings them back out again as a grey-black smut. It's probably unlikely that you can get a good mirror finish on cast aluminum. It's well worth checking out a large or university library for a copy of ASM's Metals Handbook ⇦[this on
eBay,
AbeBooks, or
Amazon
affil links]
because it has a great chapter on obtaining reflectivity on aluminum. Good luck
Regards,
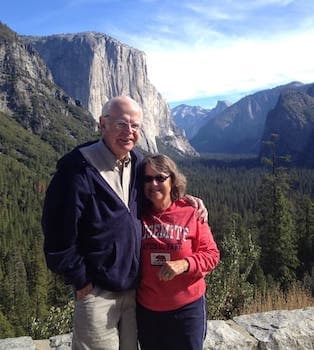
Ted Mooney, P.E. RET
Striving to live Aloha
(Ted can offer longterm or instant help)
finishing.com - Pine Beach, New Jersey
January 2020
January 16, 2020
Thanks a lot Ted for the helpful response. Some things are helpful for the chromium issues.
1 using a good barrier cream on hands and face.
2 wearing gloves, long sleeves, cap and trying to keep covered as much a possible.
3 Do any grinding you can outside wearing a full face mask and Tyvek suit.
4 Open all doors and windows to get dust out
5 Do grinding at end of day then Hoover up in morning.
6 vinegar
⇦in bulk on
eBay
or
Amazon [affil link] diluted for hands and bath. Chromium is alkaline so vinegar neutralizes it.
I found a company that does clear anodizing so going to try a sample.
Yes the gold, bronze grey and brown colours seem better options for longevity outside...
Artist - Ireland
February 26, 2020
Q. Hello! (Long time reader, first time poster) My name is Nick Lazenby and I'm currently working on a few concept art pieces. I have one piece that is comprised of aluminum and copper. I casted the piece in multiple stages, using hooks and anchors to join the metal. I'm worried about long term corrosion and was considering anodizing, not only for the perceived anti-corrosion benefits but it would also be interesting to play around with the color and texture. I'm currently using diluted sulfuric acid . My questions are:
Will that produce the desired corrosion benefits?
Should I even be worried about corrosion?
How significant would the corrosion be? (for reference there's about 10-20 sq inches of Al/CU contact). Difficult to measure since some contact is below the surface)
will the presence of copper interact with the anodizing solution or overall process?
What would the effect be on the copper post anodizing/dying?
I very much appreciate any responses and look forward to contributing to the community here. Cheers
- Kansas City, Missouri USA
A. Hi Nicholas. Assuming these pieces are for outdoors, corrosion is an issue, and aluminum in contact with copper is a bad idea. You can't anodize it with copper exposed. I'd suggest considering clear coating both the copper and the aluminum.
Regards,
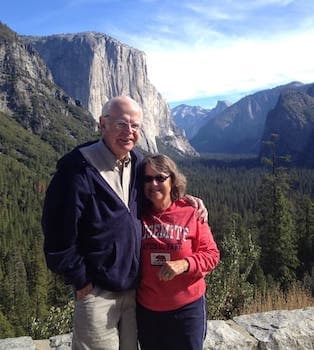
Ted Mooney, P.E. RET
Striving to live Aloha
(Ted can offer longterm or instant help)
finishing.com - Pine Beach, New Jersey
February 2020
Q. Thanks for the feedback Ted.
Are you saying the Aluminum wouldn't anodize at all due to the presence of copper in the bath?
- Kansas City, Missouri USA
February 26, 2020
A. Hi again. Yes. Even if the sulfuric acid and anodic current did not ruin the copper, you would never be able to build the electrically insulating anodic film on the aluminum because the applied current would flow to the copper.
Regards,
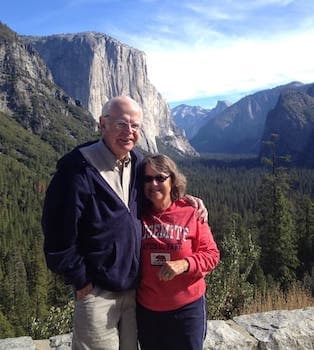
Ted Mooney, P.E. RET
Striving to live Aloha
(Ted can offer longterm or instant help)
finishing.com - Pine Beach, New Jersey
February 2020
Makes sense! I think I'm going to cast my Al part, anodize and then cast the copper parts so the Cu wont be present during anodizing. I'll post pictures if I come across anything interesting.
- Kansas City, Missouri
February 26, 2020
Q, A, or Comment on THIS thread -or- Start a NEW Thread