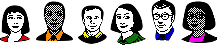
Metal finishing Q&As since 1989
-----
How to eliminate anodizing appearance variations
Hi,
I have been struggling a lot with my anodizing plant of late. The main issue I face is in the inconsistency of color coating on Aluminum products. As far as clear anodizing goes, I'm getting a consistent finish. But, when it comes to colored anodizing -- one batch of a particular product will today have a totally different color compared to another batch that I produce 2-3 weeks down the line. Please suggest what should i do to ensure consistent and uniform color coatings.
Plant Head - Anodizing - Ludhiana, India
August 5, 2021
A. Hi Vicky. Because this is a known problem to you, you should probably run coupons at the beginning and end of the run and maintain them on a sample board, and not run production until the coupon is right.
The problem could be material differences; or anodizing thickness; or dye temperature, concentration or time; or be related to sealing. But coupons will allow you to eliminate the first possibility, check on the second possibility, and move on to the dye and seal steps.
Luck & Regards,
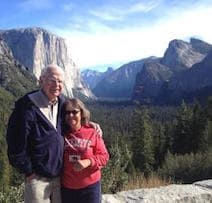
Ted Mooney, P.E. RET
Striving to live Aloha
finishing.com - Pine Beach, New Jersey
August 2021
⇩ Closely related postings, oldest first ⇩
Q. I work for a manufacturing company that is an end user of anodized aluminum extrusions. We are receiving a variation in commercial clear anodize finishes, from mill finish appearance to a uniform matted finish. Our anodizer states that the problem lies in the substrate. We are being told that the aluminum alloy will not etch to a matted appearance because of the material composition. The extruder has completed elementary metallurgical analysis on two samples from each end of the discrepant range. Laboratory analysis reports a slight difference in Cu content (.0004% to .0015%) but no other documentable differences in the alloying elements. Considering the etch pH and etching duration of aluminum alloys, what other conditions would cause this variation in finish? Thank you.
Dennis Sato- Stanton, California
1999
A. What grade of aluminum are you using, 606x?
Quite a coincidence, but I just began a consulting project for a client in a similar situation. They require, but do not yet get, a perfect match.
We are going to do some microscopic profile analysis to see if we can actually quantify in geometric terms what causes the difference in appearance. Sometimes such an approach works. However, sometimes it doesn't because no matter how hard you work, you can't see the forest when you're looking at the trees, and you can't see the trees when you look at the forest.
My first supposition, by the way, is the same as yours, i.e., that the etch time and activity is the biggest factor in the difference in appearance. I wouldn't attribute the activity solely to pH, however; temperature and dissolved aluminum concentration are surely very important.
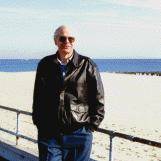
Ted Mooney, P.E.
Striving to live Aloha
finishing.com - Pine Beach, New Jersey
A. Ted is correct that the etch bath parameters are very important. The aluminum content in particular is very important in determining the matteness obtained from the etch bath. One of the problems with using reclamation units, at least when they were new technology, was that they would clean up an etch bath too well, that is, took ALL the aluminum out, leaving the etch bath almost useless in producing matte finishes. Vendors came to realize that at least 20 g/l aluminum were required in the bath. If the anodizer dumps periodically, it is a good idea to save 5-10% of the old bath, or process scrap metal in a new bath. I'm going to assume that the anodizer has his etch bath under control in making some other comments. The etch bath is one of the "lifeblood" baths of an anodizing shop, as the appearance of the final finish is usually highly dependent on a good etch. Having run a job shop for several years, a good part of my missing hair can be attributed to etching problems, especially when the cause of the problem ended up as something I couldn't control, such as metal composition. Etching technology has been around for quite awhile, and there are very few papers these days which discuss problems with etching. In the seventies there were several papers given on the effect of metal composition on the matte finish, particularly for the major extrusion alloy, 6063, which I would bet you are dealing with, Dennis. One paper I heard at an AES Conference, by E. C. Franz of ALCOA, helped to solve the exact same problem we were having at our job shop as you are experiencing. Mr. Franz showed that the matteness in etching 6063 alloy is highly dependent on the iron content. He also showed that with an iron content less than 0.2%, 6063 would not produce a matte finish, no matter how long it was etched. The 6063 specs. list the iron content of 6063 as 0.35% max, but the iron is an impurity, and if it is low, the manufacturer doesn't have to add iron to consider the alloy as In Spec. Incidentally, 6463 alloy, a modification of 6063, is the primary bright dipping extrusion alloy and bright dips to a much more specular finish than most species of 6063. However, 6463 will not etch to a matte finish. The main difference between 6063 and 6463? The iron content of 6463 is 0.15% max. Mr. Franz also showed that temper is important in achieving matteness. T6 etches better than T4. A good extrusion shop ages the extrusions to at least a T5 temper, which improves appearance. I don't know if you have any control over the alloy composition or not, but specifying an iron content of >.2% is the ultimate solution. An alkaline etch bath with fluorides will produce a more matte finish than straight caustic. I once had a large job of extruded electric switch boxes where we had to acid etch the parts to produce a matte finish, but that bath had fluorides in it and required special handling. Good luck!
Phil Johnson
- Madison Heights, Michigan
1999
! Wow, Phil. Thank you for the detailed and knowledgable reply. In my case we are dealing with 6005-T5 and/or 6061-T6 extrusions. Presumably we could stick to one or the other, or even have the spec changed to 6063 and >.2% iron because strength and mechanical properties aren't critical for this office decor application.
We're constructing a virtual wall from small pieces, so visual match must be the closest thing in the world to perfect, both for the clear and for the black parts. We had a strange result, even before we've started our instrument work: we took some photos of the extrusions with a digital camera, just for the record before shipping the parts off to the lab, expecting to be able to see no difference at all between the parts on 'film' since they were a very close match by eye. Strangely, they look far more divergent on camera than to the naked eye! I'm suspecting that this may have something to do with polarized light; now that we stumbled on it, we'll see if we can learn anything quantitative in the lab.
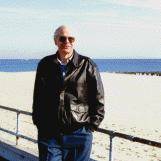
Ted Mooney, P.E.
Striving to live Aloha
finishing.com - Pine Beach, New Jersey
1999
How to avoid uneven aluminum bright dip
Q. I am using ortho phosphoric acid 85% for producing brightening finish on aluminum 6063 surface pre sand blast. I could not manage to get the polished surface even. My product finish appears to be dull and patchy. How to get the surface evenly polished.
Mohd. Zubir Othman- Prai, Penang, Malaysia
2001
? Maybe this is a silly question.. but you bright dip BEFORE sandblasting? Doesn't that defeat the purpose of the bright dip?
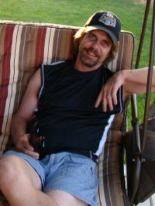
Marc Green
anodizer - Boise, Idaho
2001
Q. The bright dip process in actually done after the sandblasting process.
The actual process flow is Part machining to Sandblasting, using media aluminum oxide #80, to alkaline degreasing to caustic etching to acid desmutting to bright dip using H3PO4 85% + H2SO4 less than 5%, to anodising and complete.
The problem is that always after bright dip process the surface finishing become uneven and patchy.
How to determine free aluminum content in bright dip bath by NaOH titration method. What is the suitable indicator to use?
MOhd. Zubir Othman- Prai, Penang, Malaysia
2001
Q. Why does the surface of 6063 alloy after exiting the NaOH look black?
MOSTAFA ALIZADEH- SHIRAZ, IRAN
2002
A. Hi, Mostafa. It's because of the finely divided silicon and copper left behind when the aluminum dissolves out of the alloy.
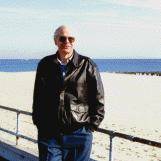
Ted Mooney, P.E.
Striving to live Aloha
finishing.com - Pine Beach, New Jersey
2002
Q. Will 6063 and 6005 look different when clear "Class 1 anodized" is ordered?
Mike Rubner- Dallas, Texas
May 22, 2012
A. I would imagine so. 6005 has a higher Silicon content. I don't know that I've come across any two differing alloys that anodize the exact same color (naturally), even if they belong to the same series. This is especially evident in the thinner coatings (you didn't mention the whether it was type 2 or type 3)
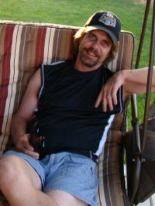
Marc Green
anodizer - Boise, Idaho
May 26, 2012
How to do Super Matte appearance on 6061 extrusions
Q. My team and I have opened up a line in Texas. We have been running material for a month or so now. We have caustic soda
[affil links]
etch and we run only 6061 extrusions. A couple of customers in the same industry have sent us samples to match which actually came from two different extruders/ anodizers. They look nothing like anything we have ever done and we are at a loss. They are soooo matte, hardly reflect light, and almost look like light grey primer or something and have no die lines ... None at all.
We thought it was an etch problem so we took a couple 5 gallon buckets mixed a perfect 8 oz/gallon etch solution and heated to 140 °F. We also got a Macdermid proprietary etch compound and did the same; the tolerance there is 2-16 oz per gallon so we did 5, 10, 15, and 16 oz/ gallon to test and heated to 140 °F. We can get all of the die lines out with a really long etch ... Like 15 minutes. But it has become clear that the extreme matte and color is not an etch issue.
Frankly, we are at a loss. I saw a very similar post on a "Double Anodize" thread and wonder if that can be the solution, but I don't know anything about double anodizing.
If anyone has any suggestions they would be greatly appreciated.
- Houston, Texas, usa
March 21, 2014
A. Hi Josh. It's hard to be sure what you are seeing from a verbal description, but is there any chance the sample parts are hard anodized? Have you, or can you, measure the anodizing thickness on those sample parts? Good luck.
Regards,
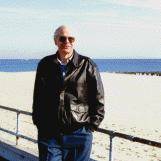
Ted Mooney, P.E.
Striving to live Aloha
finishing.com - Pine Beach, New Jersey
March 2014
![]() |
A. Josh, have you considered bead blasting before anodize? Like Ted mentioned, a picture of the coating you are trying to duplicate would be helpful. ![]() Marc Green anodizer - Boise, Idaho March 27, 2014 A. Josh - Colorado Springs, Colorado March 28, 2014 |
A. Like I've said before [Ed. note: thread 22139, "Satin Anodized Aluminum", for example], add sodium fluoride to the caustic soda [affil links] etch in increments of 1 then 2 then 3 avoir. oz/gal
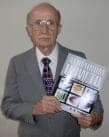
Robert H Probert
Robert H Probert Technical Services

Garner, North Carolina
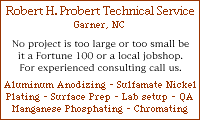
April 1, 2014
A. Bob Probert's correct. A little sodium fluoride will produce a more uniform, faster, and whiter etch.
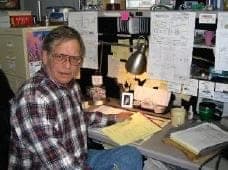
Jeffrey Holmes, CEF
Spartanburg, South Carolina
April 7, 2014
Aesthetic Problem in Anodizing 6063 T6 Profile Extrusion
Q. Can anyone tell me black patches / white patches seen after anodizing of 6063T6 profile extrusion can be avoided if alloy is changed to 6005T5 ?
- Pune, India
November 12, 2015
A. Tejes, it seems that this is the problem of extrusion and not because of anodise or alloy
Akash KadAluminium Anodiser - Uruli Kanchan, Pune, India
November 15, 2019
Bright dip solution for 6063 aluminum windows extrusion?
November 15, 2019Q. I am anodiser. currently I am using Nitric acid for deoxidation. But I could not achieve bright or mirror finish on extrusion sections.
Currently following:
1. Buffing by wheel made of jean clothes
2. degreasing by limestone powder, then rinse
3. nitric acid dip for 10 min
4. sulfuric acid anodising for 25 min, 14 volt
5. rinse
6. electrocoloring
7 rinse
8. sealing
- Pune, India
A. Hi Akash. It's possible that I am misunderstanding you, but nitric acid is a desmut-deoxidize step, it's not a "bright dip". So the first problem may be a misunderstanding whereby you think you are 'bright dipping' and you're not :-)
Search this site for "aluminum bright dip" and you will read that aluminum bright dips are generally very hot mixtures of phosphoric and nitric acid. There are also proprietary bright dips available such that you can get help on the issue if you don't want to try mixing your own.
But do not attempt to do bright dipping or even design a line for nitric-phosphoric bright dipping until you've seen a couple of installations. It is so aggressive that you need double walled 316L SS tanks, and conventional exhaust systems are not sufficient -- you need a "garage" style containment hood for the bright dip tank and its rinses.
Regards,
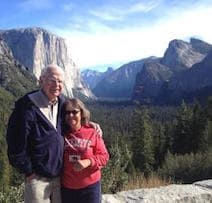
Ted Mooney, P.E. RET
Striving to live Aloha
finishing.com - Pine Beach, New Jersey
Color variations in machined aluminum castings
Q. Hi,
I work for a company performing machining on aluminum castings. We are having issues with substantial color variation of the material after machined parts are washed. Some castings have a bright, clear color, while others appear almost black. We are going to begin testing different variables in our process to see if we can figure out what is causing this, but I thought it would be worth it to ask what might be some primary root causes of this color variation.
Kraig
Aluminum Casting/Machining - Indianapolis, Indiana, USA
March 12, 2020
![]() |
A. "machined parts are washed". ![]() Robert H Probert Robert H Probert Technical Services ![]() Garner, North Carolina ![]() March 13, 2020 A. Hi Kraig, Aerospace - Yeovil, Somerset, UK March 13, 2020 ---- Ed. note: e-mail the pictures to mooney@finishing.com for posting here please. |
QC for a same manufacturer. I am getting random parts with a non-color match in clear anodizing. The parts are machined from the same billet of aluminum. I have tried 2 different anodizing vendors. Can this issue be caused by impurities in the aluminum? Wouldn't that result in an uneven finish? The finish is good, they were done in the same batch -- they are just different colors.
John Gahrmann- Charlotte North Carolina
February 8, 2021
A. 1. Inside of billet versus outside.
2. Work hardening by machining.
3. Inside/outside of an extrusion.
4. Agitation in the anodizing tank.
5. Position in the etch tank where gas evolution wipes different areas.
6. In Your case of two different anodizers: free acid, dissolved aluminum, current, temp.
7. dull machining versus sharp machining (read "work hardening").
8. Heat treatment.
The list gos on and on.
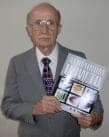
Robert H Probert
Robert H Probert Technical Services

Garner, North Carolina
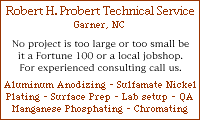

Q. So I see the picture didn't get attached. Let me clarify: 60xx series aluminum. 2 of the same part, made at the same time from the same billet on the same CNC. (our parts tend to be made in pairs) It has happened multiple times with two different vendors. but it isn't consistent. Out of 20 parts I will get 1-2 with a yellowish tint like they are 70xx series. the rest will be fine. Media blasting them and re-anodizing will not correct the issue.
John Gahrmann [returning]- Charlotte North Carolina
February 9, 2021
----
Ed. note: Hi John. The pic was on the main Public Forum page, so readers were seeing it, but it's here as well now. The "i" in your company name was missing from your e-mail address on both of your postings so mail o you was bouncing; better slow down a bit before it becomes muscle memory :-)
Q, A, or Comment on THIS thread -or- Start a NEW Thread