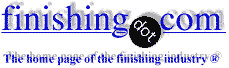
-----
Electroless Nickel Plating of holes, threaded holes, and blind holes
Q. Plating small diameter holes:
We are looking into plating billet-machined aluminum parts with 3" through holes on order 0.125" diameter. High corrosion resistance and high thermal conductivity are musts. Comments on relative cost of processes will be greatly appreciated.
Please advise with regard to plating options: hard anodize (.002" buildup) -- looks difficult/costly electroless nickel -- will this truly yield uniform plating? -- corrosion resistance? -- what is zincate and how is it applied? any other electroless processes? -- hard chrome? any other options to suggest?
Much appreciated,
- Palo Alto, California
2002
A. Hello, Jim. The biggest problem that you will have it that all of these electrochemical processes operate out of solutions which provide the necessary ions for the reaction to proceed--and the amount of solution within a 1/8" dia. hole is obviously very limited.
So, if you try to hard anodize it and you don't get fresh solution in the hole, the acid will grow depleted and unable to perform the necessary dissolution process. Similarly, to electroless nickel plate it, you must get sufficient nickel in the solution immediately proximate to the deposition point.
Maybe an anodizer or electroless nickel plater can offer you a practical solution exchange mechanism based on high agitation, ultrasonics, etc., but my feeling is you'll probably need special rigging to pump solution through these holes.
Zincate is an alkaline solution, sometimes proprietary, with zinc dissolved in it which immersion plates onto aluminum and is used as a prep step because of the difficulty of keeping an aluminum surface active for electroplating. Zincate is used as the first plating layer nearly universally, but it is not a final finish.
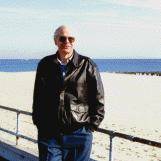
Ted Mooney, P.E.
Striving to live Aloha
(Ted can offer longterm or instant help)
finishing.com - Pine Beach, New Jersey
2002
A. Try high phosphorous electroless nickel. To insure the hole is coated uniformly you will have to cut a part at the halfway point of the 1/8 in ID and have the plating measured with a microscope. This is called a microsection and should cost about $100.00 at a testing lab.
Todd Osmolski- Charlotte, North Carolina, USA
2002
A. First build a jig that will hold a significant number of tubes in the vertical position of a manifold. Then pump Aluminum Cleaner into the manifold and up thru the tubes and spilling back into a catch basin. Repeat the pumping with each of the following solutions, (2) water (3)Aluminum Deoxidizer (4) Zincate (from "cook" book or proprietary mix) (5) water (6) alkaline electroless nickel (7) water (8) acid electroless nickel (experiment with times until you get enough thickness to withstand whatever corrosion media that you did not mention).
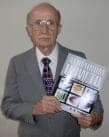
Robert H Probert
Robert H Probert Technical Services

Garner, North Carolina
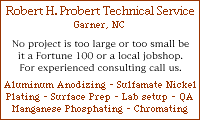
2002
Plugged hole corrosion problem
Q. I have Electroless Nickel plated parts with blind threaded holes. These holes were masked with tapered plugs during plating. Now I am seeing a white powder structure growing on the first and second lead in thread. What can be done to neutralize this corrosion?
Bill Martin- Marysville, Washington
2003
A. First off ... if your plater is worth his salt, he should gladly take the parts back and make them good. If you did the plugging on the holes, that's the risk you take! This is one plater who won't accept anyone else's masking without a specific waiver that if there is leakage, it's not our fault! Now on with a couple of solutions....
White salt corrosion so I'm presuming that your EN plated part is made of aluminum or zinc. Once you've seen the salts, the corrosion mechanism is in high gear - water from air has been adsorbed with corrosive plating and/or pretreatment chemical residue. If indeed caustic residue (i.e. alkaline cleaner, etch, etc.), then you need something mildly acidic that will neutralize alkaline salt without harming aluminum or nickel - try acetic acid
⇦ on
eBay
or
Amazon [affil link] (a.k.a. vinegar
⇦in bulk on
eBay
or
Amazon [affil link] ) or boric acid (eye wash solution from blue bottles). If acidic residue from acid deox or EN solution itself (except this would be characteristically green salts), need something mildly alkaline that will dissolve salts. Sodium carbonate (washing soda
⇦ on
eBay
or
Amazon [affil link]
) or bicarb (baking soda [in bulk on
eBay
or
Amazon [affil link]
) might do the trick. Either way, dilute with warm water and apply in holes with eye dropper. Obviously we've been here ourselves. Masking holes is tricky and never 100%.
Good luck!

Milt Stevenson, Jr.
Plating shop technical manager - Syracuse, New York
2003
A. I'll take a wild guess that you have an aluminum substrate. Then, the white corrosion could be aluminum and/or zinc hydroxide. If so, the corrosion could slowly spread beneath the EN. Try the following methods [test one part or one hole first]:
Short procedure [chromic acid]: Soak part in 1 wt% chromic acid/DI water at 120 °F for 15-20 minutes, turning and draining as necessary to fill and empty each hole. Rinse in a dragout tank, then with DI water, then blow dry with clean air.
Long procedure [nitric acid clean & chem film]
Set up a working area next to a flowing rinse or sink. Use an eyedropper to put some 50 vol% nitric acid [or deox. solution if very little corrosion] into holes on the top surface. Use caution, the nitric may foam up and stain the EN [of course, you could play safe & put plating tape over each hole area, then work through a hole in the tape]. After foaming ceases, thoroughly rinse. Final rinse each hole with DI water. After thus cleaning all the holes, move your workstation next to your chromate conversion (chem film) solution tank and its rinse tank. Apply chem film via eyedropper, rinse when coated. Rinse again with DI water, then blow dry with clean air.
Let us know the results.
- Goleta, California

Rest in peace, Ken. Thank you for your hard work which the finishing world, and we at finishing.com, continue to benefit from.
2003
Corrosion potential of unplated blind holes in aluminum
Q. We are plating an aluminum part with electroless nickel, bright nickel and tin for use in the electrical supply industry. We have been asked to plate a part with a blind hole and was wondering if, as very little if any plating will be inside this threaded hole, what is the potential for problems when a stainless steel bolt is screwed in and the part is exposed to the elements.
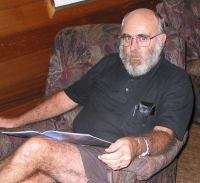
Bob Lynch
plating company - Sydney, Australia
2004
A. Galvanically, aluminum and stainless steel are not far enough apart to cause any serious problem. That said, I would recommend plugging (masking) the holes, because as you know, the oxide film forms half in and half out, so that on the sharp cutting edge of a thread the whole edge will be brittle oxide and it will break off and weaken the connection.
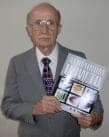
Robert H Probert
Robert H Probert Technical Services

Garner, North Carolina
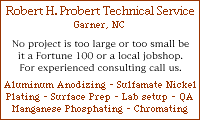
2004
A. Since you said electronics, I assume that it is a 4-40 or a 6-32 thread. The probability is that it is for helicoils. If not, it probably should be. Small holes hold a lot of chemicals after each process tank which seeps out in the next. After the EN, you normally have ugly rings around the holes and sometimes , even runs. The only way to avoid that is time consuming flushing each hole with a small stream of water. With helicoils you can use a dab or zinc chromate and the helicoil creates a metal to metal contact and seals the non contact portions. Small blind holes are a challenge.
James Watts- Navarre, Florida
2004
A. In letter 39153 James makes a suggestion regarding blind holes that will be plated that they be filled with clean rinse water before the process starts, to minimize entrapment of chemicals. I can't help but wonder then, in the case of plugged holes, if filling the holes with clean rinse water before plugging them wouldn't minimize stains, accidents, etc., from the plug not performing perfectly.
Regards,
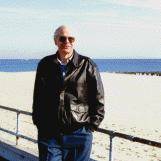
Ted Mooney, P.E.
Striving to live Aloha
(Ted can offer longterm or instant help)
finishing.com - Pine Beach, New Jersey
July 2014
Multiple threads merged: please forgive chronology errors and repetition 🙂
2007
Q. Dear sir,
We have problems regarding blind hole plating of our mechanical parts which are made of steel. We have tried electroless nickel but did not pass the salt spray requirement.
Is there any other way we can plate the blind holes in our parts?
The blind hole is 3 mm dia. and its length is 5 cm.
Any suggestion?
Regards
joe
electronics - Ankara, Turkey
A. Joe,
I would assume you are giving these parts a Woods Nickel Strike? I have found that front to back bar agitation in the EN tank helps with blind holes. With this rocker type motion, solution is forced in and out of the holes. Side to side agitation sometimes is not good enough. Good Luck!
Process Engineer - Syracuse, New York
2007
A. Joe
I would agree with Mark's suggestion about agitation but I believe that your problems start at the cleaning stage. 3:1 is about the limit for plating blind holes and problems increase as the diameter goes down.
First, cleaning is just as important inside the hole as on the surface. Vapor degrease if possible. The next problem is to get the first of the aqueous process solutions down the hole. Beware of trapped air bubbles. Ultrasonic agitation is often recommended. In my experience this just leads to a vibrating air bubble! I have been forced to use vacuum occasionally to get the air out and the solution in.
Next rinsing: Because of the aspect ratio, the removal of chemicals is largely dependent on diffusion. This is slow so allow plenty of time. Use a water jet if possible, and hot water helps. If you leave any of the chemicals in the hole they will interfere with the next process.
Now to get the next process chemicals into a hole full of water, and again diffusion limits the rate. Effectively you have a diluted process operating in the hole so allow time and don't expect fast plating.
I used to visit our design department regularly to ensure that there were no blind holes designed in to cause me problems later. Even a tiny bleed hole helps enormously.
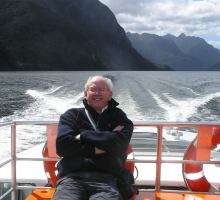
Geoff Smith
Hampshire, England
2007
A. Geoff and Mark are kind! Plating will normally go into blind holes with a 1:1 aspect ratio (width over depth). Yours is 3:50.
Individually hand plating will not plate to the bottom of these holes for the reasons stated.
Exotic printed wiring board plating solutions are not even asked for this level of plateability and they are thru holes.
True zinc chromate primer
⇦ on
Amazon (affil link)]
is about the only option.
- Navarre, Florida
2007
A. It's not easy but a good electroless nickel plating practice and fixturing will be able to solve your problem and plate those blind holes provided your substrate is plain carbon steel. Alloy and stainless steels as well as other substrates that require a galvanic activation will be subject to the described problems associated with the aspect ratio. We have successfully plated several molds with intricate geometries and very deep recesses and holes.
Guillermo MarrufoMonterrey, NL, Mexico
2007
Q. I am also facing this issue with blind holes when doing E.N. plating. Parts have 4 and 5 holes depending on the models.
M2 holes. I have one or two holes not plated nicely.
- Penang, Malaysia
July 4, 2012
A. To cover all the blind hole it is necessary that the hole facing upward to allow the hydrogen gas to escape. It is aided by the use of "wetting agent" (surfactant) to facilitate removal of hydrogen bubbles.
If it it is impossible to have all holes face upward, then rotating is required.
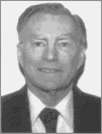
Don Baudrand
Consultant - Poulsbo, Washington
(Don is co-author of "Plating on Plastics" [on Amazon or AbeBooks affil links]
and "Plating ABS Plastics" [on Amazon or eBay or AbeBooks affil links])
July 8, 2012
A. With a proper fixture you will be able to electroless plate the blind hole.
Besides this, you must be sure that the Salt Spray test is done in a correct way.
Liquid must flow thru the surface and must prevent liquid stagnation inside the blind hole.
Bnei Berak, Israel
July 27, 2012
Electroless Nickel plating in small blind threaded holes.
July 25, 2014Q. EN-Plate .00015-.0002 thick on 0-80 and 1-72 threads on 1215 cold rolled steel.
I have been struggling with this process for some time. Threads are good before going to plate. We are using oversize taps during the machining operation.
Parts are racked on an angle to assist with draining. Unfortunately there are many holes on either end the cylindrical part.
Our plater uses a triple rinse and drying process.
There are two problems.
1. We cannot get plating all the way into the small blind holes because there is always an air pocket trapped. This makes pre-plate tapping/gauging a challenge.
2. We can never get all of the moisture/plating residue out of the small blind holes which stops are thread plug gage after plating.
Unfortunately, we cannot change the design of the part at all and need to improve the plating/machining process to reduce the need to re-tap every hole after plating.
Any input is appreciated. thanks much.
Gabe
Quality Engineer - Spencerport, New York
A. Hi Gabe,
Vibration (with vibrator) or knocking by lifting up rack then free falling (manual or automatic) is highly recommended for EN inside blind holes to get rid of trapped gas bubble quickly (mostly hydrogen gas generate from EN reaction). Similarly, post rinsing (with vibration and/or knocking system) and drying with strong hot air circulation is necessary to ensure chemical residue inside blind holes is fully removed and dried.
Regards,
David
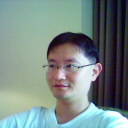
David Shiu
- Singapore
August 10, 2014
Q, A, or Comment on THIS thread -or- Start a NEW Thread