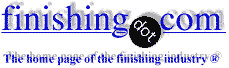
-----
Peak Anodization Resistance, a way to detect when to stop?
My situation is this;
Amateur small scale anodizing and dyeing, using type II anodization and commercial anodization dyes. By small scale I mean the work is less than 1 sq. ft. of surface area maximum (typical is half that). The electrolyte is 3 gals. of 12% sulfuric acid, the cathode is aluminum or lead sheet. Alloys being anodized are 7075,
6061/6063, "356" (al casting alloy) and 2024. I use current source anodizing only. The application is firearms parts, so only the best surface finish and uniformity in dyeing is acceptable. I an an EE by education and profession. I am not experiencing any problems but I do have a question.
In what little pertinent information I can find, it is claimed that the anodization barrier layer will continue to grow for as long as current is flowing through it. I have observed that this is not the case at all. The bulk resistance will increase from a very low value at startup to about 3 - 5 ohms/sq. ft. some time later. If the process is continued beyond this time the resistance will not increase further, but will slowly start to decrease.
This peak resistance appears independent of current density; higher currents reach peak resistance sooner and lower currents reach peak resistance later. (my range was 6 to 10 A/sq. ft.) 6 A/sq. Ft. corresponds to a peak anodization voltage of 19V after 40 min. when the work is 1/2 sq. ft. of surface area. Electrolyte temperature effects time to peak resistance slightly over a 60 - 80 °F. range, but not the peak resistance. The peak resistance value does vary with the alloy being anodized however, 7075 shows 5 Ohms /sq. ft.(highest) and "356" shows 3 ohms/sq. ft.(lowest). My electrical connections are very good, In all cases 14 AWG Al anode wire very tightly bolted to the work with Al hardware. My questions is; I am assuming that peak resistance is proportional to anodization thickness. I stop the process when the peak resistance is obtained, since I want the thickest layer. Is this assumption correct? It appears to be. Sorry this is so long.
- Columbia, Maryland, USA
Ed. note: it is our sad duty to advise of the passing of Paul Yursis in August 2005.
Here is a brief obituary by Mike Caswell.
2003
Two competing reactions are going on. One is the buildup of the aluminum oxide as you describe, but the other is the dissolution of the aluminum oxide by the sulfuric acid. So, at a given temperature and voltage, you will reach a peak thickness; and after that, nothing useful happens. You will need more accurate temperature control for best quality anodizing though. You really should hold 68 ± 2 degrees F; 60-80 F is much too wide a range. Other than that, things sound fine.
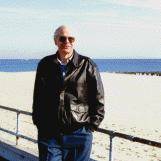
Ted Mooney, P.E.
Striving to live Aloha
(Ted can offer longterm or instant help)
finishing.com - Pine Beach, New Jersey
2003
Thanks Ted for your quick response. However I don't think I'm asking my question right. I'll try again.
I am using a current source that has 60 Volts of voltage compliance (sorry I left this out) this means that zero to 60V is available to drive the preset anodizing current. The voltage applied is whatever is required to maintain the preset current. This is done automatically by the current source (a lab power supply run in constant current mode). This peak resistance is independent of the anodizing current, and is not being limited by available voltage. The peak resistance rises to it's characteristic peak value and then stops increasing. If I set the power supply for voltage mode and force more voltage across the work, all that happens is that the current increases proportionally. By Ohm's Law this can only mean that the resistance has stopped increasing.
The questions: 1. Is this peak resistance proportional to the overall anodic layer thickness? 2. Or, is this peak resistance only proportional to the barrier layer thickness? 3. Is this a valid way to detect when the maximum anodization layer thickness is reached? Your answer that the reduction in the resistance is due to layer dissolution in the acid makes sense. I ran experiments over a 60-80 °F. range in order to see if this characteristic resistance was only a temperature effect, which it is not.
- Columbia, Maryland, USA
Ed. note: it is our sad duty to advise of the passing of Paul Yursis in August 2005.
Here is a brief obituary by Mike Caswell.
Q, A, or Comment on THIS thread -or- Start a NEW Thread