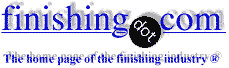
-----
Equivalence between ASTM B-117 vs. ISO 9227 NSS
Q. We have a customer, that we supply some zinc electroplated mechanical components to. He requires at least 300 Hr Salt Spray according to standard ISO 9227.
Our finishing supplier gives us a 96 Hr Salt Spray BUT according to the standard ASTM B117.
Is there any equivalence between this two standards ? Could this 96 hr (ASTM B117) be the same as the 300 hr (ISO 9227 NSS) that my customer requires of me ?
I'll really appreciate your help....
Regards,
- MEXICO CITY, MEXICO
2003
A. Hi Sergio, ASTM B117 does not address corrosion behavior of test specimens, but describes the parameters for conducting a salt spray test. So if you want to know how to set up a salt spray cabinet or how to make the salt solution, then B-117 is a reference. But benchmarking performance is something altogether different. I suggest that you send some parts out for testing according to the ISO standard to see if they meet the spec. That's the only way to know for sure.
George Gorecki- Naperville, Illinois
2003
A. ASTM B117 and ISO 9227 are essentially the same-- standard specifications for conducting corrosion testing. ASTM B117 is specific to neutral salt spray, whereas ISO 9227 also covers acetic acid (AASS) and copper acetic acid (CASS) tests. Conventional electroplated zinc (9 micrometer thickness) that is subsequently coated with a yellow chromate conversion coating typically produces less than 5% red rust after 96 hour salt spray testing. In order to meet the same % red rust for 300 hours of testing, you will need to do something different. Options include the following:
1. Thicker zinc plating (12+ micrometers) with a thicker chromate
(olive green instead of yellow)
2. A sealer over the existing zinc plating + yellow chromate
3. Something totally different like zinc-alloy plating, organic coatings, etc.
- Troy, Michigan
2003
Q. Hello. A personal good afternoon to all, I am Jose of Curitiba, I am a painting inspector, I am a specialist in the area of Salt Spray, and have a problem and knowing of the competence of all readers in corrosion, perhaps they can help me. I am needing to know if a gradual table of corrosion in assay exists of Salt Spray, if this table exists and if anyone would be able to post it, I will be thankful. Thanks a lot.
Jose Nunesinspetor de pintura - Curitiba, Parana, Brazil
October 2, 2010
Q. I will be using ISO 9227 for testing our Component, standard test duration is 1440 hrs of NSS test.
Is it possible to reduce test duration by some accelerated Testing? Any ISO standard is available for this Testing?
- India
March 16, 2012
A. Hi, Sagar.
As Toby mentions, ISO 9227 includes CASS testing, which is more aggressive than neutral salt spray. But which, is any, accelerated test is appropriate depends on what the finish is, and what you hope to test against. Remember that accelerated testing is not a proper indication of real world performance. Good luck.
Regards,
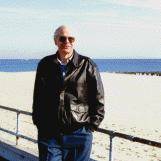
Ted Mooney, P.E.
Striving to live Aloha
(Ted can offer longterm or instant help)
finishing.com - Pine Beach, New Jersey
March 16, 2012
Q. Dear sirs, could you inform me please if there are any difference between standards ISO 9227 and ASTM B117? We did tests of our products under ISO 9227. Our competitors declares surface protection under ASTM B117. Could you inform me please, if ASTM B117 is easier to meet the requirements?
Many Thanks.
- Vrchlabi, Czech Republic
May 20, 2014
![]() |
A. As far as I know, there isn't much difference between ISO9227 and B117, just the temperature accuracy in testing chamber is 35+-2 °C in B117, while it's 35+-1 °C in ISO9227. Davey ShawShenzhen, Guangdong, China May 21, 2014 A. Hi David, Aerospace - Yeovil, Somerset, UK May 22, 2014 |
Dear Brian and Davey,
Thank you very much for your answers. I appreciate it! So I will start with benchmark with these two standards.
Thank you.
David
- Vrchlabi, Czech Republic
May 26, 2014
Q. What is major difference between ISO 9227 & ASTM B117 excepts to temperature?
Neeraj Rao- New Delhi, India
October 6, 2018
A. Hi Neeraj. Brian Terry has directly answered your question, but please post your situation rather than an abstract question so that readers can best help you. Thanks.
What do you want to test? ... because the specs you mention have to do with how to design and operate a salt spray cabinet; generally the plating, painting, or other metal finishing spec for your components tells you how to test them and how to interpret the results of the tests. A requirement that a component 'pass' an accelerated corrosion test isn't often meaningful until the finishing spec tells you what that means :-)
Good luck.
Regards,
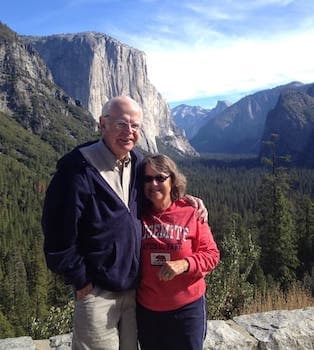
Ted Mooney, P.E. RET
Striving to live Aloha
(Ted can offer longterm or instant help)
finishing.com - Pine Beach, New Jersey
October 2018
Q. Hello I've been tasked with finding the main difference between the testing standards ASTM B117 and "EN ISO 9227" by my director.
Our issue is that we have a coating of Heresite which is suitable to 6000+ hours according to ASTM B117. However our main supplier occasionally has supply chain issues and has recommended us an alternative which suffers a break down at 1500 hours according to EN ISO 9227.
Obviously as our supplier they wouldn't recommend us a product that is considerably less efficient than what we are already getting -- are we missing something?
Thanks,
Ollie.
Kelvion - Fareham, Hampshire, UK.
February 12, 2019
A. Hi Ollie. Do you have both specs in your possession? If you do, you should be able to check what Toby has told us: that ASTM B117 covers only one type of test, Neutral Salt Spray; different ASTM standards are used to call out other salt spray tests like AASS ( ASTM G85) and CASS (ASTM B368) ... whereas ISO 9227 covers all three.
ASTM apples are fairly close to ISO apples, but not to ISO oranges. Are you certain that the 1500 hour ISO rating is for Neutral Salt Spray? If so, which is probably the case, you're pretty close to comparing apples to apples, so the finishes don't sound equivalent if one lasts 6000+ hours in NSS and the other fails at only 1500 hours. Good luck.
Regards,
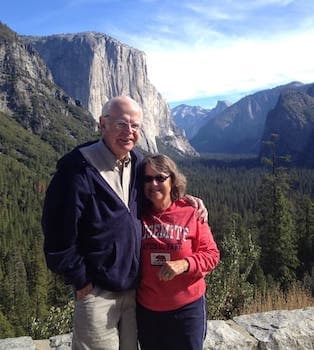
Ted Mooney, P.E. RET
Striving to live Aloha
(Ted can offer longterm or instant help)
finishing.com - Pine Beach, New Jersey
February 2019
A. Hi Sergio,
ISO 9227 is used to check corrosion resistant performance for metal parts or metallic plating parts by using salt solution 5% (NSS method - neutral salt spray). This standard also has option for acetic acid salt spray (AASS), copper-accelerated acetic acid salt spray(CASS)
ASTM B117 is used to test salt pray for metal parts or metallic plating parts by using salt solution 1%.
The step by step how to test set-up is almost the same between ASTM B117 & ISO 9227.
Time range to test is usually: 24h, 48h, 72h, 96h, 120h, 144h,.....
300h ISO 9227 & 96h ASTM B117 is not equivalent in 02 factors: salt solution & time duration, since the quality also not the same.
Hope it useful for you.
Eurofins CPT Vietnam - Ho Chi Minh city, Vietnam
Q, A, or Comment on THIS thread -or- Start a NEW Thread