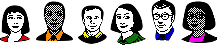
Metal finishing Q&As since 1989
-----
Hardcoating using Pulse Rectifier
Please see also --
• Topic 0208 "Interference coloring of aluminum by pulse anodizing"
• Topic 14519 "Pulse anodizing"
for Shops, Specifiers & Engineers (affil links)
"Aluminum How-To" -- Chromating, Anodizing, Hardcoating by Robert Probert (2005)
avail from finishing.com
"The Metallurgy of Anodizing Aluminum" by Jude Mary Runge (2018)
avail from eBay, AbeBooks, or Amazon
"The Surface Treatment & Finishing of Aluminium and Its Alloys" by Wernick, Pinner & Sheasby (1959 - 2001)
avail from eBay, AbeBooks, or Amazon
"Surface Treatment and Finishing of Aluminum" by Robert King (1988)
avail from eBay, AbeBooks, or Amazon
"Anodic Oxidation of Aluminum and Its Alloys" by V. F. Henley (1982)
avail from eBay, AbeBooks, or Amazon
"The Technology of Anodizing Aluminum" by Brace (1979)
avail from AbeBooks or Amazon
"Aluminum Finishes Process Manual" by Reynolds Aluminum (1973)
avail from eBay, AbeBooks or Amazon
"The Anodic Oxidation of Aluminum" by A. Jenny (1940)
avail from AbeBooks or Amazon
"Anodizing and Coloring of Aluminum Alloys" by S. Kawai (2002, VERY RARELY avail)
from eBay, AbeBooks, or Amazon
Q. At our shop we are having troubles with hardcoating 2000 series aluminum. We get either an uneven coating or our parts burn. I do know that 2000 series aluminum is difficult to hardcoat due to amount of copper in the aluminum causing hot spots in the metal which leads to burning, but I've been researching ways to hardcoat 2000, and the best answer I've been seeing is to pulse hardcoat.
Our rectifiers do have the pulse setting on it. But I cannot find the manual for the rectifiers. It is a Dynapower touch pad, and I cannot find anything online that shows me how to use this pulse setting. I was wondering if anyone has any knowledge on how to work this pulse setting? ... and just to be clear I need it to be a simple explanation so I can teach our line operators how to do so. thank you
Jared Goddard- Green Bay Wisconsin
October 29, 2020
A. The 2000's, especially 2024 and especially heat treated 2000's require higher free acid to prevent the problems you are having, run the free acid on up to 220 g/L.
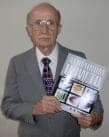
Robert H Probert
Robert H Probert Technical Services

Garner, North Carolina
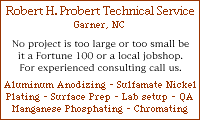
⇩ Closely related postings, oldest first ⇩
Q. We currently do Hardcoat anodizing on high copper alloys using an old proprietary system called IMPERV-x.
The system is really hard to maintain as the company that mfg'd it is long ago out of business & it is impossible to get replacement parts.
One of the main items we hardcoat with this system is a very small (1/8" dia x 3/4" long) military part which is 2024 alloy. We have been processing this item for 10+ years.
With our Imperv-x system getting older & older we are considering switching to a new Pulse Rectifier. Should we expect to be able to run the above mentioned parts no problem with pulse rectifiers?
Any advice appreciated.
David A. Kraft- Long Island City, New York
1998
A. David,
A. We have been pulse hard anodizing for 15 years. So long as we set the automatic ramp slow enough and control the maximum voltage we don't have problems with 2024. We use a conventional solution with 1% oxalic acid added.
Pete Faxon- Oxnard, California
Aluminum How-To
"Chromating - Anodizing - Hardcoating"
by Robert Probert
You'll love this book. Finishing.com has sold 880 copies over the years without ever a single return request :-)
Q. Dear Sirs,
I will be very thankful to him if anybody sort out my this problem.
I have job in aluminium alloy which is to be hard anodized. The coating thickness requirement is 100 microns, Hardness req'd is 1200 VPN. The area of the job is 1.2 Sq. Ft. and required time would be around 8 mins.
To do this with the normal rectifier it is practically impossible in 8 min. using conventional rectifier. But if we use Pulse Rectifier it is possible we feel. If so what should be the specification of the rectifier? At what frequency should we operate the pulse?
In pulse rectifier if we need to maintain average current of 100 amps then maintaining duty cycle 50% and ON current for 1 millisecond and zero current for 0.5 millisecond then the maximum peak current will be 200 amps and minimum will be of course zero. In that case what will be effect on the surface of aluminium? it's hardness? and also on the temperature rise?
Is it acceptable to use such a high current? What should be the frequency range of the pulse rectifier to achieve 100 amps current?
Please explain.
Rajendra Khatavkar- Pune, INDIA
1998
A. Dear Sir,
There are many issues which need to sort out.
1. You cannot get hard anodising of 100 microns in 8 minutes. On an average you may require minimum 70 minutes to get to your 100 microns even if you use proper Pulse.
2. Your pulse on and off time is high frequency. Generally your need on time and off time in the range of 0.5 sec to 10 sec.
3. You need to work with low temperature of around 0 °C. in hard anodising. Or else you may have to use proprietary additives to work with temp range of 8 to 12 °C
4. You need to have proper experience and information about anodising, hard anodising and use of Pulse rectification.
5. The conc. of electrolyte, temperature of operation also plays important role in thickness and hardness of coating.
6. Further please consult with somebody who has worked in hard anodising before proceeding.
metal finishers - Bangalore, India
A. Hi Rajendra. I am not especially versed in pulse anodizing but I must agree with Rudresh that your desired process time is impossible -- out of the realm of possibility by approximately a full order of magnitude.
Luck & Regards,
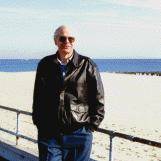
Ted Mooney, P.E.
Striving to live Aloha
finishing.com - Pine Beach, New Jersey
A. Dear Sir,
The most important reason for using using pulse anodizing is the recovery period.
If an anodizing voltage E1 is quickly reduced to a lower value E2, the current falls to a very low value and may take a considerable period of time, amounting to minutes, to attain the steady state condition characteristic of the second voltage: but if the voltage reduction is carried out slowly the recovery is much quicker.
Sunny regards
Anne
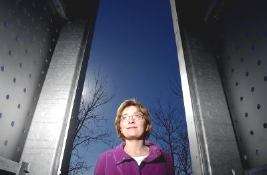
Anne Deacon Juhl
- - Trustrup Denmark
Multiple threads were merged: please forgive repetition, chronology errors, or disrespect towards other postings [they weren't on the same page] :-)
Q. We are interested to set up a hardcoat anodising plant with pulse rectifier. Please help us to get the pulse rectifier which is the best source and which is the best brand available. Also, let us know the various industrial applications of hard coat anodising.
With best regards
Masood. A. Khan M.D- Bangalore-India
1999
"Theory and Practice of Pulse Plating"
on
AbeBooks
or
eBay
or
Amazon
(affil links)
A. "Best" is only opinion, Masood, and sorry but we cannot print brand & sourcing recommendations or slams on this semi-anonymous site (why?), but there are a number of manufacturers of pulse-plating rectifiers. Good luck.
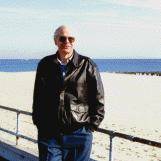
Ted Mooney, P.E.
Striving to live Aloha
finishing.com - Pine Beach, New Jersey
Multiple threads were merged: please forgive repetition, chronology errors, or disrespect towards other postings [they weren't on the same page] :-)
Q. We have a customer inquiring about the benefits of pulse rectification for hard coat anodizing, does it reduce cycle times, increase current density, etc. He would like to real-life examples instead of theory.
Craig Henry- East Troy, Wisconsin
2005
A. Pulse rectification has many benefits. Run times can shorten with increased amperage. For example, I have processed blasted 6061 parts at 25 amps/ft2 for 1.5 hours at an end voltage of 76v to acquire .002 of hardcoat. I took the identical load and processed pulse at 40 amps/ft2 with a 10 sec on/2 sec off wavelength for the pulse in 55 min with an ending voltage of 71.1v to acquire .00198 of hardcoat. Overall this is a 50% savings of energy and a 35% savings on production time. Depending on required amps/ft2 needed for processing pulse wavelengths may have to be adjusted to give the rectifier ample time to achieve amps needed. The more amps needed the longer the wavelengths. For a 2250 amp run I process at 10 sec on/2 sec off.
Scott Eastman- Springfield, Massachusetts, USA
June 24, 2009
Multiple threads were merged: please forgive repetition, chronology errors, or disrespect towards other postings [they weren't on the same page] :-)
Q. WHY IS PULSE RECTIFIER NEEDED FOR HARD ANODISING? WHY IS CONVENTIONAL RECTIFIER NOT SUITABLE?
INDUKUMAR NAIRbuyer - ALUVE ,KERALA,INIDA
July 26, 2011
A. Hi, Indukumar.
A conventional rectifier is suitable for hard anodizing in the general case. In fact, I would bet that there are many more conventional rectifiers in service for hard anodizing than pulse rectifiers :-)
But if you want to work at the state-of-the-art, some people feel that pulse anodizing offers advantages, especially on 2xxx aluminum. Dr. Anne Deacon Juhl did her PhD thesis in pulse anodizing, so you may wish to google her; I believe you can buy copies of that thesis. Good luck!
Regards,
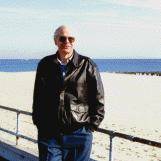
Ted Mooney, P.E.
Striving to live Aloha
finishing.com - Pine Beach, New Jersey
A. Mr.Indukumar
Anodising is an exothermic reaction. Lots of heat is generated. Hard anodizing needs more thickness beyond 40 microns. Generally it is done at 0 °C. Pulse rectifiers does on and off of current during the process. During Off time, heat is not generated and hence helps in build up.
Alloys like 2024 are very difficult to do hard anodizing in conventional sulfuric acid solution without additives.
Many suppliers do not like additive as it is expensive and difficult to maintain. Hence Pulse rectifier is used.
- Bangalore, India
November 30, 2015
Taber Abrasion Tester
on
eBay
or
Amazon
(affil links)
As of today I am keeping an open mind on the use of pulse on Anodizing. So far I have never seen any objective evidence that pulse gives faster or harder or better Taber results. I see lots of opinion but NO case studies of pulse vs. standard rectification. If the only thing you get is to be able to use higher AMPS without burning then pulse is just a means to an end not a result. Still open to feed back with OBJECTIVE EVIDENCE.
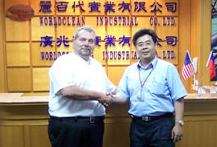
Drew Nosti, CEF
Anodize USA

Ladson, South Carolina
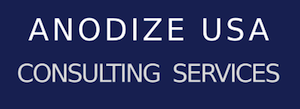
May 29, 2016

Q, A, or Comment on THIS thread -or- Start a NEW Thread