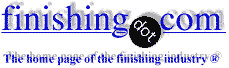
-----
Satin Anodized Aluminum

Q. I am a product design engineer working on a project for a very stringent customer. The project includes 6061 machined aluminum parts (~4 inch cubes) on which I need an "satin anodized" finish. This is a primarily cosmetic finish.
I've tried straight bead-blast then clear anodize, but got parts with a chalky appearance. I'm looking for something that has more depth & shine, but it still satin. The new Apple Powerbooks have the finish I am trying to mimic (if you've seen one!). My latest attempt included bead blasting, electropolishing, and clear anodizing. This finish is very close to what I want. A nice shiny, satiny surface. But... now I see some dark shadows in the finish (& they are sticky). I suspect the shadows are due to uneven bead blasting, but after looking through a lot of the posts here, I want to be sure. I'm on a tight deadline and want to cover all the bases. Any thoughts will be greatly appreciated! Also, any suggestions for finishing processes would be great. For the process described I've got to move the parts through 3 different shops, so no one is really accountable....
Thanks,
- San Francisco, California, USA
2003
A. The most popular method of getting satin finish in our industry is to alkaline etch in Sodium or Potassium Hydroxide with additives. Sodium Fluoride at about 1.5 oz/gal on top of about 6 oz/gal of Sodium Hydroxide at 140 F for 5 minutes should get close to what you want. Then experiment from there. Off line I can recommend proprietary mixtures for alkaline etching.
Be careful with the blasting. If the media has been used with any other metal then you will be pounding the contaminant into the soft aluminum. Also the work hardening caused by blasting will affect the uniformity of any subsequent chemical treatment.
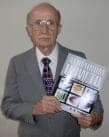
Robert H Probert
Robert H Probert Technical Services

Garner, North Carolina
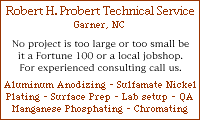
2003
Q. Hi,
My current situation with the finishing is quite similar, but the only difference is that the material we are using is Aluminum Alloy 2 series (copper), and we tried 4 kinds of finishing, most of which are not aesthetically pleasing.
E.g. Sand blasting gives a dull finish, cast finish also. SO far, only through machined surfaces have we seen acceptable results.
Is there something you can recommend to achieve a matte finishing for Al 2-series? Appreciate if you can help us.
Thanks
design - Singapore City, Singapore
June 28, 2010
May 3, 2012
Q. Hello.
This is the best forum I found so I decided to post my question here because it is very specific.
I have small pieces aluminum which need to be coated, more quality decorative but also corrosive protected suitable for minimum 5-10 years regular external use, I made them from 6082T6 aluminum rod; because they are small I prefer chemical only if possible.
The coating must be opaque, satin , grey to light grey;
also must be fine satin non-reflective, or shiny but coarse satin.
I keep several different made-in-China pieces from different manufacturers, all non conductive coatings where I can recognize one made with chromic acid anodizing, another etched with fluoride solution, but I prefer not to use dangerous fluoride acid, or any other too dangerous chemicals, I prefer to mix my own solutions suitable for room temperatures.
I made several tests:
-etching in caustic soda ⇦liquid caustic soda in bulk on
Amazon [affil link]
- crystal structure become visible, even before satin finish.
-etching in phosphoric acid - 15-30 min - fine satin, without any crystals visible.
-sulfuric acid anodizing - even fine satin etched always look like glass coated, too shiny and transparent.
-chromic acid anodizing - not very successful, the layer was too thin, semi-transparent. If I try again may look better but I read that chromic acid and dichromate are dangerous.
-boric-sulfuric anodizing - I'm not sure what I made but look like a soft transparent layer, non conductive, and still looks glass coated.
I read a lot on internet that some additives in the acid bath or in the boiling water may help but still no success, I hope someone can advise.
thanks
- Bulgaria
Q. I am an anodiser in India, struggling to get the white matte finishing on aluminium. I would like to know which chemicals are used in anodising starting from degreasing, etching, desmutting, anodising, electro colouring and sealing. Kindly help.
Mansukhjitsingh Walia- Mumbai, Maharashtra, India
May 19, 2012
Treatment &
Finishing of
Aluminium and
Its Alloys"
by Wernick, Pinner
& Sheasby
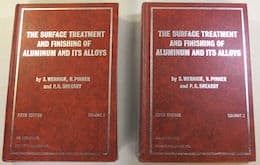
on eBay or Amazon
or AbeBooks
(affil link)
A. Hi, Mansukhjitsingh.
If you will detail your process and chemicals, I am confident that people will offer hints about what they think can be optimized but, sorry, considering everyone's preferences & prejudices at every step, and the 1001 "ifs, and, & buts" involved, it's not possible to do it in the other direction in this forum :-)
There are books available that completely detail the anodizing process though, one of which is 1279 pages.
So please describe exactly what you are doing and what problems you are having, and in what way the process is not yet where you want it. Can you tell us what alloy you are trying to get this finish on? Do you have any pictures of what you have achieved to date? Do you have pictures of what you are aiming for? If not, are you sure that the finish you envision is even possible (white anodizing is achieved with only limited success)? Thanks!
Regards,
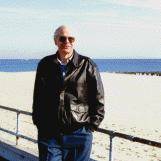
Ted Mooney, P.E.
Striving to live Aloha
(Ted is available for instant or longterm help)
finishing.com - Pine Beach, New Jersey
May 22, 2012
Q. Hello All,
Attached please find pics of one of our customer's jobs apparently 'clear anodized', according to their end customer. However, they claim that even scratches and machining marks get covered up due to the clear anodizing which seems to have a matte type appearance and whitish in shade, whereas our clear anodizing comes out as usual, glossy, and does not hide any machining blemishes.
Can anyone throw some light on any additional processes that we can carry out so that we can achieve the same finish? Does electrolytic cleaning (reverse polarity ) help? We have tried out some 'Satin Etches' in the past for some other jobs, but can't say for sure that such a finish was achieved -- would that be an option? I vaguely remember once, that a development sample which was repeatedly caustic etched for stripping and re-anodizing during trials had achieved a similar finish, but obviously it cannot be called a 'solution' :) ! Please suggest any options that may be worth trying out. Thanks in advance !
Ravi Rao- Belgaum, India
August 10, 2017
topics 2758 and 18655 are also similar.
A. If I were you I would try "shot blasting' process which gives more matte and satin finish. Also I think you won't see any scratches, machining marks ... it should be (of course) first shot blasting after etching (5-10 min.) before anodizing.
I hope you would try and share your results with us.
Good luck
- TURKEY,sakarya
September 30, 2017
Q. Hi Alaattin,
Thanks for your response! Wondering if the 'Shot Blasting' media that uses 'steel balls' might also cause 'Iron Contamination'? Another cause for worry is that the machined blocks that we usually get have drilled and tapped holes and various small holes. It had been observed in the past that these tend to get dented and damaged during shot blasting. The alternative to this - Sand Blasting OR Glass Bead blasting - is relatively 'gentler' but comes with the 'excess baggage' of 'Surface Silicon Contamination'...
Your thoughts on the above would be highly appreciated !
- Belgaum, India
October 3, 2017
A. Ravi,
There are other media options beside steel and glass. If you do some experiments and use the proper equipment and settings such as grit or shot size and shape, psi, appropriate nozzle and gun, and with some practice the results should be favorable. As long as you follow the OP's directions, contamination should be not a big problem but one to be aware of and screen for, especially in the beginning as the new or revised process is rolled out.
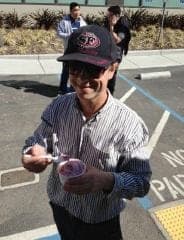
Blake Kneedler
Feather Hollow Eng. - Stockton, California
December 26, 2017
A. Hi Ravi,
I understand your worry but I don't suppose, as you say, iron contamination. The logic of shot blasting is that very small iron balls hits over profile and enhance it so a more matte surface occurs. It is not related to iron contamination. If I say about very small holes, actually I don't know -- may be harmful for those parts. But if I were you I would try somewhere who does toll manufacturing, then you can decide after that. Most important point in shot blasting issue, true iron ball are chosen. There are many special iron balls in the market but you must discuss with an expert who knows shot blasting issue.
Sincerely
- sakarya,TURKEY
December 31, 2017
April 4, 2018
To suggest two options for achieving the matte or frosty finish, and based upon experience (we have many customers that request 'satin mask' and also many who require 'blasted matte' finishes)...
1. A proprietary solution of stabilized Ammonium bifluoride, available through a respected North American plating chemical manufacturer, operated WITHOUT the optional addition of Nitric acid (pH remains around 5-5.5, keeping the HF concentration lower than it would be at higher acid content), works quite well. It does build up metallic contaminants which sludge out into a big mess at the bottom of the tank, and also slow down the reaction time. It needs to be run in plastic tanks. Filtration increases bath life but ya blow through filters like crazy! Decanting and manually desludging is an option. Also, because the titration for this cocktail is SO wildly inaccurate, and titration results and performance aren't as closely linked as one would like due to interference of metallic contaminants in an ageing tank, there's a bit of an art to maintaining it, and your line tech and lab person need to have frequent communication about performance and reaction time.
As much of a PITA as it is to maintain the tank, the results look very nice and give a bright frosty finish on TyII. It is also helpful to maintain the concentration to give a slow enough reaction that the operator can check progress and really finesse the degree of masking. Back in the day it used to be called 'clepo sat-n-mask' and there might still be an SDS or even TDS kicking around the internets somewhere if someone dug it outta the 70s and scanned it, lol... the formula was purchased and rebranded but should be easy enough to find out who sells it now. It's marketed as an 'acid etch salt'.
2. Aluminum Oxide blast media is your friend. And keep it clean, processing only Al in your blast system and preventing cross contamination. We have done some testing on various media developing a true matte-black hardcoat finish for military items with a lot of contours and sharp corners. The absolute worst was glass bead, and the winner was AlOx. With glass bead, no matter how we adjusted pressure/feed/pattern, there were issues with failure to accept dye evenly across all contours of the part, giving a burnt appearance even on parts that had absolutely NOT 'burnt' in the tanks, and components ended up a sickly, powdery, off-black. AlOx is more forgiving and when adjusted correctly, will not interfere even with processing dyed parts. And anyway, who REALLY wants to risk dragging more silicon through the line? *shudder
Just my two cents; I think satin masking is a fabulous and relatively low cost option for a shop that wants to add a new finish texture to their repertoire :)
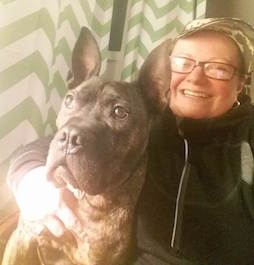
Rachel Mackintosh
lab rat - Greenfield, Vermont
Thank You Alattin Tuna, Blake Kneedler and Rachel Mackintosh for your suggestions and thoughts! Will try out and post results at the next opportunity.
- Belgaum,Karnataka, India
April 5, 2018
A. Hello Mr. Ravi. I am using shot blasting system from last many years. I was the first one in my area to introduce it. After a good trial & error we are able to master it. Shot blasting does hide a few scratches and machining blemishes to a certain extent. Using shots of steel with high nickel content will make surface satin. Shot blasting is a costly affair but it's better than controlling a chemical bath. Even pollution levels are low in shot blasting. For me pollution is very crucial. I can't pollute my surroundings for my personal interests. Finish is also consistent in shot blasting. So I can say no need to worry about contamination. It will easily give you the required finish.
Regards,
- Ahmednagar Maharashtra India
April 7, 2018
Q, A, or Comment on THIS thread -or- Start a NEW Thread