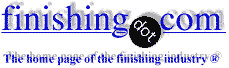
-----
Cadmium Plating Thickness Control
Q. I am trying to control the Cadmium plate thickness on drive shaft components. We have a hard time measuring and thus controlling thickness on small diameter parts. Currently we plate by setting a certain voltage (2-6 volts) on a constant voltage rectifier. This should give a fairly consistent current density regardless of the size or number of parts plated (within the limits of the rectifier). For a desired thickness we then need only to plate for a set time:
example: 3.0 volts gives 30 amps/sq. ft at the part so plating for 8 minutes will give a thickness of ~ 0.0004 inches.
My question is: As the anode area decreases (cadmium balls dissolve) will the effective resistance of the circuit increase and thus decrease the current density for a given set voltage? Or vise versa - by adding anode area (i.e internal anodes for ID's) will the resistance of the circuit decrease and thus increase current density?
Would it be better to plate by 1)finding total wetted surface area of the part and 2)plate by setting a constant current at the rectifier to get the proper current density?
We have thousands of cadmium plated parts of complex shapes and this would be a big task.
How does throwing power of the cadmium plating bath come into play here?
Greg Haatajahelicopters - Fort Worth, Texas
1998
A. Dear Greg,
Rather than use constant voltage to control your bath, I would recommend Constant Current.
The example you give is fine but you must bear in mind that the thickness will be AVERAGE over the whole parts surface, the actual distribution of plated metal will be in accordance with the Current density applicable to each item, the current density will vary according to some or all of the following parameters, Shape of the part, geometry of the racks used to hold the parts, efficiency of the solution at varying current densities, anode contacts, rack contacts with both the part & cathode bar, etc.
To run your shop at maximum productive efficiency, each part should have a "File" on which is recorded, the surface area of the part, the rack used to hold the part ( i.e., its specific number or identifying mark ), the number of racks per "Flight bar" of work, and of course the finish required in terms of Metal deposited, its thickness, & any post plating treatments such as Chromate conversion coating, Hydrogen Embrittlement relief, etc.
Yes it will take a long time to do now, but remember it only has to be done once, and once done no one can complain about not knowing what to do if you have to take a week off to go fishing !
The effective resistance of the circuit depends more on the chemistry of the bath & the resistance of the anode basket hooks to the anode bar (poor or dirty connections make a big resistance) than the anode area in the baskets, which should be kept full at all times.
regards

John Tenison - Woods
- Victoria Australia
1998
1998
A. It would take several chapters of a book to answer all of your questions in any detail.
I am not a believer in plating by voltage. Very tiny changes can have a significant effect on plate distribution and thickness.
The voltage amperage relationship is not linear. i.e., if 100 parts take 3 volts and 10 minutes, 200 parts will not take 6 volts for 10 min OR 20 min at 3 volts.
If 100 parts take 50 amps and 10 min, 200 parts will take 100 amps for 10 min with a modest ±.
Anode to cathode distance makes a huge difference in most, if not all, plating. It certainly has a huge effect on plate distribution.
Solution resistance will change with the strengths of the individual components, the amount of impurities dragged in and the temperature. Intensity of agitation affects the diffusion layer at the part making it look like it has affected the resistance. Within reason, most plating tanks will plate a given amount for a given number of amps, regardless of minor changes in resistance.
The size and number of anode balls in a basket effects the anode area and thus the anode efficiency.
The amount of anodes in a tank will affect the plating distribution. Some metals have a tighter anode cathode relationship than others, with all else equal.
I could easily go on for a couple of hours with my opinions, based on actual experience and what I have heard and read.
James Watts- Navarre, Florida
A. My answer to your question/problem is to use current density control to regulate deposit properties and use amp-hour or amp-minute totalizers to control deposit thickness. The two work hand-in-hand.
Constant current is not critical, but a convenience. A relatively stable rectifier output and a timer are necessary if you don't have amp-time totalizers.
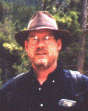
Bill Vins
microwave & cable assemblies - Mesa (what a place-a), Arizona
1998
Q. How to get uniform cadmium plating on steel parts like bushes with smaller internal diameters in the range of 5 to 16 mm.
Sreenivas RaoAerospace - Bangalore, Karnataka, India
April 3, 2013
A. Hi Sreenivas. The plating goes where the current goes (Faraday's Law of Electrolysis), and the current (as a slight simplification) takes the path of least resistance. Cyanide cadmium plating will have slightly better throwing power than acid cadmium plating, so if you are getting almost enough plating on the ID, then switching to cyanide might help. But if the length of these bushes is, say, twice their ID or more, you won't be able to plate the ID without "stringing" the bushings on an anode wire and insulating them from it for plating. It's certainly possible, but it's no longer an inexpensive, commodity, bulk processing situation. Good luck.
Regards,
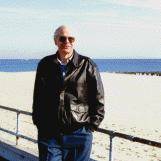
Ted Mooney, P.E.
Striving to live Aloha
(Ted can offer longterm or instant help)
finishing.com - Pine Beach, New Jersey
April 4, 2013
Cadmium Plating thickness distribution problem
Q. Dear All;
I'm working in an aerospace company. We performed Cad plating by barrel for bolts. We have parts with long shank (with a 7-10 cm length and 11-12 mm diameter) and threads (diameters about 7 mm). When we plated cad on these parts, we have some homogeneity problem on long shank area. The beginning and the end of the shank is about 10-11 micrometers, but the middle of the shank is about 6-7 microns sometimes it is about 5 microns. If we try to keep plating to increase lower thickness places, other places are out of tolerance especially threads and sharp corners at the end of shank. The thickness of plating should be 8-12 microns. It is low alloy steel (AISI 8740). I need help on this issue. Do you have any idea?
Regards
Savas
- Turkey
November 1, 2016
A. Hi Savas. You didn't yet answer my implied question from the previous answers of whether you are running cyanide cad or acid cad. Cyanide offers more even thickness distribution. Thanks.
Regards,
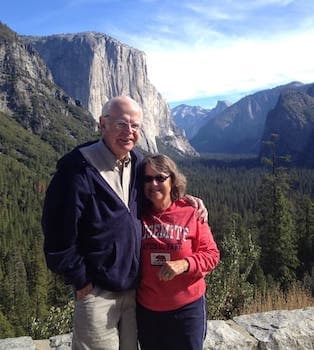
Ted Mooney, P.E. RET
Striving to live Aloha
(Ted can offer longterm or instant help)
finishing.com - Pine Beach, New Jersey
November 2016
Q. Hi Ted;
Thank you for response. I'm running cyanide cad plating. I guess that the middle of the parts don't get enough current to be plated. I have tried just parts in the barrel, I have tried parts with dummy parts. All the time, I have put same volume (60% of volume for one barrel) and I have tried same current during plating. I m using 0.6 A/dm2 current density. When I used higher current density (1-2 A/dm2), I couldn't control the thickness of the plating. In addition to this, I have tried 45 sec-1 min plating with high current density (3-4 A/dm2), like strike in the same bath, then I came back to 0.6 A/dm2 for plating. the result was same. I'm really stuck. Any idea?
Regards,
- Izmir, Turkey
November 2, 2016
A. Hi again Savas. My book learning says:
(Garden State Branch AESF "Electroplating Course Manual")
You might also look at Khozem Vahaanwala's response on letter 10000 to see if you feel that some of it is useful.
Beyond that, I'm going to have to rely on one of our readers for further suggestions. I understand everything you have said, but do not have personal experience in solving this particular problem.
Regards,
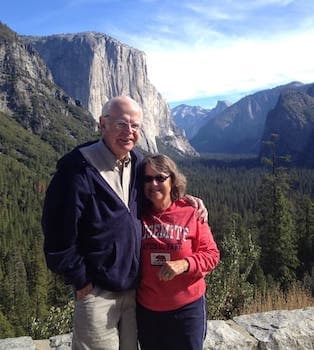
Ted Mooney, P.E. RET
Striving to live Aloha
(Ted can offer longterm or instant help)
finishing.com - Pine Beach, New Jersey
November 2016
Q. Hi Ted;
Thank you for info. Could you advise me that how can I find the book called Garden State Branch AESF "Electroplating Course Manual" to buy it? I have tried to find from google to buy it but there is no info to find it.
Regards
- Izmir, Turkey
November 2, 2016
A. Hi Savas. Regrettably, I think you'll find that particular book unavailable. But there are numerous good electroplating books.
Regards,
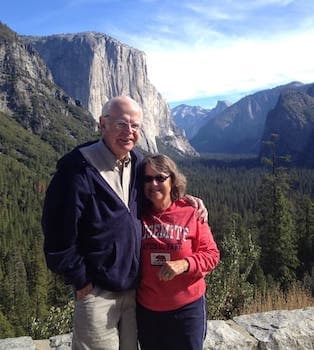
Ted Mooney, P.E. RET
Striving to live Aloha
(Ted can offer longterm or instant help)
finishing.com - Pine Beach, New Jersey
November 2016
![]() |
A. What is your cyanide number? It should be 12 - 14 oz/gal, if memory serves. ![]() Dave Wichern Consultant - The Bronx, New York November 3, 2016 November 4, 2016 A. Good day Savas. Aerotek Mfg. Ltd. - Whitby, Ontario, Canada |
Q, A, or Comment on THIS thread -or- Start a NEW Thread