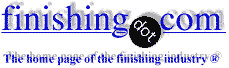
-----
Current question and answers:
Q. We are trying to achieve chrome look in various metals here in Moradabad for one of our USA-based buyers who was purchasing goods from China so far ... but issue is that chrome plating is banned by local government. We have tried multiple ways to get that chrome look but nothing is coming close. Can anyone suggest a way to get the chrome look without going for chrome plating?
So far we have tried bright nickel, shiny polish, tin plating.
- Moradabad India
December 24, 2020
A. Hi Rahul. We have attached your inquiry to a long thread discussing the many alternatives. But make sure you very clearly tell your customers that what you are providing is not chrome plating ... not only because a perfect match may not be possible, or the corrosion resistance may not be equal, but because you cannot read the designer's mind and know why chrome plating was specified.
You can certainly suggest alternatives, but the essential step is for the specifier to change the specification, never for a supplier to decide that what they are offering is 'equal' :-)
Luck & Regards,
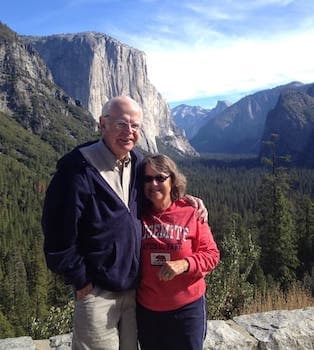
Ted Mooney, P.E. RET
Striving to live Aloha
(Ted can offer longterm or instant help)
finishing.com - Pine Beach, New Jersey
December 2020
⇩ Related postings, oldest first ⇩
Q. With forthcoming European Regulation for Hazardous Materials, Chromium & Chrome plating will be prohibited in Automobile Application. We use Chrome Plating for Company Logo fixed on Cars. What could be the alternative to Chrome Plating to give same performance at approximately same cost ?
Zafar Shaikh- Pune, Maharashtra, India
2003
A. I don't think that's true, Mr. Shaikh, although you may know something that I don't.
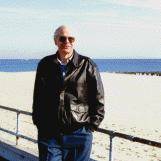
Ted Mooney, P.E.
Striving to live Aloha
(Ted can offer longterm or instant help)
finishing.com - Pine Beach, New Jersey
2003
A. What's banned is hexavalent chrome, not chromium metal. Chromium metal is not banned.
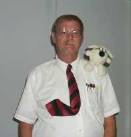
James Totter, CEF
- Tallahassee, Florida
2003
Q. My company is in the business of custom street rod and restoration. We are interested in learning more about chrome plating alternatives for decorative reasons over metal and plastics. Any information you can supply will be greatly appreciated.
Tommy G [surname deleted for privacy by Editor]custom automotive - Hayden, Alabama
2003
A. Hi Tommy. It's but difficult to respond to such a broad question. There are at least a dozen books just about chrome plating, and there are indeed numerous possible alternatives, some suitable for certain applications but not for others. Alternatives range from vapor deposition of aluminum with an organic topcoat (which was used on interior plastic parts almost 50 years ago), to sputtering (which was used on some GM cars 3 decades ago), to trivalent chromium replacement for hex chrome, to cobalt replacements for hex chrome, to imitation chrome spray coatings ("chrome-look" paint), to electrolytic lacquers.
Chrome plating is the standard, used almost universally by OEMs. Why do you want to replace it, and in what applications (interior, exterior, tiny parts, bumpers)? Thanks.
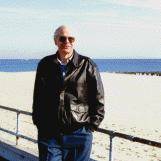
Ted Mooney, P.E.
Striving to live Aloha
(Ted can offer longterm or instant help)
finishing.com - Pine Beach, New Jersey
2003
Q. I am sorry for my previous question being so broad. Let me see if I can give you some specifics as to what I am inquiring about. I would like to do decorative chrome plating on nonconductive and non-metallic surfaces. I would like to be able to plate over epoxy, polyester, fiberglass, gel coats, urethanes, etc. Is this possible? and Is it possible to do different colors of chromes such as red, green, or purple, similar to a decorative Christmas ball?
Tommy G [surname deleted for privacy by Editor]Automotive restoration - Hayden, Alabama
2003
A. Virtually anything at all, from a rock to an orchid, can be electroplated, Tommy. The main issue is whether the finish is durable enough and exhibits sufficient adhesion to meet your needs in a specific situation. Most exterior automotive brightwork is nickel-chrome plating on ABS plastic. ABS has the special advantage that it can be etched to develop a very good "tooth" for the plating.
If you are speaking of soft substrates, you also need to recognize that nickel and chrome are hard metals, and are brittle, and will therefore generally crack like your decorative Christmas ball if plated onto a flexible substrate. Chrome plating at all is a difficult multi-step process (please see our Intro to Chrome Plating). Trying to do it on a variety of challenging substrates is a task for a specialty shop with many years of experience.
Chrome is metallic; it is never red, green, or purple. A translucent organic tint can sometimes be successfully electrophoretically applied on top of metallic surfaces, but there are adhesion and durability issues there as well.
What you may be looking for is proprietary organic "chrome-look paint" coatings offered by a number of suppliers including G.J. Nikolas [a finishing.com supporting advertiser] and Gold Touch [a finishing.com supporting advertiser]. These are specialty paints, that can be any color, with very tiny reflective flakes and/or a silver nitrate mirror formulation that flow to form a highly reflective surface. Good luck.
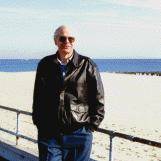
Ted Mooney, P.E.
Striving to live Aloha
(Ted can offer longterm or instant help)
finishing.com - Pine Beach, New Jersey
2003
Multiple threads merged: please forgive chronology errors and repetition 🙂
Q. Hi-
I own a small family business in Athens which is involved in nickel/chrome plating through electrolysis. I have noticed several items in the market like motorcycle exhausts, chairs, which have high quality nickel/chrome plating which cannot be achieved through electrolysis (at least by the process, chemicals, etc. I'm currently using) and was wondering if there is another method, more cost effective, with high quality results and environment-friendly out there. I greatly appreciate any feedback.
- Athens, Greece
2004
A. There are alternatives, but when it comes to quality of appearance, nickel-chrome plating is the standard that the alternatives are trying to match. If you are doing nickel-chrome plating and it is less beautiful than something else you have seen, it is because you are not doing the nickel-chrome (or the prep work associated with it) right.
There are alternatives that are cost effective, and there are alternatives that are more environmentally friendly, but none that look or perform quite as good, let alone better.
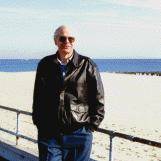
Ted Mooney, P.E.
Striving to live Aloha
(Ted can offer longterm or instant help)
finishing.com - Pine Beach, New Jersey
2004
Q. Ted thank you very much for your response. I understand that chrome plating has the best appearance which is very hard to meet. I'm looking for an alternative which has a good appearance but that is cost effective and most importantly environmentally friendly. So actually I'm not looking for the 'best' quality but for a good quality which is also a low cost investment. Since I'm primarily concerned with Decorative items and most importantly the automotive industry, what alternative methods are there for me? I greatly appreciate your feedback and looking forward for your response.
Sincerely yours,
Electroplating - Athens, Greece
2004
A. There are proprietary alternatives to the traditional chrome plating layer, such as trivalent chromium and tin-cobalt. Any of the major suppliers of plating processes can introduce you to their proprietary alternatives. These should be satisfactory for automotive industry use, while moving you away from the use of hexavalent chromium, but you would still be doing nickel plating.
Tremendous progress has been made in the last few years on the "chrome-look" paints and "chrome-look" PVD processes. Chrome-look stuff of OEM quality is now routinely applied to wheels and some other items by many of the major automobile manufacturers ... but real chrome plating is still what is done for the brightwork.
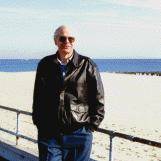
Ted Mooney, P.E.
Striving to live Aloha
(Ted can offer longterm or instant help)
finishing.com - Pine Beach, New Jersey
2004
Q. Ted again thank you very much for your input. I'm currently researching the organic coatings you mentioned and stumbled onto another process called Vacuum Metallizing. Do you think this is appropriate for chroming car wheels? Do you know how expensive this can be? I have been looking into PVD which uses vacuum technology and thought that Vacuum Metallizing is similar. However, I have the impression that the cost of equipment for Vacuum Metallizing is A LOT lower than that for PVD equipment so I gather that this is a totally different method. Is this true? How does Vacuum metallizing compare to organic coatings? I greatly appreciate your feedback! Kind regards,
Angeliki Skafida [returning]Chromio - Greece
2004
A. PVD is an acronym for Physical Vapor Deposition. Usually when people talk about vacuum metallizing they are trying to restrict themselves to mean the one type of PVD that evaporates a thin film of aluminum onto the substrate, and without using any voltage to accelerate the plasma to bombard the substrate to cause an impact for better adhesion. So a vacuum metallizing machine can be less expensive than other PVD chambers.
The thin film of aluminum cannot be left exposed, so it is covered with a thin, specially designed, clear organic topcoat. This is indeed a cheap coating that is used on model cars rather than real cars, although some automobiles used it on interior plastic parts in the 1960s, which made them age as gracefully as a child's toy ring from a gumball machine.
There are much higher quality PVD deposits, some of which require organic topcoats and some of which don't. My knowledge of them is pretty much only book knowledge, but some of our readers like Jim Treglio would have the expertise to be able to further assist you.
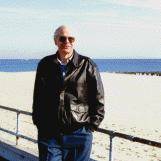
Ted Mooney, P.E.
Striving to live Aloha
(Ted can offer longterm or instant help)
finishing.com - Pine Beach, New Jersey
2004
Shops which offer chrome plate alternatives?
Q. We are a swiss lathe turning job shop. We outsource all plating. We currently have several customers who will not allow us to utilize TRUE chrome for their components. We have since found a house to do a chrome alternative plate that gives all the qualities of TRUE chrome. The problem is their leadtime is much longer than my customers are willing to allow. Do you know of any other plater doing this type of chrome alternative plate?
Dean Palladino- Waterbury, Connecticut, USA
2004
Ed. note: This RFQ is outdated, but technical replies are welcome, and readers are encouraged to post their own RFQs. But no public commercial suggestions please ( huh? why?).
A. Silver offers SOME of the qualities of gold, plastic offers SOME of the qualities of wood, and chrome alternatives offer SOME of the qualities of chrome. Nothing offers ALL of the properties of something else or it would be that other thing instead of itself :-)
You are probably speaking about decorative chrome rather than hard chrome, Dean, and one of the alternative coatings that offers a lot of the properties of a chrome topcoat over nickel is a proprietary tin-cobalt plating process offered by the major plating process suppliers. I'm sure that there are a number of shops who offer this, including some of finishing.com's supporting advertisers who will contact you in private.
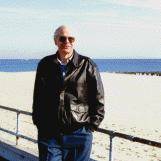
Ted Mooney, P.E.
Striving to live Aloha
(Ted can offer longterm or instant help)
finishing.com - Pine Beach, New Jersey
2004
Chrome-look paint
Q. On a TLC program 4/19/05 Rides XXX they showed a flexible chrome plating on soft plastic. Any one know more info?
R. Dawdy- Pauls Valley, Oklahoma, United States
2005
A. Hi R. It certainly wasn't chrome plating but, sorry, I don't know which brand of "chrome-look" paint it was.
Regards,
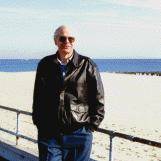
Ted Mooney, P.E.
Striving to live Aloha
(Ted can offer longterm or instant help)
finishing.com - Pine Beach, New Jersey
2005
A. The "rides" company is Alsa Mirrachrome.
Steve A [surname deleted for privacy by Editor]- Amsterdam, New York
20052005
2007
Q. I am a quality technician in South Wales in the UK. I have been tasked with finding an alternative to Hexavalent chromium in order for my company to become RoHS compliant. I have done research into the various alternatives, however, the criteria required is stated below:
i) Conductivity
ii) Salt Corrosion Resistance (500 hours Ideally)
iii) Wear resistance
iv) Colour - Green & Black Ideally
I would appreciate it very much if you were to provide some suggestions for alternative plating methods to Hexavalent chrome.
Best Regards
Mr Ceri Rhys Thomas (BSc)
Quality Technician
South Wales
Quality Technician in a plating shop - South Wales, UK
? Ceri,
Green and black chromium?! What do you mean?
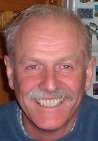
Trevor Crichton
R&D practical scientist
Chesham, Bucks, UK
2007
A. I think Ceri is referring to green and black chromate conversion coatings (perhaps on zinc). Hopefully he'll get back to us.
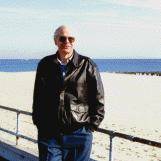
Ted Mooney, P.E.
Striving to live Aloha
(Ted can offer longterm or instant help)
finishing.com - Pine Beach, New Jersey
2007
A. I presume you are talking about conversion coatings on zinc plate. The finishes you are referring to are the most difficult to find trivalent replacements for. The black is available although every product on the market has some shortcomings in corrosion resistance, bath life, ease of use or cost. The green (I presume this to mean olive drab) has not to my knowledge been able to be formulated as a trivalent material except as a dye color for other chromates. The vast majority of parts processed for this finish must meet military or government specs (in the U.S.) and for this finish no trivalent product is on the QPL (qualified products list).
Gene Packmanprocess supplier - Great Neck, New York
2007
A. Certainly know of black chrome. It can only really be used for decorative purposes, has little wear or corrosion resistance and has an even poorer throw than conventional chromes.
Must admit that I have never heard of green chrome though.
Aerospace - Yeovil, Somerset, UK
2007
2007
Q. Thank you very much for your responses to my inquiry.
I apologise for the vague inquiry but Ted was correct to assume that I do not have an in-depth knowledge of plating.
With regards to Black & Green, it is not chromate, but the paint specifications that must adhere to our connectors.
The connectors are to be used in harsh environments including the military & traction industries.
I apologise once again for the little information I am able to provide. Any information will be gratefully accepted.
Many Thanks,
Connectors - South Wales, UK
A. Ceri,
So now we need to know what the substrate you want the paint to stick to. Do you want it to stick to hard chrome? If it is I would suggest an etch primer to start with, followed by an epoxy primer and then probably a polyurethane topcoat.
Do you need paint specifications? If so, do you want US military specifications or UK defense specifications or even BS/ISO specifications?
Give us a prod in the right direction and I'm sure that we will be able to find a suitable answer for you.
Aerospace - Yeovil, Somerset, UK
2007
January 9, 2008
Q. Hi all,
The base material that we require the coatings to adhere to is 20/11 aluminium alloy. We require a RoHS compliant plating method such as electroless nickel for example to plate the aluminium shells.
could you suggest any RoHS compliant plating methods?
With regards to the use of primers, would this decrease the electrical conductivity of the aluminium alloy shell?
I Have been investigating Alodine, but I have not been able to get in contact with anyone who knows this method in great detail.
Many thanks for your responses and I hope to hear from you soon.
Best regards,
- South Wales, UK
A. Ceri,
Assuming you want electrical continuity then electroless nickel is the way to go. Note that there will be some slight drop off in performance due to surface pretreatment. You should talk to the chemical manufacturers such as Atotech if you want RoHS compliant coatings. They make them and will be better able to advise on their use.
There seems to be some confusion on the primer side of things though. Alodine is a conversion coating for Aluminium, not a primer. There are non-hexavalent chromium conversion coatings on the market. Again talk to the manufacturers such as Henkel.
Depending on how you apply the coating there may well be an increase in electrical resistance. If uncertain when calling up the coating you should either call up
MIL-C-5541 Class 3 or DEF STAN 03-18 for low electrical resistance.
If you mean paint primers, well that's another story altogether.
Aerospace - Yeovil, Somerset, UK
January 15, 2008
Hi all,
Thank you for your assistance, its very much appreciated. I have contacted Atotech as you suggested and I shall keep you informed.
Many thanks,
Connectors - South Wales, UK
A. Maybe you could choose MIL-A-8625 / MIL-PRF-8625
[⇦ this spec on DLA] Type III class 2 Black hard anodizing but leave the contact point area bare (by masking).
Doing so you could meet all of the requirements:
i) Conductivity
ii) Salt Corrosion Resistance (500 hours Ideally)
iii) Wear resistance
iv) Colour - Green & Black Ideally
- Singapore
Alternatives for Hexavalent Chromium plating: Sn-Co-Zn or Sn-Co-Zn-Ti
Q. Within my company we have already for long pursued the ban on Hexavalent Chrome in the processing for our decorative plated components and switched to Trivalent Cr. Recently I came across a plater who claimed to have the perfect alternative for the 'shiny' Hexavalent Cr plating. He described a process using Sn-Co-Zn or Sn-Co-Zn-Ti. The second one should have better color stability at higher temperatures.
The issues I have with this is the following:
- Is there someone here who can share some experience with this type of plating. Is it really a valid alternative? We require color stability up to 180 °C, similar color as Hexa Cr and 5% salt spray resistance of 48 hours.
- In a final step, the plated part is passivated, but I hear from other sources that in this passivation step there is again use of Hexa Cr, is this correct?
- Are there other valid alternatives in the sense of appearance compared to Hexa Cr. We require color stability up to 180 °C, similar color as Hexa Cr and 5% salt spray resistance of 48 hours.
Supplier Quality Manager - China
November 30, 2009
Q. Hello, I'm restoring a 1969 Cougar Xr7. A lot of the chrome is heavily pitted, with areas on the underside of the bumper actually flaking. After reading several of your discussion threads, I'm no longer convinced that I can save money rechroming it myself. I don't have a big budget. Could I get a nice, durable finish with a "chrome" paint or other imitation product?
Michelle Schneiter NerdinCar restorer - Sherman Oaks, California, USA
August 27, 20162005
Nickel/Cobalt plating as alternative to Nickel/Hexavalent Chrome
Q. Good after noon folks, I wonder if it's acceptable (color wise) to completely replace Hexavalent Chromium with electrolytic Cobalt for decorative finishes.
Instead of the usual Triple Chrome system: Copper/Nickel/Chrome, I could use Copper/Bight Nickel and finished with a fast and simple Cobalt strike.
I am aware that I could just replace the bright nickel step with bright cobalt, but nickel makes way more sense because it's less expensive and tried and tested (and what I currently have), cobalt would be there just for the color, unless cobalt could be replaced with simple chromium sulphate/chloride strike?
- Managua, Nicaragua
November 16, 2016
Q. I would like to hear your feedback on this, Bright Nickel Plating is a very popular and understood process, while Cobalt is rather expensive and not so common; would simple Watts cobalt plating bath setup be the best route to go about this?
Bright copper followed by a bright nickel plating and finished with a short (30 minutes at most) Watts cobalt coat for the final cosmetic coat.
- Managua, Nicaragua
November 18, 2016
A. Hi Marvin. Here in the USA no plating shop attempts to design their own decorative plating processes, so I have no relevant experience to enable me to make even a guess. But all of the major plating process suppliers have offered alternatives to hexavalent chrome, such as trivalent chromium plating, tin-cobalt, nickel-tungsten, and various other alloys. I think if you contact them, there will be food for thought.
As you know, though, it's not just about color. Chromium plating greatly improves the corrosion resistance of the underlying nickel plating. Topcoats have never been necessary with nickel-chrome plating, but perhaps you can get the color right with your cobalt alternative, and then topcoat with a silicate coating or an organic clearcoat. Good luck.
Regards,
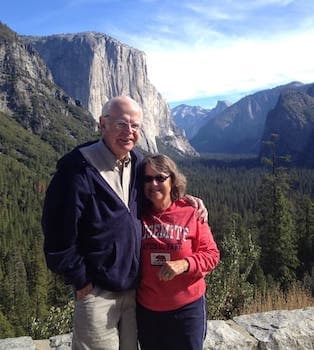
Ted Mooney, P.E. RET
Striving to live Aloha
(Ted can offer longterm or instant help)
finishing.com - Pine Beach, New Jersey
November 2016
![]() |
! I have been testing a flash coat (10 minutes at most) of Cobalt on top of copper/nickel plating for decorative purposes -- first because a Watts cobalt plating is a lot more expensive than a Watts nickel plating bath, cobalt looks almost as good a chrome and that is what I am needing at this moment. I really would like to get rid of chrome plating at least for decorative purposes. Marvin Sevilla- Managua, Nicaragua March 2, 2017 Q. What would be the future of the decorative chrome market with the government getting stickier with regulations on Chromium release, what are the alternatives used currently to replace hexavalent chromium plating and what would be the Impact of REACH on Chromium Plating market outside Europe? Molsri Goel- India March 2, 2017 A. Hi Molsri. Woody Allen once said that he took a speed-reading course and then read "War & Peace" in 15 minutes; when asked to summarize it, he said "It's about Russia". So it is when trying to summarize 'alternatives to chrome'. Millions upon millions of dollars have been spent on reports concerning alternatives to chrome plating but, in brief, alternative topcoats on top of the decorative nickel plating include trivalent chromium and various alloys, some of which are mentioned on this page; most plating suppliers offer one or more such alloys as proprietaries. Chrome-look paint is a possible alternative. Various vacuum metallizing approaches followed by a topcoat have been used. Sputtering has been used. In general, PVD coatings are taking over some areas like automobile wheels. To a certain extent, redesign is a replacement, e.g., auto headlights and tail lights rarely have chrome plated surrounds anymore, but the "shiny stuff" is sealed away from the environment behind clear plastic lenses so that vacuum metallizing can replace the chrome plating without the durability issues it would have if exposed to the environment. Regards, ![]() Ted Mooney, P.E. RET Striving to live Aloha (Ted can offer longterm or instant help) finishing.com - Pine Beach, New Jersey March 2017 |
A. I am working on a hybrid between PVD coating process and Electroless Cobalt, I am adapting the PVD basecoat/topcoat system with the Electroless cobalt/nickel metal deposition for wheels, ideally the basecoat/top coat would need to be a UV curing coat that provide a smooth and adherent base for the autocatalytic cobalt or nickel to be deposited without the need to use harmful etching chemicals, and the top coat would need to last for a many years of road abuse, so far the testing has been on a very small scale and automotive basecoat/clearcoat have been used instead (like spray on silver process), I am trying to get around the expensive Palladium activator too.
Marvin Sevilla- Managua, Nicaragua
March 8, 2017
Need alternative to decorative chrome plating
November 13, 2019Q. Hi
We are chandelier manufacturer team , and we want to start our electroplating process.
I have searched a lot about electroplating nickel and chrome , but I have found that chrome electroplating is strongly destroying environment and also may affect our worker's health
So
I have suggested our manager that we dont manage to have chrome electroplating process in the factory , but he says that nickel plated metal doesn't look like chrome and it is yellowish.
Anyway , my question is that:
1- can we add something to nickel electroplating solution that turns color, so it look like chrome?
2-Is that safe process to electroplate chrome?
3- and if both are answered as No , can we do something to make normal chrome electroplating more safe?
4- and is there any alternative that makes shiny reflective finish like chrome plated finish?
Chandelier Manufacturing - mashhad , North Khurasan
A. Hi Ali. As you see from the previous postings on this thread, you are asking lots of questions which cannot be thoroughly dispatched in a simple response in a forum, but I can give it a start:
1. No, you can't make nickel look like chrome because all non-precious metals tarnish, and the tarnish on nickel is yellowish.
2. "Safe" is relative. Trivalent chromium plating is probably, per your definition and concerns, "safer" than traditional hexavalent chrome plating.
3. Chrome plating can be way way safer than lots of things medical personnel are exposed to. But handling the air emissions and rinsewater from chrome plating, preventing human exposure, and being certain there are no leaks under any conditions is not an easy thing to do.
4. Talk to local plating process suppliers about their proprietary alternatives to chrome. None are 100% the equal of chrome plating, but they can be very good.
Regards,
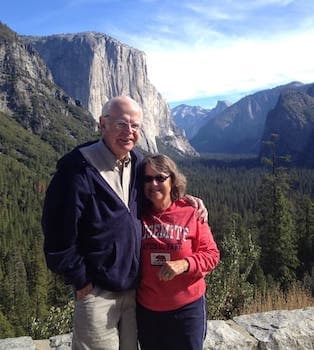
Ted Mooney, P.E. RET
Striving to live Aloha
(Ted can offer longterm or instant help)
finishing.com - Pine Beach, New Jersey
November 2019
Q. Hello Ted
Thanks for your great responses.
Unfortunately , electroplating suppliers here are not pro.
I have seen in your previous responses that Tin-Cobalt Electroplating looks like chrome plating, is there any comparison that compares their reflectivity, color, and IOR?
in your text I have seen that one beaker of chromic acid will pollute all wells around, I don't just like money! I like people and environment -- So that's why I try not to electroplate chrome in our factory.
Chandelier Manufacturing - mashhad, Khurasan, Iran
November 16, 2019
A. Hello again Ali. Any reader is welcome to respond, but I don't have the experience or knowledge to guide you through non-proprietary substitutes for chromium plating.
In the USA, the plating industry just doesn't work that way; rather, plating shops do production plating as a rule. They don't spend their time experimenting with different combinations of commodity chemicals; rather, the plating process suppliers do the research & development and market their processes to plating shop. I've heard about suppliers offering alternatives to hexavalent chromium; I know that the most popular is trivalent chromium, and that there are others, but I would have no clue how to formulate them, nor knowledge of their reflectivity, color, etc.
I would suggest searches on surfacequery.com, scholar.google.com, and patft.uspto.gov/netahtml/PTO/search-bool.html. Good luck.
Regards,
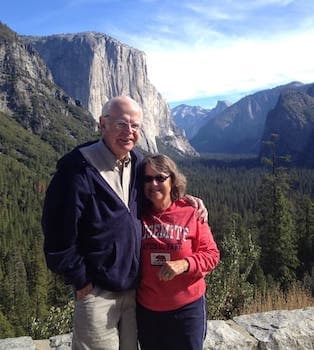
Ted Mooney, P.E. RET
Striving to live Aloha
(Ted can offer longterm or instant help)
finishing.com - Pine Beach, New Jersey
November 2019
November 24, 2019
Hello Ted
Thanks a lot.
I have found article on internet that says:
"Tin-cobalt alloy plating is at least equal to, or better than chromium plating in adhesion and tarnish test, while chromium plating is better than tin-cobalt alloy plating in corrosion resistance and abrasion test. "
The article is named :
"Tin-Cobalt Alloy Plating in a Pyrophosphate Bath
S.K. Cho1*, H.S. Han1, C.K. Lee1, C.I. Ahn2, J.I. Park2 1Yonsei Unversity, Shinchon, Seodaemun, Seoul, Korea, 120-749 2Agency for Technology and Standards, MOCIE, Kwacheon, Kyonggi-do, Korea, 427-010 "
It fully describes about tin-cobalt electroplating and it seems that this is good alternative for chromium plating.
I have also found a patent named "Bath for the electrodeposition of bright tin-cobalt" at united states , aug 21 , 1975 , that was helpful.
Chandelier Manufacturing - Mashhad , Khurasan , Iran
A. Hi again Ali. Glad that you seem to have found a solution. Depending on how high quality your chandeliers are, another alternative is rhodium plating. This is roughly as expensive as gold plating, but is a bright reflective finish that looks even brighter & better & more scintillating than chrome plating ... you've probably seen it on white gold engagement rings.
Regards,
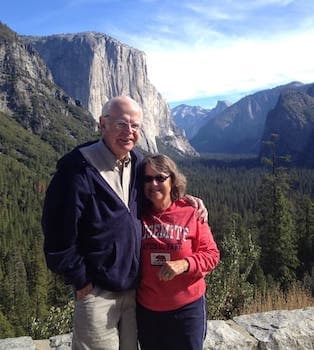
Ted Mooney, P.E. RET
Striving to live Aloha
(Ted can offer longterm or instant help)
finishing.com - Pine Beach, New Jersey
December 2019
Q, A, or Comment on THIS thread -or- Start a NEW Thread