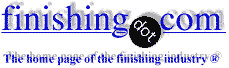
-----
Basic Anodization of Aluminum Process
2002
Dear Sirs,
I am a college student who is interested in measuring the optical effects of small amounts of metal deposited at the base of the pores of a piece of porous aluminum. I have looked up a great many articles and the majority have different processes of anodizing aluminum. I was hoping that someone here might be able to tell me a process that they have used themselves so that I can skip the experimental phase of trying to find a specific pore size, density and depth. The reason for this is that I have to prove the pore size, density and depth by using an electron microscope and they charge $150 and hour (with a minimum 1 hour charge) so I am trying to minimize the amount of time spent on the electron microscope.
I have access to a college chemical lab so I should be able to get use of just about any device needed and safety equipment such as ventilation hoods. I also have access to a large number of chemicals. I am assuming distilled water will be used at each stage.
I would like to maximize pore density. I have read where approximately 50% of the surface area can be made porous. The pore diameter seems to be a function of voltage and solution used, I would like a diameter of 30-40 nm, although larger would also be usable. The pore depth (disregarding the barrier layer) also seems to be a function of voltage and 6-10 microns would be nice.
Part 1
The type of alloy I intend to use is either 1100, 3003, or 6061. I was hoping that someone would tell me which would be the best and worst alloy to use.
Part 2
I have Sodium Hydroxide and can use it to strip the Al2O3 layer from the Al plate. Would someone have a optimal NaOH concentration, temperature, and time?
Would some other method work? I have also read where electropolishing works but I am not eager to use HF (nasty stuff).
I read where acetone
⇦ on
eBay
or
Amazon
[affil link] Warning! Flammable!
may also take off the Al2O3 layer. I tried this and did indeed get a grey residue on a white cloth towel I was using but I don't know how effective this would be.
Part 3
Assuming NaOH was used to remove the Al2O3 layer, I have read where nitric acid is useful in removing the "smut" that remains on the plate. Would anyone know of a optimal concentration, temperature and time for this process?
Part 4
It seems that most people use sulfuric acid and I have access to this but there are also articles regarding oxalic acid, phosphoric acid, etc. Does anyone have a preference? It seems that sulfuric produces smaller diameter pores but it might be better start off with something larger in diameter and work down. Again would anyone know of a optimal concentration, temperature, time and voltage and amperage for these acids? I have access to a DC unit that can deliver up to 4 amps at 30 V or 2 amps at 60V. Just about any range between 0 and the above values can be made, it also allows for constant current or constant voltage to be used.
Part 5
Since I need the pores to remain open, I won't be dropping the plate into boiling water. But is there a good way to wash the acids off? I ask this because if I used water, will that leave residue? Or could even cold distilled water hydrate the Al2O3 and cause pore closure? Could I useacetone
⇦ on
eBay
or
Amazon
[affil link] Warning! Flammable!
which would evaporate much quicker than water, but since it is a solvent would it eat away at the Al2O3 material constituting the pores?
Thank you for taking the time to read this.
- Jackson, Mississippi
1. You need to get into
The Technology of Anodizing Aluminum
[on
AbeBooks, on
Amazon, on
eBay" (affil links)affil links] by Brace and Sheasby and The Surface Treatment and Finishing of Aluminum and Its Alloys by S. Wernick, R. Pinner, P.G. Sheasby.
2. Etch in 4 oz/gal NaOH for 5 minutes at 120 F.
3. Remove smut in 30%/vol commercial Nitric Acid, however, in the real world, nit picking, nitric does not remove all of the salts from the alloying ingredients, therefore, proprietary mixtures are used. For your purposes, 30% Nitric Acid should suffice.
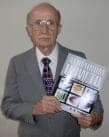
Robert H Probert
Robert H Probert Technical Services

Garner, North Carolina
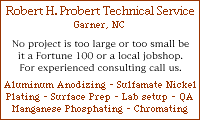
2002
Try an electrolytically colored anodic coating which utilizes tin chemistry deposited at the bottom of the pores. It's widely used in architectural industry and referred to in Europe as 2-step anodizing. As someone has already suggested
Wernick, Pinner & Sheasby's book on the subject, a chapter in it on electrolytic coloring will tell you that salts of tin, copper, cobalt and nickel can be used in this application.
The bulk of our experience is on 6061. Due to 1100 being nearly pure aluminum, I'm sure it would work as well. I haven't any recollection of a job on 3003, however, it's not heavily alloyed thus I'd suspect no trouble coloring it. 7xxx alloys like 7075 is difficult and requires special techniques and 2xxx are impossible to color using this technique.
Good luck!

Milt Stevenson, Jr.
Plating shop technical manager - Syracuse, New York
2002
2002
Hello,
Thank you both for the helpful comments. I will try and get both of those books.
Thank you again,
- Jackson, Mississippi
Q, A, or Comment on THIS thread -or- Start a NEW Thread