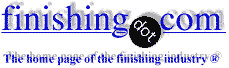
-----
Problems / defects in powder coating
2002
Q. Following problems on mild steel panels powder coating are observed after the process is complete:
1) Powder peel off
2) Dust particles observed
3) Orange peel
4) Color shade difference one compared to other panels
5) Pin holes observed on the coated surface.
You are requested to give probable reasons and solutions.
Thanks and regards,
Jagdish S. Rane- Pune, Maharashtra, India
2002
A. Hi Jagdish,
The problems you are experiencing are quite common, I will answer then in the order you asked them:
1) Powder peel off. A. Poor adhesion caused by poor substrate preparation or insufficient curing. You must make sure the substrate is suitably pretreated.
2) Dust particles observed. A. Poor housekeeping, poor air control in your spray booth, etc.
3) Orange peel. A. A number of aspects may cause this, most commonly poor particle size distribution and poor gun control. (Try turning down kV on gun, and control your reclaim system)
4) Colour shade difference one compared to other panels. A. Poor oven conditions / controls. You may have "Hot Spots" in your oven. The work pieces must have the same curing conditions.
5) Pinholes observed on the coated surface. A. Cross contamination or back ionisation. Clean your system down thoroughly and make sure when you spray the gun is at least 12 inches (30 cm) away from the work piece. Try spraying at 70 kV.
Hope this helps,
Drew Devlin- North Lincolnshire, U.K.
Hi Jagdish.
You seem to have mentioned just about every possible powder coating problem :-)
Can you tell us what kind of powder are you depositing and under what conditions. And also what is your pretreatment process? Thanks!
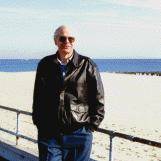
Ted Mooney, P.E.
Striving to live Aloha
(Ted can offer longterm or instant help)
finishing.com - Pine Beach, New Jersey
2002
A. Dear Mr. Rane,
From your question it seems you are not using quality product. Please use quality product. Please tell me which colour you are using.
Kuldeep Verma- FARIDABAD, India
2004
January 31, 2010
A. Hi...
To add reply from our friend - Mr.Drew Devlin -UK..
1.Powder peel off - mostly came from improper pretreatment process. Check with your chemical provider and please do daily check on your chemical level every time to start production , add chemical to stabilize the level if need
2. Dust particles - Make sure your powder booth is secure enough from dust. Some of applicator make room to secure the powder booth . Keep your house keeping well.
3. Orange peel - make sure your powder coating is orange peel . BUT if you use matte type and the result ...looks orange peel...make sure do not over thickness.. good thickness in range of 60 - 100 micron...if you use type matte and thickness too thick up 250 micron...there is orange peel effect come up..
4. Colour shade different - Check your oven ..stabilize your oven. Ask your powder supplier to check your oven and make sure your heat distribution is OK and match with your powder specification .. eg. 200 °C - 10 minutes. After you make sure it's OK .. then test your result using gloss tester ... and make it as standard (range).
5. Pin holes.... agree with Mr.Drew Devlin.
thanks
Kemal
- Jakarta Indonesia
----
Ed. note: Readers: this is one of dozens of threads about problems in powder coating. Many defects have their own thread or threads here. For additional insights you can search the site for the specific problem or defect.
Q. Dear Sir,
My question is about a rusting problem on powder coated panels. We have outsourced one of our products from our supplier which is metal enclosures for telecommunication kits. It is fully exposed to the outdoor atmosphere; it is rusted after a period of 11 months. The treatment is done for M.S., 7 tank process with hot phosphating. The powder used is pure polyester texture pattern.
telecommunication products - Bangalore, Karnataka, India
2005
A. Hi,
As far as my knowledge is concerned I'm thinking that the powder you are using is not of good quality polymer percentage of the powder is to be checked so that it gets better response to your department. And secondly thing is to clean the proper specified area where process is done.
- jaipur,rajasathan, India
March 8, 2009
A. Hi Srinivasan,
Depending on exactly what those enclosures look like, it doesn't surprise me that there is some rusting after nearly a year outside. I think electrocoat priming may be required in between the hot phosphating and the powder coating. Good luck.
Regards,
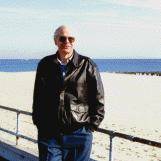
Ted Mooney, P.E.
Striving to live Aloha
(Ted can offer longterm or instant help)
finishing.com - Pine Beach, New Jersey
Gravity, Drips and Powdercoating
Q. Does gravity have an effect on powdercoating? Will a "DRIP" spot appear at the lowest point of the item being powdercoated?
Thank You
Hobbyist - Beaufort, South Carolina
April 26, 2008
A. You should NOT get any drips with powdercoating.
Drips only normally form from liquids. Powdercoating should not get to the liquid stage.
However it is sometimes possible to get "sags", an run that's almost a drip, but you have to add an excessive amount (thickness) of powder, and it can (rarely) happen.
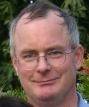
Geoff Crowley
Crithwood Ltd.
Westfield, Scotland, UK
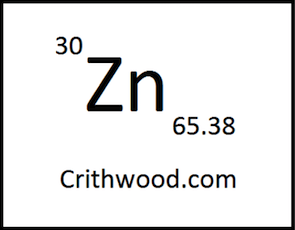
May 1, 2008
Q. We are using polyester powder, we facing pinholes problem now ... so how to reduce?
ganesan [last name deleted for privacy by Editor]- Bangalore, India
August 9, 2012
Hi cousin ganesan. Advice on your pinholes problem has already been offered by two experts on this page -- so the first question is whether you have tried to follow their advice?
- Did you start by cleaning your system thoroughly as suggested? If not, why not?
- Have you double checked that the gun is at least 30 cm away? If not, why not?
- Are you operating at 70 kV, or are you unable to do that for some reason? What reason?
Please comment on that advice before we try to move on to additional possibilities. Thanks!
Regards,
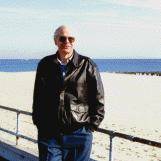
Ted Mooney, P.E.
Striving to live Aloha
(Ted can offer longterm or instant help)
finishing.com - Pine Beach, New Jersey
Q. Hi. I use a number of different colour powder coats, but when I am using the colour "cloud grey" I have black speckles in paint (this is before placing in oven). I am wondering if it's the pigments in the paint? Regards, pete
peter thorne- united kingdom
September 10, 2012
Q. You have not covered bubbles created during curing in the crevices of rims, which is the problem I have. Is the heat source too close to the rims causing this effect?
Edward Mitchell- Langsville, Ohio, USA
December 2, 2014
A. Hi Edward. "Rims"? Are you referring to automobile wheel rims? I don't know what you mean by crevices -- deep recesses in the design, or perhaps the bead area just inside the rim? Are these pressed steel or cast aluminum or what?
In any case, I think I would suspect poor cleaning before I would suspect overheating. We have a hundred threads about similar powder coating problems and probably half a dozen about cast aluminum rims if that is the situation. More data please, so we can direct you.
Regards,
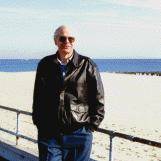
Ted Mooney, P.E.
Striving to live Aloha
(Ted can offer longterm or instant help)
finishing.com - Pine Beach, New Jersey
December 2014
A. Hello Dear,
We have that problem before but it's gone after using auto-machine and powder coating line system.
Try updates.
- Shanghai, China
April 22, 2015
July 23, 2015
Q. Dear Sir,
ACRONYMS:
EP = epoxy-polyester
We are doing a coating on auto part size is about 1500 mm in length and 30 mm in dia. We used EP powder manufactured by a reputed company. But we face Pin Holes, rough surfaces, which are common problems -- but one more serious problem we face is that less coating is seen on the down side of the diameter; otherwise jobs DFT is about 80-125 micron.
Thanking You.
Regards.
Rajendra gatkalcoatings - Chakan, Pune, India
A. Hi Rajendra.
The first step is to walk the line and see for yourself exactly what is being done. It is easy for me to picture an operator (or the programmer of a robot) spraying more lightly near the bottom, based on an assumption that the melting powder will run, and gravity will even things out :-)
Is there any evidence to suggest that the problem is more elusive than that? Good luck.
Regards,
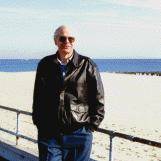
Ted Mooney, P.E.
Striving to live Aloha
(Ted can offer longterm or instant help)
finishing.com - Pine Beach, New Jersey
(you are on the 1st page) Next page >
Q, A, or Comment on THIS thread -or- Start a NEW Thread