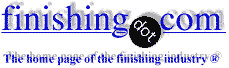
-----
Dyed Anodizing Color Matching

Q. Hi, can anyone advise on a simple way to test the concentration of the organic dyes we use in our anodising. I know a spectrophotometer will work but are quite expensive. Would a refractometer possibly work? I am looking for the simplest way to maintain 5g/l in solution. Any advice would be appreciated
Craig short- Plymouth England
June 2, 2021
A. Hi Craig
if not looking to make the investment in equipment then the next best and most cost effective way to have dye concentration checked is to ask the supplier of your dye to check the levels for you. They may perform this service for a nominal fee but some may even check for free.
Sorry for the late response but I just came across your post.
supervisor - Cicero, Illinois
Saporito Finishing Co.

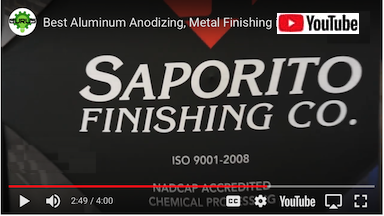
A. Hi Craig!
Seriously, don't be put off by the price of a spectrophotometer, there's a huge used market for them, and unless you want bells and whistles like UV range, scan function, data ports, etc... the technology is practically antique! I got a 1996 ish shimadzu uv-vis with a new bulb off eBay a few years ago for $500... that's the cost of the bulb... thing is a beast. Disposable Cuvettes are a dime a dozen on Amazon.
You make your own standards from demonized (ok, i typed DEIONIZED, but that is funny) water and dye stock weighed on a good balance, correcting for specific gravity if the stock is liquid, check the msds, and diluted in volumetric flasks. Your time of use calibration is just 4 data points (blank, 50%, 100%, 150%) and an excel spreadsheet to fit a calculation.
I posted my calibration sheet on here somewhere but if you want a freshie, I'll pass it along in digital form.
Your dye supplier *should * be able to give you periodic testing support. I mostly use the manufacturer for routine tests, and my dinosaur rig for custom-blended dyes, or to open a new tank for use the day it's brought online.
Also, unless you have an automated line... don't underestimate the art that a good line tech brings to the process. +/- concentration in simple single component dyes just changes the strike time. The tech will be able to judge the depth of strike and estimate leaching/bleaching in the seal, I am in awe of my work bestie who has that uncanny sense... It's really an art.
Multi component dyes (prime examples being any of the military tans and olives, plus the pinks/purples and some copper/Bronze shades, oranges and true greens seem to be more often single-component and stable) where individual components strike or are used up at different rates are much harder to handle, leading to off shdes... And with those, you need to talk to the manufacturer and get the peak wavelengths for all the components, test for them individually even if it means buying samples of the base components to use as standards, and be ready to dump a tank when one gets used up faster.
With greys, bath age and pH variation will give you pinks or greens. Talk to your tech rep!
I'll keep an eye on this thread because I think maintaining anodic dyes independently is a cool skill to put in your pocket. I'm releasing my email to Ted for this one in case you want my boring excel calculator.
Cheers!
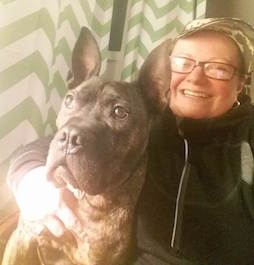
Rachel Mackintosh
lab rat - Greenfield, Vermont
`
⇩ Related postings, oldest first ⇩
Anodizing Dye Bath Analysis & Control
for Shops, Specifiers & Engineers
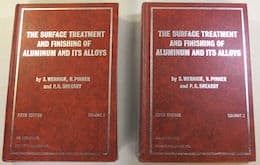
avail from eBay, AbeBooks, or Amazon
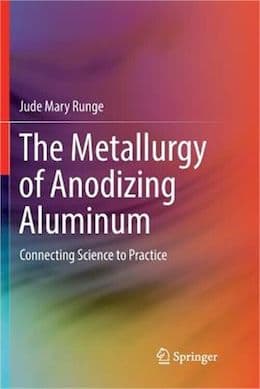
avail from eBay, AbeBooks, or Amazon
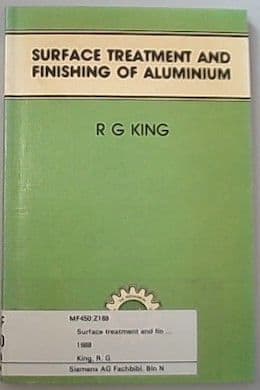
avail from eBay, AbeBooks, or Amazon
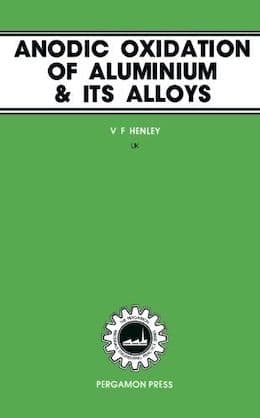
avail from eBay, AbeBooks, or Amazon
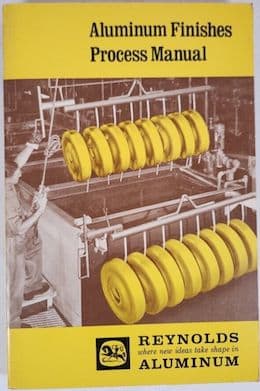
avail from eBay or Amazon
(as an Amazon Associate & eBay Partner, we earn from qualifying purchases)
Q. I am looking for information regarding analytical control of anodize dye bath. We are using a Sandoz DBlack MLW bath. We have discussed using a photometric method but I'm unsure how viable this is in regards to background metal ions in particular. It seems like a valid analysis method as a rough control but I haven't found any mention of it. Comments or references are welcomed. Thanks!
R. GuthrieBall Aerospace - Boulder, Colorado
1997
A. This has been a controversial subject in the past. I worked on controlling this bath for over five years and presented a paper on the control of this bath at the 93 Sur-Fin in Anaheim. This was due to the fact that frequently the only way we knew the bath was bad, or the dye activity was low, was from seeing rejected parts after processing. An independent lab was used for the analysis of the various contaminants.
One of the main concepts in controlling this type of dye bath is the difference between the concentration as made up, and the actual activity. The difference between dye bath activity and the nominal concentration is affected by many factors, primarily the amount of dissolved aluminum, and sulphates from drag-in. I should mention that at the time of my research sodium sulphate was used to standardize the activity of the dye during the manufacturing process, and the amount of that added varied from dye lot to dye lot. Other organic polyatomic and metallic ions also have been shown to impact the actual effectiveness of the dye. There have been some studies shown which have attributed air agitation to the degradation of the dye molecule.
There are really three ways to control the bath:
- "bleed & feed",
- using a spectrophotometer, and
- stripping dyed test panels from the process bath versus stripping dyed test panels from a control dye solution, and using calculations from math functions which are derived from the affects of various contaminants upon the dye bath activity.
I don't consider the method of just using a spectrophotometer a control method as many do, because in that case one is only measuring the total amount of the dye, not the activity. There are quite a few research articles on this subject and dyes in general, also Clariant (formerly Sandoz) has material on process monitoring. The method I used for several years was the last one, using calculations to determine dye efficacy, and in the process saved several thousand dollars in dye purchases. We also eliminated the periodic quality issues. Now, I am a proponent of the "bleed & feed" control system, and I know it is being used with success at a couple of shops. I have too many references on this subject to put in this response.
Ward Barcafer, CEFaerospace - Wichita, Kansas
A. I have been using this dye for over a year. People form Clariant told me that the Aluminum sulphate attaches to the pigment preventing it from dyeing the anodic coating, but keeping it on solution, so the spectrophotometric method will only give you the Nominal Dye Concentration and not the Effective one.
They give me a procedure for the later that consists of making a new dye bath and diluting it to 2 or 3 concentrations. Dip some pre-anodized aluminum strips in this solutions as well as in your dye bath for a predetermined time, then check the intensity and color and decide upon it.
Right now I am dumping it every month but I am looking for a solution like the "bleed & feed".
Armando TijerinaFormas Metalicas, S.A. - Monterrey, N.L. Mexico
A. I am writing this to talk about the bleed & feed method of controlling the black dye bath. I have been deluged with emails and calls about this. I didn't know so many people were having problems or were interested in the control of this bath. Many of you indicated that you didn't want anyone to know your company was having problems with your black anodize. I think that this is what finishing.com is all about, your customers probably don't log on as much as do others in the industry who might be able to help. Anyway, basically for those of you who just dump the baths every four weeks and make up a new one, here is an example --
A 600 gallon bath is ~2260 liters. Let's say this bath has an average accumulation rate of ~17 ppm of dissolved aluminum per week. Assuming an 82 ppm dissolved aluminum content target, then 17/82 = ~.2. Twenty percent of the bath is then to be decanted every week with a fresh makeup of ~8.5 pounds added back weekly. A new bath of 600 gallons at 10 g/l every four weeks would require ~45 pounds. By bleed & feed, every four weeks the bath would use 34 pounds. The target concentration of 10 g/l can be dropped to 8.5 g/l based upon the characteristics of the decrease of concentration over the first 8 hours due to drag-out. That drop brings the concentration down about 15% where it levels out. By the way this is common for many plating tanks whose requirement for additions is due to concentration decrease as opposed to contaminant increase.
In any case, one needs to determine the rate of build up for the main contaminant in question, which in this case is dissolved aluminum. Check periodically to maintain a baseline. This also allows for evaluating changes in the accumulation rate due to dissolving parts in the bottom, varying production rates, etc. Decant whatever the accumulation rate over time is from the total (bleed) and replace what was taken out (feed). Quality problems go away, and costs go down. This will work for almost all tanks given certain parameters. The above example is from an anodize line in a shop where I worked for a number of years and they are still using this method for control. (For those of you whose correspondence I haven't replied to yet, I have been out of the country and will respond this week.)
Ward Barcafer, CEFaerospace - Wichita, Kansas
Multiple threads merged: please forgive chronology errors and repetition 🙂
Aluminum Color Dye & Pigments
Q. Dear Sirs,
We are now intending to develop a series of products that are made of aluminum, in various colors. We had cooperated with our material supplier and anodizing factory to work together and the basic sulfuric anodizing process for clear anodizing seems can be solved.
The problem is, we find it is difficult to maintain the stability of colors during dyeing production and the usual colors we know are limited. We know that this is a usual problem for a beginner in this industry according to many factors that may influenced. But, surely , we have confidence to solve the factors step by step with the aid of factory and from your expertise.
We want to know is there any pigments or methods that can take anodizing and coloring at the same process ? We are looking for numbers of colors.
Do anyone knows any quality suppliers that can supply the above said pigments/ chemicals ? Or, is there any stable and quality organic/ inorganic chemicals suppliers that can assist in this to maintain a slighter variations during dyeing mass production.
All comments are highly appreciate and with deep thanks !
Sammy Shum- Hong Kong
1999
A. I don't know if there is any pigment that can be used during anodizing. But about the stability of the colour, I've talked to a pigment supplier before, and they said there is virtually no way of controlling the stability(in a factory setting at least), all is down to the experience of the factory. The pigment company's advice for me is to go for a reputable anodizing company. And all the pigments currently used are organic, so degradation is inevitable. About colours, if you order is big enough, e.g. >5 kg, you can ask the pigment company to customize colours for you. Or, you can mix your own colour with existing colours, but then again, that depends on experience, cause a lot of factors, e.g. particle size or pH of the pigment, can affect the results. My advice for you, go and ask the pigment supplier(good one of course), they probably know more than the anodizing factory, this is particularly true in the PRC region.
Doris Wong- Hong Kong
A. Exact color match from one lot to another is extremely difficult. Close is possible with great care. The first is the aluminum. It is never exactly alike, even from the same lot number. It gets worse with extrusions and is nearly terrible with castings. Things like the rate that it cooled down makes a difference in how it anodizes.
No production facility controls its solutions exactly. They use a range. The amount of aluminum and other metals dissolved in them makes a difference in the surface. thus the color appearance.
It is not easy to maintain an exact dye concentration, which affects the color.
The largest affect, after surface condition, is the anodizing process. A 1 degree C difference makes a difference in the pore size which affects the color adsorption. The next is the amount of anodize, thickness, which also affects the amount of dye absorbed, which affects the color appearance.
All reputable dye manufacturers have a stability rating for each dye. It makes a difference.
Some dyes have a metal constituent also and are not purely organic.
It takes a serious amount of control of every parameter to get very very close color match.
Normally, it is a tradeoff of cost vs the acceptable color match.
James Watts- Navarre, Florida
A. Sammy, The best way to control your dyes is to purchase from a reputable dye manufacturer. They are listed in the Metal Finishing Guide Book Directory.
For proper control of all colors we used to do a daily analysis for pH, temperature and twice per week a colormetric check. The dyes are all expensive.
Proper anodize bath controls are necessary as well as very good clean water rinses after anodize. The seal following dyeing cannot be overlooked.
Bill Hemptech svc. w/ chemical supplier - Grand Rapids, Michigan
QUICKSTART:
It is unusual to dye hard anodizing because the dyeing and sealing somewhat softens it, making it less than optimized for wear resistance. But it is occasionally done for blacker blacks (hard anodizing tends to be gray to charcoal in color depending on the alloy), and for special needs (such as differentiating live ammunition rounds from practice rounds).
Q. Dear friends,
I am dealing with hard anodizing; after anodizing I used black dye to color the parts, but it is observed that after some cycles of anodizing and coloring, the black dye bath doesn't produce the same colour as previously, and there is no volumetric method available to estimate the concentration. We use agitation for this bath, so what could be the reason behind it, or shall I need to add more colour after some cycles of anodizing?
- Abu Dhabi, UAE
April 1, 2014
A. Hi Aijazullah. We appended your inquiry to an earlier thread which hopefully answers it for you. You should probably set up a "bleed & feed" regimen to keep the power of your dye consistent. Good luck.
Regards,
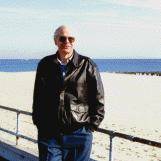
Ted Mooney, P.E.
Striving to live Aloha
(Ted can offer longterm or instant help)
finishing.com - Pine Beach, New Jersey
A. It's been awhile since I've done dyed work, but there were two ways (assuming you don't want to purchase a spectrophotometer) to analyze dye bath concentration. And of course you have to add dyestuff periodically to maintain concentration.
1. The suppliers I'm familiar with offer free testing of your bath. And while this is most helpful, it obviously doesn't give you an immediate results.
2. What we used to do was to purchase some filter paper (I don't recall what the micron was, perhaps 1-2 µm), and make up several known dye concentrations, i.e., if your concentration spec is 10 gr/lt, then make a 10, 9, 8, 7, 6, 5. and store in air tight eye dropper bottles. Put a drop of your bath on the filter paper, and then do the same with your test bottles. When you match the color of your bath, you then have a good idea of what your bath dyestuff concentration is. Make your addition accordingly. Nowhere near as accurate as a spectrophotometer but it's an acceptable, and much cheaper, workaround.
Of course, you also have to maintain the pH and temperature of your bath as well in order to achieve consistent results on your work.
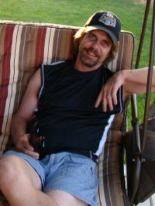
Marc Green
anodizer - Boise, Idaho
A. Aijazullah
Similar to Marc's response, we periodically use our supplier for an accurate analysis. In between, we use an Hach colorimeter, commonly used for testing waste water (for zinc), to evaluate the strength. Make up a standard of your desired concentration, determine a dilution that will yield a value near the upper end of the unit's measuring limits (2.2 ppm on ours) and compare to your process bath.
- Colorado Springs, Colorado
Q. Hi,
I'm trying to colour match a component and having relatively good results ... just trying to get that bit extra.
The sample pieces have quite a matte/satin finish to them whereas my parts are glossy and shiny.
What would the best way to get to the satin look?
I know you may need more specs of my process so please ask away and I'll try and answer with what I am doing.
- Worcester, Worcestershire
January 14, 2021
A. Hi Gavin. We've appended your inquiry to a thread that will give you some hints, but I'm assuming you are a hobbyist rather than a production anodizer, because while we can encourage you on your 'relatively good results' as a hobbyist, they aren't even in the ballpark for commercial anodizing :-)
The matte or satin finish is not achieved in the anodizing or dye tank, but via an etching process -- probably after a scratch brushing process (a quick one-time thru with sandpaper/scotchbrite on a "Timesaver" sanding machine. Etches may be caustic soda for a more matte look or ammonium bifluoride for a more satin look. Please spend some time with our search engine because we have dozens of threads on the topic.
The iridescence in your 3rd pic is an interference pattern indicative of a very thin transparent/translucent film of some sort. Either you have oil somewhere or your anodizing is too thin.
Luck & Regards,
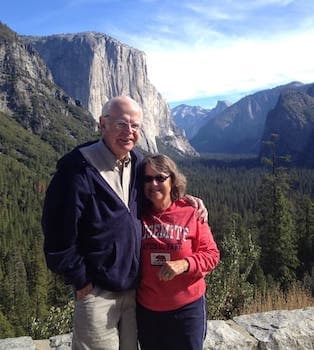
Ted Mooney, P.E. RET
Striving to live Aloha
(Ted can offer longterm or instant help)
finishing.com - Pine Beach, New Jersey
Q. Hello Ted,
Thank you for pointing me in that direction.
although yes this is my first venture into anodising I would like to become a part of my business as I'm creating some products and having the ability to anodise as they come off the machine so to speak would be great.
I have made some strides towards the end goal. Learning the importance of temperature, cleanliness, times, and rinsing between tanks.
With that said I welcome any criticism you can give.
- Worcester, worcestershire
A. Hi again Gavin. I think the point I'd make, but which you apparently already are understanding, is that consistent output can only come from consistent inputs :-)
Dye color will vary if anodizing thickness, dye concentration, or dye temperature vary.
Luck & Regards,
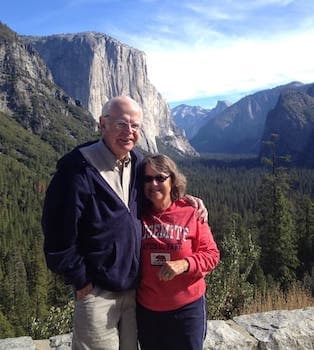
Ted Mooney, P.E. RET
Striving to live Aloha
(Ted can offer longterm or instant help)
finishing.com - Pine Beach, New Jersey
Q, A, or Comment on THIS thread -or- Start a NEW Thread