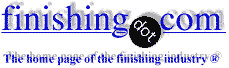
-----
Activating old Nickel plating for Replating
Q. Hi.
I recently moved to Australia working in a plating shop; I've been plating in Lebanon for about 20 years now I'm in a debate with the shop's technician. I would like some input from other experienced people.
For plating freshly buffed/polished or satin'd nickel our process was...
ONLY anodic degreasing-rinse-acid dip-cyanide copper then nickel
We did not have any issues with adhesion even if the piece got scratched -- we could sand it back and replate.
Note if we ran cathodic decreasing also, we needed to strike in Wood's strike.
Also, for example, big bumper bars that wouldn't fit in our degreaser we manually washed the piece until we couldn't see any water breaks then straight into the cyanide copper.
The shop's technician says it's impossible, and says even if it plates the edges wouldn't pass the file test.
Any thoughts?
I appreciate your patience with my lengthy question.
Employee - Sydney nsw
February 10, 2023
A. Hi Sam. Plating is still largely an empirical science. What works works, and what doesn't work doesn't work ... there isn't an answer to your question based on first principles, there is only experience. Anodic cleaning is certainly more effective than cathodic cleaning, but my own limited experience says that the shop technician's approach is correct and yours is "iffy".
I would suggest plating some coupons with both approaches and trying adhesion tests such as strong tape, filing, and bending the coupons around a small mandrel. If the Wood's strike proves better in your coupon tests, then it's better, and I would resist arguing for "good enough"
If you can find it in a local library, Electrodeposition
[on
Amazon
or
on AbeBooks affil links] describes incredibly strong adhesion results for Wood's Nickel on stainless steel, and I would suspect similar results are possible for nickel on nickel -- but be sure to read the postings on this thread by Jeffrey Holmes suggesting that an iodine process is better for nickel on nickel.
Luck & Regards,
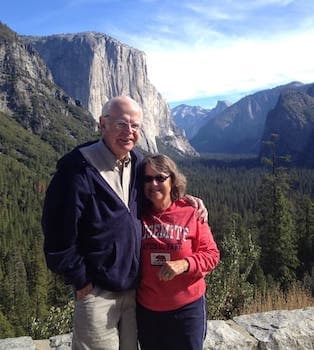
Ted Mooney, P.E. RET
Striving to live Aloha
(Ted is available for instant or longterm help)
finishing.com - Pine Beach, New Jersey
Q. Hi Mr Mooney, thank you for your reply.
To my knowledge the purpose of HCl in the Wood's nickel is to "bite" into the chromium and various alloys in stainless steel and deposit a thin layer of fresh nickel which will be ready to accept further plating -- although this must be done with little time spent in rinsing cycles to avoid oxidation of the thinly plated nickel, thus a properly activated nickelwill yeild same results.
There are quit a few ways to activate nickel. In the literature the one I found most effective is using an alkaline electroclean containing 10% cyanide strictly only anodic, followed by a strike of cyanide copper using a conventional cyanide copper plating tank.
Unfortunately I cannot do comparison tests in the shop because they don't have cyanide copper.
- Sydney nsw
February 12, 2023
Hi again, Sam. You may well be right. Activating nickel is probably somewhat different than activating stainless steel, and it's possible that other approaches are as good as Wood's nickel or better.
Luck & Regards,
Ted Mooney, P.E. RET
Striving to live Aloha
(Ted is available for instant or longterm help)
finishing.com - Pine Beach, New Jersey
⇩ Related postings, oldest first ⇩
See also topic 36223, "Plating nickel on nickel"
Q.
I have some Nickel plated parts and I would like to activate them to be able to do soldering (to mount die).
I tried following steps:
- 1. Foaming gas 600 °C 15 minutes
- 2. 10% HCl, 15 Sec
- 3. Rinse with methanol [affil link]
- 4. Dry
I still have a wetting problem. Do you have any suggestion, or reference I should look at? Please let me know
Regards
1999
A. Try light and uniform sandblasting on the surface, then ultrasonic rinse in acetone ⇦ on eBay or Amazon [affil link] Warning! Flammable! for a few seconds to loosen dust. Water rinse may also work.
Mandar Sunthankar- Fort Collins, Colorado
A. Rajiv, I suggest you to use the following process 1. Soak cleaning 3 minutes to eliminate possible oil and dust dirties on the surface; 2. Tap water rinse 2 minutes; 3. 30% HCl immersion for 1 minute to remove oxide on the surface; 4. tap water rinse 2 minutes. If this process does not work well, use 15%BV sulfuric acid + 20 g/L iodide 80 °F 3 minutes to replace step 3, which is more efficient to remove nickel oxide. Your adhesion problem mainly results from surface contamination and oxide. Good luck! Ling
Ling Hao- Grand Rapids, Michigan
A. The best way to activate "old" nickel deposits is a cathodic cyanide activation: 60 g/l sodium cyanide plus 60 g/l sodium hydroxide. In case you can not use cyanide, activate cathodically with hydroxide alone. Another possibility is activating with a 5 % sulfuric acid, also cathodically.
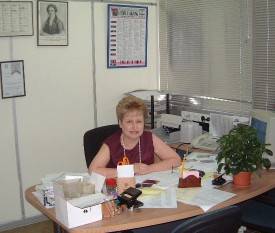

Sara Michaeli
Tel-Aviv-Yafo, Israel
A. I think you can use Sara's recipe but I would use 50 g/l sodium hydroxide and 40 g/l orthophosphite 10 g/l sodium cyanide activate cathodic 2-3 min. And second step activate in a sulfuric acid 60 % until it starting gas-formation. But you must rinse between. Third step activate in a nickel strike. Good luck
Regards
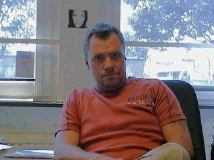
Anders Sundman
4th Generation Surface Engineering
Consultant - Arvika,
Sweden
A. If the nickel has been work hardened, then it is very difficult to activate or even dissolve. First make sure the surface is clean of all oil, grease, or other soil. I would use a stronger solution (e.g. 50% by volume) of hydrochloric acid for at least 2 minutes. Do not rinse with methanol, acetone, or deionized water. These will re-oxidize the surface. Alternatively you could use a Wood's Nickel solution to first etch then nickel strike the "old Nickel" surface. Is your wetting problem too much wetting, with flashing going everywhere, or too little wetting? If the wetting is excessive, selective plate (brush plate)nickel on the area that will be soldered. If adhesion is also a problem try brush copper plating on top of the "old nickel." and then solder on the copper.
Marjorie Turton- Winnipeg. Manitoba Canada
Multiple threads merged: please forgive chronology errors and repetition 🙂
Q. I have few questions regarding the activation of Nickel surface prior to Nickel plating. (Nickel over nickel). The Nickel layer is not fresh; it is coated using some other technique and sand blasted.
1. What is the best method for activation of Nickel surface prior to Electrolytic Nickel?
2. If electro-Activation is preferred which is the best -- cathodic or anodic? Is there a possibility of contamination if cathodic is used?
3. Which cathodic method is advantageous (cyanide or acid)? What are the pros and cons (contamination / Hydrogen embrittlement - occlusion / etc.)
4. What is the best anode material for cathodic activation? (cyanide Alkali / acid ) How to take care of the material dissolving into the solution? what is the expected life of the solution? How often should it be discarded?
5. What are the DSA (Dimensionally stable anodes) that can be used? Do I have to use a membrane / anode cover if graphite or carbon anode is used?
I tried to search for the particular topic but very minimal information could be found in the site. please help
- Singapore
2002
Tip: This forum was created to help build camaraderie through sharing tips, opinions, pics & personalities.
The operator & those readers who want that might not engage with anonymous posters.
![]() ![]() |
A. Hello Karthik. 1. Sorry, I do not know the "best" method of activating nickel, but I do know that many nickel chrome platers who do products like bumpers generally include a nickel strike step these days; this allows them to mix alloy steel raw bumpers and previously plated bumpers together. So my answer is that a nickel strike step is an essential feature of activating old nickel. ![]() Ted Mooney, P.E. Striving to live Aloha (Ted is available for instant or longterm help) finishing.com - Pine Beach, New Jersey A. Karthik. ![]() Anders Sundman 4th Generation Surface Engineering Consultant - Arvika, Sweden A. In my experience, plating nickel on nickel is usually a tricky job. If you are doing a secondary build on top of a fresh first build, usually you can just let the work cool and plate it a second time - without any extra preparation. However, building on top of an older "in service" or "cured" build is different. I work mostly with steel as a base metal , so I use a normal steel to nickel preparation, then follow that with a cathodic acid etch ( usually 24% sulfuric ) and a nickel acid pre-plate. I have the same problem - most people really don't know. But I have done several repairs like this with approximately 95% rate of success. - Kansas City , Missouri A. KARTHIK, ![]() Popatbhai B. Patel electroplating consultant - Roseville, Michigan |
Multiple threads merged: please forgive chronology errors and repetition 🙂
Q. We recently have taken on a new project from an outside polisher and unknowingly have plated a ton of parts with substandard polishing, most of them were pulled after being plated in Nickel only (as opposed to Nickel and Chrome). They were touched up and are ready to go but we have been unsuccessful in our attempts to reactivate the old nickel since we have recently gotten rid of our cyanide cleaners.
Our current process involves an alkaline soak for 5 mins, electrocleaning (cathodic) for 2 mins.,Hydrochloric dip (non-electrolytic, 18-20%)for 1 min, Wood's Ni- no reverse current for 30 sec, then Ni plate. We get adhesion issues nearly every time.
I have read the other posts on this issue and most of them involve using baths that are not practical or possible for us to implement at this time.
Does anyone have a process to reactivate Ni without using cyanide?
plating shop - Pennsylvania
2005
![]() |
A. Hi, - ON., Toronto A. Try this: ![]() Jeffrey Holmes, CEF Spartanburg, South Carolina A. If your cleaning cycle is faultless (water break proof), most surely the problem lies in your Wood's strike. How is the level of HCl and Ni metal in your chemistry? It should gas a lot? Guillermo MarrufoMonterrey, NL, Mexico A. Try dry acid salts containing fluorides, one lbs per gal at 140 °F, 5 min soak time, in place of the Hydrochloric Acid. Contact your chemical supplier for details, such tank & heater materials, ventilations, etc. Hamilton Solidum- Mays Landing, New Jersey |
Cathodic cyanide activating 'old' nickel surface for gold finish
Hello, can anyone tell me more details about cathodic cyanide activation. I want to put a layer gold on top of a passivated nickel surface. Many thanks
James Zhuproduct designer - UK
2007
It will not work if the "passivation" (read oxidation) is extreme. However, mild passivation may be reactivated in one pound per gallon sodium or potassium cyanide, perfectly clean D.I.water, stainless steel anodes, work cathodic at about 6 to 8 volts, absolutely no other cyanide soluble metals present. If any copper, zinc, or other is present as contaminant, then it plates onto the passive nickel and does not bond.
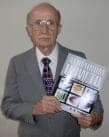
Robert H Probert
Robert H Probert Technical Services

Garner, North Carolina
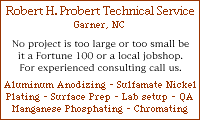
Q. Hi All
I am about to make up a Woods solution and wondered if Wood's Nickel Strike was okay to use as an activator to Re-Activate old plated nickel then plate Bright nickel on top ?
Can anybody advise me further?
Thanks to all.
Fred
polishing bike parts - London, United Kingdom
March 30, 2011
A. It will work most of the time and is the best strike for your purpose. You will find that some old oxidized and some polished nickel will take a lot stronger activation step.
James Watts- Navarre, Florida
Q. Hi,
I have seen three references in this thread to using lead counter electrode as a step in nickel activation, however in one case the work piece was anodic, and in two others it was cathodic. Is there a preferred direction here?
Cheers,
Stan
- Boston, Massachusetts
October 19, 2011
A. Hi, Stan.
Actually I don't think I would summarize the thread exactly the same way:
A Wood's nickel strike, using nickel anodes and direct current (the workpiece being cathodic or negatively charged) is a very widely accepted approach to activating nickel for plating upon it. Some users do apply reverse current for a period of time first.
But if the nickel is "old" or "not fresh", some readers suggested that the nickel strike should be proceeded by etching in acid with lead (or much more expensive DSA) cathodes. Mr. Patel said that the current for this should be "direct", but I think this may be a semantic error, and I agree with Mr. Sundman's posting that the workpiece should be anodic for this step.
If possible, please review the "Adhesion" chapter in Jack Dini's "Electrodeposition: The Materials Science of Coatings and Substrates" as it offers quantitative data from testing some different approaches to Wood's Nickel activation (although it actually tests nickel on stainless steel rather than nickel on nickel)
Regards,
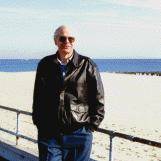
Ted Mooney, P.E.
Striving to live Aloha
(Ted is available for instant or longterm help)
finishing.com - Pine Beach, New Jersey
Multiple threads merged: please forgive chronology errors and repetition 🙂
Electroless nickel on nickel alloy
Q. Which is the best method to activate nickel & nickel alloy for electroless nickel plating
Joshua joshuaplating shop employee - tamilnadu, India
November 14, 2015
by Jack Dini
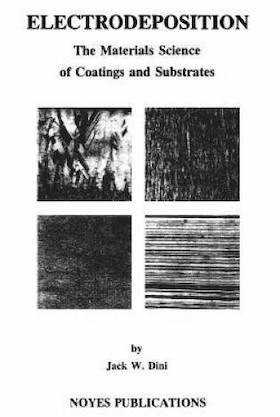
on eBay or Amazon
or AbeBooks
(affil link)
A. Hi Joshua. We appended your inquiry to a rather similar thread as food for thought. Whether electrolytic nickel on nickel or electroless nickel on nickel, Wood's nickel strike is the standard answer. If you can comment with specifics regarding anything you've tried, and what results you got, the dialog can probably continue most productively. Thanks.
The issue is well covered by the "Adhesion" chapter in Jack Dini's "Electrodeposition".
Luck and Regards,
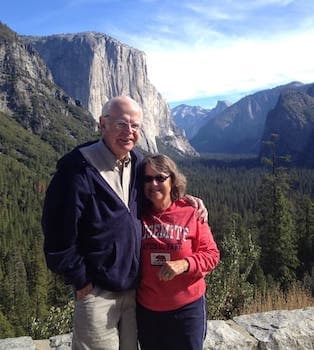
Ted Mooney, P.E. RET
Striving to live Aloha
(Ted is available for instant or longterm help)
finishing.com - Pine Beach, New Jersey
November 2015
A. Hi Joshua,
Follow below steps for activating nickel alloy for better adhesion in electroless nickel plating.
1. Etch with ferric chloride
⇦ on
eBay or
Amazon [affil link] 280 - 290 g/l + HCl 38 ml/l for 90 seconds operating temperature RT.
2. Rinse with DM water
3. Wood's nickel strike--> NiCl26H2O 350 g/l + HCl 22 m/l for 110 Sec at 3.5 amps/dm2
4. DM Water rinse
5. Electroless nickel plate
- Bengaluru-Karnataka , India
June 1, 2018
Citric acid for Nickel-on-Nickel Plating?
Q. Recently I have been having troubles with plating a two-layer part, both layers being Nickel Sulfamate with some added cobalt. The first layer is a "plate down" - a pattern on a glass mandrel is replicated via electroforming. The part is then pattered with dry film photo resist, exposed and developed, and prepared for a second layer of nickel cobalt. Now you know Nickel does not plate very well on nickel, so before electroforming the second layer, an "activation" solution is used - made up of potassium iodide diluted with DI Water. The first layer nickel with photo resist sits in this solution for 30 minutes, then it is rinsed well with DI and placed into the tank to be electroformed. However, this solution almost always reveals a white-ish staining across the part.
Do you know of any other chemicals or solutions that are used to "activate" nickel for a second layer of nickel?
I appreciate any and all responses!
thanks,
Process Engineering - Precision Electroformed Parts - Lowell, Massachusetts - USA
March 16, 2017
A. Hi Ben. Have you tried a Wood's Nickel Strike or a Sulfamate Nickel Strike before the 2nd layer of Sulfamate Nickel?
Regards,
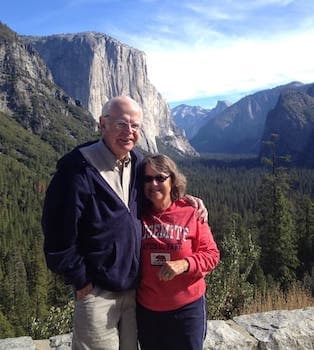
Ted Mooney, P.E. RET
Striving to live Aloha
(Ted is available for instant or longterm help)
finishing.com - Pine Beach, New Jersey
A. The cyanide or citric acid activation must be with current; the part is cathodic and it's only good for moderately oxidized nickel. Ted's advice of Nickel Chloride Strike is required for old tenacious heavily oxidized nickel.
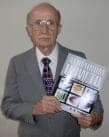
Robert H Probert
Robert H Probert Technical Services

Garner, North Carolina
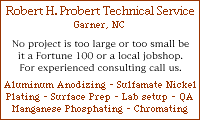
A. I suggest that you activate the first nickel electroform by immersing it in the nickel plating bath and then make the part anodic for 30 to 60 seconds and then make the part cathodic without removing it from the bath. As long as your nickel anodes are working properly, this activation process will work.
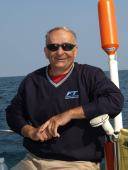
Pat Mentone
St Paul, Minnesota
A. The Iodine based formula for nickel over nickel activation contains potassium iodide, sulfuric acid and iodine. I have used it, and it works every bit as well as the Wood's nickel strike. Maybe even better.
If you can find a copy of The Canning Handbook it is in there.
Here is the iodine activation formula -
Add to one gallon of water the following chemicals:
3 Fluid ounces of concentrated sulfuric acid slowly with stirring.
One third ounce of Potassium Iodide.
0.002 Ounce = 0.062 Grams of solid Iodine.
The Potassium Iodide is dissolved in a separate small amount of water and the solid iodine is added. When the iodine has dissolved the solution is added to the cold diluted sulfuric acid solutions and thoroughly mixed. In use, the iodine should be added periodically to maintain a straw color.
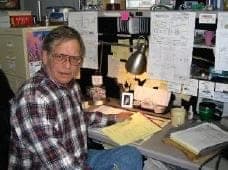
Jeffrey Holmes, CEF
Spartanburg, South Carolina
Q. Hello,
This is my first attempt at electroplating. I have a instrument with chrome plated buttons. The problem is that the manufacturer didn't do it right and the plating is starting to rub off. For this reason I am trying to nickel plate the parts myself instead. The issue is that the plating doesn't seem to stick. Is it possible to nickel plate parts that are already partially chrome plated?
-Tom
- Germany
April 14, 2020
A. Hi Tom. Removing the chrome is necessary, but easy; a quick dip in muriatic acid will do it. But that isn't the big issue confronting you :-)
We appended your inquiry to a thread about activation/re-activation of nickel plating so you can read about the importance of it and a few different approaches you can try towards accomplishing it.
However, as general advice to you & others, I don't think that trying to re-nickel plate an instrument's chrome plated buttons should be your very first attempt at plating. There is so much to proper plating, so many variables to manage, that I think you should get some clean, highly plateable, brass coupons (as typically used in a Hull Cell ⇦ huh? ) and demonstrate to yourself that you have workable chemistry, operating conditions, and technique for very basic nickel plating before trying to get good plating on a substrate which challenges people with decades of experience. Good luck.
Regards,
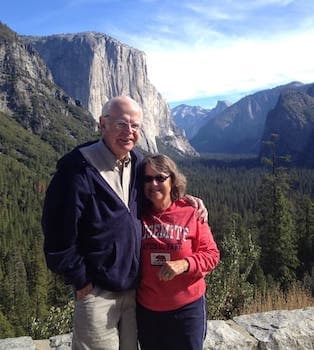
Ted Mooney, P.E. RET
Striving to live Aloha
(Ted is available for instant or longterm help)
finishing.com - Pine Beach, New Jersey
Q. I work as an agent for a plating chemical supplier here in the Philippines as a Technical guys for support and service. I am interested on the topic of "nickel surface activation prior plating".
I want to know whether the solution of 15% by volume Sulfuric acid plus 20 g/L of Iodide as Potassium Iodide as recommended earlier (1999) by Mr. Ling Hao of Grand Rapids, Michigan is STABLE -- the stability of the solution is proven to be okay or not? Are the active ingredients of this Sulfuric acid + Potassium Iodide solution okay and do not easily degrade in time during this use? Please kindly advise us accordingly.
Thank you so much!
Sincerely,
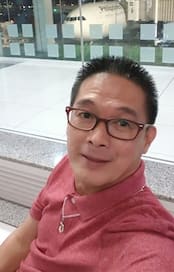
Ferlito Guinto
Private employee / technical person for plating - Calamba City, Philippines
February 14, 2022
A. I've never heard of any of these nickel reactivation systems before. What we usually do is either use an electrocleaner with the polarity reversed, or you can also use a sodium bisulfite and sodium fluoride solution that is an immersion process. No electricity. You can also use both in series (electrolytic activation, steel acid, and then immersion process).
Thomas SwanLab Technician - Portland, Oregon
Q, A, or Comment on THIS thread -or- Start a NEW Thread