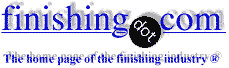
-----
Anodize vs chromate conversion
Q. I would like to know the difference in corrosion protection of type II anodize, clear sealed vs. chromate conversion. Perhaps Someone knows the salt spray hours for each ? Any help would be appreciated.
Brian Marty1998
A. Hi Brian. Chromate conversion coatings offer electrical conductivity, which can be important sometimes, and significantly lower costs.
Per MIL specs, chromate coatings must survive 168 hours and anodic coatings 336 hours, but I think that underestimates the difference. I believe that heavy anodic coatings with good sealing treatments often routinely survive 1000 hours. Good luck.
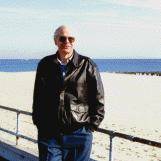
Ted Mooney, P.E.
Striving to live Aloha
(Ted can offer longterm or instant help)
finishing.com - Pine Beach, New Jersey
A. Salt spray tests are performed monthly at my shop for each of the anodize treatments that I perform.
I don't recall the exact amount of hours but I can get that info for you next week and include it in another message for you.it is also performed for chromic conversion each month. will let you know later.
ken neuts1998
1998
A. This is a relatively simple question which doesn't have a simple answer, because there are so many variables involved. Salt spray resistance is highly dependent on the aluminum alloy involved, regardless of whether the finish is anodize or conversion coat. A high quality anodize on an architectural alloy such as 6063 will withstand 3000 and even up to 5000 hours salt spray. (At those times salt spray resistance isn't a good measure of quality- 3000 hours is 18 weeks, and not too many shops can hold production parts for that length of time to see if they are finished properly.) Other alloys which don't have copper in them will withstand extended hours when anodized or conversion coated. We have customers who conversion coat cast alloys of boat motor parts that withstand 1000 hours bare salt spray. Our company even offers non-chrome conversion coating products that will withstand extended salt spray exposure times- on certain alloys.
It's a different story when the alloys contain copper. With the 2000 series alloys not only the alloy composition but the temper and even the age of the panels or parts can affect salt spray resistance. (I once had a conversation with Nathaniel Hall, then the finishing "expert" of Metal Finishing magazine. I thought he had lost it when he told me that the copper in 2024 will precipitate out in the alloy, with time, until I went back to our lab and looked under a microscope at some old vs. new 2024 panels. The old panels had "chunks" of copper sitting on the surface. Tempering/artificial aging can have the same effect.) In general, MIL-A-8625 / MIL-PRF-8625 [⇦ this spec on DLA], the major military anodizing specification, calls for 336 hours salt spray. With 2024 alloy this is difficult to achieve with a straight hot water seal, easy to achieve with a dichromate seal, but the dichromate seal gives a yellow-green finish.
The military processing specification for chromate conversion coatings, MIL-C-5541 calls for 168 hours salt spray resistance with 2024 alloy, but the specification which we vendors worry about to qualify our products, MIL-DTL-81706 [⇦ this spec on DLA] , requires passing 336 hours salt spray. In other words, the requirements of anodize and chromate coatings are quite similar. When trying to decide whether to anodize or conversion coat, one must consider all the factors of the coating, and not just salt spray resistance. Conversion coating is more economical, in the short run, but the process needs tighter controls. Ted pointed out some of the differences. Chromate coatings have almost no abrasion resistance, while anodize can have better abrasion resistance than even paint.
I didn't mean for this to turn into a long dissertation, but while I'm at it I might as well bring up the question of what salt spray resistance means, as related to the real-world life of finished parts. Except for the industry that makes boat parts or other marine-related products, probably not much. I have been involved with qualifying processes with 2024 panels, even though the parts to be processed were not a high-copper alloy. As I indicated in the paragraphs above, there is a world of difference.
Phil Johnson
- Madison Heights, Michigan
1998
A. As I previously stated: I would get salt spray times for the processes I perform at my shop. They are as follows:
Chromate conversion is indeed 168 hrs.
our regular anodize is 240 hrs and special anodize for corrosion resistance is indeed 336 hrs -- that's all I'm at liberty to say about it except that we use test parts made with 2024 material for testing in same loads of production parts -- this helps reduce lost time of using production parts and gives accurate results as loads are numerized.
That's an interesting observation about copper content going to surface after some time -- I'll have to consult about that. As you can see from all these letters, there does seem to be similarities. Hope any info here helps you out. Oh yeah, the above responses came from guys that know their stuff: my hat's off to you.
ken neutsQ. Hi, I have worked over 30 years on aircraft.
In the fuel system it was common to sand off non-conductive anodized area under a bolt head, then brush Alodine the exposed area and place a "jumper grounding lanyard" sandwiched between the bolt and the Alodined part.
So the Alodine was conductive where as the Anodizing was not. (This was for lightning protection)
So my question is, would one use Alodine as a primer for paint? Or is it always used on a bare exposed area.
Sincerely,
- Burlington, Ontario, Canada
September 5, 2013
A. Hi Joe. Alodine is a brand name of one particular MIL-DTL-5541 chromate conversion coating for aluminum, but yes, chromate conversion coating is the preferred pretreatment for painting and powder coating on aluminum.
Regards,
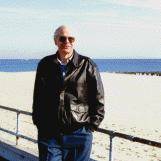
Ted Mooney, P.E.
Striving to live Aloha
(Ted can offer longterm or instant help)
finishing.com - Pine Beach, New Jersey
September 2013
September 13, 2013
Q. Good afternoon!
A problem I've never got to the bottom of:
- An EN AW-7022 machined part is anodised black (5-10 micron)
- Anodised part is selectively machined to remove anodise from surfaces which require EMC-compatible surfaces. - These conducting surfaces are now blank aluminium with no surface treatment - bad.
What can I now do to the parts to ensure that the machined surfaces do not oxidise?
Passivate?
Thank you!
- Thirsk, UK
A. Hi Angus. Yes, you've got it.
Regards,
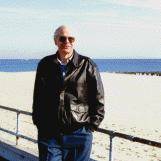
Ted Mooney, P.E.
Striving to live Aloha
(Ted can offer longterm or instant help)
finishing.com - Pine Beach, New Jersey
September 17, 2013
A. Hi Angus,
In my company bared aluminium for EMC purposes are then protected with chromate conversion coating to MIL-DTL-5541 Class 3 for electrical bonding.
I don't have experience of the non-chromated version, but I would guess that they would be just as acceptable if you cannot use chromates.
Aerospace - Yeovil, Somerset, UK
September 18, 2013
Q, A, or Comment on THIS thread -or- Start a NEW Thread