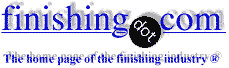
-----
Black Oxide versus Black Phosphate
Q. During my last navigation by internet I've found your web site and certainly it looks interesting. I'm trying to get technical advice about application of Black Oxide on some metallic components. On one of our products we use black phosphate as a rust retardant. But, rather than using black phosphate we could apply Black Oxide, will this last help to retard or avoid the rust, too?
Thanks in advance for your help
Regards
David M. Vazquez- El Paso, Texas
2001
A. David - Yes, black oxide can be used as a rust retardant, but it is not as effective as black phosphate. The black zinc phosphate acts sacrificially to protect the steel, whereas the black oxide will rely on the after-finish for corrosion protection. The decision should be based on how much protection you need - a good oil on black oxide can pass a 96 hour salt spray test.
Dan Brewerchemical process supplier - Gurnee, Illinois
2001
Q. I am interested in Black Phosphating:
1. How it is applied.
2. Chemicals used in the process
3. If paint is to be applied over it, what paint would be compatible with it.
Thanks
Jun
- Angeles City, Philippines
2006
Q. I would like please to understand the difference between Black Oxide and Black Phosphate
Amir Avni- Karmiel, Israel
2003
A. Black oxide is an exceptionally thin process which, as the name implies, is an iron oxide film. It is formed by putting iron parts into a very hot and very strong solution of caustic soda ⇦liquid caustic soda in bulk on Amazon [affil link] with nitrates and other ingredients.
Black phosphate, as I understand it and depending on who is selling it, is either a color variation on a standard phosphatized coating achieved with either a pretreatment or post-dip dyeing, or it is a very heavy less porous phosphate.
You didn't say what your interest was, so I would be general and say that the black oxide is probably cheaper, less corrosion resistant, and prettier.
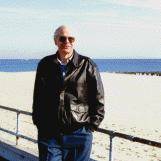
Ted Mooney, P.E.
Striving to live Aloha
(Ted is available for instant or longterm help)
finishing.com - Pine Beach, New Jersey
2003
A. AS I HAVE PRACTICALLY HANDLED THE PROCESSES OF CHEMICAL BLACKENING OF FERROUS SUBSTRATES AND PHOSPHATING WITH BLACK FINISH, I CAN SAY THAT PHOSPHATING WILL BE CHEAPER AND MORE CORROSION RESISTANT THAN BLACK OXIDE WHICH LOOKS ATTRACTIVE. THE CHEMICAL BLACKENING USING ALKALINE SOLUTION IS A DIFFICULT PROCESS WITH CLOSE OPERATING RANGE OF 136-140 ° C. IN PHOSPHATING MANGANESE PHOSPHATING WILL LOOK JET BLACK WITH MATTE FINISH BUT THE PROCESS NEEDS TO BE CONTROLLED VERY CAREFULLY. IF ZINC/IRON PHOSPHATING IS CHOSEN BASED ON THE FORMULATION OF THE PROPRIETARY CHEMICAL WITH NICKEL OR CALCIUM THE ATTAINMENT OF BLACK FINISH IS ENSURED. THIS PROCESS WILL BE THE CHEAPEST AND ESPECIALLY FOR SMALL COMPONENTS LIKE FASTENERS WHICH CAN BE HANDLED EASILY BY BARRELS. THERE IS YET ANOTHER COLD BLACKENING PROCESS WHEREIN THE FERROUS MATERIAL IS DIPPED IN A SOLUTION CONTAINING COPPER WHICH GETS COATED WITH COPPER BY DISPLACEMENT REACTION AND IMMEDIATELY BLACKENED BY SUITABLE ACETATE/SILVER CONTAINING PROPRIETARY SOLUTIONS. BUT THIS IS ONLY DECORATIVE AND VERY THIN COATING WHICH DOES NOT CONTRIBUTE TO THE CORROSION RESISTANCE OF THE SUBSTRATE METAL..
RAMASWAMI SUNDARMANUFACTURERS OF FASTENERS. - ALKHOBAR, EASTERN PROVINCE,SAUDI ARABIA
2003
Thank you for the fine exposition on this, Ramaswami. After thinking about it further, I'll concede that phosphating may be less expensive than black oxiding, even with the cost of proprietary chemicals whereas black oxide is usually done with commodity chemicals … but your hands-on experience trumps my book knowledge in any case :-)
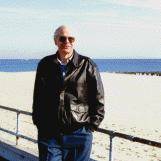
Ted Mooney, P.E.
Striving to live Aloha
(Ted is available for instant or longterm help)
finishing.com - Pine Beach, New Jersey
Q.
Could you please advise whether black phosphate is the same as 'blackening'/'blueing' on steel?
How phosphate coating prevents intrusion from salt?
Thank you.
- Roscoe, Illinois, USA
2007
A. Hi, Ming. No, "blackening/bluing" is the same thing as black oxide. I don't think that phosphate coating does significantly "prevent intrusion of salt", but it can help minimize galvanic hot spots, provide a "key" for paint, and minimize undercutting at scribe marks and filiform corrosion. Phosphating is a base for paint or sort of a oil-retaining dry film lubricant rather than a final finish.
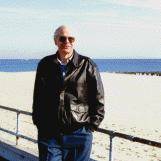
Ted Mooney, P.E.
Striving to live Aloha
(Ted is available for instant or longterm help)
finishing.com - Pine Beach, New Jersey
2007
Q. HOW THE PROCESS OF PHOSPHATING TAKE PLACE?
HOW CAN WE DO THE PHOSPHATING FOR VALVES?
VALVE MANUFACTURER - MUMBAI, MAHARASHTRA & INDIA
February 15, 2011
A. Hi, Shahid.
"Phosphating" is a pretty broad subject, involving cleaning the steel, then putting it into one of many different phosphatizing solutions, including iron phosphate, zinc phosphate, or manganese phosphate. Of these, manganese phosphate is the one usually used for internal engine parts. The coating holds oil well, and is somewhat softer than steel, so engine parts are often treated with it as a "break-in" agent.
Regards,
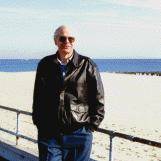
Ted Mooney, P.E.
Striving to live Aloha
(Ted is available for instant or longterm help)
finishing.com - Pine Beach, New Jersey
January 1, 2012
Q. Are black phosphate coatings electrically conductive? We are using BP-finished hardened steel spring nuts to secure 6-32 machine screws to the steel yoke of electrical devices to ensure a proper ground. The finish on the contact areas is almost always removed when the spring nut is installed on the yoke, but we are concerned in the instance that it may not be removed.
Kenneth Fiskengineer - New York, New York, USA
December 30, 2011
A. No. Since iron, zinc or manganese coatings contain phosphates, along with in some cases calcium, they are non-conductive.
Kishore Phadnis- Mumbai, Maha, India
January 17, 2012
Q. Galvanic corrosion question.... Does Black Phosphating provide any protection against galvanic corrosion between steel (low carbon) and magnesium (AZ91D)?
Ricardo Blutowski- Lith, Illinois, USA
June 28, 2012
A. Dear Ricardo,
Nope, phosphatizing is not a galvanic barrier. You need a dielectric, an isolating agent like paints or lacquers, to avoid galvanic corrosion of magnesium.
I hope you can solve this issue! Regards,
Self-Drilling Fasteners Manufacturer - Cañuelas, Buenos Aires, Argentina
August 27, 2012
Need composition for jet black phosphatizing
Q. Hi there!
Hope you all fine,
I want to ask bath composition of black phosphate immersion coating for jet black finish on screws and bath parameters; please help me for this enquiry. I have experiments with manganese phosphate, but in that, finish was gray to dark gray not jet black, so please give me some time for this.
international electroplating - Lahore Pakistan
March 29, 2017
March 2017
A. Hi Mustanser. What is the composition of, and the parameters for, the manganese phosphating that you were using which yielded a gray to dark grey color? What grade of steel are these fasteners that you are treating? In addition to processes that may be inherently darker, there are also dyeing processes to obtain black coatings, and perhaps that's what you are seeking?
Regards,
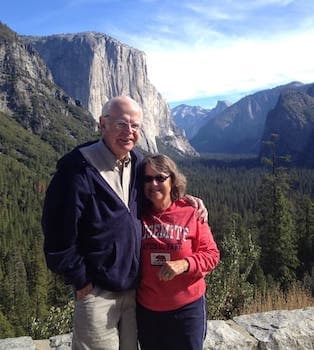
Ted Mooney, P.E. RET
Striving to live Aloha
(Ted is available for instant or longterm help)
finishing.com - Pine Beach, New Jersey
Q. Can I ask the difference between Auto Blackening & Black Phosphate Process?
Rupinder kaurJas udyog - Delhi, India
June 21, 2018
June 2018
? Hi Rupinder. Sorry, I am not familiar with the phrase "Auto Blackening". Please avoid posting abstract questions; rather, please tell us your situation and what motivates the question -- that way we may be able to figure out from the context how to help you rather than wasting your time and everyone else's. Thanks.
Regards,
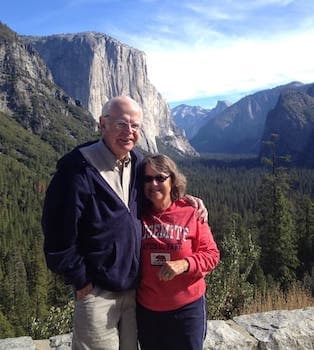
Ted Mooney, P.E. RET
Striving to live Aloha
(Ted is available for instant or longterm help)
finishing.com - Pine Beach, New Jersey
Q. How can small fasteners pass the 72 Hours Salt Spray Test for Black Phosphate Coating? Can you please elaborate?
Christian johnAreek Inc. - Oslo, Norway
June 26, 2018
June 2018
by Biestek & Weber
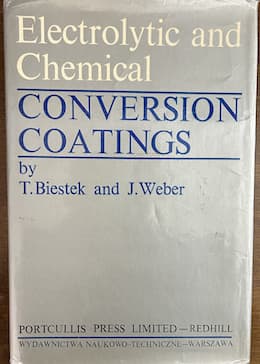
on AbeBooks
or Amazon
(affil link)
A. Hi Christian. Biestek & Weber .
claims that 100 hours is possible with phosphate & oil, and suggests that non-drying vegetable-based oil applied in heavy thicknesses is the most effective for corrosion resistance.
But guessing what will be the most helpful paragraph in a 400-page book is difficult :-)
Please start the dialog by telling us what your processing sequence is, what things you have been trying, and what results you have been getting. Presumably you can't use stoving varnish on the fasteners, but must use oil? Presumably you will reject the idea of a hot chrome based passivation rinse before the oil based on environmental considerations? Presumably the process line exists and there are limitations regarding what changes are possible? Are you, together with the process vendor, exercising close regulation over the process control parameters? Thanks.
Regards,
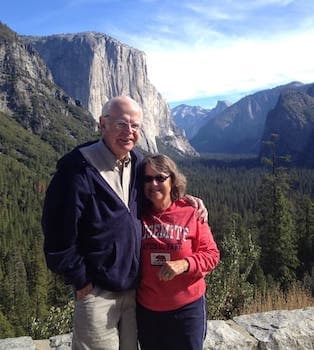
Ted Mooney, P.E. RET
Striving to live Aloha
(Ted is available for instant or longterm help)
finishing.com - Pine Beach, New Jersey
A. Hi Christian,
It is possible, with a heavy coat of zinc or manganese phosphate, hex chrome sealer and a heavy water displacement oil.
We make phosphate coating to screws to meet 72-120 hours of SST, with good results. Hex chrome replacement in this case is not too easy, but there are some non-chromic sealers you could try.
Best of luck!
TEL - N FERRARIS - Cañuelas, Buenos Aires, Argentina
June 29, 2018
Q, A, or Comment on THIS thread -or- Start a NEW Thread