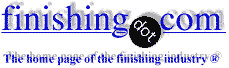
-----
Q&A: Electropolishing 304 stainless steel, or alternatives to it

Q. Please suggest best chemical composition for water bottle electro polishing, steel grade ss304, 0.3 mm thickness
Jayavel/jay/s jayavel/shanmugam/s- Chennai Sriperambathur, India
June 21, 2022

Probable cause: Corrosion on non-immersed area above the solution level.
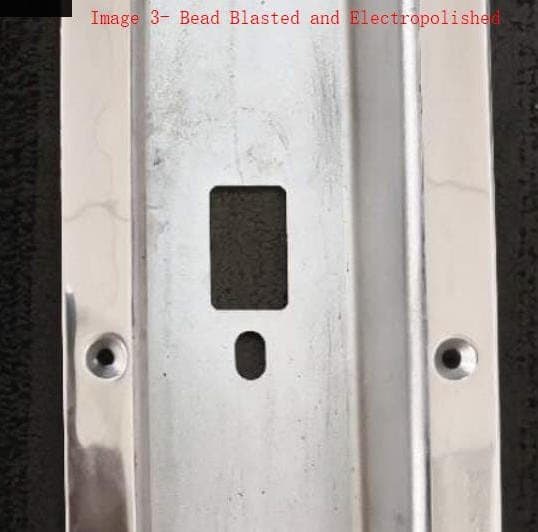
A. Hi Jayavel. The oldest and most conventional solution is perhaps phosphoric-sulfuric acid, originally Battelle U.S. Patent 2,334,698 from 1938: Bath 1 is 63% phosphoric, 15% sulfuric, 22% water. There are many other formulations, including proprietaries which overcome the weaknesses of this solution, but there is no "best" without your weighted list of what parameters you want the "best" to most closely match.
You probably know this, but there will be a lot involved in successful electropolishing of water bottles besides choosing an electrolyte.
Luck & Regards,
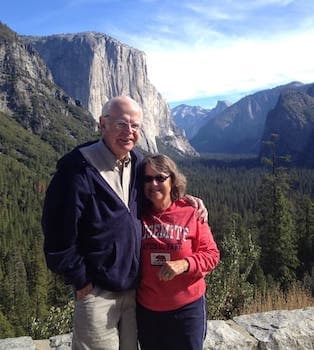
Ted Mooney, P.E. RET
Striving to live Aloha
(Ted can offer longterm or instant help)
finishing.com - Pine Beach, New Jersey
⇩ Related postings, oldest first ⇩
Q. How do I Electropolish SS304?
V.LakshminarayananLakshminarayanan, India
2003
and Chemical Polishing
of Metals in
Research and Industry"
by W.J. Tegart
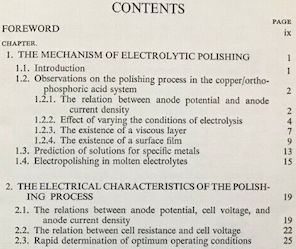
on eBay or Amazon
or AbeBooks
(affil link)
A. Hi, V. Electropolishing is an electrolytic procedure which operates with the opposite polarity of electroplating to smooth and brighten stainless steel by taking advantage of the fact that any high points (asperities) experience the highest current density and can consequently be preferentially dissolved into the solution. Some dairy & pharmaceutical folks, boating accessory suppliers, etc., feel that electropolished stainless steel is the only acceptable material for some applications.
Practically speaking, however, many variables are involved ... and etching rather than polishing will occur unless everything is right: correct solution, proper current density, no excessive water in the solution, etc., etc. The Electroplating Engineering Handbook ⇦ this on
eBay,
AbeBooks, or
Amazon [affil link]
has a 21-page chapter which is a great summary of those things, but it's is hard to further summarize it, or condense it all into a public forum response.
Many of the "must-have" textbooks, including The Metal Finishing Guidebook, and ASM Metals Handbook Vol. 5 ⇦[this on
eBay ,
Amazon,
AbeBooks affil links]
can introduce you to it as well.
For deeper coverage there is a well-known book on the subject of electropolishing by W.J. Tegart ⇨
and another by P.V. Shchigolev.
In the days before Powerpoint, AESF had a great Illustrated Lecture / Slideshow about it; one of your friends in the plating industry may have a copy. Please get back to us with any questions you may have. Thanks.
Regards,
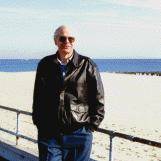
Ted Mooney, P.E.
Striving to live Aloha
(Ted can offer longterm or instant help)
finishing.com - Pine Beach, New Jersey
A. SS304 is one of the easiest stainless steels to electropolish. There are numerous commercial electrolytes around that will do an excellent job. They are generally based on phosphoric acid, usually with sulfuric acid. It can also be done with a citric acid based system. Talk to your chemical supplier.
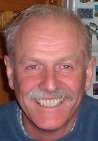
Trevor Crichton
R&D practical scientist
Chesham, Bucks, UK
Q. Dear Sirs,
Kindly let us know the basic chemicals composition of the S.S Electropolishing bath, its density, working temperature and current density required for efficient results.
Thanking you,
Kirti Parekh- Secunderabad, India
2003
A. The basic chemicals are sulfuric acid and ortho-phosphoric acid. However, there are many additives that will improve the performance of the bath. It would be foolhardy to specify these operational details without knowing what is available. I suggest you consult the references that Ted gave above and decide what you can obtain. Then follow the instructions in the references.
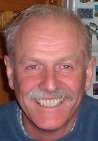
Trevor Crichton
R&D practical scientist
Chesham, Bucks, UK
Q. What is bath composition for electropolishing of SS304. What is the process of doing electropolishing.
G.Santhakumar- India
2003
A. Hello G.,
We appended your inquiry to a question which answers it. Hopefully this will get you started, and you will come back with any specific difficulties. Good luck!
Regards,
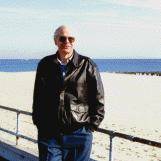
Ted Mooney, P.E.
Striving to live Aloha
(Ted can offer longterm or instant help)
finishing.com - Pine Beach, New Jersey
Multiple threads merged: please forgive chronology errors and repetition 🙂
Q. I happened onto this site today while trying to find information regarding the finishing of 304 ss. I manufacture a piece of equipment that is used in meat processing. We manufacture an average of 30 units per year. Made of 304 ss mill finish, 7 ga. and 10 ga. sheet, 14 ga. tubing, 1/4"plate. The basic footprint is 5' long, 4' tall and 2' wide. I had inquired about having the frame (welded complete) electropolished. I have a source with a tank sufficient to submerge the entire machine but I was told that the finish would not be uniform because of the bends, angles and shape. It was suggested that welded and non-welded sub-components be electropolished and then final assembly welded. It was recommended that a gel(?) be used to clean those welds. It seems to me that it would defeat part of the purpose of electropolishing and that is to have a uniform shiny/clean appearance. My objective is to find a finishing/polishing process that seals the pores of the material the way electropolishing would, is economical, not entirely labor intensive and suitable for food contact and can withstand a harsh cleaning environment. Plating or surface coating is not an option.
I hope this is sufficient information to form a conclusion. Thanks in advance.
Judy Godfreymetal fabrication,food processing equipment - Canton, Georgia, USA
2004
A. Hi Judy. Electropolishing will only occurs at sufficient current density and with good agitation to constantly deliver fresh solution. Without it you'll get etching rather than polishing, so your source is correct that simply dropping a complex item with I.D.s, etc., into an electropolishing tank will not work.
I believe you need an electropolishing shop with large enough tanks and the time to give attention to the jigging of this part with auxiliary cathodes, special agitation, and whatever else is required to electropolish it despite its peculiarities.
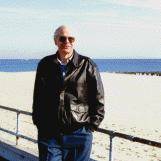
Ted Mooney, P.E.
Striving to live Aloha
(Ted can offer longterm or instant help)
finishing.com - Pine Beach, New Jersey
A. Large electropolishing tanks can handle your size part. Ted is correct in saying that proper cathoding can produce a uniform appearance on a complex shaped part.
Dan Weaver- Toccoa, Georgia
A. The simplest and easiest way is to get it electropolished by someone who knows what he is doing. If that is not possible, there is one other way that is not very labor intensive and will give you what you need. You can rig an electric wand using the right chemistry and equipment with enough power to give you the speed you need. This is being done quite effectively to welds by a number of companies.
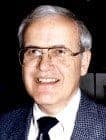

Lee Kremer
Stellar Solutions, Inc.

McHenry, Illinois
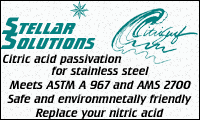
Multiple threads merged: please forgive chronology errors and repetition 🙂
Q. I am a student doing a project on electropolishing Stainless Steel grade 304. I would like to know
1) what is the best electrode for the cathode,
2) best electrolyte
3) temperature of the bath (electrolyte), voltage and DC supply
Thank you
School - Singapore
2007
9th Edition, Vol. 5
"Surface Cleaning, Finishing & Coating"
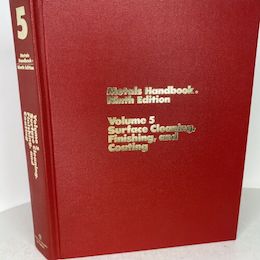
on eBay or Amazon
or AbeBooks
(affil link)
A. I am not sure that there is ever a "best", Azimah, but the Electroplating Engineering Handbook ⇦ this on
eBay,
AbeBooks, or
Amazon [affil link]
has an excellent chapter on electropolishing! If your school and town lack that book, the subject is also covered in the Metal Finishing Guidebook and ASM Metals Handbook, Vol. 5, Surface Engineering ⇨
Consulting these accepted sources, and having real information available, will probably prove to be a better way to do student research than to rely on a claim from a stranger on the internet what are the best best electrodes, electrolyte, temperature and DC supply. Good luck.
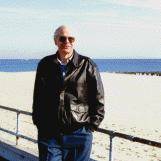
Ted Mooney, P.E.
Striving to live Aloha
(Ted can offer longterm or instant help)
finishing.com - Pine Beach, New Jersey
Q. I'm hoping someone can give me some insight, for I am at a loss. We are electropolishing 304SS and we just started getting corrosion on the parts. These are parts that we have done for years, using the same process. The parts are stamped, cleaned in CIP 100, rinsed 2x, partially electropolished (meaning only a section of the part is EP'd), rinsed 2x and then hot rinsed. We changed out the baths and the rinse tanks and we're still having this issue. The EP rinse baths are part of a closed loop filtration system that go through carbon and mixed bed tanks. We use DI water. We thought maybe the EP rinse water was too acidic, but even after the change out, we're still having this issue. Any thoughts or input is certainly welcome.
Thank you
-Dana
- Freeport, Pennsylvania, USA
May 8, 2013
A. Dana,
adv.
If you switch to the Universal Electrolyte (the one I supply to you for 420 stainless steel electropolishing), then there will be no rusting areas. 304 steel polishes well in this electrolyte (but in different regimes). I am in town right now and can deliver electrolyte if you need.
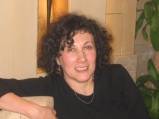
Anna Berkovich
Russamer Lab

Pittsburgh, Pennsylvania
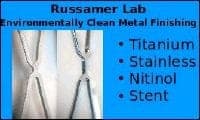
A. It's funny, one stain is above the EP line, meaning this part did not enter your electrolyte ... still you are in no doubt, that your process is to blame?
To make sure the problem is in your polishing line, try to take some parts, degrease those parts and leave the parts to dry, see if they get stains also.
- Aalborg, Denmark
A. If one uses conventional electropolishing solution, fumes from the electrolyte can contact the metal surface above the electrolyte level surface and impact the metal above the polishing line. Do not forget that the whole metal part is under current.
adv.
Our electrolyte does not have this problem. That is why we successfully use it for partial polishing or for reel-to reel continuous electropolishing, when wire or tape or conveyor exit the electrolyte tank while under electrical current, and enter the rinsing tank.
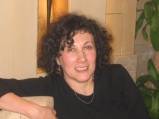
Anna Berkovich
Russamer Lab

Pittsburgh, Pennsylvania
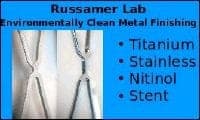
A. You've got a point, but conventional electrolyte consists of sulfuric and phosphoric acid; neither tend to evaporate at normal operation temperature, but splashes from hydrogen bubbles might be an opportunity. Still, my first shot would be would look for iron contamination of the work piece.
Bo Koenig- Aalborg Denmark
Thank you, everyone, for your responses. I actually was able to find the problem. We run these parts through CIP 100 w/ an ultrasonic, and somehow the sweep on the ultrasonic got moved from its standard position and the parts weren't being cleaned properly. We had to scrap out a bunch of parts, but at least we found the problem and got it resolved.
- Freeport, Pennsylvania, USA
Q. I'm researching non-toxic replacements for corrosive acids for electropolishing solutions.
Can you tell me what problems are commonly associated with electropolishing solutions and the electropolishing process?
I'm focusing on stuff like contamination of metal surfaces with acids from the bath, minor & major imperfections caused by acid ingredients. Please tell where I can get info also.
nanobiotech - Woodbury, New York, USA
July 28, 2013
A. Hi Neil. Is the objective to buy and use them or to formulate them? What substrate do you wish to electropolish -- stainless steel? Unfortunately I think that some of our understanding of electropolishing is empirical, and our successes are not really based on deep understanding of first principles theory :-)
Regards,
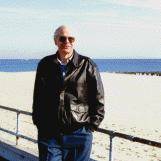
Ted Mooney, P.E.
Striving to live Aloha
(Ted can offer longterm or instant help)
finishing.com - Pine Beach, New Jersey
Q. Hi everyone. Thanks for all the great info from this community; I'm having a crash course and cramming hard to try and pass through the eye of needle with a current situation we are experiencing.
Part:
Material: SS304
MFG: Cast
Parts size: 40 cm x 18 cm x 12 cm
The required finish is for the pocket (visible surface) to be cosmetic electropolished (clean, shiny and consistent)
1st try -- the part was, the supplier said, tumbled and then electropolished it; I was to see the EP step.
Results- it looks as if the part is oxidizing/rusting
The 2nd attempt --
The caster bead blasted the parts with SS beads which looked good when they came out of the machine. I then said we need to clean it as it had dust on it from the bead/shot blast. So we cleaned it with hot water (it looked better 2 days ago when we cleaned it with water but it started to oxidize within 10-20 min; now 2 days later it looks like this)
The other part was bead blasted, same batch as previous part, and Electropolished. The part looks 100 times better after bead blasting and then electropolishing, however the electropolish is not consistent on the floor of the part; we are adding a permanent gating to the mold to eliminate the non-surface treatment issues.
Conclusion: the shot blasted part then EP, came out much better.
So my question is: Is it possible to get (cosmetic finish): consistent, shiny polish inside here? If So any recommendations would be great. I was thinking to an extra cathode might help and make sure the part is facing it (front and back side). 2nd after shot blasting does the part need to be cleaned? If yes with what?
Thanks for any tips if anyone has any.
Scott.
Project - fort pierce, Florida, USA
July 23, 2018
A. My post above about electro-polishing the inside of the my cast part was resolved by adding a Cathode inside the cavity.
scott stefan [returning]- fort pierce, Florida
December 13, 2018
Q, A, or Comment on THIS thread -or- Start a NEW Thread