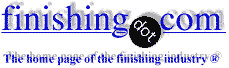
-----
Acid vs. Alkaline Copper Plating
2002
I am currently doing an electroplating experiment for my final year 12 chemistry assignment (as it seems the rest of the world is). We are required to design a cell which will produce the best possible copper plated spoon (stainless steel to start with). Our tests so far have been going well, we are getting an even copper-coloured coat over most of our spoon. The curved head of the spoon seems to be causing some problems. It coats around the edges, but very little copper adheres in the middle. Is this to do with the shape? I am also curious about alkaline plating vs. the acid plating I have found so much information about. We are currently using an electrolyte which is a diluted mix of copper sulphate ⇦ on eBay or Amazon [affil link] and sulfuric acid (about 1:3), with a little copper chloride. I have read a lot about the success of alkaline plating, non-cyanide alkaline plating in particular, but am unable to find any information about what might be in an alkaline copper plating electrolyte, or indeed any simple experiments involving this type of solution. Is it a very difficult process? One last question - which variables contribute most to a smooth/shiny deposit?
I'd appreciate any help you can give.
Cait [last name deleted for privacy by Editor]- Sydney, ACT, Australia
According to Ohm's Law, the current will equal the voltage divided by the resistance; the current will tend to take the path of least resistance (the shortest path). According to Faraday's law the thickness of the plating will be proportional to the current. So the thickness will be lower in recessed areas.
Copper pyrophosphate is the basis for alkaline non-cyanide plating.
There are many factors discouraging a bright, even plate, so it's hard to say which contribute "most". But organic addition agents are necessary for such plating because they cause more nucleation sites for a finer grain and because they are intended to try to encourage more plating in the low current density areas by blocking the high current density areas.
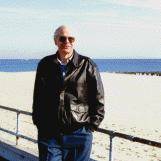
Ted Mooney, P.E.
Striving to live Aloha
(Ted can offer longterm or instant help)
finishing.com - Pine Beach, New Jersey
2002
Q, A, or Comment on THIS thread -or- Start a NEW Thread